Discover Reliable
發現信賴
CTCI Builds a New Smart Green Energy Landmark for Shilin Technology Park: CTCI Second Headquarters EPC Project
— Peter Lee, Project Manager, CTCI Resources Engineering Inc., CTCI Group Intelligent Solutions Business
- Market:Building and structural engineering
- Owner:CTCI
- Executive team:CTCI Resources Engineering Inc. (CTCI REI)
- Completion time:2021
- Project location:Shilin Technology Park, Beitou District, Taipei City
- Project Scope:Engineering, procurement, and construction (EPC)
With the continuous expansion of CTCI's global businesses, the group has selected Beitou Shilin Technology Park to be the base for its second headquarters in order to leverage its synergy and accelerate business development in various fields. This was the first project in the park to pass urban deliberation, obtain a construction license and use said license, as well as the first corporate headquarters to move into the park. In order to implement the concept of a smart city and promote the sustainable development of the city, the Taipei City Government plans the overall direction of the city's development, developing the Beitou Shilin Technology Park to complement the existing Neihu Technology Park and Nankang Software Park. As for its industry positioning, Beitou Shilin Technology Park is committed to providing a space for industry development and operating strategies, and an innovation-driven base for emerging technologies. "Smart health" and "digital technology services" were introduced as the main industries for the park to focus on, becoming a base for developing emerging technologies and innovations for the future. In terms of this project's structure, it is a commercial office building consisting of 12 floors of steel construction (SC) above ground, 2 floors of reinforced concrete (RC) underground, low-radiation glass (D-low E), with an outer curtain wall made of granite. The building stands at 49.95m with a base area of 5,180m², and a total floor area of 27,400m². Planning and design began in December 2017. Construction license was obtained in February 2019, followed by construction beginning in June. The project was completed at the end of July 2021. In August 2021, the Second Headquarters was officially unveiled, with staff moved in. In all, the building took 3 years and 8 months to complete, and is entirely built by the CTCI team.
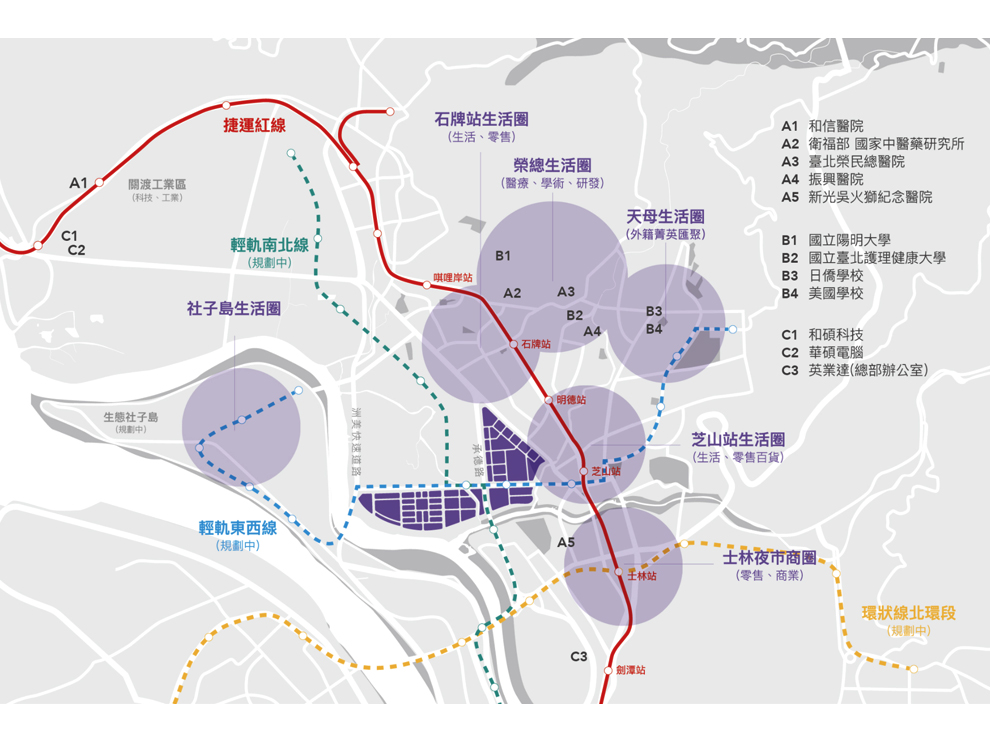
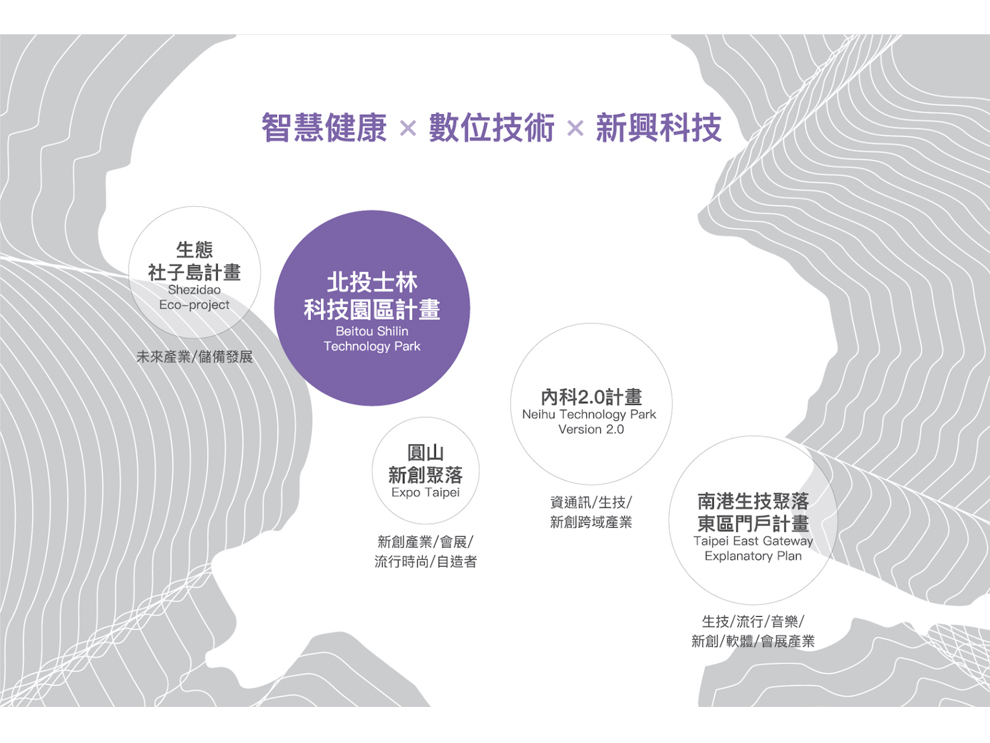
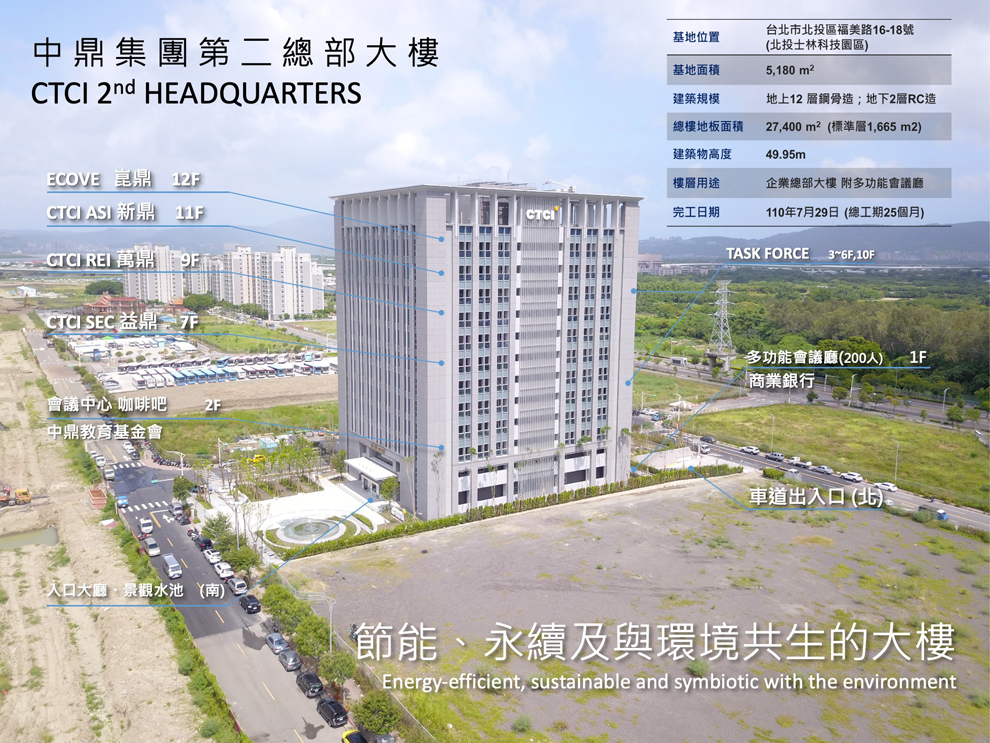
Why CTCI?
