Discover Reliable
發現信賴
CTCI Plays Successful Role in Offshore Wind Power Localization: The Changfang & Xidao Offshore Wind Farm Pin Piles Supply Project
— Janet Chang, Project Engineer at CTCI MAC, Group Engineering Business
- Market category: Offshore Wind Power
- Wind Farm:Changfang and Xidao Offshore Wind Farm
- Developer: Copenhagen Infrastructure Partners (CIP), Denmark
- Contractor: CTCI Machinery Corp. (CTCI MAC)
- Completion date:November 2021
- Wind farm location:Off the coast of Changhua
- Project scope:117 pin piles
Changfang & Xidao Offshore Wind Farm is the first 100% localized wind farm in Taiwan, developed by Copenhagen Infrastructure Partners (CIP). CTCI Machinery Corp. (CTCI MAC), a subsidiary of CTCI, was responsible for fabricating 117 pin piles (PP), which at the time was the largest pin pile contract for a single local supplier in Taiwan's offshore wind power industry. Located off the coast of Changhua, the wind farm has a total of 62 offshore wind turbines with a total generating capacity of 600MW, which can supply electricity to about 600,000 households in Taiwan annually. With excellent fabrication and management capabilities, CTCI MAC completed the overall fabrication 2.5 months ahead of schedule and delivered the first batch from June to August 2021. Delivery of the second batch began in February 2023, fully demonstrating the expertise and supply capacity of the local supply chain. Offshore wind power is one of Taiwan government’s key projects in developing green energy and securing energy independence. By leveraging more than 40 years of expertise in pressure vessel fabrication and the mother group’s exceptional interface capabilities from turnkey projects, CTCI MAC has aggressively taken part in offshore wind power underwater component fabrication since 2018. This has not only helped the government achieve its energy policy targets, but has also enabled the localization of offshore wind power industries.
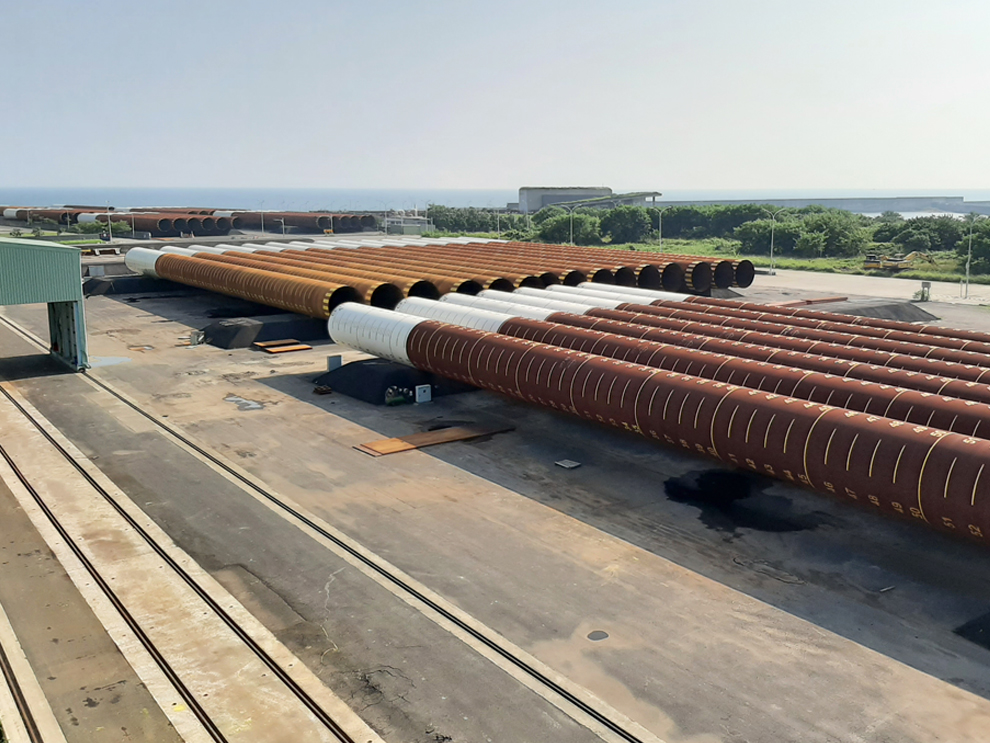
Changfang & Xidao Offshore Wind Farm pin piles assembly and storage yard
Why CTCI?
