Technology
技術分享
Connecting the Past and Sensing the Future, CTCI Sets New Sustainable Image for Southern Taiwan Science Park
— H.C. Han, Manager at Tainan Science Park Resource Recycling Center, ECOVE Environment Services Corp., CTCI’s Group Resource Cycling Business
ECOVE Environment Services Corp. (hereinafter referred to as ECOVE) is affiliated to the Group Resource Cycling Business, CTCI Group, and has rich experience in the field of waste management and incineration, in particular a great expertise in incineration plant overhaul. The Southern Taiwan Science Park Tainan Park Resource Recycling Centre (hereinafter referred to as the Resource Recycling Center) has been in operation for nearly two decades. As the number of operation years goes by, the mechanical and electrical equipment has undergone natural wear and tear while efficiency has decreased over the years. In consideration of factors such as energy conservation and carbon reduction, environmental assessment requirements, and increasingly stringent air pollutant emission standards, the Southern Taiwan Science Park Bureau has scheduled a plan to improve equipment efficiency and meet future pollution emission standards for the resource recycling center. Through tendering and selection process, ECOVE clinched the equipment overhaul and function upgrade project for the Resource Recycling Center in December 2021, with a performance period of 400 days. ECOVE arranged for an optimized construction schedule within the limited timeline, and made improvements in the following four key aspects: enhancing original design capabilities, improving the efficiency of air pollution control, introducing energy-saving and intelligent application systems, and spatial transformation for technological image, as detailed in this article.
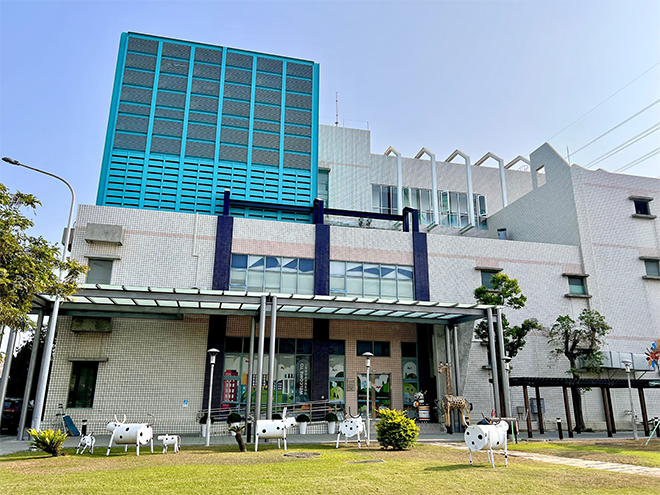
Southern Taiwan Science Park Tainan Park Resource Recycling Center.
I.Enhancing Original Design Capabilities
In view of growing amount of solid waste in Southern Taiwan Science Park (STSP) over the years, the heterogeneity of waste solvents, and the aging of incinerator shell steel plates and refractory lining, the project focused on enhancement of the feeding system and incineration system. Post enhancement of equipment functions, the waste crushing and feeding speed would be raised, with the solid waste crushing capacity to be increased from 3 metric tons per hour to 5 metric tons per hour, the operating speed of the waste crane to be increased from 23m/min to 26m/min, and the hoisting speed of the crane to be increased from 12 m/min to 20 m/ min, hence reducing the workload of operators, overhauling the waste solvent tank circulating pump and pipeline, and ensuring that the treatment of waste in the park would become more flexible as the waste solvent being evenly mixed to cope with the changes in the nature of waste in STSP. In addition, the incinerator shell steel plates and refractory lining were given an overhaul. The steel plates were replaced with original sized ones, assembled and welded by sections on site, and all weld points were subjected to Liquid Penetrant Inspection (PT) nondestructive testing. Based on the conditions in the furnace, refractory bricks, wear-resistant materials, or acid and alkali resistant materials were selected as refractory lining. For example, acid and alkali resistant refractory materials were used for the lower end of the sludge injection nozzle to extend the service life of the incinerator and refractory lining by up to 15 years.
