Technology
技術分享
Technology and Development of Precast Construction Method
— Qiu-Jin Hong, Manager of Manufacturing Department at CTCI REI, CTCI Group Intelligent Solutions Business
CTCI has long been committed to ESG development, with a focus on "green engineering". CTCI REI, a subsidiary of CTCI, shares this commitment and continues to promote carbon reduction in construction methods. In particular, for reinforced concrete structures which traditionally require a lot of labor, the "precast construction method" has been introduced since 2023 to enable independent production. From the building life cycle perspective, this effectively shortens construction time, reduces the use of raw materials, improves construction quality, enhances workplace safety, cuts future operating and maintenance costs, and extends the lifespan of the building. This article will share the outcome of CTCI REI’s development of “precast construction method”.
Challenges and Advantages of Developing Precast Construction Method
Since the Industrial Revolution, various industries have been industrialized to control product quality and reduce costs through mass production in factories. However, a lot of workers and technicians are still needed, as reinforced concrete structures remain the majority in the civil and construction engineering industry. Due to factors like technology, processing methods, labor, and site conditions, precision is usually in the centimeter level, unlike steel structures that can be precise to the millimeter. In recent years, the introduction of the precast construction method has enabled reinforced concrete structures to be mass-produced in factories. This includes components like columns and beams, which are standardized and modular, enhancing quality and precision while reducing onsite labor needs. Since the precast reinforced concrete structure is manufactured in the same factory as the steel structure and hoisted on-site, the precision of the precast components has to be improved to the millimeter level in order to meet the demand, which is a major challenge in terms of technology. Therefore, the precast construction method requires comprehensive and thorough consideration throughout the design and construction process, from planning and design, factory pre-casting of components, on-site positioning of foundation and column reinforcement, on-site hoisting of components (columns and beams), to on-site connection, in order to avoid problems such as failure to complete the installation in accordance with the design due to the location of a reinforcement bar conflicting with the components after they are transported to the construction site. For CTCI REI, with its design manpower and construction technology advantages, the adoption of this method is a natural progression, providing higher quality services to clients.
Enhancing Safety and Quality, Reducing Costs, and Being Environmentally Friendly
Compared to traditional construction methods, the precast construction method has many advantages summarized as follows: I. Safety Enhancement: Traditional onsite construction conditions are complex, involving heavy reinforcement work, column-beam formwork, and high-altitude operations. By moving these tasks to a precast factory, where the working environment is flat and mobile, quality is significantly improved, and safety during the construction process is ensured. For example, vertical high-rebar columns are replaced with horizontal tied-up column reinforcement cages, and replace the work of tying up beam reinforcement bars by bending down to go deeper into the beam molds with beam rebar cages supported by work frames. II. Efficiency and Quality Improvement: Precast components are made using steel molds that is detachable and can be assembled, able to be precisely cut by laser and bolted together. The components have accurate external dimensions and can be predrilled for connecting rebar according to design needs. This ensures high precision, strength, minimal deformation, and quick assembly and disassembly, requiring only 2 to 3 workers with a crane to complete the procedures in 10 to 20 minutes. In contrast, traditional methods require at least 4 to 5 workers for wooden formwork assembly, template transportation, cutting, and nailing, taking 2 to 4 hours for one component. Moreover, during onsite excavation and foundation work, precast columns and beams are produced and stored in the precast factory. Once the foundation is completed and the ground backfilled and leveled, the precast components are transported to the site by trucks and hoisted with large cranes. The process is as precise and fast as assembling building blocks.
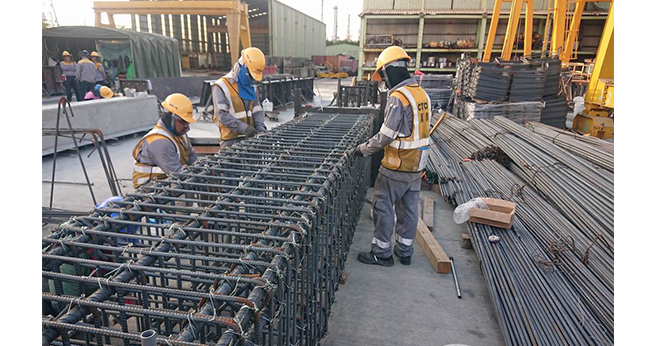
The assembly of precast column rebar cages can be performed in a horizontal position.
