Eco-friendly Innovation
綠色創新
Energy Resource Center with Highest Power Generation Efficiency in Taiwan: A Case Study of Taoyuan Biomass to Energy Center
The Taoyuan City Biomass to Energy Center (hereinafter referred to as "the Center") was established by the Taoyuan City Government to address the city's waste disposal issues and to align with the policies of "circular economy" and "biomass waste resource recovery." The Center was constructed and operated through a Build-Own-Transfer (BOT) model, with the concessionaire selected through a public bidding process. Following the public bidding and evaluation, a consortium led by the parent company, CTCI Corp., in partnership with its subsidiary, ECOVE Environment Corporation(ECOVE), and Evergreen Steel Corporation, successfully secured the project. CTCI was responsible for the construction, while ECOVE was responsible for the operation and management. The Center is the first nationwide integrated biomass to energy center that combines heat treatment facilities, anaerobic digestion facilities, and landfills. It aims to reduce, reuse, and recycle waste, effectively implementing the concept of a "circular economy" and becoming a demonstration park for the bioenergy industry and resource circulation.
The facility is the first thermal treatment plant in Taiwan to achieve certification for renewable energy generation equipment and boasts the highest power generation efficiency in Taiwan.
The Center's thermal treatment facility design incorporates advanced technologies from abroad, including: waste pre-treatment technology, high combustion efficiency and high boiler efficiency technology, providing an enhancement on the performance by integrating related system. This significantly increases the power generation efficiency of the thermal treatment facility and fully recovers renewable energy from waste. Based on relevant regulations such as the "Renewable Energy Development Act" and the "Regulations for Installation and Management of Renewable Energy Generation Equipment", the facility was certified as a waste power generation facility. After review, it met the requirements and became the first thermal treatment plant in Taiwan to obtain renewable energy power generation equipment certification. The following introduces the performance of related system equipment.
• Waste Pre-treatment System for Enhanced Heating Value and Reduced Pollution
The Center's thermal treatment plant adopted a double bunker design, with one bunker in front and one in the back, making it Taiwan’s the first plant to deploy such design. The front bunker is used to receive and store incoming waste, while the rear bunker is used to store waste after it has been treated by the waste pre-treatment system. The waste is then retrieved from the rear bunker by a waste crane and fed into the incinerator.
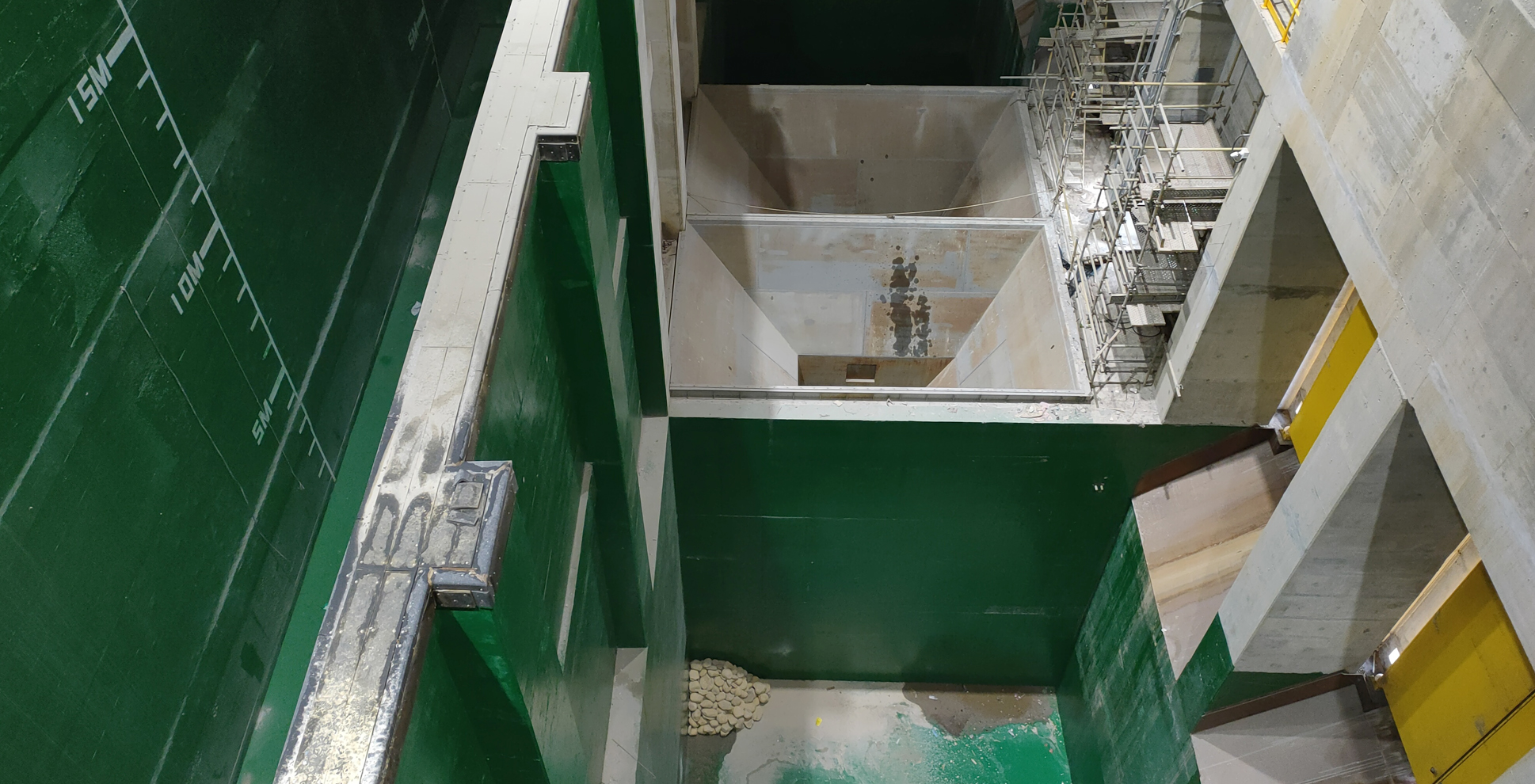
The Center's double bunker design
The waste pre-treatment system utilizes a two-line configuration (2 lines × 30 tons/hour). Waste are first processed through a double-shaft crusher, reducing their size to approximately 100 mm. Subsequently, a magnetic separator and an eddy current separator are employed to recover ferrous and non-ferrous metals, further eliminating metallic and other non-combustible materials. This process homogenizes the size and composition of the waste, resulting in several benefits: increased heating value and combustion efficiency, reduced pollution, decreased bottom ash, and minimized heat loss from the bottom ash.
