Discover Reliable
發現信賴
CTCI Creates New Value from Old Plant: Hsi-Chou Energy-from-Waste Plant Renovation Project in Changhua
— Eric Tiao, President of ECOVE Environment Services Corporation, Group Resource Cycling Business
- Market:Energy-from-waste; electrical & mechanical maintenance
- Owner:Environmental Protection Bureau, Changhua County
- Executive team:ECOVE Environment Services Corporation
- Completion time:June 2, 2021- December 31, 2025
- Project location:Hsi-Chou Energy-from-Waste Plant, Changhua County
- Project Scope:Upgrading and prolonging the use of the incineration equipment
The Hsi-Chou Energy-from-Waste (EfW) Plant in Changhua County (Hsi-Chou Plant) is one of the major facilities in Changhua County with a mission to promote zero waste and waste recycling. Over 20 years, the plant has been responsible for the recycling of wastes around the county, and is now in need of repair. In 2021, the Chuanghua County Government held an open bidding to delegate the plant operating rights for the following 15 years while upgrading the entire plant facilities. ECOVE Environment Services Corporation (ECOVE ESC), an affiliate of CTCI, won the bid based on its years of experience in EfW plant operation and renovation.
Why CTCI?
A team dedicated to handle the entire waste treatment process
Among the 24 EfW plants currently under operation in Taiwan, 20 of them have operated for more than 15 years. There will be more plants reaching their lifespan in the coming years. The efficacy of these plants may deteriorate as plants become old and suffer from low design calorific value, leading to lower amount of waste treated per day, or even causing a crisis when there is no more place to treat the waste. Therefore, the Environmental Protection Administration proposed the "Waste Treatment Diversification Plan" in 2017 to fulfill the vision of waste recycling and circular economy. More than half of the budget went into renovating EfW facilities. Ever since the 1980s, when Taiwan first started to encourage waste incineration, CTCI has dedicated itself to this field and became the only investor in Taiwan that is capable of carrying out turnkey solutions for EfW plants. As an affiliate of CTCI, ECOVE ESC takes on the task of incineration operation in big cities from home and abroad, while another affiliate, ECOVE Waste Management Corporation, offers services including waste management, cleaning, and recycling. The team not only provides an all-round service but is also the first Taiwanese company that brings its incineration expertise overseas. With years of experience in plant operation, CTCI well understands the importance of EfW plant renovation, and is eligible to complete this project with a comprehensive plan and advanced technologies.
Reliable Realized
I. 3 Principles to Complete the Renovation and Enhance Performance
Waste continues to be generated endlessly. It requires the integration cability, professional technologies, and hands-on practices to make sure the aging EfW plants can handle increasing amount of waste efficiently while complying with the latest pollution regulations. Following the Kanding EfW Plant Renovation Project, Gangshang EfW Plant Renovation Project, and Chengxi EfW Plant Renovation Project, CTCI carried out thorough assessments on Hsi-Chou EfW Plant based on the following three principles, as well as made detailed and customized plan for the plant by taking account of its characteristics and bottleneck: (1) Improve the capacity of incineration: This is done by figuring out the factors that affect incineration capacity and make repairs to increase such capacity. Smart management is adopted to enhance operating stability. (2) Increase energy efficiency: This is done by broadening the sources and controlling the consumption. For instance, we added incinerator tubes to increase air generation, and upgraded the variable-frequency drive (VFD) to reduce power consumption. (3) Enhance pollution prevention: We organize the air pollution system according to the latest emissions standards and the local air quality.
II. Shorten the construction schedule and help owners handle the waste during the construction period
To upgrade EfW plants, waste treatment during the plant suspension is a problem. Well aware of this challenge, CTCI focused on shortening the construction schedule in addition to the three principles it sticks to. As the top 100 engineering company in the world, CTCI has abundant experience in engineering, procurement, and construction. CTCI shortens the construction time by having full preparation and the ability to integrate. CTCI arranges different construction that can be carried out simultaneously, and ensures the facility, materials, and manpower are in place to carry out the project. The experienced construction team supervises the whole operation based on the standardized process to ensure the outcomes meet the standards and follow the plan. Based on the principles stated above and the past experiences, CTCI won the bid for Hsi-Chou Incineration Plant with a complete and feasible plan, and the plan is now being executed. From the beginning, CTCI actively communicated with the owner to make efficient plans and resolve the problem of waste treatment during construction. It is hoped that this comprehensive plan can be turned into facilities that echo the concept of the circular economy and create new values.