III. Environmental Protection and Cost Savings:
Unlike traditional wooden molds, which can only be reused 3 to 4 times before replacement, steel molds are permanent. The smooth surface of steel molds results in flat precast products, reducing the need for plastering materials, making it both economical and environmentally friendly. Moreover, onsite hoisting does not require as much labor as traditional formwork and rebar assembly, leading to a cleaner construction environment and significantly reducing construction waste (like formwork), thus lowering the environmental burden.
Introducing BIM Model to Eliminate Interferences
The design and construction drawings used in general projects are mostly traditional 2D (2-dimensional) plans, and the rebar has to be configured and adjusted on site by engineers and workers according to the actual space and dimensions of the beams and columns, which is difficult to be compatible with the precast construction method. Since precast columns and beams are finished products in the factory, rebar placement must be meticulously planned and reviewed in advance. The optimal solution is to use Building Information Modeling (BIM) to create a 3D (3-dimensional) model of the rebar arrangement for beams and columns. Engineers can comprehensively check from all angles for rebar collisions during the manufacturing drawing stage, preventing interferences among reserved rebar, embedded parts, and bolts during onsite hoisting. It also provides complete directional drawings of components, facilitating the precast production process.
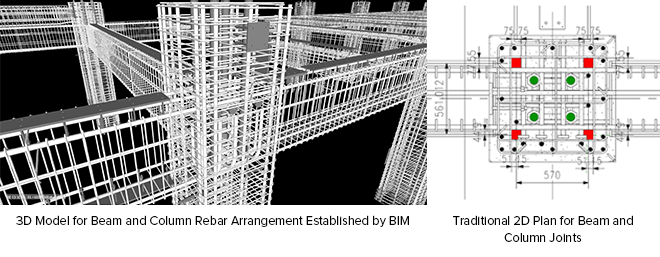
Introducing Key Technology to Overcome Column Component Connection Challenges
One of the key technologies in precast construction method is the connection of column components. The rebar connectors commonly used in domestic projects are not suitable for precast columns. To address this challenge, CTCI REI introduced the Japanese coupler technology, which connects both ends of the main rebar column. Through this method, the upper and lower rebar are inserted into the coupler, which is then filled with high-strength, non-shrinking grout (compressive strength greater than 70 N/mm²). Meanwhile, to ensure the coupler and grout performance meets the Construction Outline of the Public Construction Commission, the rebar, coupler, and grout assembly is then subjected to unidirectional tension and slip tests, as well as high plasticity cyclic loading tests. The coupler technology involves production and hoisting phases. In the production phase, jigs are used to secure the couplers to the steel mold (column bottom mold) to prevent displacement or loosening during the production process (including rebar assembly and grouting), and ensure that concrete does not flow into the coupler. In the hoisting phase, the column components must correctly fit into the lower reserved rebar. After verifying the column's verticality and coordinates, grout is injected into the coupler via a grouting machine through the coupler's grout holes to fill the coupler completely.
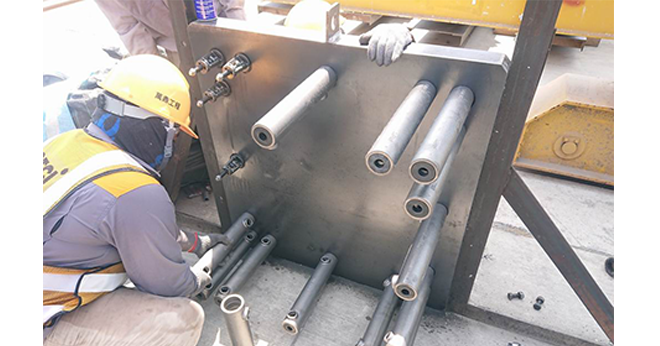
Using Japanese coupler technology can overcome the challenges of connecting column components.
Conclusion
The technology and development of the precast construction method can significantly transform traditional onsite construction practices. The government is also promoting the precast construction method with incentive measures to address the severe labor and material shortages domestically. CTCI REI will continue to advance this method and gradually apply it to various industrial construction projects, making project execution faster, better, more competitive, and more environmentally sustainable.