• Incineration and Waste Heat Recovery Boiler System with High Combustion Efficiency and High Boiler Efficiency
The Center's thermal treatment plant utilizes an incineration and boiler system from a leading Japanese technology provider. Considering the characteristics of the waste received by the Center, the system is designed with a heating value of 3,000 kcal/kg. To accommodate a higher heating value within the designed range, a water-cooled grate has been installed in the main combustion zone. This prevents localized high temperatures from damaging the furnace grate and enhances operational efficiency. Furthermore, an advanced combustion automatic control program is integrated to achieve optimal combustion with low excess air, reducing exhaust gas volume and heat loss. The hot water recovered from the water-cooled grate is then used to preheat the primary air through a heat exchanger, effectively recovering waste heat. The side walls of incinerator are constructed with welded pipe water walls, which not only increase heat recovery efficiency but also reduce the formation of sintered materials. The boiler steam temperature has been increased from the previous design of 400℃ to 430℃, increasing steam enthalpy and improving power generation efficiency.
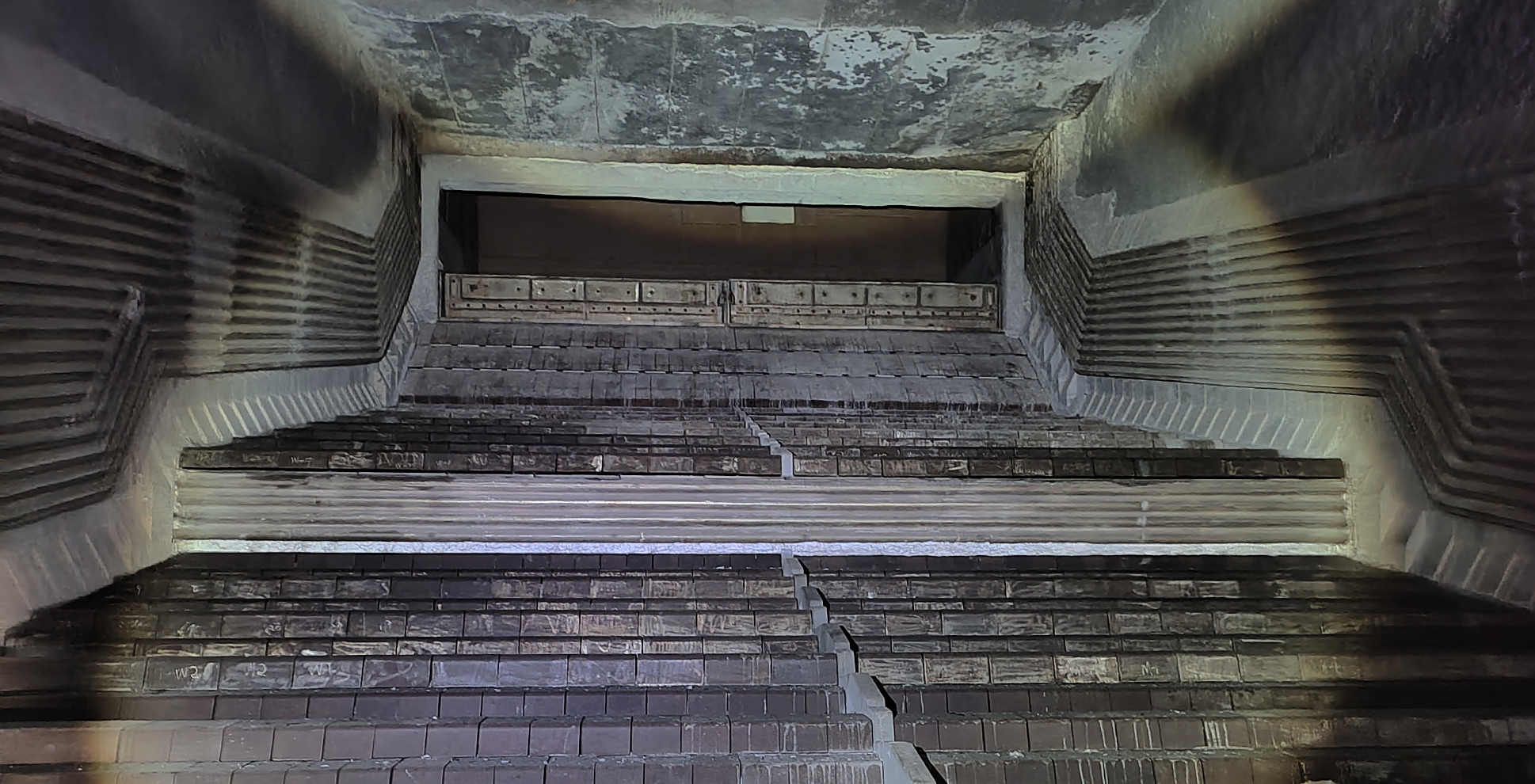
Water-Cooled Grate and Water-Cooled Walls
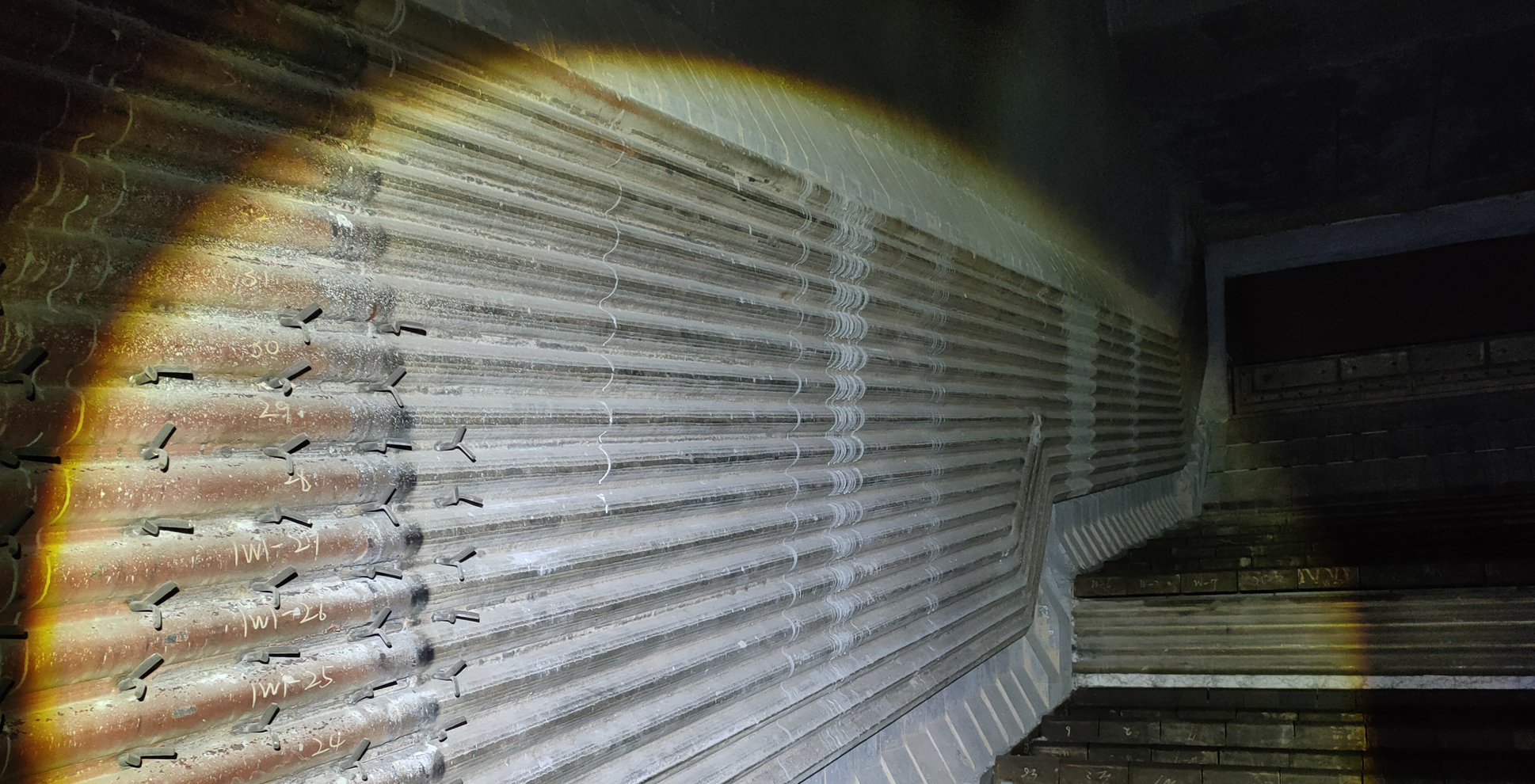
Water-Cooled Grate and Water-Cooled Walls
• High-Efficiency Flue Gas Treatment System with Heat Recovery
