Technology
技術分享
Buying Goes Digital: How Technology Aids EPC Company’s Procurement Process
— Shi-Wei Kao, Supply Chain Engineer, CTCI Corp., Group Engineering Business
For any engineering, procurement, and construction (EPC) company, an important factor to business success lies in procurement, the major goal of which is to purchase, manage, and deliver goods on time and with good quality. There are, however, pain spots within conventional procurement process that need to be tackled. A typical procurement process starts from inquiry and quotation, then goes on to price comparison, price negotiation, bid determination, prompt delivery, inspection, transportation, and finally, evaluation of vendor's performance. Each phase involves processing, transferring, and checking huge amount of different data, which are conventionally done by human. Such time-consuming process which is prone to human error becomes pain spots. New digital technologies can help EPC companies address these pain spots, streamline the process, and increase efficiency, which all make a strong case for digital transformation. In this article, we will share five digital applications used by CTCI— a leading EPC contractor on its way to digital transformation— to improve procurement process.
Application 1: Automated Batch Inquiry
An automated batch inquiry frees human from repetitive work and ensures fairness by excluding human judgment. In the past, when procurement staff wished to send out procurement inquiry to vendors, one had to first collect requisitions from the Engineering Department as well as requisition instructions and business regulations, then package this information into several electronic files, and send them to vendors by email with attachments. Since an inquiry had to be conducted with more than one vendor, it was often necessary to repeat the same procedure several times. Moreover, it is possible that not all vendors received the exact same inquiry at the same time, as some information might be altered unintentionally. In 2021, CTCI has rolled out automated batch inquiry, a new and systemic way of managing inquiries. All variables associated with the procurement process are pre-configured in the information system, which allows referral of requisition to procurement inquiry for nearly auto-processing. This greatly cuts human processing time and ensures fairness because all bidding companies receive the exact same inquiry.
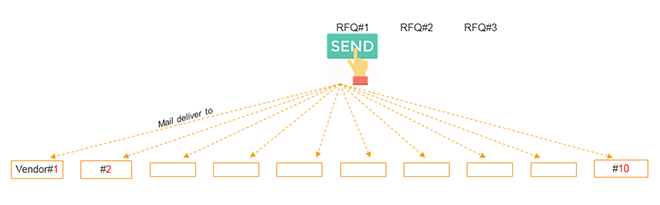
Schematic Diagram of Automated Batch Inquiry
Application 2: Vendor Online Quotation
Traditionally, procurement staff have to input key information in the electronic quotation documents provided by vendors into the database one by one, so that the information may be used for various reports and automatic system notifications. In this case, information accuracy and input time needed will greatly depend on how familiar procurement staff is with the input system, how many vendors are providing quotations, and how complex the quotation items are. This causes unideal information quality and management issues. To deal with this problem, new projects at CTCI since Q2 2021 now adopt SMat Portal (shown below), a new feature added to the commercial software Smart Plant Material (SMat) procurement module. Vendors are required to provide and input quotation information directly on this platform. This not only saves procurement staff’s time, reduces chance of data input error by procurement staff, but also ensures vendor responsibility for the accuracy of input data.
