Discover Reliable
發現信賴
CTCI Successfully Establishes Taiwan’s First Mega Battery Plant: Molie Quantum Energy Corp.’s Lithium Battery Plant in Xiaogang, Kaohsiung
— Yeh Tao, Project Engineer, CTCI Corp., Group Engineering Business
- Market category:Energy Storage
- Client: Molie Quantum Energy Corp.
- Commercial Operation Date:June 30, 2023
- Project site: Xiaogang District, Kaohsiung City, Taiwan
- Scope of work:Engineering, Procurement, Construction Management Services (EPsCm)
- Production Capacity:8 million units per month, 1.8 GW
Located in the Linhai Industrial Park in Xiaogang District, Kaohsiung City, Taiwan, Molie Quantum Energy Corporation’s Lithium Battery Plant is the first mega battery factory in Taiwan, and it is owned by Molie Quantum Energy Corporation, a subsidiary company of Taiwan Cement Corporation. In this project, we introduced advanced production processes and equipment to manufacture high-end, high-capacity, and high-charge/discharge rate nickel-cobalt-manganese (NCM) batteries with an annual production capacity of 1.8GW, equivalent to the amount of long-range battery capacity needed for the production of 24,000 electric vehicles (EV) per year. Moreover, the introduction of the advanced production processes facilitates the development of the domestic energy storage industry, helping Taiwan expand its market share in the global mega battery market and penetrate the EV supply chain, further promoting the development of green energy in Taiwan. CTCI’s project team assisted the client in completing the initial EPC cost assessment for this plant in December 2020. Then, since April 2021, the team has been working with the client to clarify all kinds of functional requirements and estimate the total project cost, as well as collaborating with the architectural team designated by the client to finalize the preliminary design, which serves as the foundational data for the EPsCm work in this project. Meanwhile, we assisted the client with the purchase requisition and order process, including the surveying projects, boring and subsurface exploration projects, the contracting of architects for the demolition of old plant buildings, demolition projects, and the hiring of design architects. As for the construction of building structure, we also assisted the client in procuring services such as civil engineering and architecture, electrical and mechanical work, and interior decoration, while also introducing CTCI Smart Engineering Corporation, a subsidiary company of CTCI, to undertake the EPC project of the electrical and mechanical work, and carried out on-site design coordination and project management.
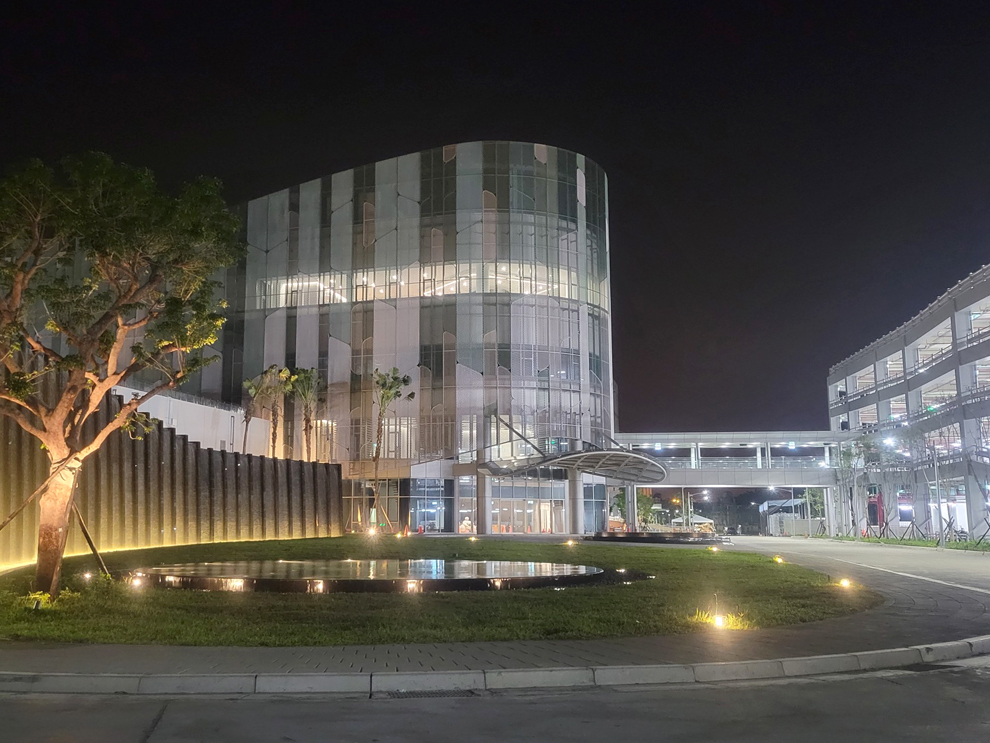
Molie Quantum Energy Corp.’s lithium battery plant in Kaohsiung.
