Discover Reliable
發現信賴
CTCI Completed Taiwan's First Energy-from-Waste (EfW) Plant Revamping Work: Gangshan Incineration Plant
— J. C. Shih, Senior Manager of Project Dep. 1, Group Resource Cycling Business
- Market type: Large scale Municipal Solid Waste EfW Plant
- Client:Environmental Protection Business Operation Center of Taiwan Sugar Corporation
- Executive unit: ECOVE Environment Service Corp. of CTCI
- Completion date: November 2017 (the first phase of revamping work)
- Location: Benzhou Industrial Park in Kaohsiung City
- Project scope:Revamp for the entire EfW plant
The Gangshan EfW Plant, hereinafter referred to as the Gangshan Plant, is located in the Benzhou Industrial Park, Kaohsiung City. It covers an area of 7.24 hectares and was completed and started operation in 2001, which can treat municipal solid waste and industrial waste. The main service areas include Gangshan, Yanchao, Qishan, Alian, Yongan, Luzhu, Mituo, Quieding, Menong, Ziguan, Tianliao, Hunei, and other administrative districts. After 15 years of operations, the plant equipment is getting old. In recent years, since the boilers have deteriorated with broken tubes, sinters on the wall, and exhaust gas flue leaking, unscheduled shutdown has occurred frequently, which has affected revenue due to low incineration availability rate and poor operation efficiency. More than 20 EfW plants in Taiwan have been operating for nearly 20 years and are entering the peak period of revamping. To improve Gangshan Plant's operational efficiency, ECOVE Environment Service Corp., a subsidiary of CTCI, took over the task of plant-wide equipment upgrading, operation, and maintenance. This is Taiwan's first EfW plant revamping example, and the first time for CTCI to work in this field. The task was very challenging. When ECOVE Environment Service Corp. took over the revamping work, the main problems of the plant were solved and equipment improvement had been completed within only four months. The plant availability rate increased from 73% at that time to 100%. Meanwhile, the daily waste treatment capacity has increased by nearly 300 tons compared to the initial period of the takeover, which has effectively relieved the pressure on waste disposal in Kaohsiung City and enabled Kaohsiung to have the ability to help adjacent Tainan City to process another 95 tons of waste per day. This successful experience has also opened up a new page for the subsequent EfW plant revamping work.
Why CTCI?
A Team of Professionalism and Innovative Technologies
ECOVE Environment Service Corp. is a subsidiary of CTCI, which is the largest turnkey contractor in Taiwan. The Group integrates engineering, intelligence, and resource cycling businesses, and offers a whole package of professional EfW plant building/operation/ commissioning services. ECOVE Environment Service Corp. has been fully in charge of seven large-scale Municipal Solid Waste EfW plants in Taiwan and two large-scale Municipal Solid Waste EfW plants overseas in terms of operation and management. Its operation performance have been constantly recognized by its clients and competent authorities, and it has also won many awards for environmental protection, engineering safety, quality, and corporate governance, including the Award for Promotion of Private Participation in Infrastructure Projects from Ministry of Finance, National Standardization Award, and the National Occupational Safety and Health Award. In addition, with an extensive network of contacts, CTCI and ECOVE Environment Service Corp. have actively researched and developed new technologies and obtained a number of patents; thus, it was favored by the judging committee members and awarded to this Gangshan Plant revamping project.
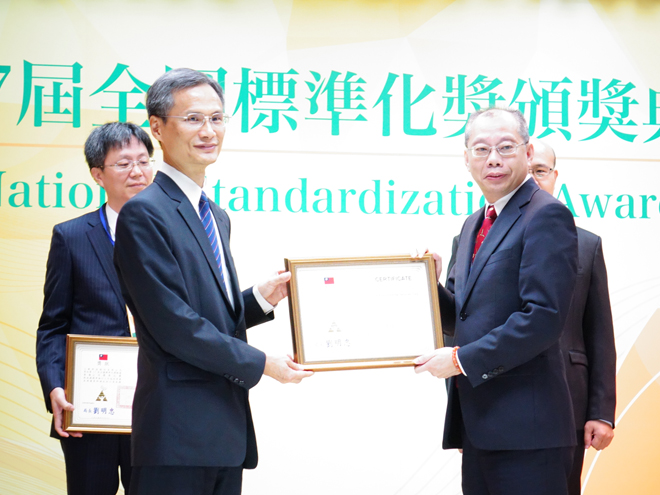
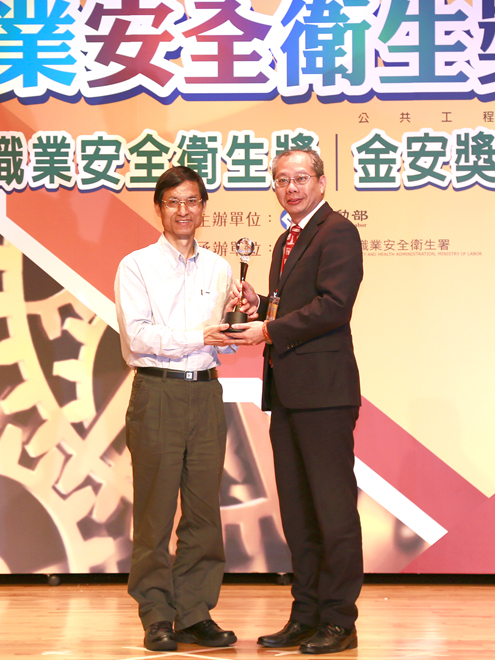
Reliable Realized
Rapid mobilization to develop EfW plant improvement plans
With rich experience and achievements, ECOVE Environment Service Corp. acquired the contract of Gangshan Plant Revamping Project in May 2017. The scope of work included whole plant equipment revamping and upgrading as well as operation & maintenance of major incineration processes. To rapidly achieve two goals: major equipment revamping and upgrading as well as improvement of operation & maintenance quality, the team was quickly mobilized. In two weeks, plant cadres were requisitioned and divided into Operation and Management (O&M) team and Revamping team. The O&M team then formulated the necessary SOP/SMP for operations management and received educational training so that they can familiarize themselves with Gangshan Plant's equipment characteristics and the procedures and safety requirements for operation and maintenance. On the other hand, the Revamping team immediately performed boiler tube measurement and life cycle analysis, and formulated detailed improvement plans for four major issues: increasing incineration capacity, enhancing energy-from-waste efficiency, reducing pollutant emissions, and improving operational safety and stability. The team went on to procure materials and assign preparation tasks. Within two months, the team had put everything in place and started undertaking the large-scale revamping work.
