Discover Reliable
發現信賴
CTCI Successfully Delivers the World's Largest Onshore Modular Project – GCGV 1.1 Million Tons MEG Project
— Roger Chuang, Senior Project Manager, CTCI Group Engineering Business
- Market category:Hydrocarbon
- Owner:Gulf Coast Growth Venture (GCGV)
- Executing unit:CTCI McDermott Integrated (Offshore)
- Completion date:2021
- Location:Corpus Christi, Texas, USA
- Scope of engineering:Engineering, procurement, modularization, and construction
- Capacity: Annual output of 1.1 million metric tons mono-ethylene glycol (MEG)
Gulf Coast Growth Venture (GCGV), is a joint venture company formed by Exxon Mobil, a world-famous oil company, and Saudi Basic Industries Corporation (SABIC). This project was initiated in view of the abundant resources of low-cost shale gas in the United States. The Texas-based plants is now the world's largest onshore modular petrochemical plant, and the MEG plant in this project is one of the key components. This large-scale modular project is jointly undertaken by the CTCI McDermott Integrated (CMI) team composed of CTCI and U.S. McDermott. The modularization project is implemented in different places across the world, including Taiwan, the United States, mainland China, Mexico, India and Malaysia. Project members from various cultural backgrounds brought in their own professional knowledge background and project implementation experience, took various indicators of the project’s vision as the project’s core spirit; under the strong leadership of the owner's project team, CTCI closely integrated with partners, module prefabrication yards, subcontractors and material suppliers into one team to overcome difficulties and challenges in the implementation process, successfully completing the module prefabrication, and transported the five largest modules with a total weight of nearly 40,000 tons to the construction site in the US via the Cape of Good Hope and the Panama Canal for assembly. (Click on the link to watch the video of the module transportation process.) With the advantage of modularization, the project team, successfully completed the module assembly within six months and reached mechanical completion in July 2021, significantly reducing on-site working hours. The plant officially started production in the first quarter of 2022, supplying millions tons of ethylene glycol every year, and creates thousands of job opportunities for the local area. In addition to setting the world's largest onshore modular engineering record, this project is also an important milestone for CTCI to expand its equipment modularization experience to whole plant modularization.

Vision Wheel of GCGV MEG project.
Why CTCI?
Professional engineering integration, real-time information sharing & exchange, and strict intellectual property control
With rich engineering performance and excellent horizontal communication and coordination, the joint venture formed by CTCI and McDermott stands out from the competitors. As transnational engineering projects have become a trend, success of engineering project depends on professional knowledge and technique in different fields from across the world, and smooth exchanges of experience among project members and transfer of information such as engineering drawings becomes the key. In addition to combining CTCI's rich experience in the construction of onshore hydrocarbon turnkey plants and McDermott's modularization related technology in offshore oil drilling platforms, the project utilized an information exchange system (Project on Web, POW) that allows project members in Taipei, the United States, China, Mexico and other places to share project information in real time. The project owner could easily check the implementation status of the project and review the design and procurement documents through transparent information channels, and give timely feedback to facilitate the project progress. While enjoying the convenience of friendly information exchanges, the project members strictly abide by the information security and intellectual property confidentiality protocols, pay attention to the confidentiality and sensitivity of information and the essential recipients when transmitting information. The project office also rigorously acts on the access control policy.
Reliable Realized
Perfect planning and optimized procurement & supply
Unlike traditional engineering projects, which only have a single job site, this project adopts modular application. According to the capacity characteristics of the module prefabrication yard, the main process modules are moved out from the United States to the two module fabrication yards in Qingdao, China and Tampico, Mexico for prefabrication. Only the foundation piles, foundations and underground pipes that cannot be modularized are carried out at the US site. In addition, considering that the engineering design and procurement operations are majorly in Asia, Taipei had been established as a horizontal coordination hub to provide engineering drawings and facilitates materials expediting according to the project needs and progress. Under the supervision of project director, project managers of each region have their independent project teams responsible for module prefabrication and onsite construction. Apart from mutual coordination and communication , there are teams responsible for the HSE, quality, contract and project control functions that directly report to the project director and provide strategies and assistance when necessary. Specifically, the Taipei project team needs to overcome a time difference of 14 hours and act as a bridge for horizontal communication among the project teams in six different regions (Taiwan, the United States, China, Malaysia, India and Mexico) to coordinate drawings availability and material delivery.
