CPC Corp. Relies on CTCI to Improve Fuel Quality & Environmental Performance
Talin #10 Sulphur Recovery Unit (SRU) EPC Project
- Market:Hydrocarbon
- Owner:CPC Corporation, Taiwan
- Licensors:Jacobs (SUPERCLAUS) / MECS DynaWave
- Completion Year:2014
- Location:Kaohsiung, Taiwan
- Scope of Work:E + P + C + C
- Capacity:250 tons sulphur / day (125 per train)
In 2012, the Taiwan government approved an investment of NTD6.6 billion (USD200 million) at CPC Corporation’s Talin refinery for a two-trained sulfur recovery facility. This consisted of one SRU with daily production of 250 metric tons of liquid sulfur, as well as auxiliary facilities and Outside Battery Limits (OSBL) pipeline work. SRUs process hydrogen sulfide and foul acid gas resulting from residue fluid catalytic cracking (RFCC) and gasoline/diesel residue hydro-desulfurization units, which improving both gasoline/diesel and fuel oil quality, while reducing air pollution. CTCI completed the project 48 days ahead of schedule, demonstrating strict control of both the procurement and construction phases. The project also received the Taiwan government’s 14th Public Construction Golden Quality Award, an annual award given to the single most successful public construction project in Taiwan. The innovated project management processes and techniques first employed in the Talin #10 SRU project are now used by the company to demonstrate as one of the best project practice models to project managers operating at home or abroad.
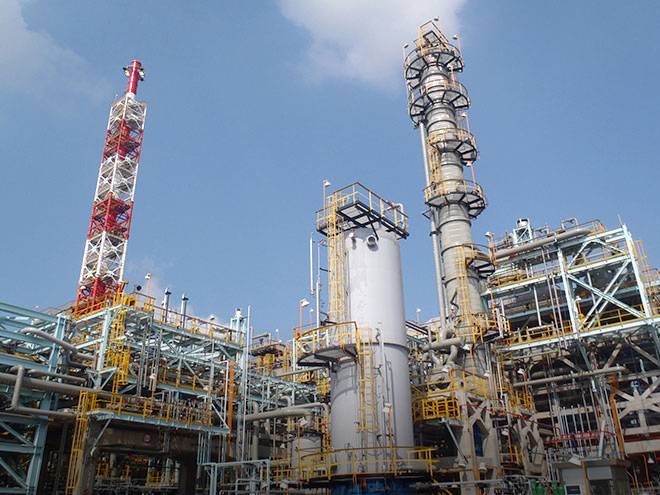
Why CTCI?
Valuable Procurement Partnerships
For the Talin #10 SRU project, equipment and material procurement represented about 70% of the contract value. CTCI actively builds long term partnerships with vendors under the CTCI Alliance Partner (CAP) scheme, which coupled with extensive experience working with international supply chains enabled the team to submit a thoroughly priced bid. Local access in Kaohsiung to CTCI’s own fabrication shop, which provided much of the stationary equipment for the #10 SRU, also provided significant quality enhancement and schedule control benefits.
Reliable Realized
Peerless Construction Management
There are few places where it is more important to strictly control construction scheduling than in Taiwan, due in part to Taiwanese construction companies’ habit of operating on wafer-thin margins. These thin margins leave projects at risk of abandonment. Skilled labor is also in short supply, resulting in a sellers’ market. CTCI’s ability to achieve mechanical completion of the SRU project 48 days ahead of schedule was a testament to the team’s peerless construction management, and their ability to create an environment in which sub-contracted labor was able to work smoothly. Costly piping welding labor was required onsite for the absolute minimum of time, with little or no idle hours—particularly impressive given the stringent quality control measures enforced by the Taiwanese government for this project.
Technical Matters
Green Engineering
The SRU plant set an industry standard by incorporating optimized electrical, piping, and instrumentation control design, as well as pollution prevention and surveillance systems. The waste heat recovered from the waste heat boiler reduced annual CO₂ emissions by 23,000 metric tons, saving 6,990,000kW of energy per year. The SRU plant also adopted a closed heat transfer circulation system and steam reuse design to reduce water consumption by an estimated 76,000 cubic meters of water each year. Moreover, the #10 SRU unit itself employed a mirror arrangement. Each train was paired with tail gas treatment units linked to a single common stack. This layout saved about 50m of 40-inch carbon steel pipes, as well as 11,825kg of pipes, related pipe supports, steel structures and foundations.
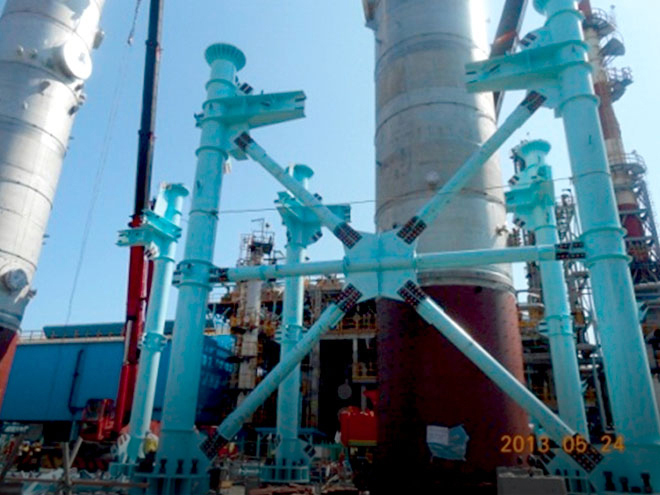
Smarter Engineering
On Mobile & in the Cloud
The Talin #10 SRU was the first CTCI project to use mobile apps and PDAs. This was essential because the project started field work before engineering design was 100% complete. This meant it was crucial that the latest design data could be shared in realtime. The availability of PDAs al-lowed the supervisors at site to have access to the latest schematics, provide correct instructions and minimize mistakes. The method also enabled monitoring supervisors to perform punch list checks without carrying bulky documents and drawings; leaving hands free to comply with safety procedures, as well as take photos, film or voice recordings. The myriad tweaks and changes made as the project progressed were processed through the cloud and uploaded in realtime, sub-stantially improving the convenience and efficiency of site monitoring and management operations.
“CTCI put great effort into procurement work during the early stage of the project by purchasing all equipment and devices well in advance. A smooth purchase process, with all the equipment and material delivered to the site on time, naturally resulted in a smooth construction process as well.”
Chih-Chin Ho Taiwan CPC Corporation Project & Construction Division, Chief of No.1 Talin Construction Office