Turnkey Project Leader in Taiwan, Smart Technology Provider
CTCI's Group Intelligent Solutions Business includes three subsidiaries: CTCI Resources Engineering Inc. (CTCI REI), CTCI Advanced Systems Inc. (CTCI ASI), and CTCI Smart Engineering Corporation (CTCI SEC), which are professional construction, intelligent solutions and electromechanical systems contractors. CTCI REI is the only professional civil engineering consulting company in Taiwan that is both an engineering consulting firm and a Class A construction company. It has accumulated a wealth of experience and technology in the field of civil and traffic infrastructure engineering, as a domestic leader in public engineering turnkey solutions. CTCI ASI is a global leader when it comes to the integration of industrial automation, smart manufacturing, and electromechanical control systems. It is committed to providing global customers with reliable, intelligent, and environmentally sustainable integrated services. CTCI SEC is a leading provider of electromechanical equipment and solutions in Taiwan. Its scope of business includes the construction of high-tech plants, high-rise buildings, and public infrastructure, providing owners with intelligent engineering solutions. Moreover, it specializes in the construction, enhancement and decommissioning of nuclear power plants, and has acquired an excellent reputation in the energy market at home and abroad with its high-quality services.
Reliable Realized
Achieving the Highest Quality in the Shortest Construction Time
CTCI is Taiwan's No. 1 engineering, procurement, and construction (EPC) contractor and ranks among the world's top 100. It has extensive plant construction and turnkey engineering projects around the world. As per the project plan, the group's Engineering and Intelligent Solutions divisions cooperated synergistically and successfully constructed a commercial office of the highest-quality in the shortest amount of time. The successful execution of the project not only benefitted the team in terms of experience and technology sharing but more importantly, demonstrates the strong engineering capability of the group. During the project's construction period, major environmental factors such as the rising of domestic prices for construction material, a lack of workers, the COVID-19 pandemic, as well as other factors directly affected the cost and schedule of the project. However, the CTCI Supervisory and Construction team displayed the professionalism, integrity, and persistence of CTCI employees, using accurate budget scheduling and a contracting strategy