The thermal treatment plant in the Center are designed to meet EU emission standards, utilizing advanced German technology systems. Taking into account factors such as acid removal efficiency and the generation of secondary waste, a dry sodium bicarbonate acid gas removal process with low excess reagent dosing is employed. The sodium bicarbonate is finely ground into small particles before reacting with acid gases in the flue gas reaction tower. To minimize the amount of unreacted sodium bicarbonate in the reaction product, a system for recycling and reusing residues has been added. This effectively reduces the concentration of acid gases (HCl, SOx) in the exhaust and the production of secondary waste, achieving both emission and waste reduction.
The Center is equipped with a Selective Non-Catalytic Reduction (SNCR) system, which is automatically controlled by a sonar temperature monitoring system. This system injects a reducing agent (liquid urea) at various heights and locations to ensure that the denitrification process occurs within the optimal reaction temperature range, achieving the best possible NOx removal efficiency. Additionally, a Selective Catalytic Reduction (SCR) reaction tower is installed, which uses the residual ammonia from the previous process for reduction reactions, effectively removing both dioxins and NOx simultaneously.
The exhaust gases in the dry flue gas treatment system are maintained at a high temperature of approximately 185°C, and a low-temperature SCR system is employed, eliminating the need for reheating the exhaust gases. An external economizer is installed in the later stage of the flue duct, lowering the temperature of the exhaust gases exiting the baghouse filter to 150°C. The recovered waste heat from the exhaust gases is then used to heat the feedwater, further enhancing energy recovery.
