Technology
技術分享
CTCI’s Innovative Research and Development of Pipeline Cleaning Robot
— Chuan-Tse Hsiang, Assistant Chief Engineer, CTCI Corporation, Group Engineering Business
Due to the concern over air pollution and the frequent occurrence of extreme weather patterns in recent years, countries around the world have made ongoing efforts to build gas-fired power plants instead of coal-fired power plants, so as to reduce atmospheric particulate matter and carbon dioxide emissions. It has led to ravenous demand for building LNG (liquefied natural gas) terminals and storage tanks. In this article, we will talk about how CTCI develops the prototype of pipeline cleaning robot for LNG terminals through innovative technologies, and thus successfully enhances the quality of CTCI’s “most reliable” engineering services.
Challenges and Current Status of Pipeline Cleaning
It is difficult to ensure that the interiors of LNG pipelines are completely clean while a LNG terminal is under construction. Normally, to clean a LNG spool at a fabrication shop, the debris inside the spools are removed by blowing compressed air or by standing the spools up, and then seal both the spool ends. During the field erection stage, environmental pollutants, such as rainwater and dust, as well as hard and sharp objects caused by cutting, grinding, welding, etc. may remain inside the pipelines. Although pipeline air blowing is carried out upon mechanical completion, a little debris may remain inside the pipelines and accumulate in the gaps because pipe fittings are not streamlined and most slags have a low wind surface area, which makes the slags remain inside the pipelines and are stuck in the gaps, such as the seams where the valves open and close. Operating the valve at this moment may cause damage to the valve parts, potentially bringing the danger of internal leakage. Natural gas is extremely flammable. Owing to a host of disasters caused by natural gas leakage in the past, the installation of flanges are minimized to reduce the risk of such leakages. Such a requirement has made pipeline cleaning even more difficult. At the same time, construction contracts often include a valve leakage test before startup, which is carried out using nitrogen or cryogenic natural gas directly. If a leak is found, a series of steps have to be then carried out, including depressurizing, purging the pipeline, removing, repairing, and reinstalling the valve before conducting the test again. This entire process not only wastes a great amount of expensive nitrogen or natural gas, but also increases the construction time. Due to the large number of butt weld valves used in a LNG terminal project, grinding debris, welding spatter and oxides, slags (if flux-cored TIG is used), and dust will remain inside the pipelines. Although most of the dirt can be removed through pipeline air blowing, a small amount of it will still stay in the gaps, such as the valve seat. Operating the valve without additional cleaning may cause damage to the valve and lead to internal leakage in the valve, which incurs subsequent repair costs. With the traditional pipeline air blowing technique already on the brink of a bottleneck, CTCI has developed its own “Pipeline Cleaning Robot” aimed at meeting the cleaning requirements of LNG pipeline. The development of this innovative technique not only enhances operational safety, but also shortens field construction time.
Innovation and Development of Pipeline Cleaning Robot
Existing pipeline robots are primarily used for clean sewers and air ducts. Equipped with either a horizontal or vertical movement function only, these robots clean pipelines using high-pressure water jets and brushes. However, such pipeline robots cannot be used in LNG pipelines because the layout of a LNG pipeline consists of both horizontal and vertical sections and water jets cannot be used to clean them. In an effort to ensure movement in both horizontal and vertical sections in these pipelines while meeting the cleaning needs of cryogenic LNG pipelines, CTCI’s Construction Division teamed up with Research and Innovation Center and applied for a R&D program support from CTCI Foundation, namely the “Industrial Pipeline Cleaning Technology Development Project”. Moreover, CTCI outsourced to Intelligent Vehicle Developing Lab at the Department of Electronic Engineering, Cheng Shiu University (CSU) to assist in the design and manufacture of a pipeline cleaning robot using the worm-like movement technique, as well as conduct research on the cleaning techniques for the inner walls of weld joints and the internal gaps of valves. The pipeline cleaning robot developed in this project is primarily aimed at addressing various problems in cryogenic LNG pipelines, such as the accumulation of slags in the internal gaps of butt weld ball valves. Therefore, the pipeline cleaning robot includes a number of major functions. The robot can move inside a pipeline and through vertical and horizontal pipes, elbows, tees, reducers, etc. It carries out real-time visual inspection of the cleanliness inside the pipeline, and cleans up slags that stick on the inner walls of weld joints and accumulate in the internal gaps of valves in the pipeline. This project has completed the development and manufacture of the prototype robot in 2020. This cleaning robot, whose body consists of a moving unit, a video unit, and a cleaning unit, can be operated inside a pipeline using a sensor transmission and control unit. Furthermore, a test skid has also been built at CSU for the purpose of simulating an actual pipeline (as shown in the figure below), which provides the development team with a field to test the prototype robot repeatedly, identify defects for improving the prototype robot, and thus complete the factory acceptance test (FAT).
