Technology
技術分享
Case Study of Energy Saving Technology Applications in Incineration Plants
— Chen-Cheng Kao, General Manager, Project Division I, ECOVE Environment Service Corp., Group Resource Cycling Business — Qiao-Xin,Cai, Engineer, Project Division I, ECOVE Environment Service Corp., Group Resource Cycling Business — Jian-Hao,Hung, Engineer, Xizhou Incineration Plant, ECOVE Environment Service Corp., Group Resource Cycling Business
As climate change becomes one of the greatest threats in global sustainable developments, nations around the world have begun to announce their net zero emissions goals. Taiwan has also started to amend the "Greenhouse Gas Reduction and Management Act" to be the "Climate Change Response Act." Besides the inclusion of "2050 Net Zero Emissions Goals," the Act will also promote the carbon pricing system. ECOVE, a CTCI company, has been putting a lot of efforts on the incineration and electromechanical maintenance sectors for over 20 years. In order to respond to the global trend of net zero emissions, the company is actively integrating various energy saving and carbon reducing technologies and applying them to the recent life extension projects of the incineration plants. Most of the existing incineration plants in Taiwan have been operating for nearly 20 years, and modern techniques and technologies make it possible for us to improve the efficiency of equipment and the efficient use of energy. However, due to the requirement to process wastes, the environmental bureaus of various counties and cities do not allow long-term shut down of incineration plants for equipment upgrade. Therefore, energy efficiency improvements are mostly focused on the optimization of equipment with high power consumption. In our plan to upgrade the equipment of incineration plants, we have called upon personnel with extensive operating experience and excellent project management skills to conduct systematic checks and analysis of incineration plants. The personnel will propose improvement plans for energy saving, carbon reduction, and utilization of waste heat during the relatively shorter shut down period of incineration plants. The following table uses the recently-upgraded incineration plants in Tainan, Xizhou, and Gangshan as examples to introduce the 5 items of improvement regarding energy saving plan for equipment with high power consumption in incineration plants.
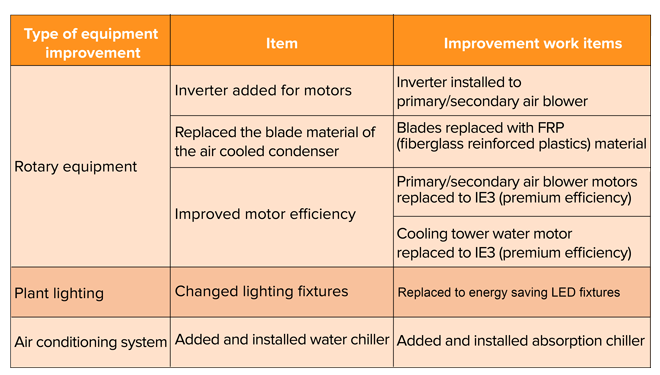
Table 1 Improvement plan of energy saving equipment
Improved Energy Saving Equipment to Increase Carbon Reductions
1. Installed Motor Inverters
By controlling the frequency, the inverter can help the rotary equipment maintain low speeds under light loads in order to achieve energy saving effects. Additionally, because of the soft starter device it equipped, it can temporarily reduce the power load during start-up of rotary equipment. For example, the variable frequency air conditioners that are familiar to most can properly adjust compressor operations to achieve energy saving effects as the compressor is under the control of the frequency variation function. To achieve energy saving effects, there are certain conditions for the installation of inverters to motors. The effects are maximized when the inverters are installed on equipment with high power, that are operating on a long-term basis, and with high load variance, such as induced draft fan motors, primary/secondary air blower motors, air cooled condenser motors, and cooling tower motors, which are rotary equipment that operate on a long-term basis and with high power consumption in the incineration plants. For the control block diagram for motors installed with inverters, please refer to figure below. Using the Xizhou and Gangshan incineration plants as examples, which process 900 tons and 1,350 tons of waste per day respectively, installing an inverter on the primary air blower motor can save energy to 400,000 kWh/unit annually. Installing an inverter on the secondary air blower motor can save energy to 300,000 kWh/unit annually.
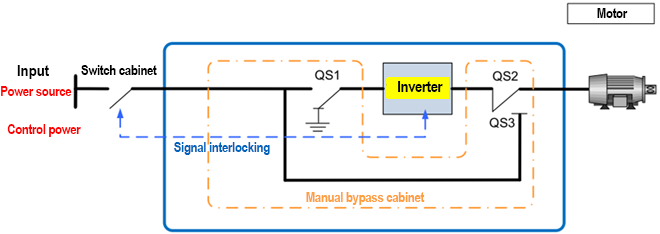
Control block diagram of motors installed with inverters.
