Technology
技術分享
Pollution Reduction and Emissions Control: A Case Study on Enhancement of SNCR System at Xizhou EfW Plant
—Zi-Yi Zhan, Engineer at ECOVE Environment Services Corp., Group Resource Cycling Business —Jian-Hau Hung, Principal Engineer at ECOVE Environment Services Corp., Group Resource Cycling Business —Chien-Tsai Sung, Assistant Chief Engineer at ECOVE Environment Services Corp., Group Resource Cycling Business
The Xizhou Energy-from-Waste Plant (hereinafter referred to as Xizhou EfW plant) is an important public facility in Taiwan’s Changhua County that has been handling local residents’ general waste for over 20 years. Due to aging equipment, stronger public awareness on environmental protection, and more stringent environmental regulations, the local government has pressing needs to improve the EfW plant’s performance by cutting pollutant emissions and optimizing the selective non-catalytic reduction (SNCR) system. As part of CTCI’s Group Resource Cycling Business, ECOVE Environment Services Corp. (ECOVE ESC) leverages its extensive experience in EfW plant operation both domestically and internationally, as well as in annual maintenance and equipment upgrades. In this enhancement project, ECOVE has carried out hardware and software updates as well as system optimizations customized to the furnace type. Additionally, ECOVE has integrated and repurposed the existing equipment while implementing construction plans that ensured effectiveness and efficiency. Through comprehensive planning, the EfW plant aims to significantly reduce pollution and emissions while enhancing the efficient utilization of resources.
Technical Principles and Background of Enhancement Plan
The SNCR technology involves the injection of reducing agents, such as ammonia water or urea, into high-temperature flue gas, where they react with nitrogen oxides (NOx) to reduce NOx to nitrogen (N₂) and water (H₂O). This technology has been proven to be highly effective in reducing NOx emissions. Additionally, its absence of catalyst requirements and its straightforward system structure not only lower operational and maintenance costs but also mitigate environmental impacts. However, with the changes in the industry and population growth, the composition of waste has differed from the conditions under which the EfW plant was originally designed, leading to a decrease in the operational efficiency of the existing equipment. Beyond this, the Ministry of Environment (formerly known as the Environmental Protection Administration of the Executive Yuan) issued the Guidelines for Reducing Pollutant Emissions from Existing Fixed Pollution Sources in Level 3 Control Areas in July 2020. These guidelines stipulate that incineration facilities with a treatment capacity exceeding 10 tons per hour or a total designed treatment capacity exceeding 300 tons per day must complete necessary improvements by June 30, 2025, and ensure that the concentration of NOx emissions does not exceed 85 ppm. Therefore, the EfW plant must upgrade its system to improve the efficiency of removal and comply with the latest environmental regulations.
Design Planning and Enhancement Plan
To avoid excessively high ammonia concentrations that could cause odors, white smoke emissions from the chimney, and secondary pollution, while also improving the efficiency of energy resource utilization, the enhancement plan involves reassessing the installation position of the nozzle to ensure it is within the optimal reaction temperature range and has sufficient reaction time. Prior to the renovation, the EfW plant conducted a simulation of the flow field distribution within the boiler and found that the original height of the urea nozzle was FL+19.5 meters. This height was insufficient to meet operational requirements, resulting in the urea solution being unable to fully react with the high-temperature flue gas, thereby causing unnecessary waste. To optimize the reaction, the enhancement plan has adjusted the height of the nozzles to a two-tier configuration, setting at FL+27 meters and FL+24 meters, so that different load conditions could be accommodated: .When the boiler load is at 100%, the upper nozzle (FL+27 meters) will be activated, with an estimated 1.33 seconds in reaction time for the urea released from the injection point to the 850°C high-temperature zone. .When the boiler load is at 75%, the lower nozzle (FL+24 meters) will be activated, with an estimated 2.69 seconds in reaction time for the urea released from the injection point to the 850°C high-temperature zone. As both values exceed the standard range for general reaction time (0.5–1 second), this ensures that the reducing agent has adequate time to react completely, thereby minimizing the generation of ammonia slip. Furthermore, this enhancement plan has incorporated the operational logic into the DCS system, resulting in fully automated control and improved system stability and operational efficiency.
