Eco-friendly Innovation
綠色創新
Improving VOCs Recovery to Reduce Environmental Impact
CTCI Advanced Systems Inc. (CTCI ASI), a company under CTCI’s Group Intelligent Solutions Business (GISB), is a leading intelligent solutions provider in Taiwan which has long been focused business in the oil refining and petrochemical industries. Due to the fact that factories frequently encounter production problems in relation to process, energy, quality, and safety, this article takes the waste solvent recovery of a special chemical plant implemented by CTCI ASI as an example to share how the company optimizes production process using core technology in virtual plant and process optimization to provide clients with optimal process solutions. This has effectively solved the owner's dilemma: benefits generated by process optimization not only improve the production process, but foster sustainable development and fulfill corporate social responsibility with the waste solvents reduced.
Solvent Recovery: Reduce Environmental Hazards & Save Production Costs
The specialty chemical factory project implemented by CTCI ASI produces UV absorbers and light stabilizers in batches, volatile organic compounds (VOCs) will be added in the front-end process. The organic solvent remaining in the powder will be evaporated by the drying system in the back-end process, and then the organic solvent gas will be condensed and recovered through the condensation system, so as to achieve solvent recovery and reuse. The schematic diagram of solvent recovery in the back-end process is shown in the figure below:
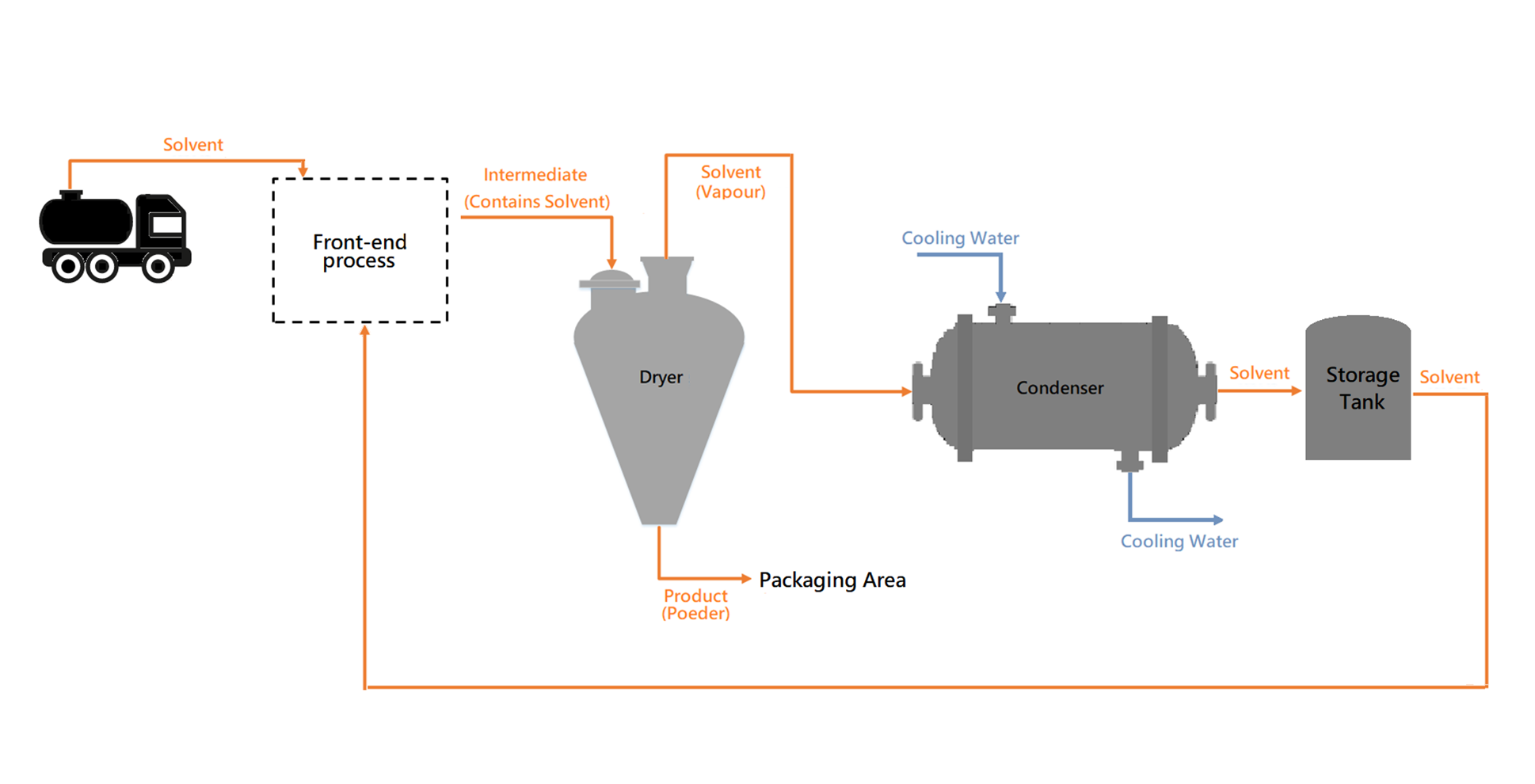
Schematic diagram of solvent recovery process.