Project Highlight
Improve the capacity of incineration, increase energy efficiency, and enhance pollution prevention
The objectives made by the owners align with CTCI's three principles, namely, improving the capacity of incineration, increasing energy efficiency, and enhancing pollution prevention. As always, with a complete plan and stringent attitude, CTCI effectively solves the waste problem for the county in the following 15 years. Below is the summary:
I. Improve the capacity of incineration
To achieve this objective, CTCI takes a dual approach that includes both hardware and software solutions: In terms of software solutions, smart management is incorporated into the waste system. For instance, weighing systems have been renovated. The monitoring systems in the public areas such as the weighing platform are completed. Car plate identification is adopted to strengthen information security and elevate security mechanisms. Additionally, CTCI also monitors the vehicles entering and leaving the plant, tracking their loading condition and waste quality to ensure the safety of the government's property. For hardware solutions, inspections are carried out on each system. Through upgrades and adopting foreign technologies, the stability and performance of the incineration plant are improved. Examples include: (1) Mobile shredding machines to increase bulk waste treatment. (2) Upgrade the waste crane system (including the tracks, controller, and inverter) to make garbage trucks moving more flexibly and fast. Enhance the crane availability to increase waste treatment capacity during peak times, preventing traffic jams. (3) Upgrade the material of water tubes to high alloy steel to prevent corrosion and enhance stability. (4) Add slag-cleaning equipment to the flues to improve the efficiency of slag cleaning in the superheater, thus enhancing the furnace performance and reducing gas consumption.
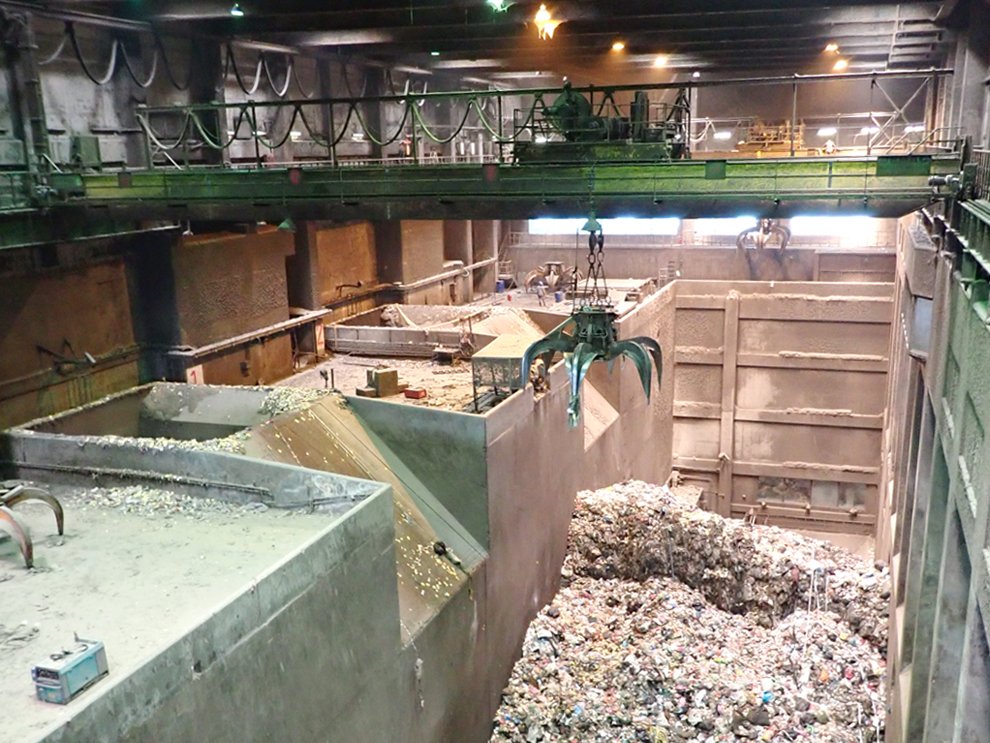
The team upgraded the waste crane system to optimize its uptime. The team also enhanced the crane availability to increase waste treatment capacity during peak times, preventing traffic jams.