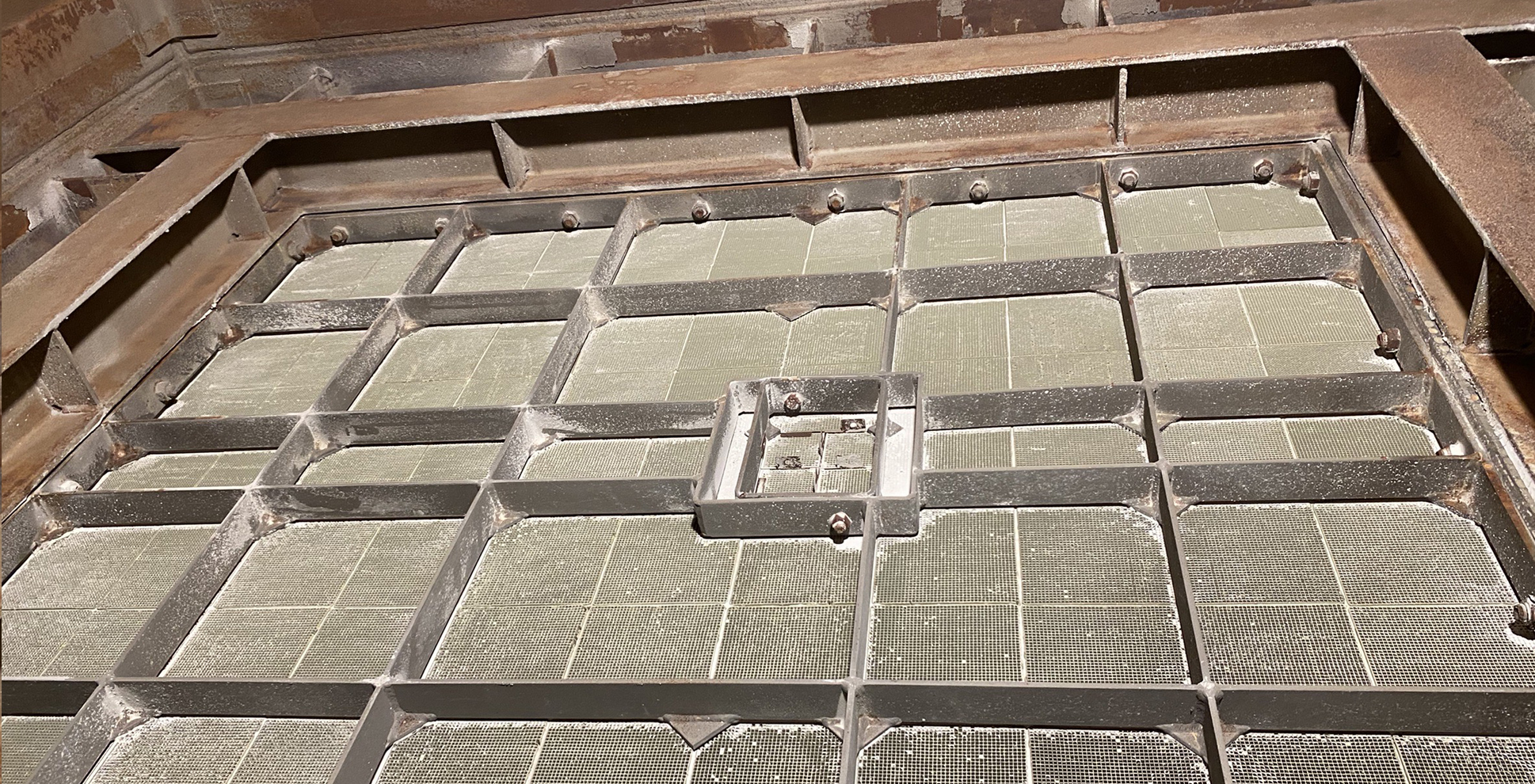
Selective Catalytic Reduction (SCR)
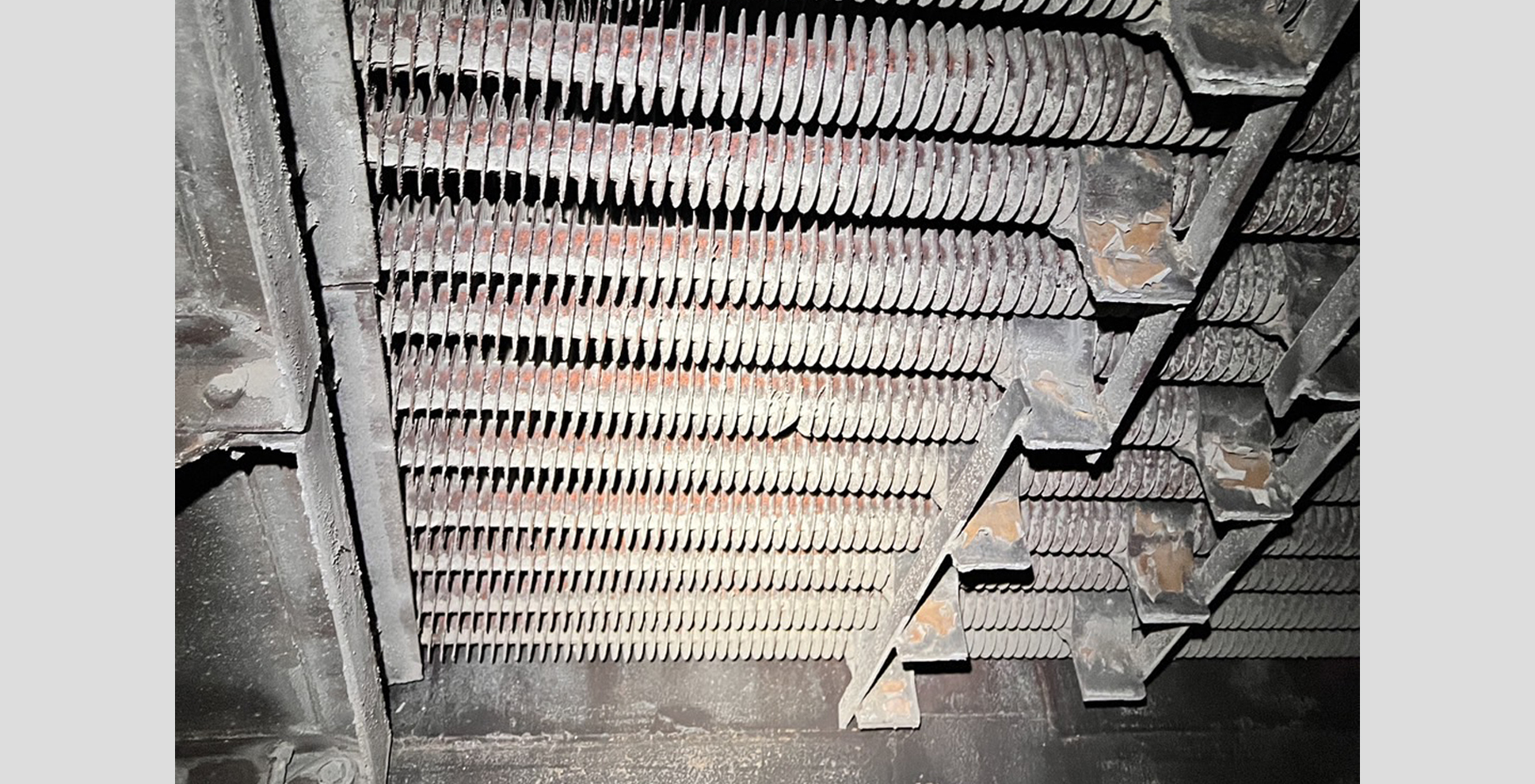
External Economizer in the Later Stage of the Flue Duct.