Due to factors such as process operating and equipment conditions in this project (e.g., worn-out equipment, poor sealing), some organic solvents will escape into the environment, affecting the recovery of organic solvents. The CTCI ASI team established a virtual factory with process simulation software, which helped analyze potential bottlenecks in the process, providing solutions to carry out process simulation optimization and on-site revamping, effectively increasing the solvent recovery rate from 17% to 80%. This significantly reduces impacts to the environment caused by VOCs emissions, and save the cost of solvent procurement in the front-end process with increased efficiency in solvent recovery. In so doing, a win-win situation for promoting the economy and reducing environmental pollution may be achieved.
Virtual Factory: Locating Process Bottlenecks & Achieving Green Production
In order to establish a virtual factory in this project, CTCI ASI project team implemented the following procedures: Information and data collection, physical properties and data analysis, virtual factory establishment, feasibility assessment, providing solutions, improvement plans implementation, and, finally achieving optimization benefits collectively with the owner, as shown in the figure below.
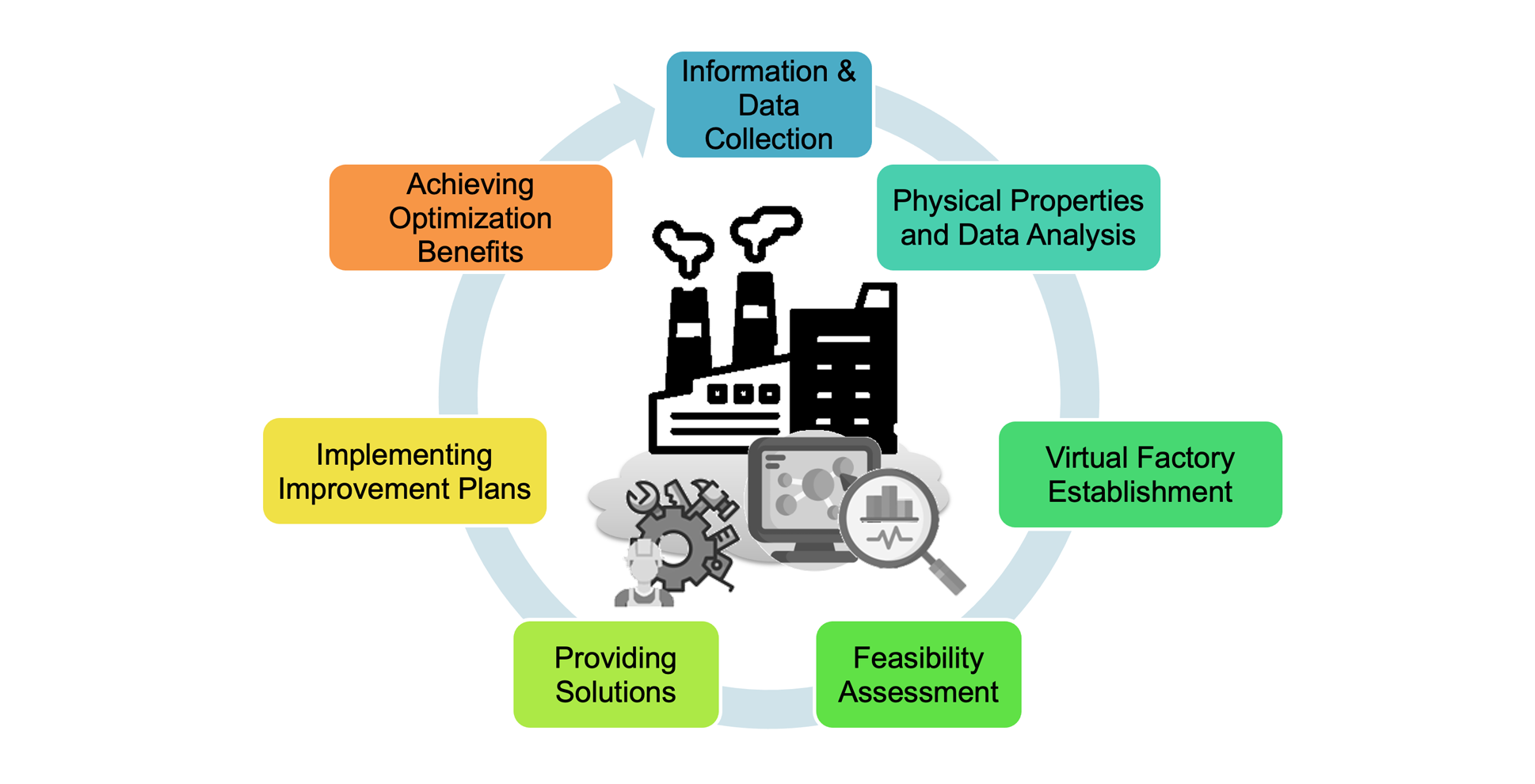
Schematic diagram of virtual factory execution.