Considering the supply stability of the components in the following 15 years, CTCI carried out a facility deterioration assessment covering construction safety, firefighting, and information security. Facilities can maintain their performance through component optimization, renewal, and repair. The facilities include: burner air-fuel ratio setter; atomizer booster for semi‑dry smoke scrubber; impellers; bearings, bearing box, and shafts on the side of induced draft fan impellers; vibration sensors and deviating sensors for the shaft of power generators; automatic voltage regulator (AVR); PCB for field exciter; oil cleaning machines; ash cranes; motor controller center (MCC); air circuit breaker (ACB); cast resin transformer (CRT); and auxiliary systems (such as monitoring system, telephone system, and fire alarm system). It is hoped that the improvements can make sure the Hsi-Chou EfW Plant remains at least 91% in operation.
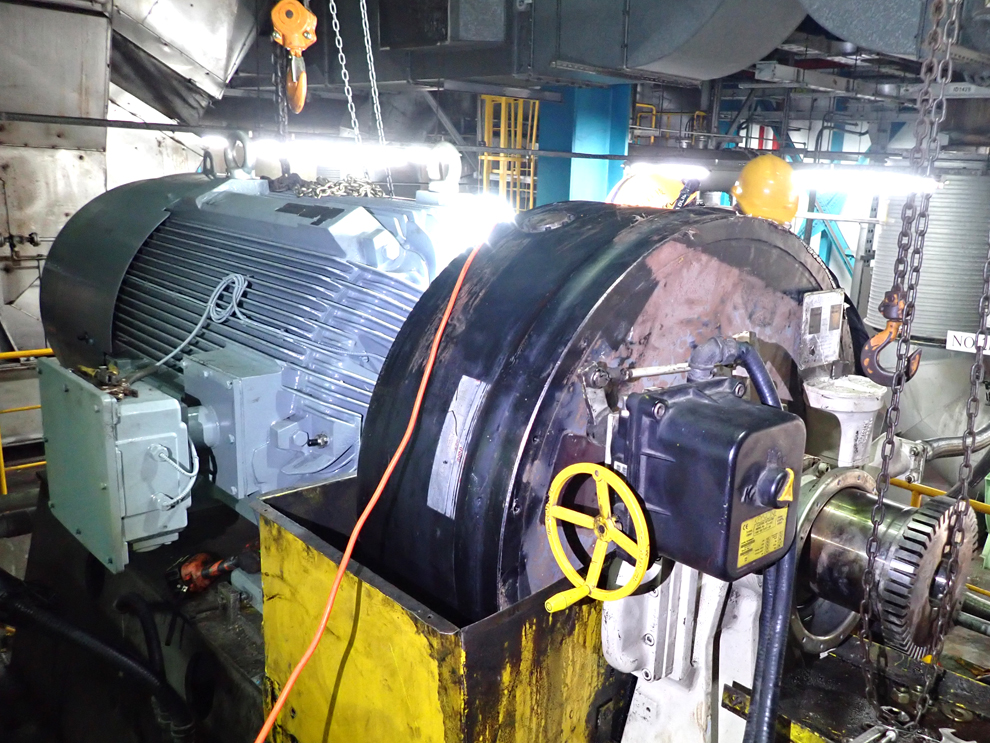
Considering the stable operation in the following 15 years, deviation assessments are carried out for various facilities. The picture here shows the inspection of the induced draft fan.
II. Enhance Energy Efficiency
Given the need for energy conservation, carbon reduction, and net zero emissions, waste incineration is considered as a form of renewable energy. By reducing the amount of power consumption, more power in the form of renewable energy can be generated. After assessing the possible factors of power consumption, CTCI team not only optimized the process but also replaces power consuming facilities with energy-conserving facilities, which include: (1) Air-cooled Condenser (ACC): Substitute the materials of the fans from alloy to FRP, which helps reduce air resistance and power consumption. (2) Add absorption chiller to cut power usage. (3) Upgrade oil-free compressor and switch to inverter-control mode to enhance performance. (4) Add inverter for primary and secondary fan motors. (5) High-power motor is replaced by high-efficiency motor (IE3) With the plans above, the expected power saved annually can reach 3 million kWh, with an annual carbon reduction of about 1,500 tonnes.