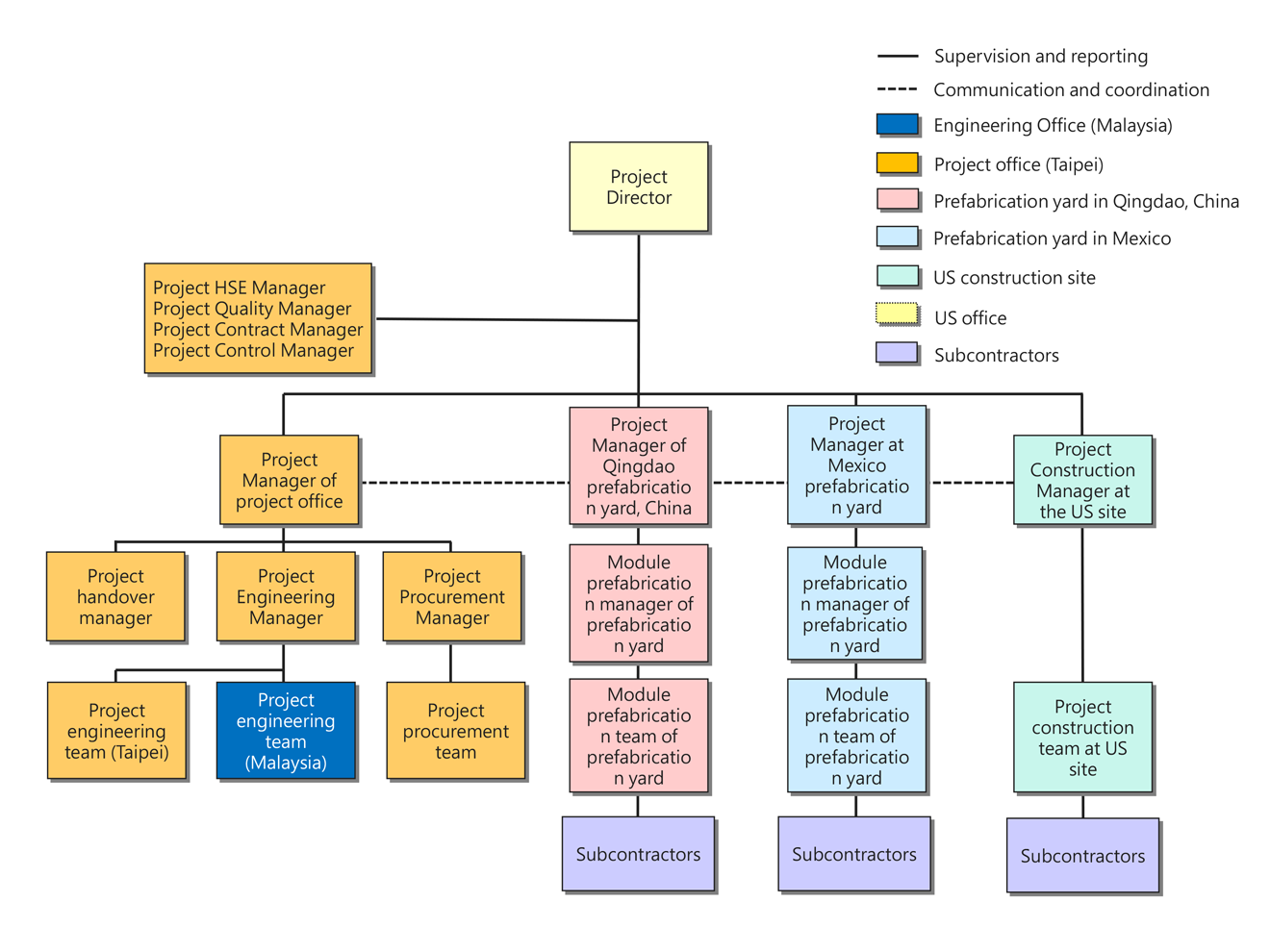
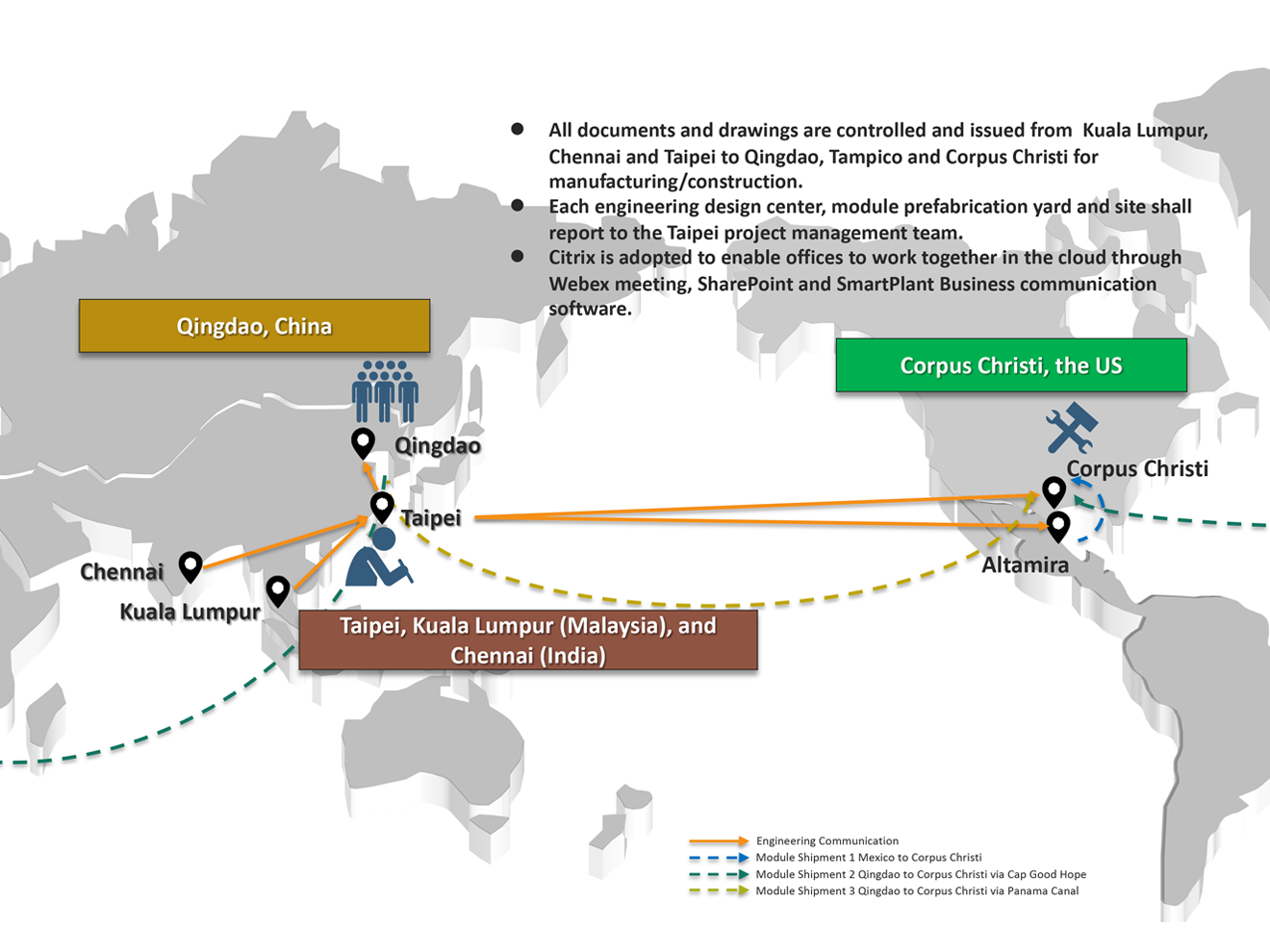
Module prefabrication and Required At Site (RAS) dates for drawings, equipment and materials are the essence of project management and schedule control. In order to meet the prefabrication and construction schedule, issue date and estimated time of arrival (ETA) of various drawings and materials needs to be specially stipulated. In particular, due to the characteristics of module prefabrication, pancake and deck stack up is often a critical path item for the project. In the case of distinctive positions or heavy equipment, installation from the side after stackup would not be possible; in order to prevent delay of subsequent work items and of construction period caused by failure to install, it is necessary to make comprehensive assessment and check on the weight, size and location of each piece of equipment in terms of schedule to determine the priority of each material and ensure smooth installation of the equipment. In terms of procurement, modularization project has the characteristics of multiple tasks at prefabrication yards and construction sites working in parallel, and its material management is more complicated than conventional construction method. Therefore, supplier source for procurement items (including selection of their countries/locations) and even