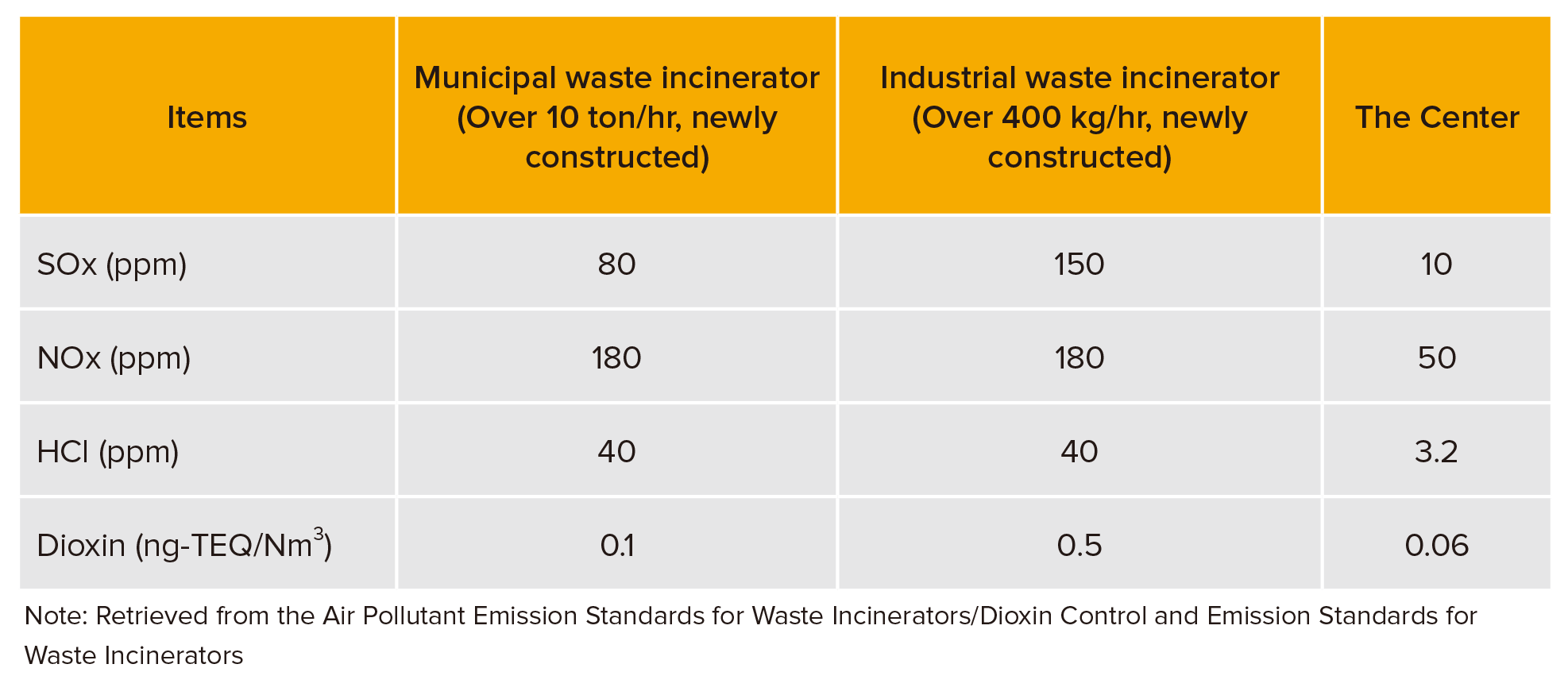
The emission standards for incinerators and the designed emission values of the Center.
• High-Efficiency Steam Turbine Generator and Air-Cooled Condenser
The Center’s thermal treatment plant utilizes a high-efficiency steam turbine generator, which significantly reduces the dryness of the outlet steam while recovering more thermal energy from them. With a high-efficiency air-cooled condenser designed for an ambient temperature of 34°C and the turbine outlet pressure reduced to 0.15 kg/cm²A, this performance surpasses most domestic incinerators, enabling greater recovery of steam thermal energy. The residual heat from the turbine is used for preheating both primary and secondary gas air heater.