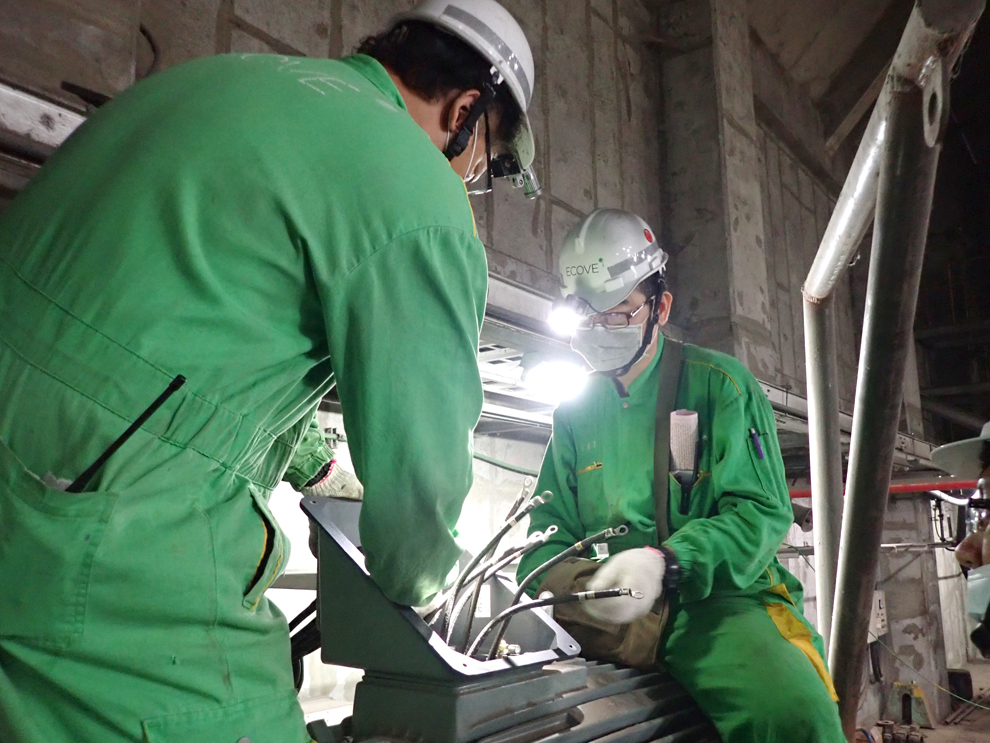
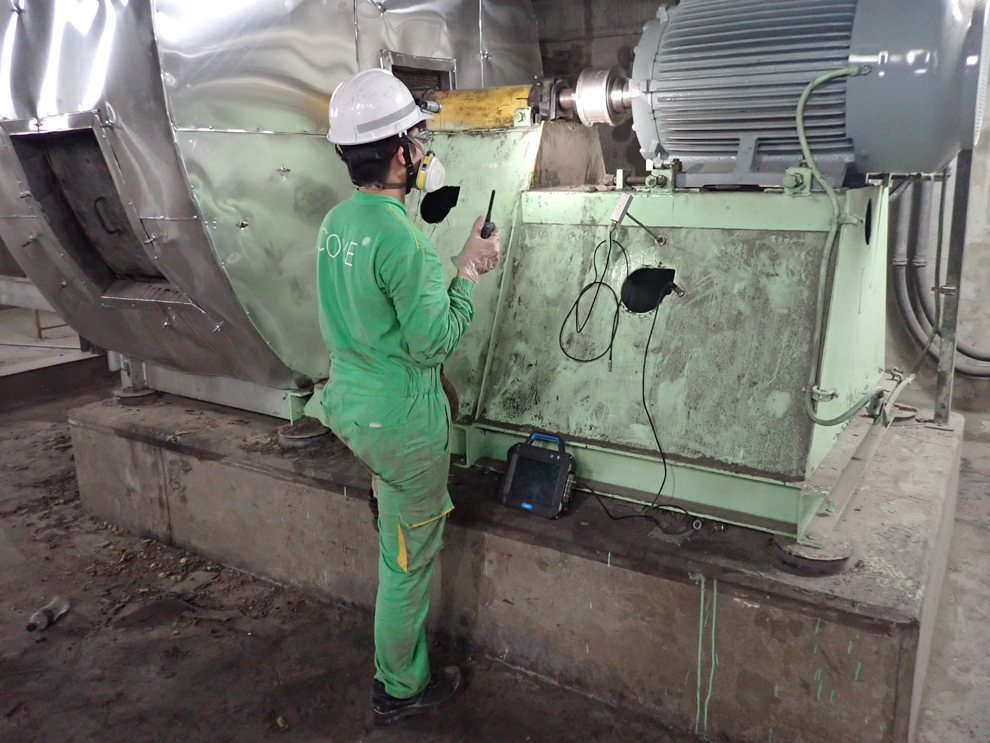
III. Enhance pollution prevention
In terms of pollution prevention, CTCI optimized the relevant facilities, including: (1) Upgrade Selective Non-Catalytic Reduction (SNCR) equipment: This significantly helps reduce the emissions of nitrogen oxides to less than 70 ppm, which is lower than the standard 85 ppm as regulated by the Guidelines for Reducing Pollutant Emissions from Existing Pollution Sources in the Tertiary Control Zone announced by Environmental Protection Administration in 2020. (2) Enhance air pollution monitoring system: Upgrade 24/7 Continuous Emission Monitoring Systems (CEMS) to optimize the pollution prevention. To handle the inevitable flying ashes that come from incineration, CTCI team reorganized the plant layout and upgraded the vibrating kneaders to batch systems. The new system can be installed outside the plant, increasing the kneading performance. The expected reduction of stabilizer can reach 8%, prolonging the plant lifespan.