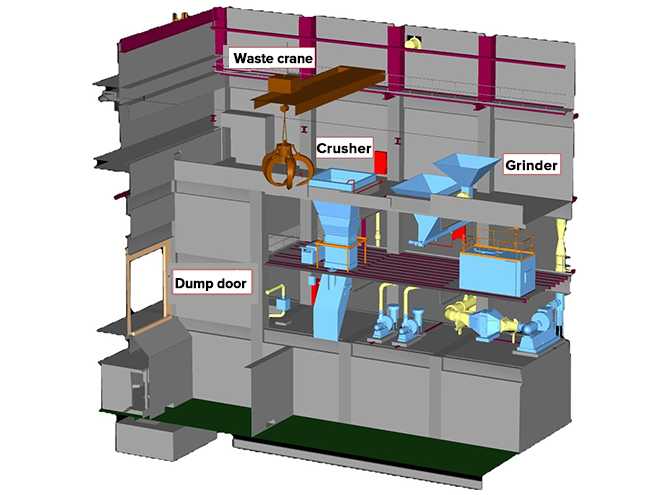
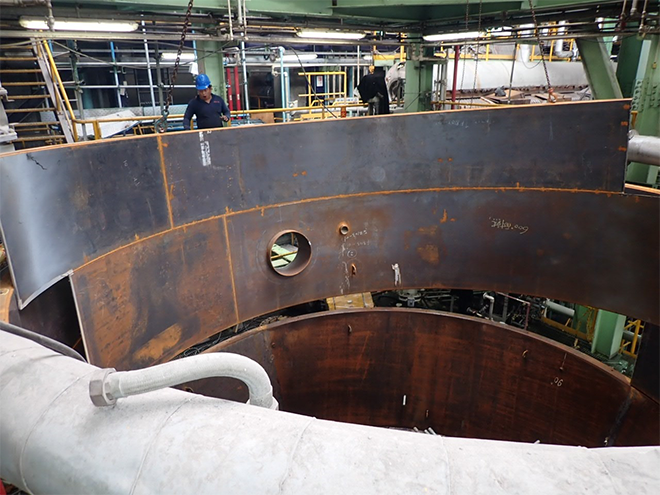
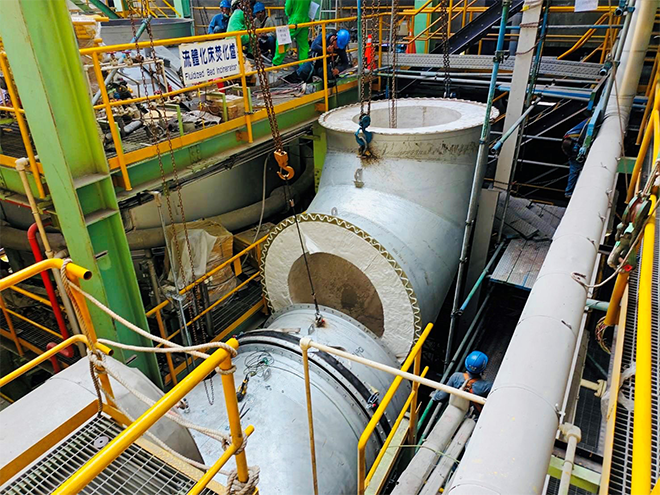
II.Improving the Efficiency of Air Pollution Control
The upgrade of flue gas treatment system mainly covered the following: acid gas removal system (newly added high-efficiency sodium bicarbonate injection system), denitrification system (overhauled high-efficiency ammonia injection system), dust removal, dioxin system (upgraded triple-effect catalytic filter baghouse system), and overhaul of relevant waste gas treatment system (flue steel and refractory lining). To cope with the complex waste types in STSP, ECOVE introduced advanced control technologies, which can significantly reduce greenhouse gas emissions higher than the new exhaust emission standards. During the test period (December 2022), NOx emissions decreased by 20 kg/day (a reduction of about 7 metric tons/year) and SOx emissions decreased by 15 kg/day (a reduction of about 5 metric tons/year) compared with the same period last year. To boot, with the improvement of the acid removal system, the amount of reaction ash was also reduced by 1,000 kg/day (a reduction of about 350 metric tons/year), thus extending the life of the landfill. Besides facilitating rapid denitrification, the replacement of urea with liquid ammonia for the denitrification system and introduction of CFD simulation technology to simulate the temperature and flow distribution of the fluidized bed and to simulate the diffusion of reducing agent at selected injection points also reduced carbon emissions by 30 CO₂e metric tons per year. In so doing, it is able to meet the original planned design goals of carbon reduction, emission reduction and volume reduction, enabling the Resource Recycling Center to take a step closer to sustainable treatment.
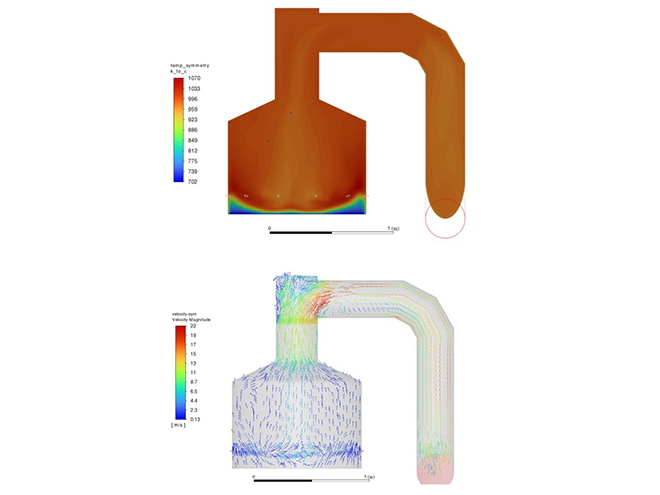
Introduction of CFD simulation technology into the denitrification system to select the injection point of the agent.
