Technology
技術分享
Enhancing VOCs Emission Reduction Technology, Implementing the Circular Economy in Practice
— Chia-yen Li, Engineer at ECOVE Environment Services Corp., CTCI's Group Resource Cycling Business. — Jie-ling Lai, Engineer at ECOVE Environment Services Corp., CTCI's Group Resource Cycling Business.
As the high-tech industry continues to develop new processes and technologies, the organic solvents used are becoming more complex, resulting in the production of various Volatile Organic Compounds (VOCs), most of which are flammable and have low flash points that can cause explosions if not managed properly. Over the years, ECOVE, a CTCI subsidary, has been actively involved in the field of circular economy.One of its primary focuses is to provide assistance in the recycling and disposal of waste generated by the high-tech industry. With it’s own plant, ECOVE helps semiconductor manufacturers recycle and recover the waste isopropanol (IPA) during the manufacturing process, concentrate then reintroduce them into the market supply chain. It also offers design, equipment installation, trial running, and consulting services for the construction of facilities dedicated to recycling and reusing waste solvents, such as waste IPA , high organic waste liquor, and waste EBR. This article introduces how ECOVE offers design solutions to improve VOCs abatement that are tailored to the specific characteristics of each plant. These solutions help clients achieve goals such as an overall emission reduction and recycling of reusable materials, putting circular economy into practice.
Advancing technology for reducing VOC emissions
When VOCs are involved in the manufacturing system and operating environment, these areas are in the risk of containing explosive gases. To mitigate these risks, in addition to segregating hazardous areas and installing explosion-proof electrical machinery, appliances, or equipment, it is fundamental to improve or enhance the air pollution control equipment in the process system. This will help reduce the emission concentration of VOCs from the source. The Ministry of Environment, Executive Yuan has been tightening its regulations in response to the regulation of VOCs emissions. The "Air Pollution Control and Emissions Standards for the Semiconductor Industry" were amended in May 2023. The previous control method, which did not differentiate by scale and limited the total hourly emissions to no more than 0.6 kilograms per hour, will be replaced by individual emission control through specific emission channels. The new method requires that the individual emission concentration be less than 14 ppm. In addition, a new provision stipulates that the concentration of newly established processes must not exceed 10 ppm. This promotes the selection of environmentally friendly or more effective equipment for new factory buildings or processes. Therefore, VOCs emission reduction technologies must continuously improve in response to industry demands. VOCs emission reduction technologies are primarily categorized into two parts: "processing" and "recovery". The primary goal of the processing technique is to reduce emissions, while the recovery technique aims to recover organic solvent materials from VOCs, thereby creating value for reuse. This article will present two distinct case studies to illustrate.
Case I: Enhancing design to boost reduction rate
Regarding VOCs reduction technology, one of the example will be the treatment of the waste IPA solvent produced during the manufacturing process of the high-tech industry, and scrubbing towers is a first option for the air pollution control equipment of this kind of treatment. For the scrubbing towers will selectively adsorbs the IPAdue to its hydrophilic properties, achieving a VOCs reduction rate of over 90%. Additionally, adjustments to the body of the scrubbing tower, wetting factor, specific surface area of the packing material, and stacking method must be implemented based on the airflow design of the process system. In the case of a certain high-tech factory served by the CTCI Group (hereinafter referred to as Case I), the initial design of the scrubbing tower filler was raschig rings (specific surface area: 109 m²/m³). However, during the system design period, there were regulatory amendments. In addition to changing the packing design inside the scrubbing tower to wire mesh filler (specific surface area: 205 m²/m³) to increase the specific surface area, fresh water was continuously added to the second section of the scrubbing tower to ensure sufficient contact between the liquid and gas inside the tower. The mixture is then circulated into the first washing section of the scrubbing tower, allowing the liquid to adsorb the pollutants in the waste gas exhausted. This design ensures that the final VOCs emission concentration meets the individual emission standards for each discharge pipe, which is less than 14 ppm.