logistics arrangements such as sea, land and air transportation have a crucial impact on the work fronts of prefabrication yards and construction sites. To successfully implement procurement task, two crucial strategies have been adopted in this mega-module project. First, pre-bid was carryout out for the critical equipment. We approached a number of suppliers at early stage of the project, to inquire about the bids, detailized requirements in terms of specifications and requirement date, and obtained solicitation documents on product specifications, quantities, delivery dates, etc. from suppliers in various countries. After multiple pre-bid meetings, a consensus on cooperation has been reached, which effectively accelerated the cumbersome procurement process in the early stage and facilitated the implementation of subsequent engineering design and other project tasks. The second strategy is to adopt a large number of suppliers in Asia. A considerable amount of module prefabrication works were performed by module prefabrication yards located in China. On that ground, in addition to the approved vendor list (AVL) provided by the owner, procurement and materials was mainly sourced from local Chinese vendors or those from neighboring Asian countries, such as Taiwan, Japan, Malaysia, India, Thailand and South Korea, so as to facilitate priority planning for prefabrication and construction drawings.
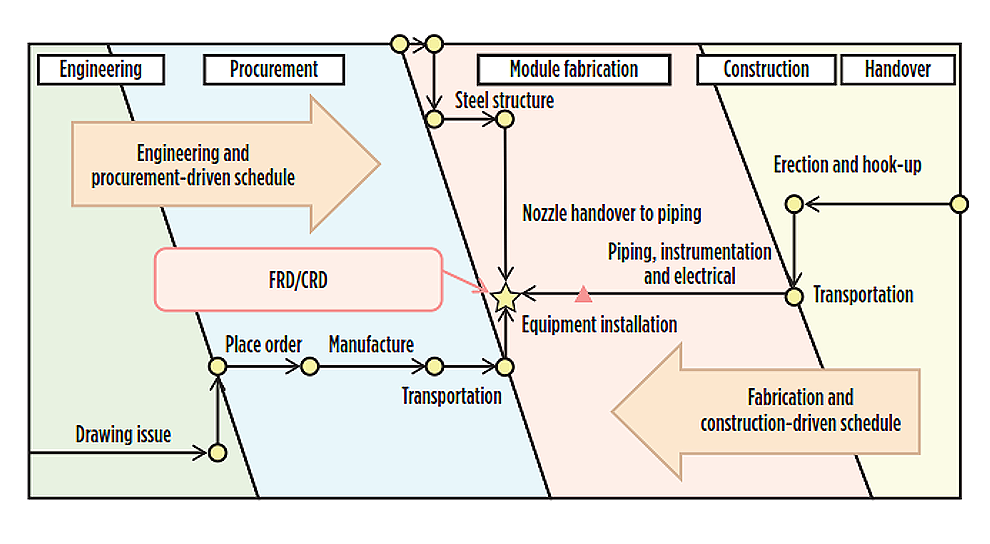
Project Highlight
Minimize on-site operation and manpower requirements
The purpose of modular engineering is to systematically and centrally integrate the process equipment and piping lines, and move them out in modular type to the prefabrication yard. The more items are moved out, the higher the degree of modularization of the project. Through well-grounded module planning, the space utilization efficiency of equipment and piping of prefabricated units can be improved, and the number of prefabricated units required and the site module occupation reduced. These additional plant space vacated by modularization and optimized configuration can be used by the owner as an advanced configuration for improving production capacity or as space for future plant expansion. With the modularization of most process related equipment and systems to the prefabrication yard, workload on the construction site is reduced, and the demand for construction manpower and equipment resources is optimized. Construction work can be carried out in a relatively spacious working space with a safer environment and strengthened industrial safety management. Due to this reason, more than 14 million safe man-hours without lost-time injuries have been accumulated during the implementation of this project.