III.Introducing Energy-saving and Intelligent Application Systems
Responding to the issues of energy conservation, carbon reduction, and net-zero emissions, ECOVE refined the heat recovery and condensation system, updated the fan motor and added frequency conversion control, and enhanced the air conditioning frequency conversion system for the plant. After installing a solar energy system (55KW), enhancing the fan motor and air conditioning on top of adding frequency conversion controls, about 70,000 kWh was shaved off the electricity consumption data for December 2022 compared to the same period last year, which is an energy saving of 16%. In addition, ECOVE has developed a weighbridge management system which is incorporated with vehicle license plate recognition. The system can identify vehicles before they enter the weighbridge platform, which are instantly compared against the authorized license plates in the database. When non-authorized or specific license plates are detected, the system will issue an alert automatically to remind staff on duty to immediately verify the situation and handle abnormalities. This would effectively reduce human error and pressure incurred, while making records more detailed and automate operations thus ensuring the accuracy of data, preventing fraudulent alterations and eliminating malpractices.
IV.Spatial Transformation for a New Technological Image
In order to improve the of NIMBY(Not In My Back Yard) image for a municipal incinerator, ECOVE transformed the administrative building of the Resource Recycling Center to one with a modern technology vibe, using light beams to convey the message of the wondrous efforts of the Resource Recycling Center to safely treat complex and diverse waste in STSP and progress towards a brighter future of net-zero emissions. The illumination also created a spatial atmosphere of “connecting with the past and sensing the future” through technology, thus giving rise to a brand-new technological image with semi-humanoid guiding robot interaction installations.
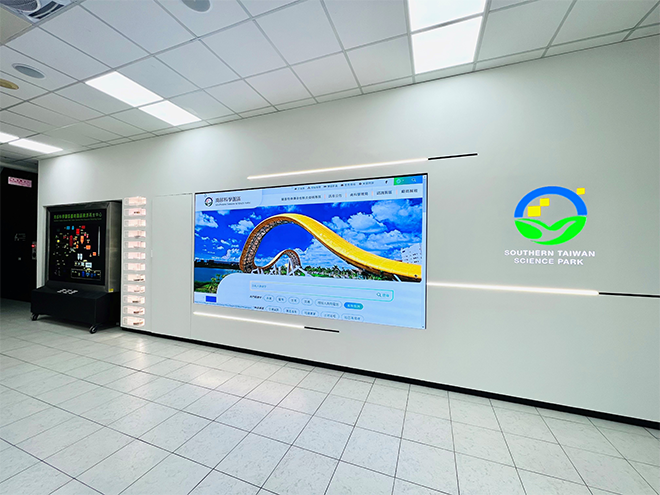
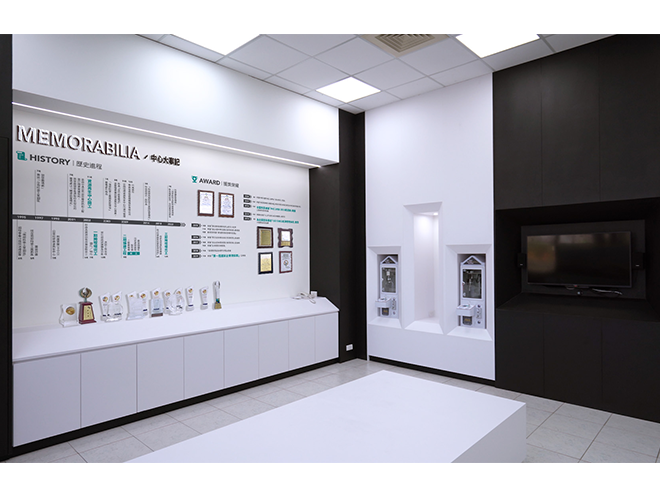
Conclusion
ECOVE effectively overcame the aging and reduced efficiency of incinerator equipment issues with rich experience in plant overhaul and annual maintenance, supported by skillful manpower and professional technical expertise of each plant, excellent equipment suppliers, and one-stop professional services for waste treatment. By introducing innovative technologies to optimize equipment efficiency, ECOVE helps maintain the plant’s operation stability, improve pollution prevention capabilities and energy utilization efficiency, successfully assisting the client to achieve the sustainability goals of being safe, environmentally friendly and minimize pollution to establish a new sustainable image for the Resource Recycling Center.