2. Replaced the Blade Material of the Air Cooled Condenser
The aluminum alloy material of the air-cooled condenser (ACC) blades can be replaced with fiberglass reinforced plastics (FRP), as shown in the figure below. FRP is a composite material created through composite processes that uses macromolecular epoxy as the matrix and fiberglass as the reinforcement. The advantages of the material include its high unit intensity, corrosion resistance, aging resistance, high/low temperature tolerability, flame resistance, great insulation, and low thermal conduction. FRP can be designed with better tortuosity, curvature, and blade installation angle according to the onsite environment. Once installed, it can reduce motor power consumption under the same operating conditions. Using the Xizhou plant, which processes 900 tons of waste per day, as an example, the replacement of 12 sets of blades made of FRP can save energy by 18% under 100% MCR (maximum continuous rating) speed. It is expected to save 1GWh of power in a year. For the Gangshan plant, which processes 1,350 tons of waste per day, the replacement of 10 sets of blades made of FRP is expected to save 820,000 kWh of power in a year.
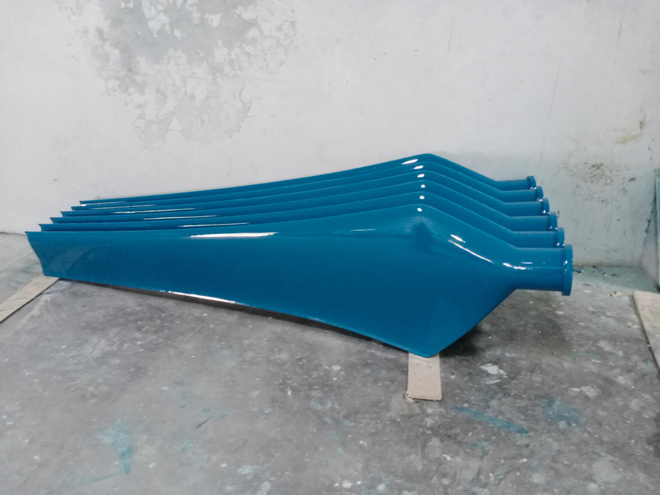
FRP blade
3. Improved Motor Efficiency
The motor is the core device that drives the operation of all power equipment. High efficiency rotary equipment aimed to save energy is now the focus of international developments. In order to harmonize different national motor efficiency standards, the International Electrotechnical Commission (IEC) announced the international efficiency standards in 2008, which ranks three efficiency classes from IE1 (standard efficiency), IE2 (high efficiency), to IE3 (premium efficiency). After the replacement of primary/secondary air blower motors with IE3 motors in the Xizhou plant, the initial estimate of energy saved annually is around 20,000 kWh/unit for primary air blower motors and 405,000 kWh/unit for secondary air blower motors. Additionally, the energy saved for cooling tower motors is around 3,000 kWh/unit per year.
4. Changed Lighting Fixtures
Incineration plants are grouped under Category C of the Hazardous Workplace, making lighting in the plant particularly important. In the light of the trends of environmental protection and energy conservation, environmentally friendly LED products are adopted to replace traditional, high power consumption lighting fixtures. Compared to traditional light sources which convert electricity to thermal energy then to light, LED lights can convert electricity directly into light, providing a more efficient light source. For example, the types of light replacements and light on hours of Gangshan plant (as shown in the table below) are estimated to save 570,000 kWh of power in a year.
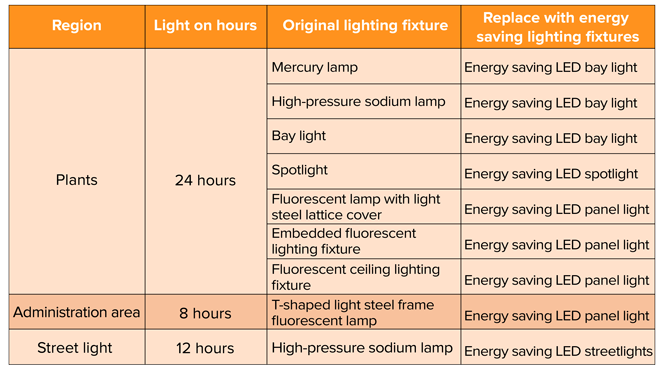
Table 2 Original lighting fixtures and proposed replacements in incineration plants
5. Added and Installed Absorption Chiller
The chiller is a high power consumption equipment in incineration plants. Taking the Xizhou plant, which processes 900 tons of waste per day, as an example, the chiller uses 200 kWh of power every hour in the summer. Absorption chillers, which have become popular in recent days, is able to take advantage of the waste heat in the incineration plants to replace the compressor and drive the chiller with low pressure steam, which greatly reduces the power needed for the chiller. For the Xizhou plant, the absorption chiller saves to 85% to 95% of the power used by the original chiller. The installed absorption chiller can save around 1.02 GWh of power in a year
Breaking the Status Quo and Looking Towards the Future
“Apply technical knowhow to advance efficiencies in ‘resource cycling’” is the corporate mission of ECOVE. To respond to government energy saving policies and combining design and planning, ECOVE has chosen the right energy saving equipment to incineration plants with compliance to project deadlines and conditions onsite, to maintain the operation rate of equipment and enhance the value of incineration plants. While rejuvenating the old incineration plants, ECOVE is also actively responding to the climate change crisis, as well as implementing sustainability in daily operations with core competencies. By making substantial contributions to global sustainability, ECOVE envisions a future with net zero emissions.