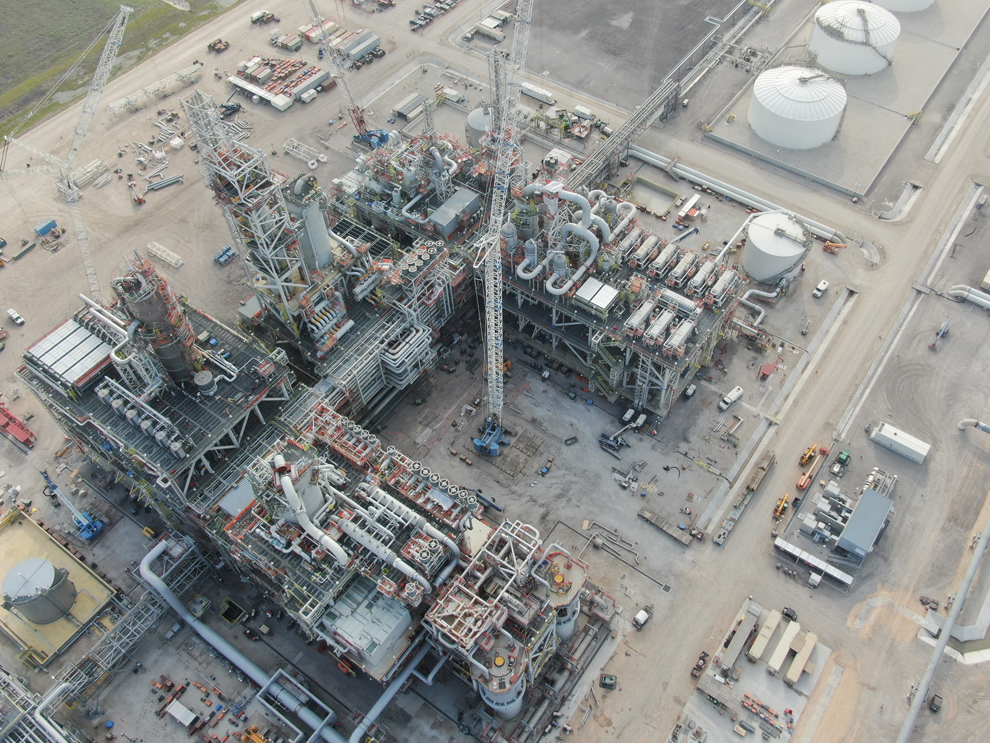
Smarter Engineering
Application of module engineering improves planning flexibility & execution efficiency
Module engineering emphasizes efficiency, with prefabrication and engineering design carried out concurrently. As soon as the main structure design is completed, shop drawing can be made and steel structure prefabrication (first cut) can be initiated. Therefore, weight management is one of the key highlights of the project. The weight control report records the changes of module weight, size and center of gravity from the initial engineering data to the completion of prefabrication. The design parameters are input to the modeling software to model steel structures, piping and other work items. With the progress of the project, the model is constantly updated, and the software automatically calculates and produces a new weight report, so that the module yard can manage prefabrication work and adjust process accordingly. In order to cope with the huge prefabrication work, the selection of prefabrication yards must be centered on a number of evaluation criteria. In addition to sufficient prefabrication and installation working space, attention should also be paid to their geographical location, past achievements, prefabrication plant capacity, human resource allocation, and other indoor and outdoor auxiliary facilities such as blasting and painting plant, warehousing and storage, quay capacities, and so on. Moreover, location of the selected yards also reflects the accessibility for coordinating resource and transportation types to suppliers in various countries. At the same time, stability of the weather in the region with factors such as typhoons, sandstorms, earthquakes and so on must be duly considered. Among them, the manpower and facilities of the prefabrication yards are the most decisive factors for production capacity and production stability. The prefabrication yards selected for this project are located in the free trade zone and tax-free zone of Qingdao and Mexico, respectively, so that the imported and exported materials and equipment can be exempted from custom tariffs , which is also one of the benefits of choosing prefabrication yard. The application of modular engineering technology has multiple advantages. It is better than conventional construction in that it improves the safety of the construction environment, reduces on-site man hours, saves costs, and ensures timely delivery.