1.Information and Data Collection Collect the existing design data of the factory, including process flow diagram (PFD), process piping and instrument flow diagram (P&ID), equipment specification drawings, instrument specification sheets, process historical data, and process operation status discussion and site survey. 2.Physical Properties and Data Analysis Based on the above information, the physical properties and thermodynamics of various process conditions are verified, and historical operation data is used to conduct exploratory data analysis. 3.Virtual Factory Establishment Using the plant data provided by the client, including design document diagrams and on-site operation history data, the process simulation software can start building a virtual factory, which is capable of simulating anything—from a single equipment to a complete process section. In this waste solvent project, we use the information provided to build a virtual factory for the organic solvent recovery process section in the back end, as shown in the diagram below.
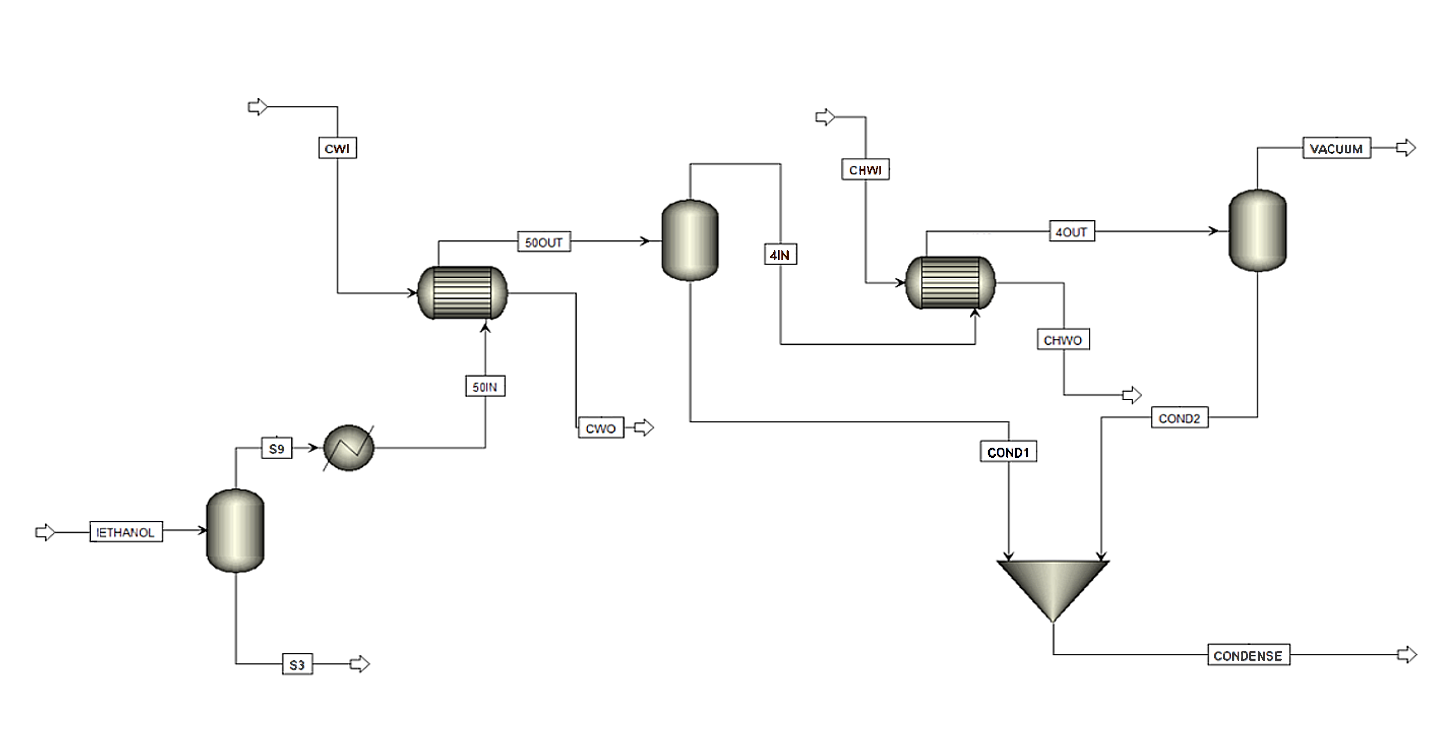
Virtual factory diagram.
4.Feasibility Assessment Combined with virtual factory and process knowledge, the simulation results are used to analyze potential bottlenecks in the process and evaluate subsequent solutions. In this project, bottleneck that affects solvent recovery is the ineffectiveness of the solvent vapor condensation system, which would result in low recovery efficiency. 5.Providing Solutions After feasibility assessment is completed, an optimal solution will be provided according to the current factory operation status. Given that the project is to make a change to the existing process and production line, and the production schedule needs to be arranged in accordance with the market demand, we must ensure that the revamping period is not too long, and that the revamping scope not too broad. After considering the comprehensive situation of on-site revamping costs and owner's production scheduling requirements, CTCI ASI project team draws up the best improvement plan to the condensing system. 6.Implementing Improvement Plans Based on the optimal solution proposed, we implement improvement plans by carrying out pipeline revamping and operating conditions adjustment. Regarding pipeline revamping, the existing operation mode remains unaltered to facilitate changes of production line products in subsequent batch processes. While for different organic solvents, the condensing system can be adjusted back to the original mode when no large load is required to make operations flexible. 7.Achieving Optimized Benefits After completion of the revamping project, the organic solvent recovery rate has increased from 17% to more than 80%, significantly reducing volatile organic solvents from escaping. Meanwhile, we successfully assisted the client to reduce the environmental impact, and saved the amount of solvent purchased in the front-end process.
Conclusion
With core competencies in smart plants and process optimization, CTCI ASI successfully assisted clients to fix process bottlenecks with optimal solutions for factory revamping according to their needs and achieve waste reduction goals. We hope to make concrete contributions to the sustainability of the planet and fulfill corporate social responsibility.