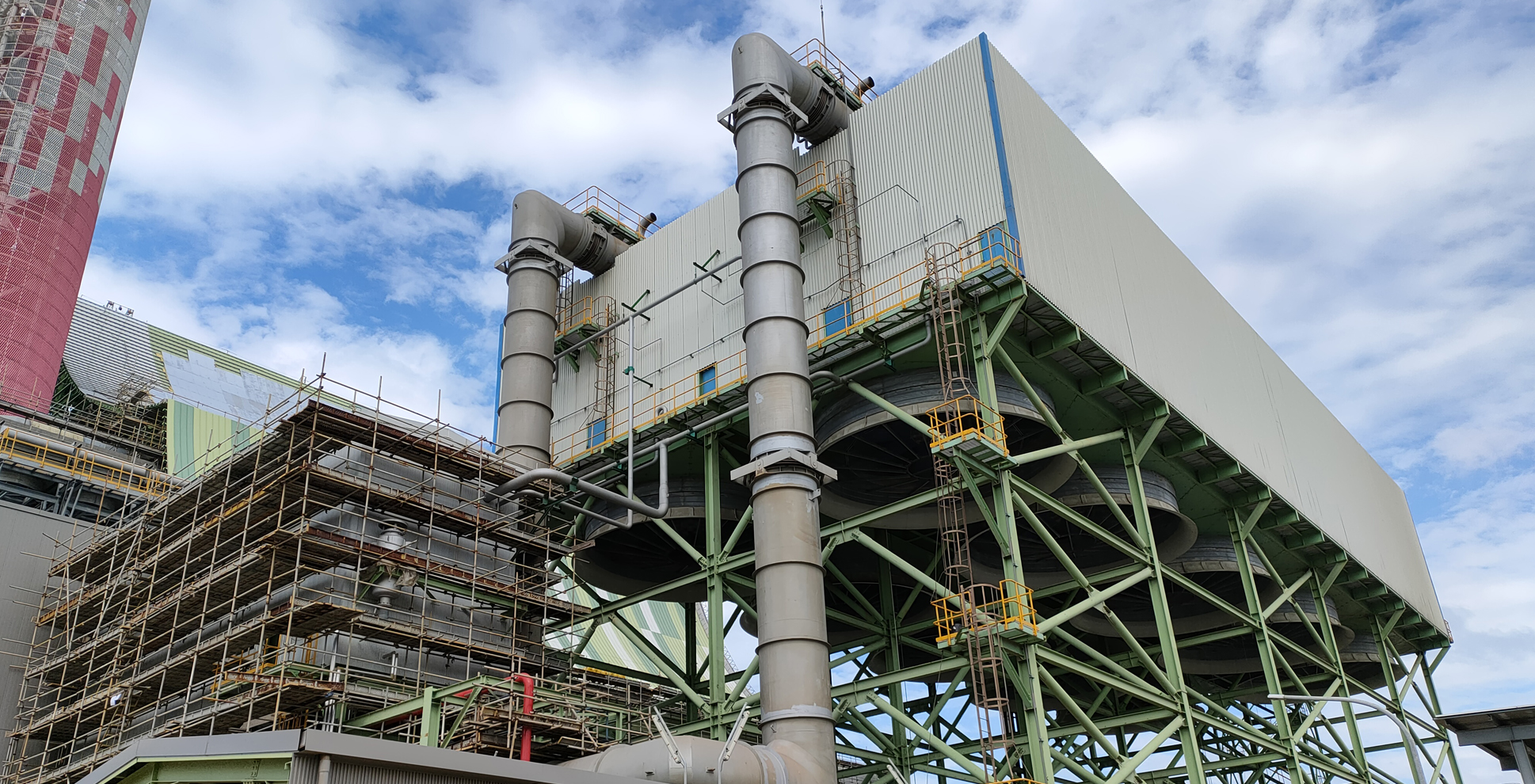
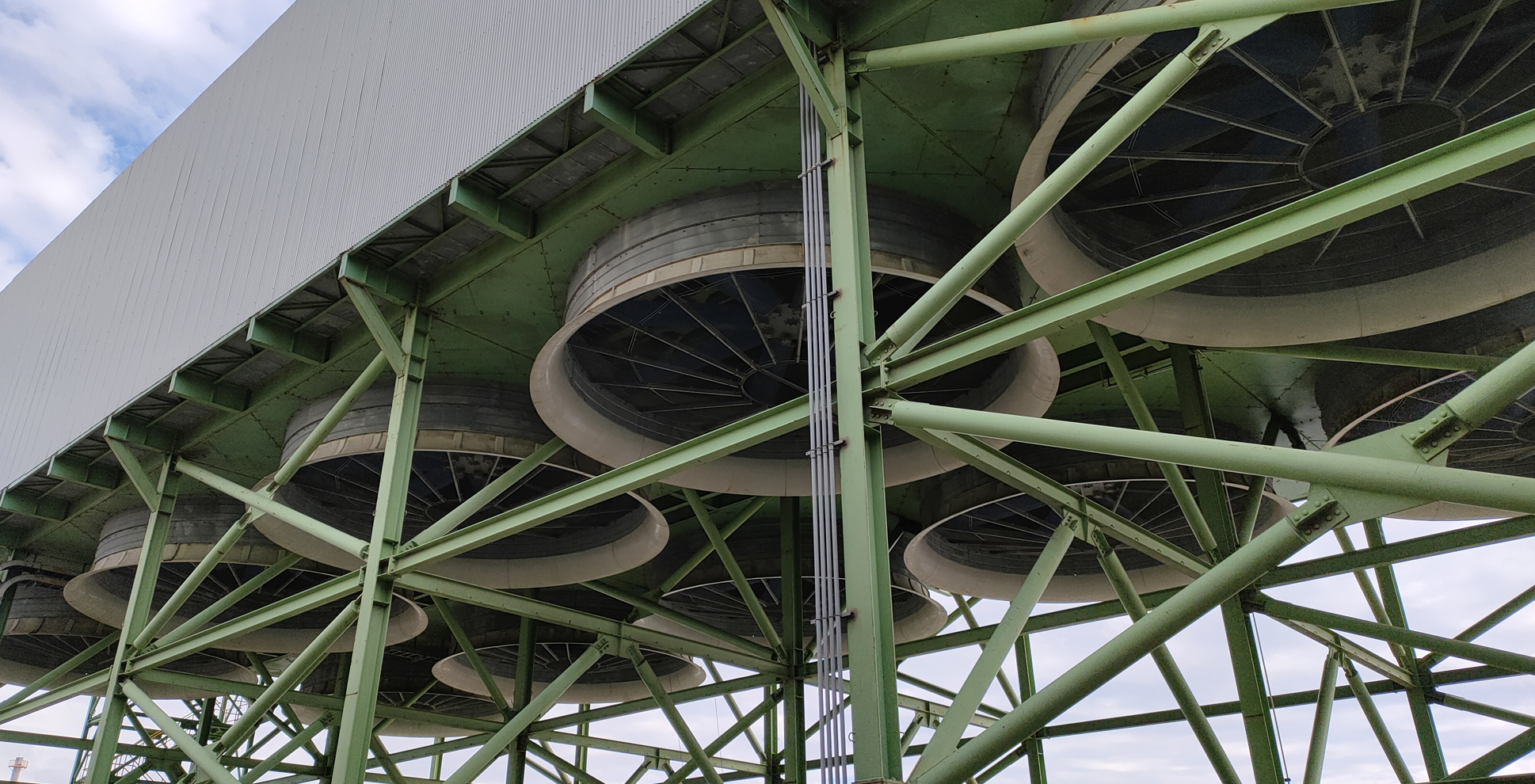
Currently, the operating incinerators in the country have relatively low power generation efficiency, averaging around 21%. To achieve the high power generation efficiency target for the Center's thermal treatment facility, energy recovery and electricity consumption for each system were key considerations during the design phase. The facility focuses on the comprehensive integration and reuse of waste heat from flue gases, steam, and other energy sources. After implementing various performance enhancement measures, the power generation efficiency has been significantly improved to approximately 28%, which is well above the standards for domestic incinerators and renewable energy waste-to-energy equipment. This makes it the highest-efficiency thermal treatment facility in the country today.