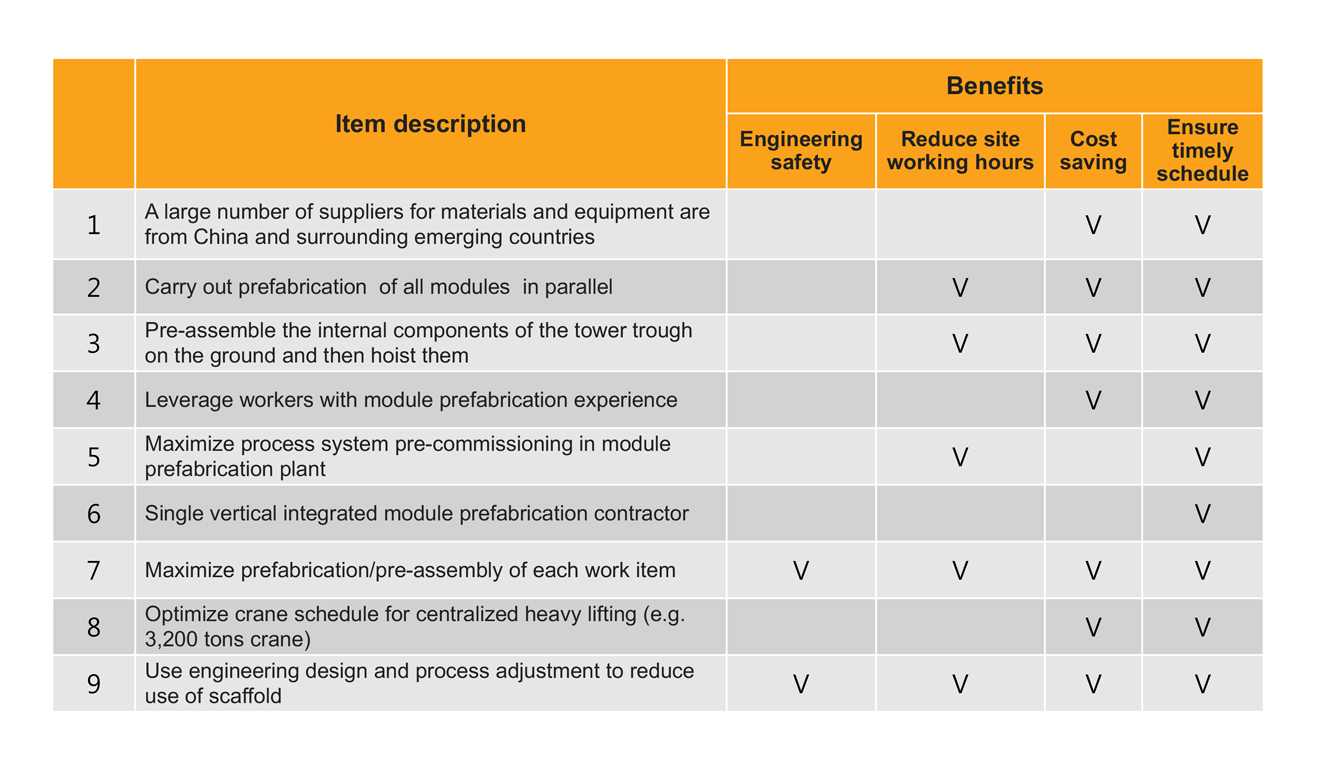
Benefits of modularization projects
Message from the Group Chairman
CTCI is honored to be part of this world's largest onshore modular turnkey project. The implementation of this project spans six places, including Taiwan, the United States, mainland China, Mexico, India, and Malaysia. While team members come from all over the world, we worked together under one common goal to overcome the challenges in the process brought by the COVID-19 pandemic, and successfully completed the engineering design, prefabrication, assembly and reached mechanical completion. This sets a new record for CTCI's international project execution and a new milestone in modularization. --John T. Yu, Group Chairman of CTCI