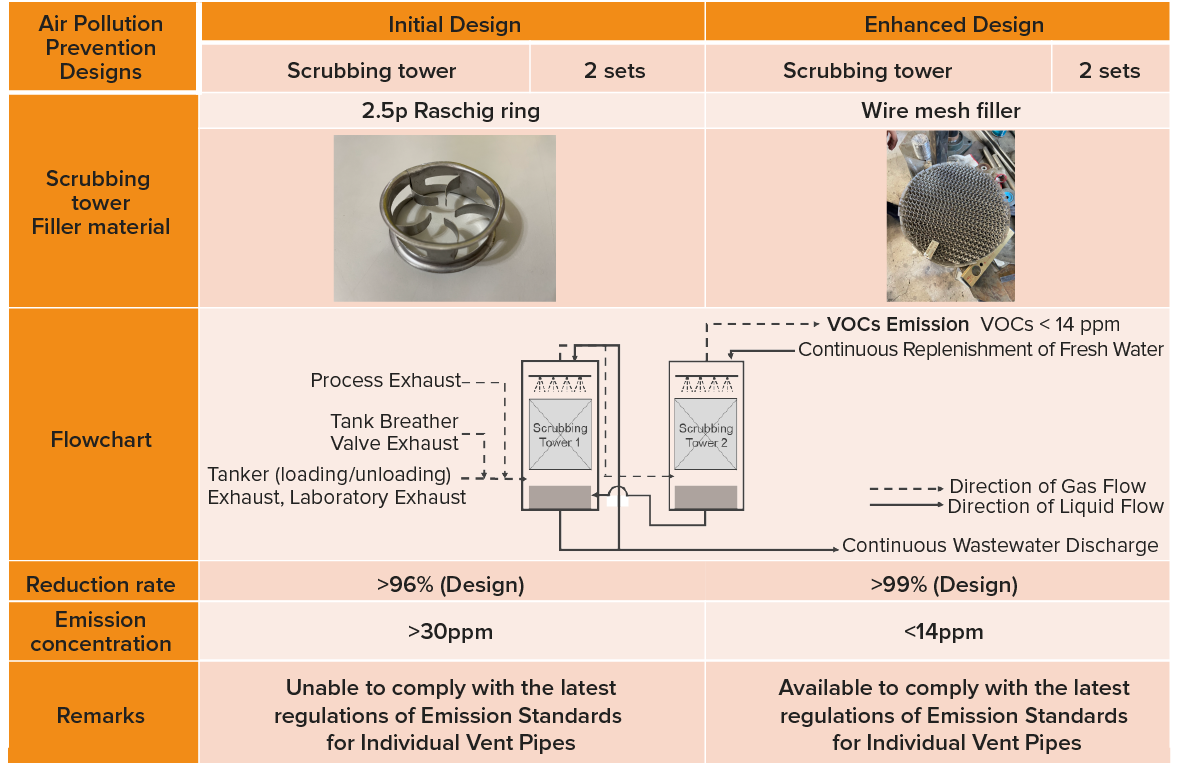
Case I: Comparison of Air Pollution Prevention Designs
Case II: The Miracle of Condensing technology
When it comes to recycling and reusing technology, the exhaust gas condensers are highly recommended in both existing and newly constructed plants with high-concentration IPA solvent tanks. This reduces VOCs emissions and enhances solvent recycling and reuse efficiency. Taking the example of the IPA concentration reuse system at another high-tech plant of the CTCI Group (referred to as Case II), the VOCs generated have an emission concentration of more than 50 ppm after the existing air pollution control equipment, which does not meet the requirements of the latest regulations. However, due to limited space configuration in the plant area, it is not possible to install additional control equipment, such as adding up to two scrubbing towers. By replacing the existing Raschig rings in the scrubbing tower with wire mesh packing, it is expected that the emission concentration can be reduced to less than 30ppm. However, this approach alone may not fully comply with the regulations. In Case II, a condenser is installed in the high-concentration IPA storage tank of the system. This utilizes the hydrophilic property of IPA in the exhaust gas. The IPA vapor (0.85 kg/hr) in the tank is then cooled to 15℃ with chilled water, allowing the recovery of 0.5 kg/hr of high concentration IPA. Furthermore, the scrubbing tower's existing filler is replaced with wire mesh filler, resulting in an estimated overall VOCs reduction rate of approximately 99%, an improvement from the initial design of 96%. Consequently, the final concentration of VOCs emissions will meet the Regulation of Emission Standards for Individual Vent Pipes, with a standard emission limit of <14ppm. After condensation, the highly concentrated IPA can be reintroduced into the distillation and purification process system for further purification, allowing for the recycling of resources.
