Eco-friendly Innovation
綠色創新
Promoting Circular Economy through Incineration Bottom Ash Sorting
In the past, bottom ash generated by energy-from-waste (EfW) plants in Taiwan were primarily disposed of through landfilling. As increasing amount of waste nowadays is disposed of through incineration, the volume of bottom ash continues to rise. Given the diminishing landfill capacity, the local Environmental Protection Administration (EPA) surveyed global practices and established the "Management Methods for the Reuse of Bottom Ash from Waste Incineration Plants" in 2002, an initiative that encourages the processing of bottom ash into recycled aggregates and implements controls over its quality, quantity, and flow, while also clearly defining its applications and scope of use. ECOVE Environment Corporation, a part of CTCI's Group Resource Cycling Business, upholds the core value of "every resource counts." Armed with professional expertise in EfW plant operation and maintenance with intelligent data management, the company addresses the current bottlenecks faced by EfW plants. It translates ESG (Environmental, Social, and Governance) principles into concrete actions. In addition to ensuring the stable and efficient operation of EfW plants, ECOVE actively integrates the goals of circular economy, energy saving, carbon reduction, and pollution reduction. A prime example is the Kaohsiung Gangshan EfW Plant project, where ECOVE made additional investment plans to install bottom ash sorting facilities in its Rehabilitate-Operate-Transfer (ROT) proposal, with the intention to promote the subsequent reuse of bottom ash and implement a circular economy.
Bottom ash features and its uses after treatment
Bottom ash mainly consists of siftings that fall through the gaps between the furnace grates and slag discharged from the end of the stoker, with the latter accounting for over 99.5% of the total bottom ash (Note 1). Its components include slag, sand, ceramics, glass, metals, and other non-combustible materials, along with a small amount of unburned organic matter. Bottom ash needs to go through physical sorting and stabilization treatment before it can be made into recycled aggregates. The treated bottom ash recycled aggregates are porous, lightweight, heterogeneous materials with inert properties, high strength, low compressibility, and no plasticity. These characteristics allow them to be reused as civil engineering materials, replacing natural aggregates and thus reducing the extraction of earth and stone resources and minimizing environmental damage. Compared to natural aggregates, bottom ash recycled aggregates are more prone to cracking, have higher abrasion rates, lower specific gravity, and higher water absorption ability. Nonetheless, they still meet the relevant aggregate standards. According to regulations in Taiwan, aggregates that come from recycled bottom ash can be widely used for road base layers, controlled low strength material (CLSM), bricks, cement raw materials, and landfill cover soil. This would not only transform waste into resources but also broaden the reuse pathways for bottom ash, further promoting the concept of a circular economy.
Requirements and regulations for bottom ash reuse
When bottom ash is transported out of the EfW plant, it is considered as industrial waste and must be strictly managed according to the Waste Disposal Act. Its reuse follows the "Management Methods for the Reuse of Bottom Ash from Waste Incineration Plants." According to regulations, EfW plants are required to test the total toxic equivalent concentration of dioxins and the leaching characteristics of heavy metals quarterly, and provide the test results to bottom ash reuse organizations as a reference for adjustments in process parameters. Additionally, the reuse organizations must conduct tests at least once every 500 metric tons, including the same testing items mentioned, to ensure that the reuse process is environmentally safe.
Multiple benefits of bottom ash reduction measures
The composition ratio of bottom ash varies depending on the waste composition and the combustion efficiency of the EfW plant. To effectively minimize bottom ash generation, management practices can be implemented in three stages: front-end, mid-stage, and back-end. In the front-end stage, waste inspections can deter poor waste disposal practices, such as the inclusion of non-combustible waste—like sand, clay, or metals—thereby reducing the generation of bottom ash at the source. In the mid-stage, operators must regularly review the combustion conditions inside the furnace, while ash crane operators monitor the quality of bottom ash. If unburned waste is detected, they must immediately notify the control room and adjust combustion control parameters (such as furnace grate speed, feed rate, and excess air ratio) to ensure complete combustion of waste and reduce the amount of bottom ash. In the back-end stage, the installation of bottom ash sorting facilities allows for the recovery of valuable metals, which reduces the amount of bottom ash transported out of the plant, thereby lowering carbon emissions during transportation and cutting outsourcing treatment expenses, ultimately enhancing the value of resource reuse.