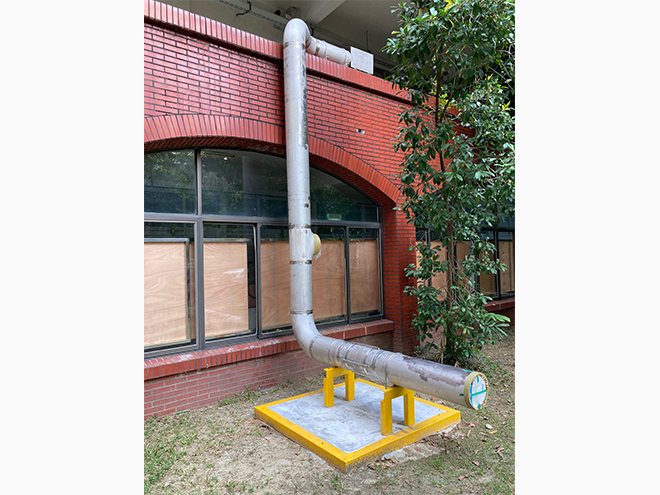
Test skid at CSU
In mid-2021, the pipeline cleaning robot was tested at the site of the China General Terminal & Distribution Corporation (CGTDC) Petrochemical Tank Farm project in Kaohsiung City. Specifically, it overcame the challenges of turning inside the elbow and resistance to gravity during vertical crawling, display clear images of the inside of the pipeline in real time, and carried out cleaning task normally (as shown in the figures below), thereby completing the site acceptance test (SAT) successfully.
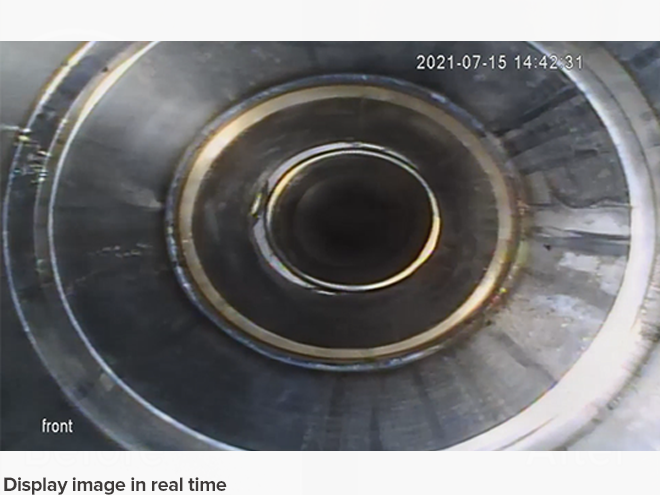
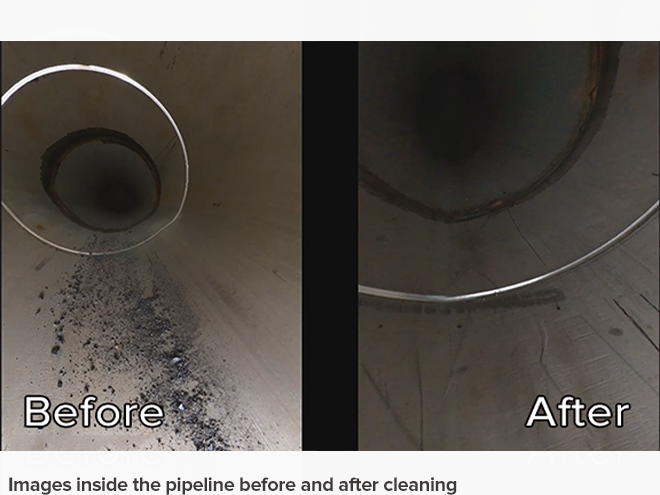
At the end of 2021, the pipeline cleaning robot was introduced and used at the site of the Adani LNG Receiving Terminal Regas Facilities Project at Dhamra Port, Odisha in the east coast of India. The field operation of the pipeline cleaning robot is illustrated in the figures below.