Smarter Engineering
I. Efficient amorphous metal transformer
Transformer is crucial in electric power transmission. CTCI uses efficient amorphous metal transformer instead of silicon steel transformer. Compared to the traditional transformer, the amorphous metal transformer can increase 25% of power efficiency and minimize the wear of iron, which satisfies efficiency and power conservation requirements. Even though the procurement cost would increase, overall power consumption would decline. The amorphous metal transformer adopted by the team is green product certified by Energy Commission, Ministry of Economic Affairs. Thanks to the adoption, CTCI was commended as a Green Procurement Unit by Changhua County Government.
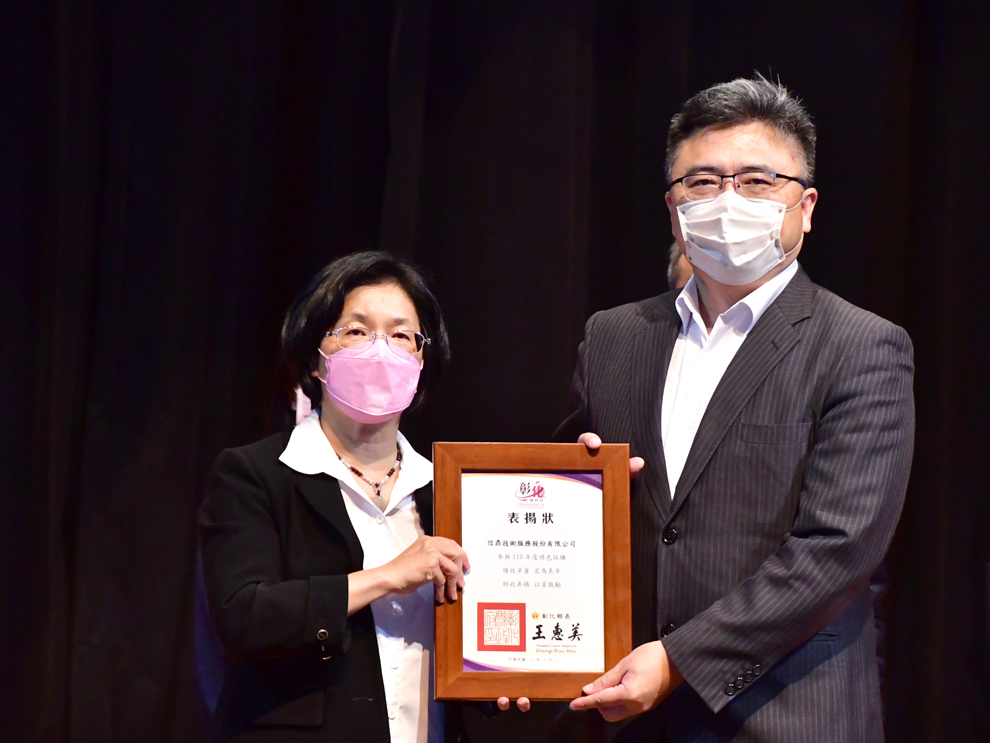
Hsi-Chou EfW Plant used the green products certified by the Energy Commission, Ministry of Economic Affairs, and won the Green Procurement Unit award. Eric Tiao (right), President of ECOVE ESC, attended the award ceremony and received the award from the County Mayor Hui-Mei Wang.