The First Thermal Treatment Plant in the Country Complying with EU Operating Standards
To ensure high quality of life and environmental friendliness, the Center’s thermal treatment facility is designed according to EU standards and incorporates advanced technologies from Germany, Japan, and other countries. In addition to the flue gas treatment system being designed to meet EU standards, the operational management model is also the first in the country to comply with relevant EU operational regulations. Key management measures include: furnace temperature management, flue gas emission management, and continuous monitoring of flue gas emissions.
Anaerobic Digester for Kitchen Waste Biogas Energy Production
The Center’s anaerobic digester system includes equipment for kitchen waste pretreatment, buffer tank, digester, biogas desulfurization, biogas power generation, dewatering machine, and flare. The facility accepts organic waste such as kitchen waste and manure. The kitchen waste undergoes a pretreatment process to remove non-biodegradable contaminants like plastic bags and gravels. It is then processed through a hammer mill and pumped to the buffer tank for acidification. Subsequently, the organic material is pumped hourly in a controlled manner to the anaerobic digester. The organic matter is digested by methanogenic bacteria to produce biogas, which is sent to a biogas generator for power generation. A heat recovery module is also installed on the generator to capture and reuse waste heat. The sludge from digester is pumped to the dewatering machine for solid-liquid separation. Since the digestate and liquid digestate are nutrient-rich organic materials, priority is given to finding methods for reuse (such as application to farmland or as liquid fertilizers) to achieve the goal of complete recycling and reuse.
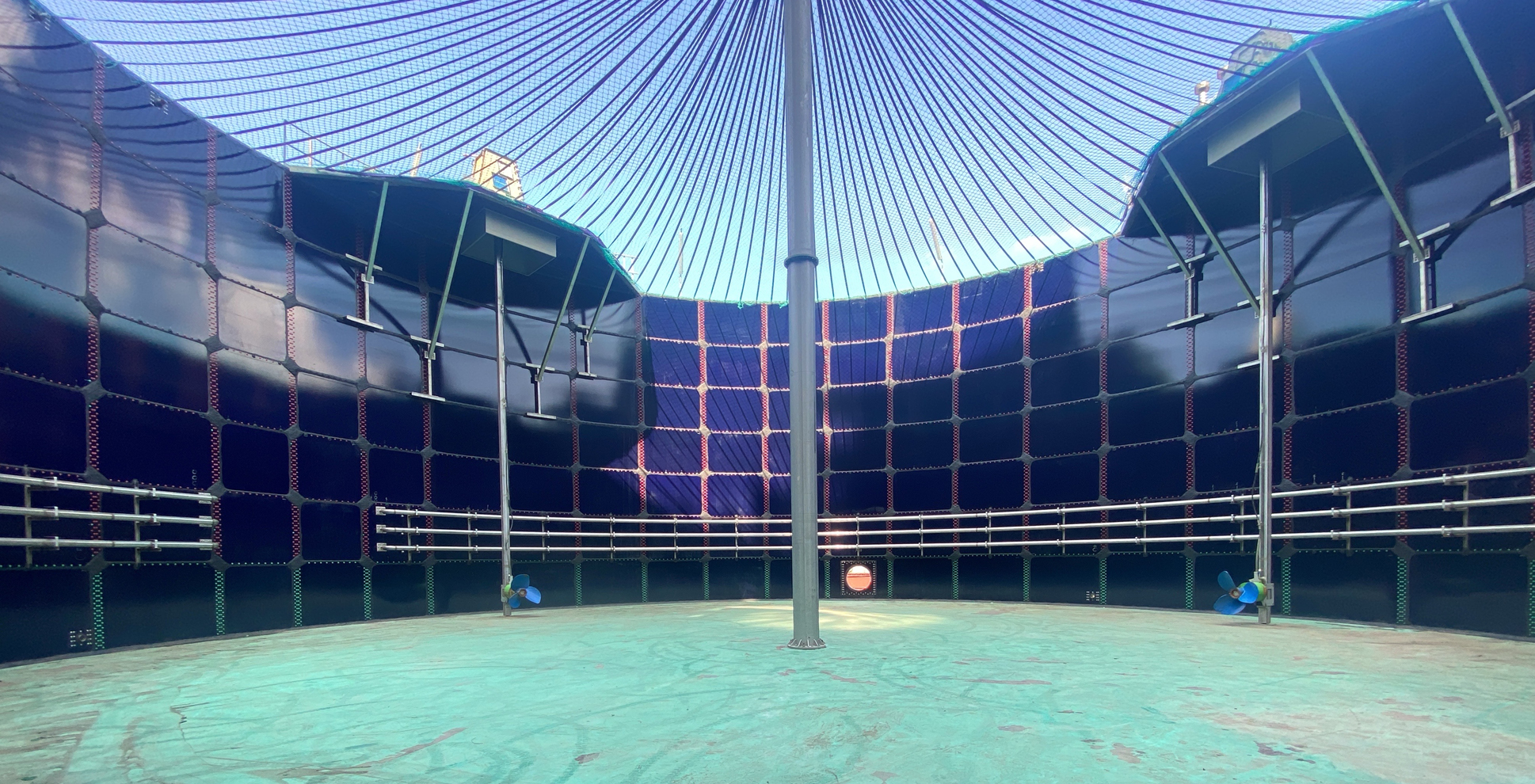
Interior of the Anaerobic Digester (Construction Phase)
Landfill Integrated with Waste Resource Recovery Technology Development
In line with the principles of proper waste management in environmental technology parks, the Center's landfill is primarily used for the disposal of stabilized fly ash generated by the Center and inorganic sludge from the water treatment and wastewater treatment facilities managed by the industrial zone. As resource recovery technologies continue to advance, the amount of waste disposed of in the landfill will gradually decrease, extending the landfill's operational lifespan. In the future, once the landfill is closed and rehabilitated, it will become an open recreational space rich in ecology and greenery, serving as a demonstration and educational site for waste reduction, recycling, and reuse.