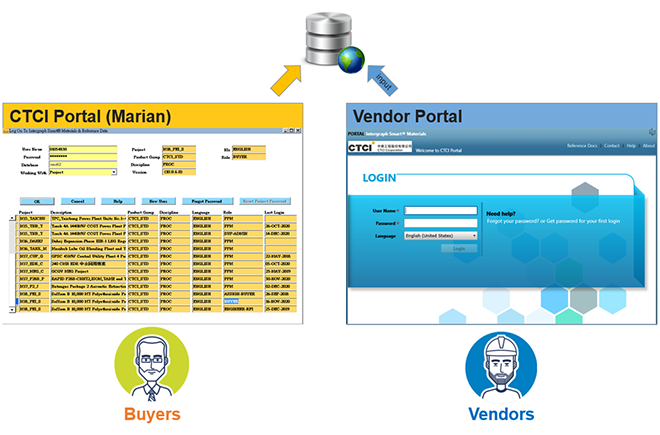
Schematic Diagram of Vendor's Online Quotation
Application 3: Synchronizing Government/Vendor Public Data through RPA/API and Government Open data Platform
Keeping vendor information accurate and up-to-date is critical. That includes legal and valid company name, company operational status, registered address, capital amount, payment account number, and among others. There are two ways to ensure such information is accurate and up-to-date. The first method, similar to vendor online quotation, is to request vendors to input vendor data into online platform directly rather than having procurement staff to do the work. The second method is to leverage vendor’s open data on government platform and synchronize it with CTCI database through robotic process automation (RPA) or application programming interface (API) connection. Beginning from 2021, CTCI screens vendor open data accessible on the “Open Platform for Commercial and Industrial Administrative Data,” a platform made by the Ministry of Economic Affairs. Vendor data can either be retrieved by downloading original CSV files or through API (XML or Jason). If the data needed can be easily obtained from the CSV files, the files are downloaded and then synchronized automatically with CTCI's proprietary RPA technology regularly (as shown below). As for data that is not easily accessible from the files, it is synchronized through API. This ensures that CTCI vendor database is consistent with government data, keeping vendors' data up-to-date and accurate.
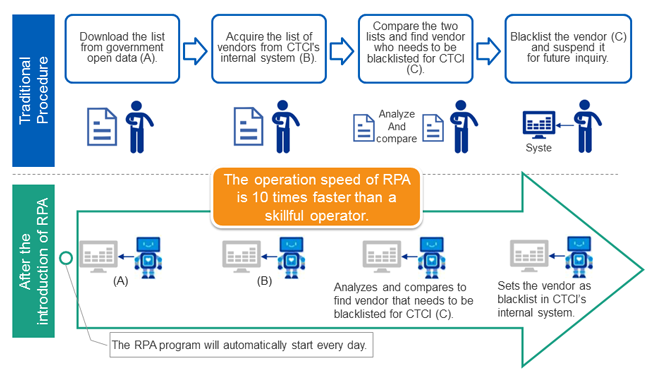
One benefit of RPA in synchronizing open data with CTCI’s database is that it can greatly speed up all processes necessary to identify and take actions against vendors that have been blacklisted by the government.
Application 4: General Terms and Conditions Database
General terms and conditions are detailed and lengthy information included in a vendor contract’s appendix. However, every vendor contract’s terms and conditions may slightly differ. Having a terms and conditions database in place can help organize important information systematically, ease the search for clauses used in the past, reduce chances of human error, and save time for negotiating particular clauses. Beginning in 2021, CTCI uses optical character recognition (OCR) technologies to scan and turn general terms and conditions in paper contracts into digitalized information to be stored in the database, as shown below.
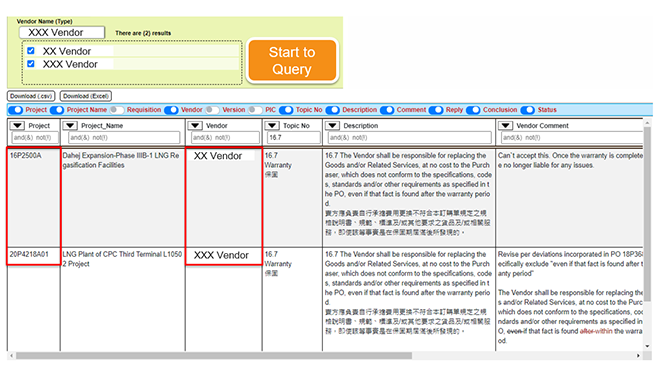
Schematic Diagram of General Terms and Conditions Inquiry System
Application 5: Remote Inspection
Once goods are procured, they must be inspected to make sure they comply with project procurement standards. Thanks to digital technology, some inspections can now be done remotely through cameras. As long as clients and project team accept remote inspection, internet connection is stable, and there is no safety hazard present, remote inspection is always given priority over physical inspection. Each inspection starts with project procurement inspection plan (PPIP) once an order is placed. Then it is planned based on the project equipment/material requisition plan, inspection level, as well as the inspection test requirement provided by the Engineering Department. The PPIP is adjustable by deciding the number of inspections for each requisition, the inspection method (an inspection representative makes in-person visits or through video calls), the candidate for the inspector, and whether the customer will participate in the inspection. Besides goods inspection, remote inspection can also be applied for PIM inter-departmental issue discussions or multiple discipline equipment inspections, such as package facilities and electrical, instrumentation with interfaces, or equipment that needs to be integrated. Remote inspection can also be used for training purposes, such as when a senior instructor remotely guiding an onsite, less-experienced inspector; or let other trainees sit in front of the computer and watch through remote imagery to learn how inspection is done. The following are some of the remote inspection cases in pictures.