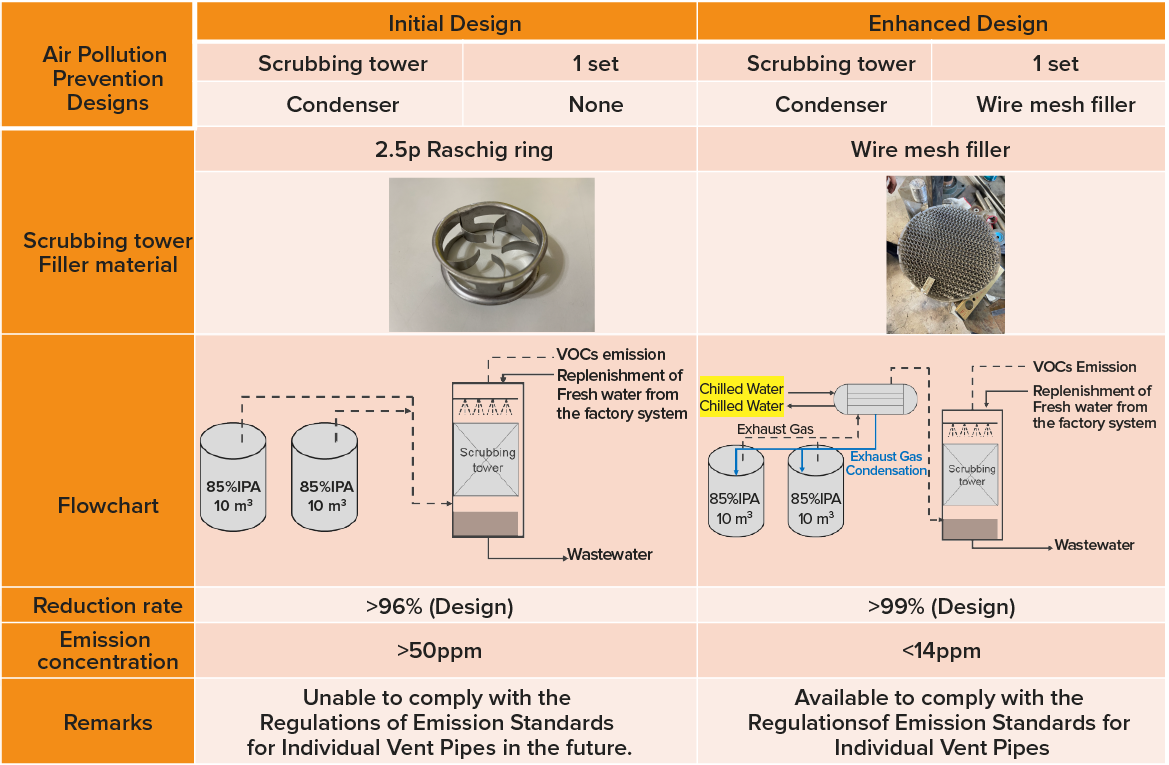
Case II: Comparison of Air Pollution Prevention Designs
Conclusion
In recent years, as climate change has taken center stage, countries worldwide have made commitments to reduce carbon emissions and promote the development of a circular economy to facilitate the reuse of resources. The cases served as a concrete evidence of CTCI Group practicing Green Engineering . The CTCI team is able to choose the most suitable air pollution control equipment for our clients taken in the consideration of their process system, as well as the compound and characteristics of the exhaust gas. Moreover, these equipments are able to effectively improve air quality and maximize the benefits of reuse. We aim to reduce carbon emissions and progressively achieve ESG's vision as “the Guardian of Sustainable Earth”, while working closely with customers to move steadily toward the net-zero goal.