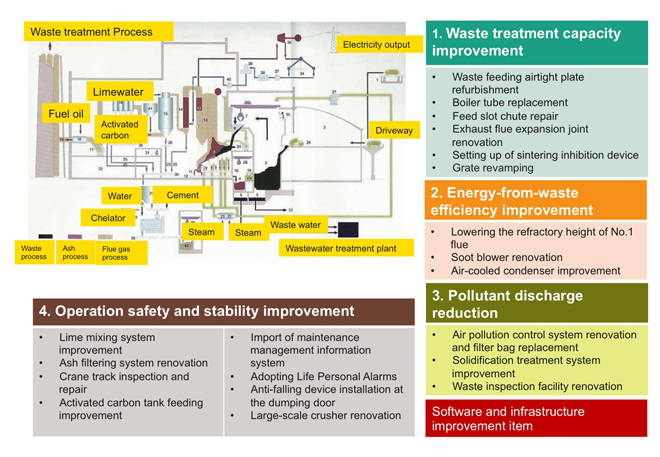
Comprehensive Revamping Planning
Technical Matters
Life cycle management of boiler tubes and anti-corrosion technology
The Gangshan Plant's industrial waste accounts for more than 50% of the total amount of the waste. Since industrial waste contains high calorific value and high levels of chlorine, the boiler temperature may exceed 1100°C, and the concentration of hydrogen chloride in the exhaust gas is quite high. According to the statistics in 2016, the water wall tube and superheated tube breakages had led to 21 times unscheduled shutdown; thus, addressing the tube breakages was the key to the success of the revamping work. ECOVE Environment Service Corp.'s Revamping team has already conducted a detailed plant inspection even at the stage of preparation for bidding, analyzing various operation reports, maintenance records, and accident records, to identify the boilers' risk parts at Gangshan Plant. After moving in, the team conducted measurements of the thickness of each section of the boilers' tubes, analyzed the tubes' thinning rate, evaluated the tubes' life cycle, developed tube replacement and management plans, and introduced highly corrosion-resistant INCONEL welding tubes, which has solved the tube breakage problem and prolonged the tubes' operational life. Within four short months after taking over the revamping work since July 2017, ECOVE Environment Service Corp. enabled continuous operation without any tube breakagesand the availability rate increased from 73% in the beginning of the takeover to 100%, which greatly relieved the pressure of waste treatment and was recognized by the client.
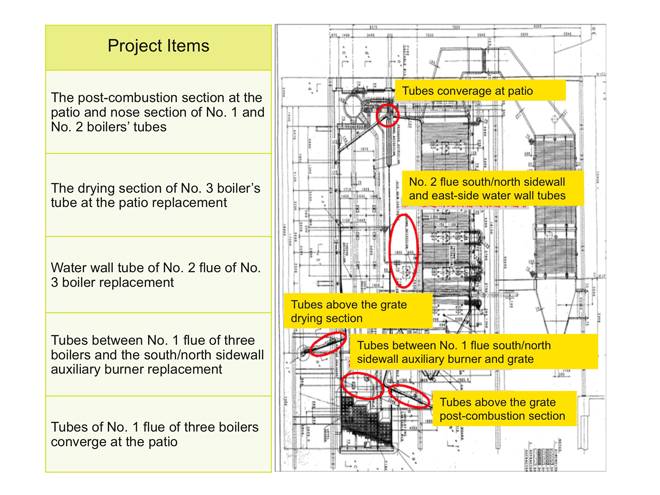
Identifing boiler tubes' life cycle and developing a proper tube replacement plan
Smarter Engineering
Boiler bottom anti-sintering patent
Another issue that bothered Gangshan Plant was that the sinters on the grate would cause boilers to shut down. According to the statistics, before ECOVE Environment Service Corp.'s team taking over the plant, the Gangshan Plant had to shut down roughly once every two weeks to remove the sinters, which seriously affected the plant's availability rate and the amount of waste treatment. ECOVE Environment Service Corp. applied its own developed patented technology (Taiwan Patent No.: M424465; China Patent No.: 2076209) to adjust and set up an anti-sintering device. As of April 2018, no boiler shutdown due to the sinters on the grate has occurred. Compared to the once-every-two-weeks shutdown for removing the sinters before the takeover, ECOVE Environment Service Corp.'s anti-sintering device has achieved remarkable results.
ECOVE Environment Service Corp. requisitioned professional personnel when taking over the revamping work, implemented timely operation & maintenance service, and actively introduced patented technologies and intelligent systems to improve the equipment. Every part of the work has demonstrated its professionalism. Within just six months, Gangshan Plant's operation efficiency was significantly improved. The devotion and hard work of the on-site staff of ECOVE Environment Service Corp. accelerated the repair and maintenance work at the plant, and further enhanced the usage efficiency of the equipment. It is truly worthy of recognition and appreciation. -- Director Huang, Ming-Te, Environmental Protection Business Operation Center of Taiwan Sugar Corporation