Bottom ash sorting arrangement: A case study of the Gangshan EfW Plant
The design and arrangement of the bottom ash sorting facilities at the Gangshan EfW Plant have primarily taken into account of the following aspects:
1.Drying and storage plan for bottom ash
The unburned components in bottom ash are primarily large-sized ferrous metals, with a high moisture content after the ash discharge process. To reduce the moisture content, the team tried to improve ventilation or shortening the cooling time of the bottom ash, so as to enhance the moisture evaporation rate. Before being transported out of the plant, the bottom ash is stockpiled and dried in situ. To achieve this, the bottom ash storage pit is divided into the following areas: a temporary storage area for discharged bottom ash, a drying area for stockpiled bottom ash, and a storage area for sorted bottom ash, as shown in the following figure.
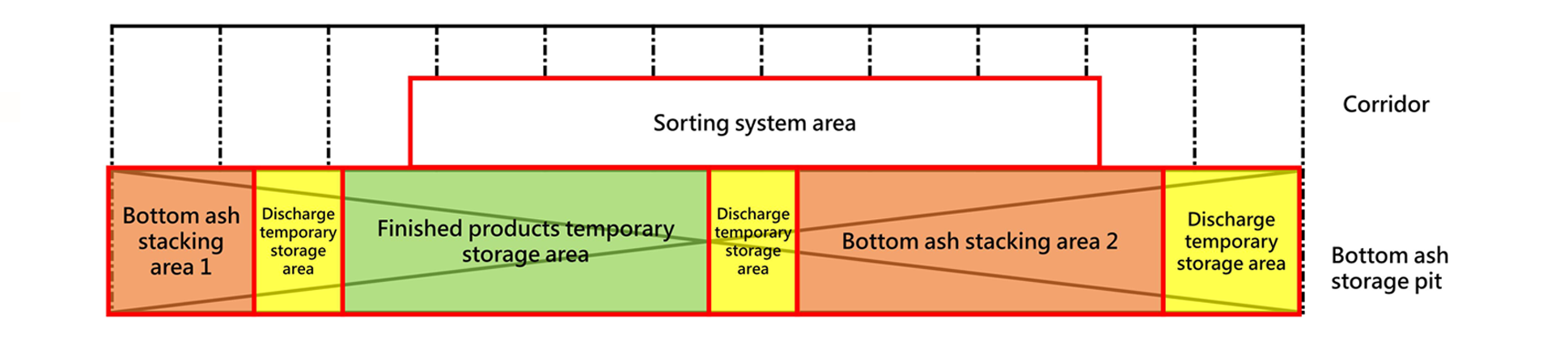
Schematic diagram of bottom ash storage pit planning
2.Design and processing workflow of bottom ash sorting facilities A bottom ash sorting facility with a processing capacity of 15 metric tons per hour has been installed in the ash corridor, with the workflow outlined below. This facility can effectively reduce the content of ferrous metals, non-ferrous metals, and unburned materials in the bottom ash, thereby improving its quality. The screened ferrous and non-ferrous metals will be recycled by reuse organization. The specific steps are as follows: (1)Coarse vibrating screen: This helps screen out large unburned materials and returns them to the waste pit. (2)First magnetic separator: This is installed above the bottom ash vibrating conveyor to separate large-sized ferrous metals. (3)Ballistic separator : This helps screen materials with a particle size smaller than 19 mm into the storage pit to meet the size standards for recycled aggregates. (4)Second magnetic separator: This helps recover ferrous metals again to further enhance recovery efficiency. (5)Eddy current separator: This is used to screen non-ferrous metals in medium-sized bottom ash for recycling. 3.Monitoring system setup Given that bottom ash contains many large objects and has a high moisture content, multiple monitoring screens are set up to enable operators to quickly identify and address issues. Cameras are installed at key equipment locations, such as above the bottom ash vibrating conveyor, coarse vibrating screen, magnetic separator, and eddy current separator.