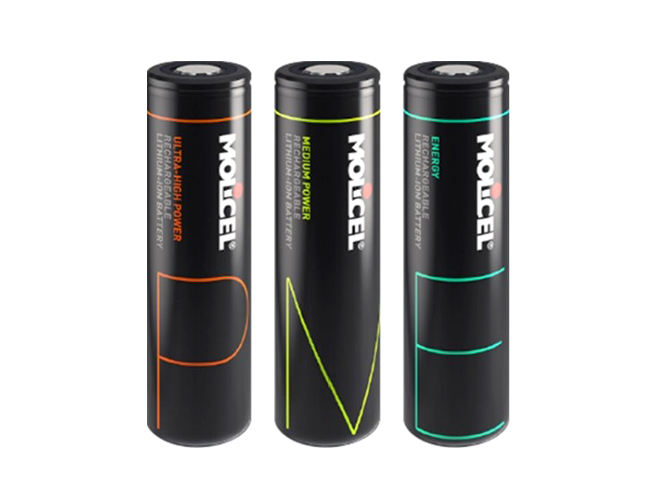
Lithium battery samples
Why CTCI?
Establishing a Project Management Model to Ensure Client’s Intellectual Property Rights are Well Protected
High-tech clients place great emphasis on the confidentiality of information. In order to ensure that information is not misused, leaked, lost, or damaged and thus results in reputational damage or financial loss for both the client and CTCI, we are committed to taking action to protect intellectual property. This is achieved through the control of document and access, development of project IP plans, rigorous management of information security, and periodical review of action effectiveness. These efforts effectively manage and protect the client’s intellectual property, earning their trust and recognition. Being a goal-achiever, CTCI adopts precise work regulations and effective project operation procedures to ensure the protection of the client’s intellectual property, thus winning wide acclaim in the industry. This long-established project management model is also followed in this project to deliver the client’s expected outcome.
Reliable Realized
Venturing into the High-Tech Industry with Rich Project Management Achievements
Being in business for forty years now, CTCI has become a global turnkey engineering group and ranks first in Taiwan and among the top 100 in the world. With numerous challenging projects completed worldwide, CTCI has earned a distinguished reputation in the industry at home and abroad. CTCI is widely acknowledged to be exemplary for Taiwan’s engineering industry due to its rich experience in engineering contracting, outstanding performance in operational management, commitment to the quality of safety, health and environment, emphasis on innovative technology, and dedication to sustainability and ESG. In this spirit and attitude, the project team endeavors to provide the most reliable engineering services for the client. This project represents CTCI’s foray into the high-tech field, as it is the first project secured by the newly-established Advanced Technology Facilities Business Operations (ATFBO) and also CTCI’s first EPsCm contract. With its many years of experience in project management and turnkey contracting, CTCI’s project team has punctually completed numerous onerous tasks during project executions, including the coordination for parallel installation of civil engineering and electrical and mechanical work, allocation of the space of each floor/area, and the entry/deployment of the client’s process equipment, etc. These actions have allowed the client to confidently install and operate the process equipment in the plant and start production as soon as possible.
Project Highlights
Taiwan’s First Mega Battery Plant
This mega battery plant manufactures lithium battery cell, which possesses advantages of being high-end, having high-capacity, and high-charging/discharging rate. In view of the increasing demand for lithium batteries, the client anticipates insufficient production capacity at its EMT1 and EMT2 plants run by Tainan’s E-One Moli Energy Corporation and therefore converts the Taiwan Cement Paper Mill into the EMT3 plant, expanding its capacity to meet the overall operational efficiency. At the construction stage, CTCI assists the client with various supervision services, including the management of various construction projects, quality control of on-site construction, construction inspections, parallel installation and construction, and management of safety, health, and environment.
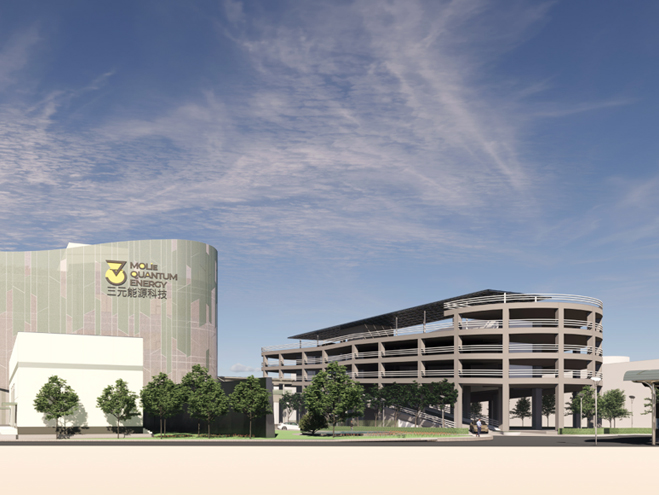
The overall image of Molie Quantum Energy Corp.’s lithium battery plant.