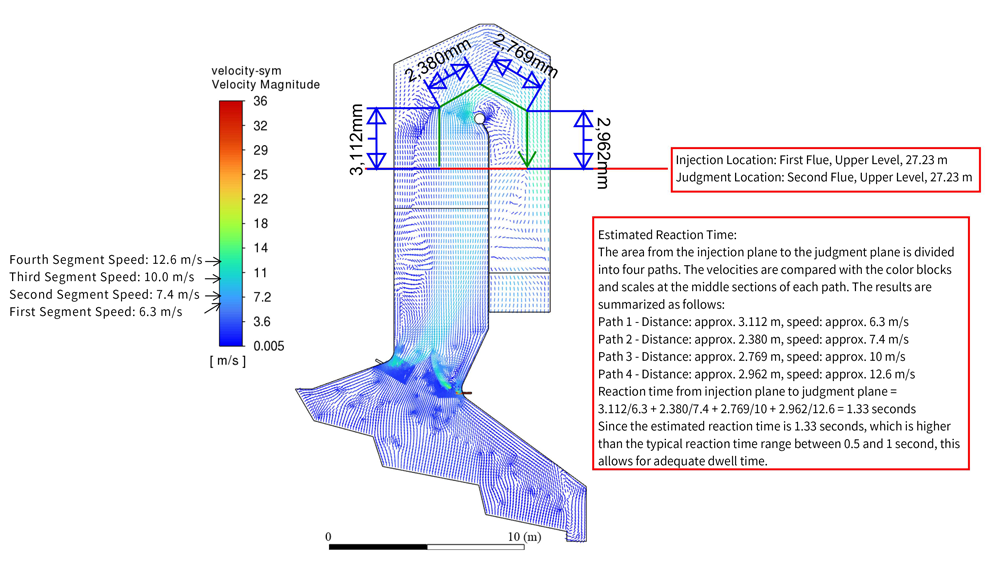
Simulation Diagrams of the FL+27 Meter Nozzle Configuration.
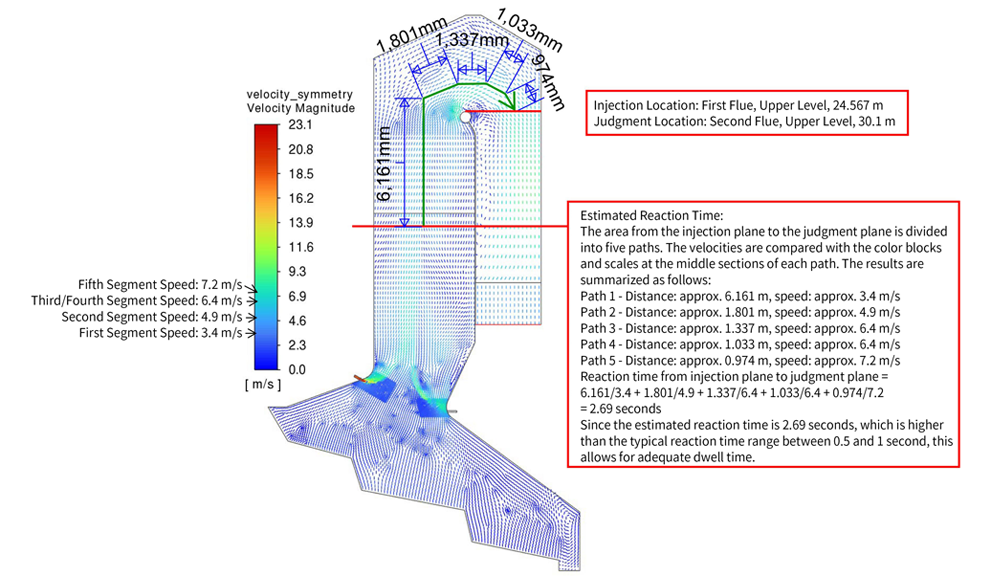
Simulation Diagrams of the FL+24 Meter Nozzle Configuration.
Before the enhancement, the original SNCR system had only four urea nozzles per furnace. Due to the limitations of the installation positions, the injected urea solution could not uniformly cover the entire surface of the flue gas duct, which adversely affected the efficiency of NOx removal. To address this issue, the enhancement saw each upper section equipped with six urea nozzles (two on each side wall and four on the front wall) and eight injection points. Adjustments can be made based on operational or maintenance requirements to ensure stable system operation and enhance the utilization efficiency of the reducing agent.