II. Switching to fluid mechanics FRP fan blades to achieve immediate power conservation results
ACC is a high power-consuming facility. To reduce the power used, transformers were installed. During a low workload, the fan will operate at a low frequency, but during a high workload, the transformer cannot reach expected results. Therefore, CTCI team used fiberglass reinforced plastics (FRP) to replace the alloy steel fans. FRP fans are lightweight, durable and flexible. These features allow fans to be designed according to the plant requirements, with ideal thickness, radian, numbers, and angles. Such optimization can enhance operating efficiency, lower motor workload, and reduce power consumption.
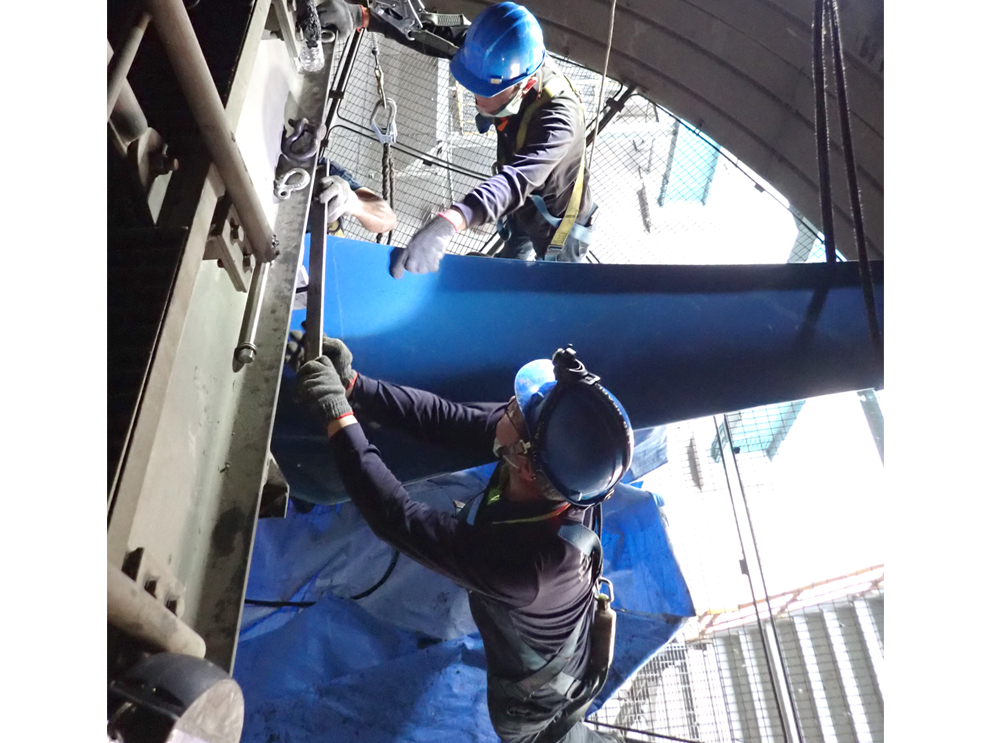

III. High alloy steel for furnace water tubes to conserve more energy and maintain stable operation
Due to corrosion from flue gas, the tubes become thinner, often leading to unexpected downtime. With years of experience in EfW plants and co-research with suppliers, high alloy steel tubes were installed in areas of the plant that have higher risks of acid corrosion and heat corrosion. The installation was extended to the 2nd flue during bidding to effectively reduce downtime risk and prolong the tube’s lifespan.
Hsi-Chou EfW Plant has now operated for 20 years. Ever since ECOVE ESC took over in June 2021, we have seen great performance. As of the end of 2021, the incineration amount has a year-over-year increase of 4,800 tonnes, while the operating rate increased by 1.8%. During the repair downtime, CTCI rescheduled the construction time to cooperate with the County Government. We appreciate the professionalism and effort brought by the ECOVE team. --Deng-Jia, Yeh, Director of Environment Engineering Division, Environmental Protection Bureau, Changhua County