Taiwan's Leading Mechanical Equipment Fabrication Company, with the Most Trustworthy Engineering Quality
CTCI MAC has more than 40 years of experience in pressure vessel fabrication. Thanks to its solid quality control system, CTCI MAC successfully obtained the European certifications required for wind power equipment fabrication in 2017, including EN 1090, ISO 3834- 2. AD 2000 HP0, and PED module H. Owing to superb welding capability, extensive equipment fabrication experience, well-grounded quality control system, and the successful implementation of the 40 monopile transition pieces of Yunlin Wind Farm in the previous project, it has won the trust of the client.
Reliable Realized
Strict Construction Quality Control and Precise Project Delivery
Pin pile fabrication projects have extremely demanding quality requirements. CTCI MAC strictly controls the fabrication quality and checks the qualifications of subcontractors. All welders, including those who come from CTCI MAC or come from the subcontractors, had passed the client’s qualification examination and acquired certifications. The fabrication yard and hinterland for the subcontractor have also passed the owner's audit to prevent unnecessary waste caused by product defects and re-fabrication, allowing effective control of the budget. At the time, this was the largest project undertaken by a single supplier in Taiwan in terms of the number of foundations to be fabricated for offshore wind power generation. It was also CTCI MAC’s first business cooperation with CIP. Due to the large number of pin piles and the tight fabrication schedule, it was necessary for CTCI MAC to plan the capacity load management in advance to ensure that the workstations and manpower planning of the production line meet the schedule requirements. This included sequential fabrication such as rolling, fit-up, shear keys welding, assembly, and external marking lines. The aim was to ensure that the components of each workstation were in place in time, and the production line continued to produce without interruption. The staff did not slack off when the progress was ahead of schedule, and when the progress fell behind, the team quickly sought corresponding mitigation measures and streamlined the production line.
Project Highlights
Overcoming the Impact of the Pandemic to Achieving Localization of the Largest Number of Wind Farms Pin Piles
At the initial stage of this project, Taiwan was under nationwide level 3 COVID-19 alert. In order to reduce the impact of the pandemic, CTCI MAC complied with the government regulations and formulated various contingency measures to ensure that production progress was not affected even during the severe stage of the pandemic. Since the length of the pin pile is up to 78 meters, the overall project execution flow needs to be fully considered to ensure that the entire process— from production to shipment— is completed in one go. This includes the sequence starting from steel plates arrival, fabrication planning, storage arrangements, transportation planning, as well as intensive communication, schedule confirmation, and coordination with the owner, wharf, installation, and transportation companies to ensure everything goes well at the time of load-out campaign. In addition, CTCI MAC used the serial production process for the pin pile fabrication in this project. Through continuous optimization of the fabrication process and construction methods, despite the challenges of the pandemic, CTCI MAC still achieved the highest completion rate of 12 pin piles in one month, and wrapped up all fabrication 2.5 months ahead of schedule. The excellent results demonstrate its strong capability.
Smarter Engineering
Synchronous Welding with Multiple Welding Machines to Deliver High-quality Pin Piles
The pin piles in this project, which are steel structure foundations that help fix the 3-legged jackets onto the seabed, are one of the important components of the wind turbine substructure. The exterior of the pin piles requires 15 meters of anti-corrosion coating with the overall piling depth properly marked; the interior of the pin piles needs to be welded with 16 shear keys to increase the connection strength with the jackets. Their structural strengths and welding precision can only be achieved with mature fabrication technology. In order to successfully produce 117 pin piles within 14 months, CTCI MAC led the industry in developing and adopting multiple cross welding arms for simultaneous welding, which improved production efficiency by multiple times, helped maintain a low grinding rate while meeting quality requirements, and completing the project ahead of schedule. In the future, CTCI MAC will continue to make efforts in securing new offshore wind turbine pin pile fabrication projects, so as to gradually accumulate track records and experience in the field of offshore wind power, optimize production lines technologies, hoping to promote localization of offshore wind power supply chains. In so doing, CTCI MAC expects to become the preferred supplier of offshore wind turbine substructures in Taiwan and the Asia-Pacific region, sustaining its position in the global offshore wind power market.
Message from the Owner
CTCI MAC completed the production of pin piles ahead of schedule. In addition to the quality, price, and delivery time being fully up to standard, their emphasis on environmental safety and the professionalism demonstrated during contract execution could serve as benchmarks for local supply chain partners. --Dennis Sanou, CEO for the Changfang and Xidao Offshore Wind Projects, Copenhagen Infrastructure Partner, Denmark