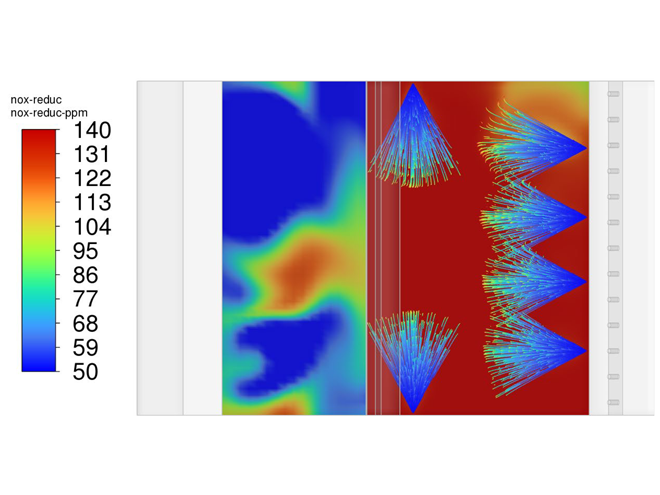

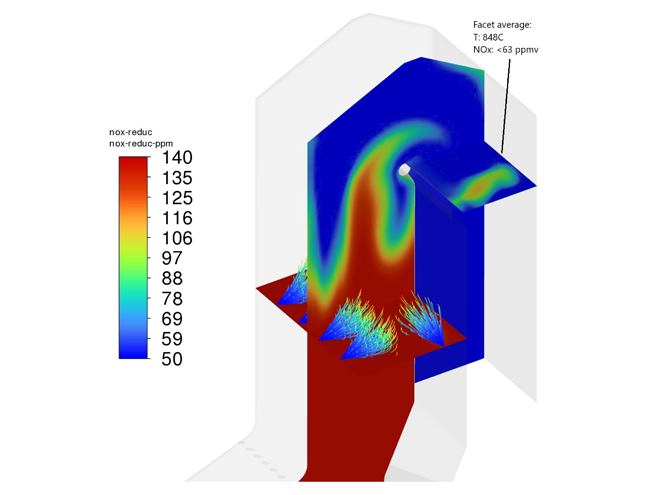
Equipment Regeneration and Efficient Resource Utilization
Along with the technological upgrade, it is necessary to consider the integration and reutilization of existing equipment. After evaluation, the original SNCR equipment was modified into a backup system through partial piping adjustments to mitigate operational interruption risk caused by equipment anomalies. Furthermore, the existing urea storage tank and its associated equipment, such as the agitator and heater, will be retained and optimized through piping integration into the new SNCR system. This approach ensures the optimization of NOx removal efficiency while minimizing equipment updates.
Hardware/Software Updates and System Optimization
The enhancement focuses on optimizing the SNCR system, which includes updating the equipment and adjusting outdated designs to ensure the stability of system operation. The original design positioned four nozzles at the same height and in close proximity to one another, leading to a considerable overlap in the chemical reaction area, which negatively impacted the NOx reduction efficiency. In addition, the old control panel only displayed basic operational status and alarm indicators, making it difficult for operators to understand the detailed condition of the equipment in real time. After the enhancement, the piping design in the nozzle area has been simplified, resulting in a clearer layout and a reduced risk of operational errors. At the same time, a float-type flowmeter was installed at the nozzle source, facilitating equipment maintenance and real-time monitoring. If a single nozzle requires maintenance, it can be independently isolated without affecting the overall system operation, thus preventing abnormal exhaust emissions due to equipment maintenance. Furthermore, the on-site control panel screen has been updated to display various information, including the flow rates of dilution water and urea, the operating status of equipment, and alarm notifications. It also facilitates the switching function between the primary and backup pumps, thereby automating the operational process and improving management efficiency.
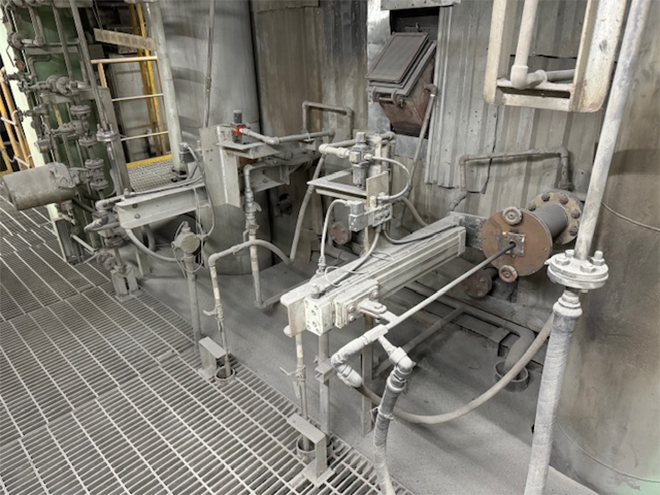
Insufficient spacing between the old urea nozzles results in less than optimal reaction efficiency.