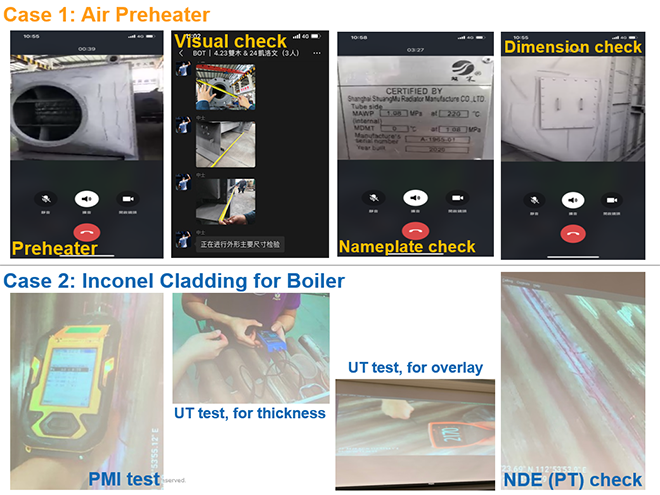
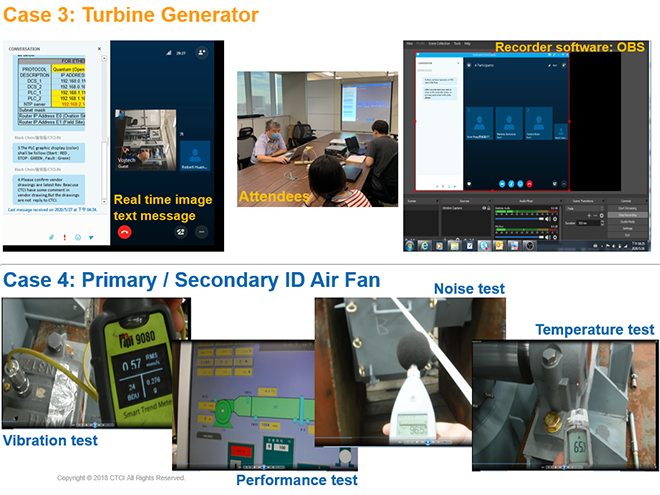
Despite its convenience, remote inspection does have room for improvement. Inspection cameras are currently handheld, which makes it a hassle for inspectors to hold the camera and inspect things with hands simultaneously. In the future, cameras will be improved to become fixed lens offering inspector’s point-of-view perspective, so as to increase convenience and safety during inspection.
Conclusion
There is no doubt that digital technologies can greatly enhance convenience and efficiency of procurement for EPC companies, as witnessed from CTCI’s practical examples. However, digital transformation is a long journey, requiring considerable amount of investment initially to build strong foundation. Automation and intelligence rely on massive amount of accurate data; therefore, it is critical in the first place to have good planning, optimal operational process, and the right tools to create, collect, and determine the relationship of such data, so that processes can be automated and operations become smarter.