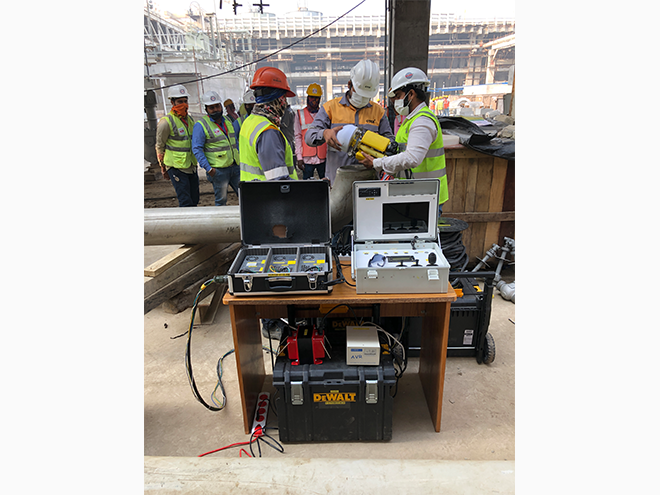
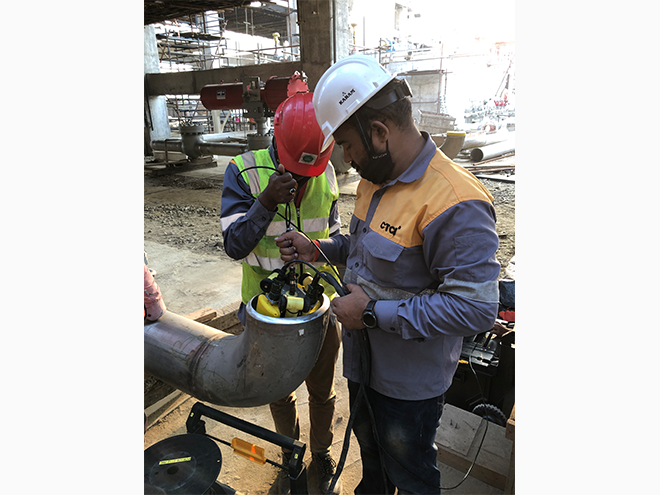
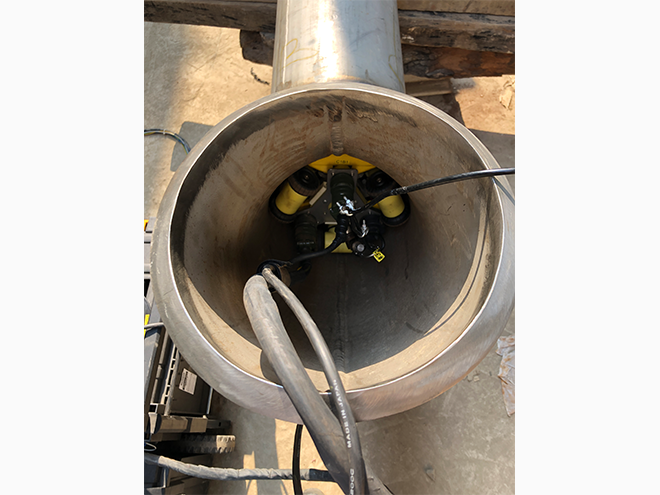

Field Operation Mode of Cleaning Robot
The CTCI team developed a field operation mode based on the experience of field operation of the pipeline cleaning robot at the Indian site. This mode is expected to improve the cleanliness of pipelines and reduce the chance of valve leakage while cutting down the consumption of other types of gases used for pipeline inspection, such as nitrogen and cryogenic natural gas. More importantly, it can prolong the service life and reliability of valves and other accessories such as instruments and pumps when the pipelines come into operation in the future, thus providing a safer and more economical operating environment for the client. Traditionally, cryogenic pipeline blowing is mainly carried out by releasing pressurized gas or using foam pigs. However, the actual cleaning performance can only be determined based on the amount of discharge particles through this method. The pipeline cleaning technique developed in this project allows for a more complete inspection of the inside of the pipeline and enhances the ability to locally clean the leeward sides of gaps, sludge or protrusions, which are things that cannot be overcome by previous techniques. Therefore, this pipeline cleaning technique is going to play a vital role in CTCI’s construction work in the future. In the past, the cables of borescope inspection are usually no more than 15 meters long, and it is often impossible to move them further forward especially when there are elbows in the pipeline. The pipeline cleaning technique developed in this project also provides owners of petrochemical pipelines with the option of going deep inside the pipeline to inspect the appearance of the parts after operation. Due to the ability of local cleaning in this technique, the inspection data obtained using this technique are expected to be more accurate than those using the traditional technique, which can be regarded as important references for preservation and maintenance or performance tuning of process.
Conclusions
Through this project, the CTCI team has successfully developed the “Pipeline Cleaning Robot”, which is the first application model of in-pipe moving vehicle. In the future, different techniques can be developed for the domains of inspection and construction based on this vehicle, which in turn provides the petrochemical industry with new and reliable techniques with great potential for development. As far as market application strategy is concerned, this technique can be gradually promoted and improved in close cooperation with actual operators during the periods of piping installation and cleaning, thereby creating the highest application value in the process.