Smarter Engineering
Flooring Design of Chemical Warehouse
It is considered illegal to have chemicals in the warehouse of lithium battery raw materials seeping into the environment, such as the soil and groundwater. Therefore, the anti-seepage design for the flooring has to be rigorously planned. In addition to assessing the structural strength, it is also necessary that the floor paved with effective anti-seepage materials. Having conducted feasibility assessment of all proposed solutions and multiple meetings with the client, environmental engineering technicians, architects, and civil engineering contractors, the project team decides to apply silicon crystal hardening coating for floor paving. This method adopts a concrete silicon crystallization hardener that is highly sealed, dustproof, and wear-resistant, which effectively seals the capillary pores of the floor surface and completely resolves the issue of dust extraction due to weathering of the concrete formation over time. Compared to the FRP (Fiber Reinforced Polymer/Plastics) coating, not only does it meet the requirements for seepage prevention, but it also reduces construction and material costs by nearly 80% - which represents an example of value engineering.
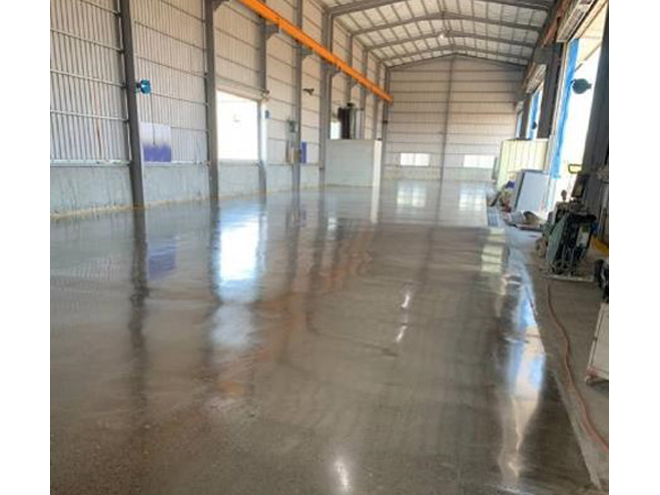
Demonstration of silicon crystal hardening and corrosion-resistant coating.
Precasting Method
In the first construction phase, the goal is to conduct the civil engineering of structure. The main building is a four-floor structure. With an average floor height of 6 meters and elevated ceilings in certain areas, the total floor area is approximately 84,000 square meters. To meet the client’s requested completion deadline and the need for concurrent construction of electrical and mechanical work, the precasting method is adopted based on the concept of modularization in this project. The beams, columns, and exterior wall panels for the main structure are dismantled into several components, precast in a yard, and then transported for assembly on-site. Compared with on-site casting, the required time is 50 working days shorter, significantly reducing on-site operation time. Additionally, the method also meets the requirements for drainage, waterproofing, etc., fulfilling the client’s needs.
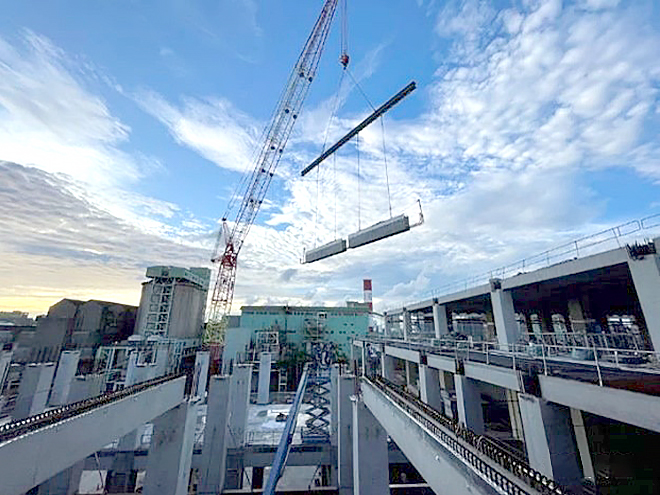
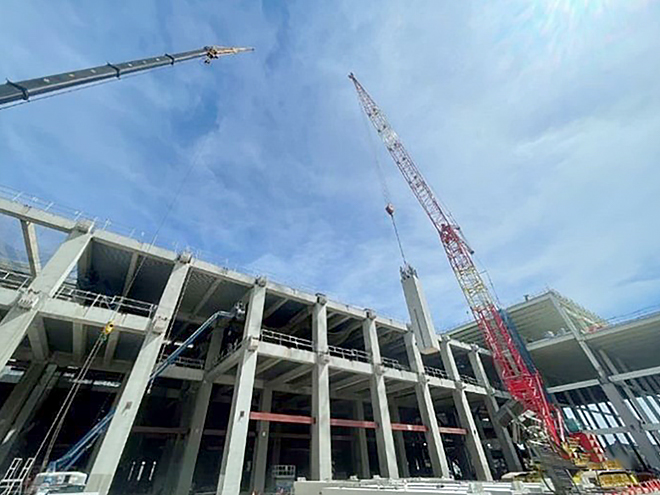
Message from the Project Team
This project marks the first EPsCm project since the establishment of ATFBO. The CTCI team upholds our corporate culture of “Professionalism, Integrity, Teamwork, and Innovation” and is dedicated to creating the highest level of trust in the quality of engineering services. We have fully supported our client in constructing this plant by providing excellent services in project management, engineering design, scheduling, procurement, and quality supervision. This has enabled our client to smoothly embark on the production stage, and continue to achieve further success in the energy storage sector. --MT Kao, General Manager, Technology Department, ATFBO