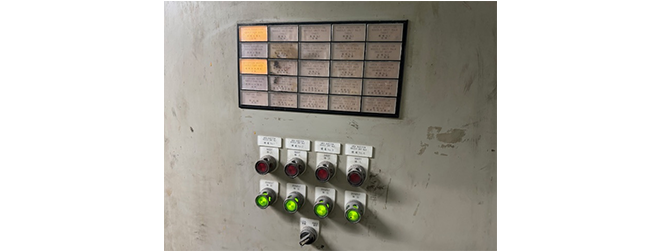
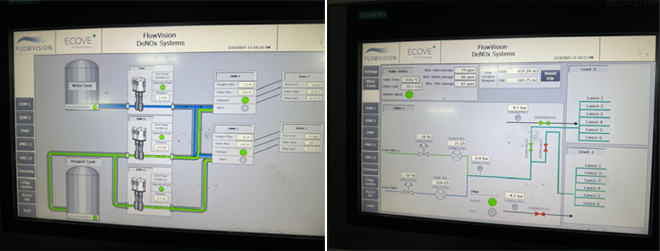
Enhancement Outcome and Future Vision
After the enhancement of the SNCR equipment, testing has shown significant reduction of NOx emissions to less than 70 ppm, with average emission concentration at 65.15 ppm for both furnaces in 2024, which is well below the 85 ppm standard set by the Guidelines for Reducing Pollutant Emissions from Existing Fixed Pollution Sources in Level 3 Prevention and Control Areas. The NOx emission per ton of waste at the EfW plant decreased from 1.08 kg to 0.793 kg, achieving a reduction of 26.57%. This not only significantly reduces the plant's environmental impact but also enhances the efficient use of resources, aligning with environmental policies and circular economy goals.
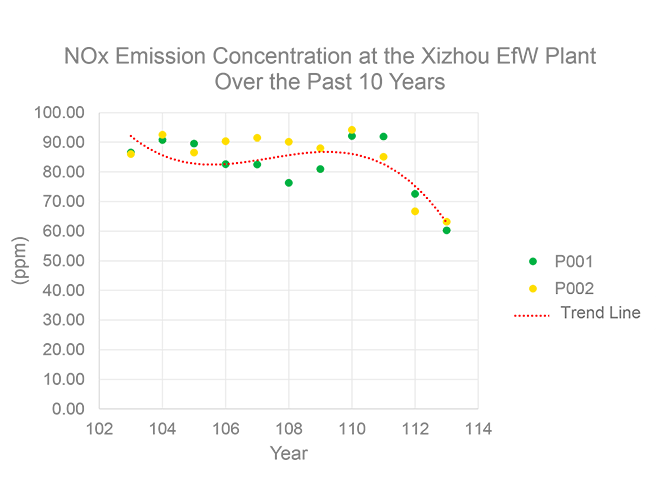
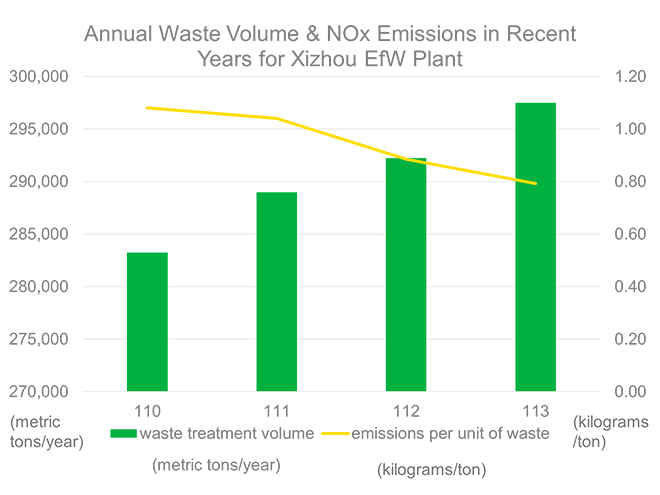
In the future, CTCI’s Group Resource Cycling Business will continue to uphold the principle of "every resource counts" and strive to strike a balance between environmental protection and economic development. It will also continue to carry out various resource cycling tasks and actively engage in R&D of new technologies to become more efficient, so that the ESG vision as a "Guardian of Sustainable Earth" may be fulfilled.