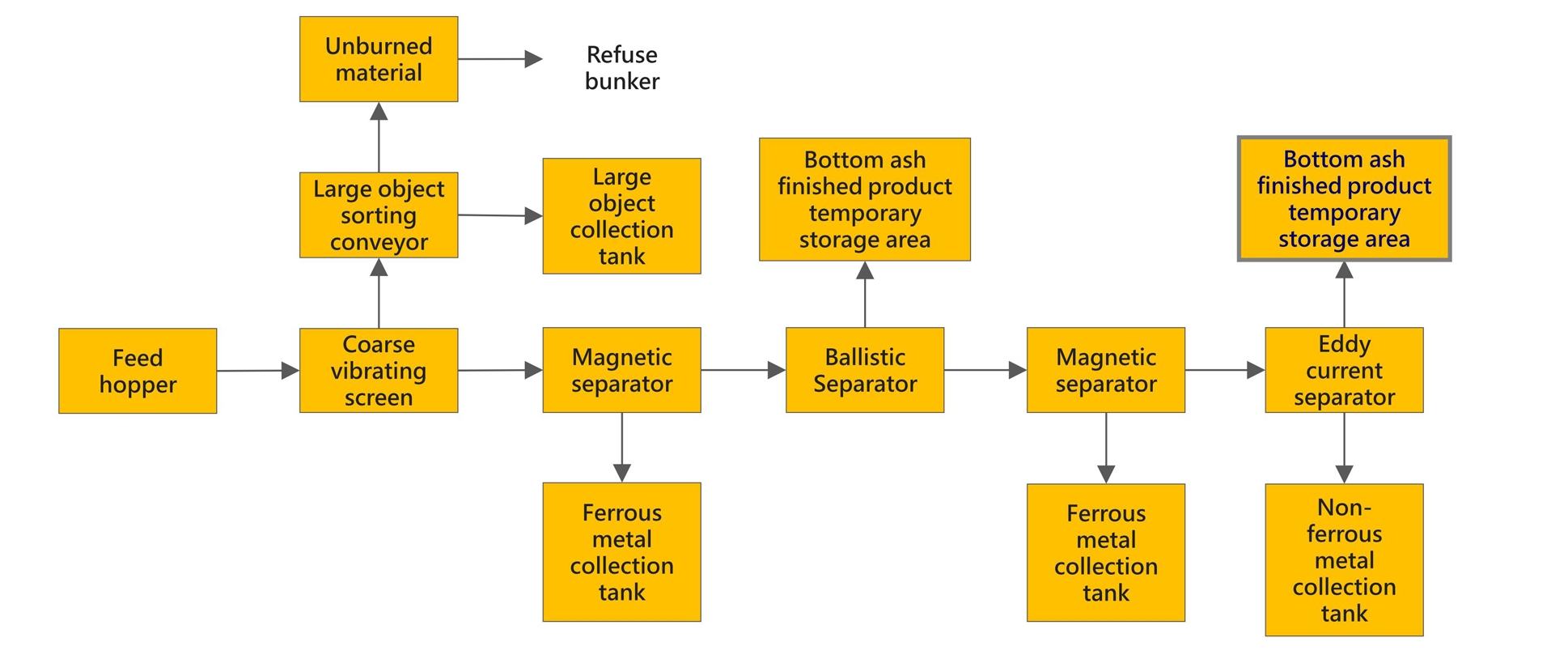
Flow chart of bottom ash sorting process
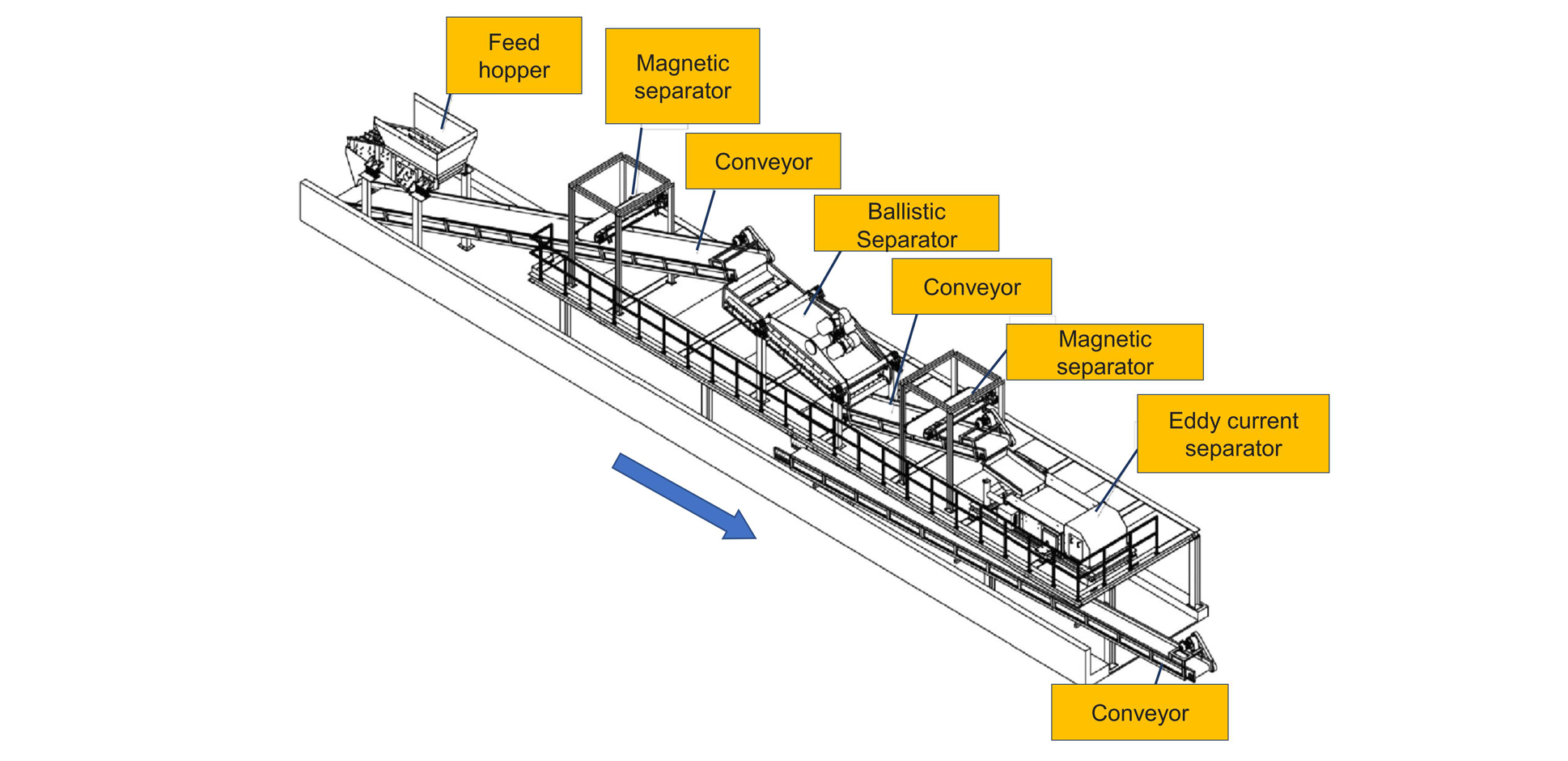
Schematic diagram of bottom ash sorting system
Benefits of the bottom ash sorting system at the Gangshan EfW Plant
The bottom ash sorting facility at the Gangshan EfW Plant completed its trial operation in 2024. After 10 months of operation, it has yielded significant benefits, including: 1.Metal recovery and reduction of carbon emissions from recycled products The facility successfully recovered valuable metals, including 1,380 metric tons of iron and 220 metric tons of aluminum, boosting the circular economy. The carbon footprint (Note 2) of the recycled metal products is lower compared to that of virgin metal products, reducing carbon dioxide emissions by a total of 4,180 metric tons. 2.Reduction in bottom ash and transportation carbon emissions After screening and separating ferrous and non-ferrous metals, the amount of bottom ash transported out of the plant was reduced by 1,600 metric tons, resulting in a decrease in carbon dioxide emissions during transportation by 23,500 metric tons. 3.Reduction in unburned material proportion The proportion of unburned material in the bottom ash before being transported out of the plant was reduced to only 0.7%, complying with the "Management Methods for the Reuse of Bottom Ash from Waste Incineration Plants" regulations, and meeting the requirement that the proportion of unburned material must be less than 2%. 4.Optimization of bottom ash production rate Under the existing waste intake plan, the bottom ash production rate was reduced from 17.23% before sorting to 14.71% after sorting. As a practitioner of the circular economy, ECOVE’s four main business pillars—waste management, recycle and reuse, renewable energy, and electromechanical maintenance and improvement—are closely aligned with the principles of net-zero sustainability. Moving forward, ECOVE will continue to promote and capitalize on the advantages of resource cycling initiatives, expand its influence, and offer diverse and sustainable economic solutions to clients and the government. Together, we will tackle climate change and achieve the objectives of sustainable development and net-zero emissions. Note 1: Shih-Chin Sun and Pei-Te Chueh (2005), “Introduction to the Maturation Methods of Incineration Bottom Ash,” Industrial Pollution Control, Issue 94. Note 2: Carbon Footprint Information Platform