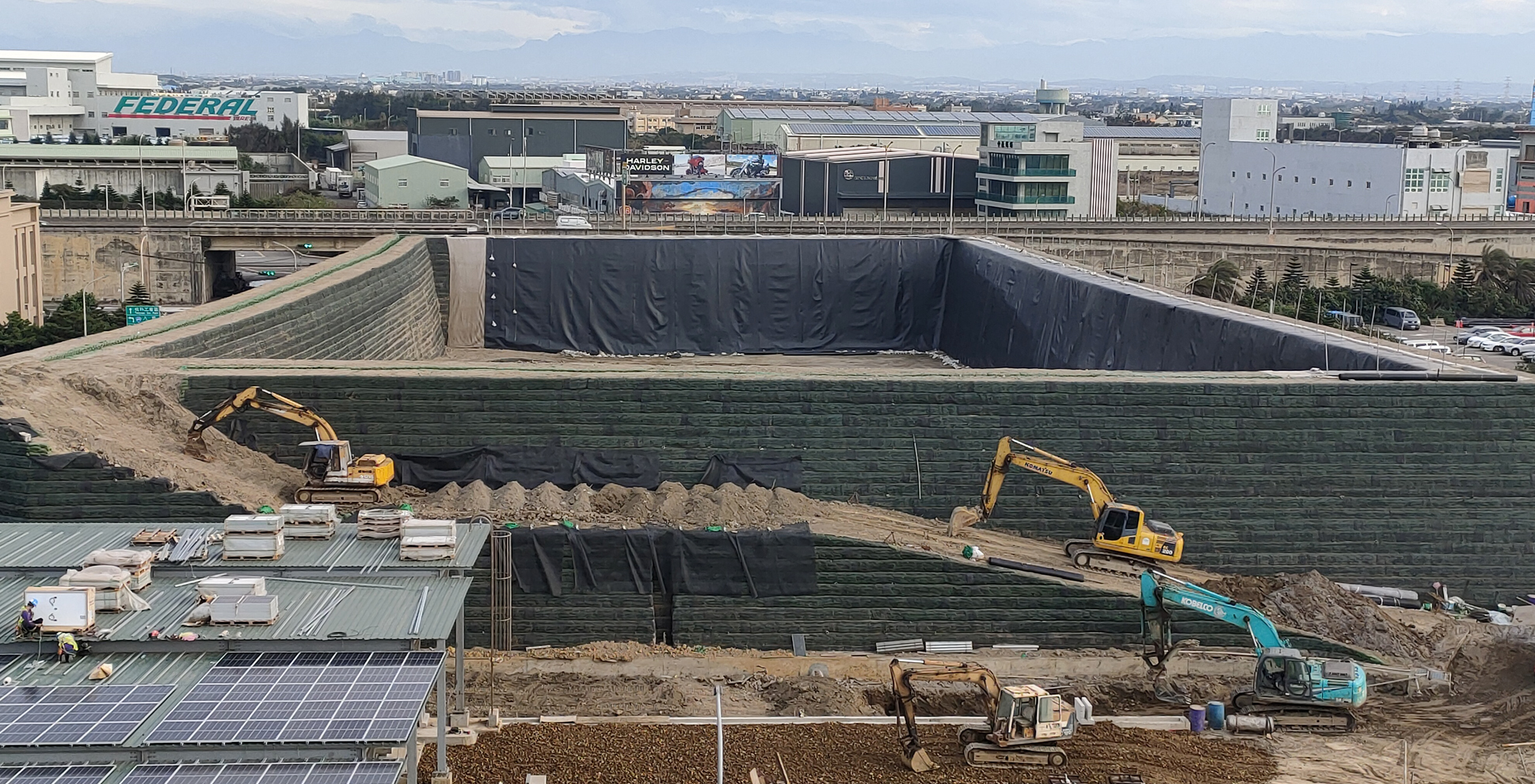
The Center’s Landfill (Construction Phase)
Leading the Way to a New Generation of Circular Biomass to Energy Centers
It is the Center’s goal to become a sustainable circular processing facility with zero-waste, low-pollution, and diversified treatment. In the future, the operational team aims to provide comprehensive solutions and herald the arrival of a new era in waste management, focusing on the principles of the circular economy. . We hope that by implementing the principles of circular economy, waste will no longer be considered as waste but as a usable energy resource (Energy from Waste). Our goal is to realize our vision through the three cycles of "Waste Recycling, Water Recycling, and Energy Recovery," making the Center a low-carbon, sustainable "Green Engineering" project.