to reduce the impact of the rising costs of construction materials. As for the construction progress, multiple aspects of construction were carried out simultaneously, with the construction process being overseen by professional, meticulous, and efficient construction procedures that allocated company personnel, machinery, and materials to overcome the challenge of shortage of workers. In terms of pandemic prevention and control, a number of measures were formulated to manage it on-site, with risk control being implemented as well. Due to the efforts of the CTCI team, the project was finally completed at the desired quality and within the 25-month schedule in spite of construction and relocation difficulties. This is a testament to the company's spirit of defying hardships and accomplishing missions as it continues to work towards its vision of becoming "The Most Reliable Global Engineering Services Provider".
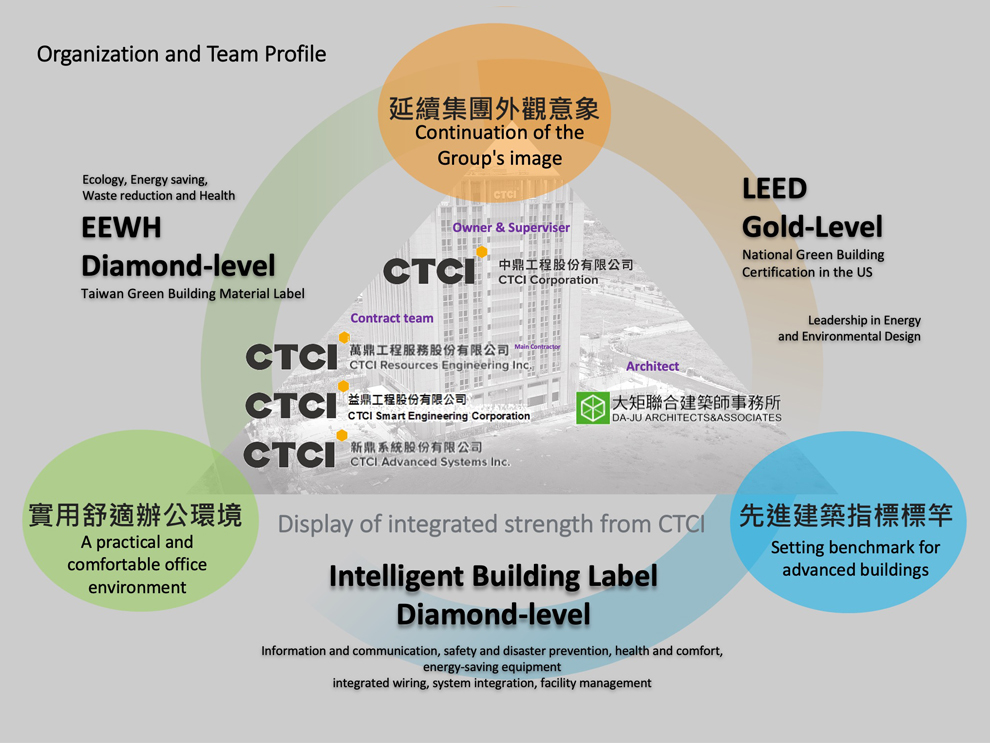
Project Highlight
Three Certifications for Intelligent Solutions and Green Energy
The project introduces green building design and smart applications, aiming for creating an energy-saving, sustainable and eco-friendly building. The overall appearance of the building is designed in the style of the group's first headquarters, with vertical and symmetrical dividing axis lines for a simple and stable design, which is in line with the group's steady and understated corporate image. In terms of landscape design, the use of many native arboreal trees and low-light-damage lighting resulted in an overall green coverage of 89.7%, with 1,600 tons carbon capture capability, far exceeding the minimum legal requirements. As for its interior design, green building materials, high-grade water-saving sanitary appliances and energy-saving lighting fixtures were mostly used, together with the energy-saving D-Low E outer shell glass, resulting in the building's overall cost-saving rate of 19.6% (according to the calculation basis for obtaining LEED certification from the U.S). The project has been listed as a Taiwan Green Building EEWH Mark Diamond Candidate as well as the Smart Building ITB Mark Diamond Candidate (official mark application underway) because of the above-mentioned smart and green energy design. Additionally, the US LEED Green Building Mark is currently undergoing gold level certification.
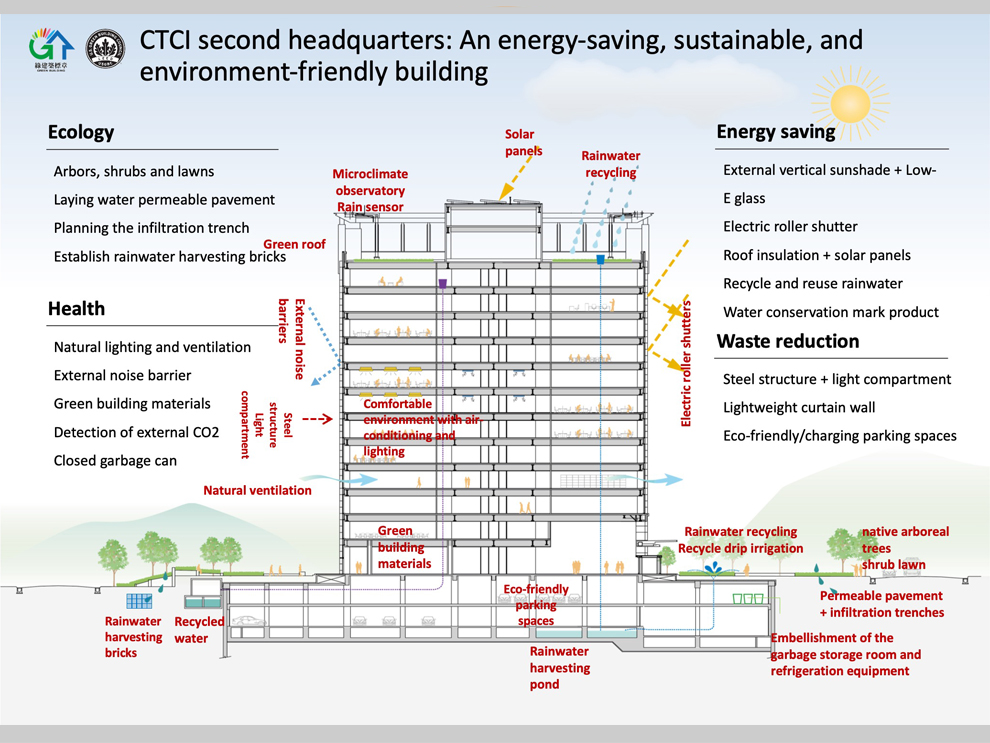
Multiple smart and green energy designs for CTCI's second headquarters.
When it comes to the building's structural system, a total of 96 buckling-restrained braces certified by the National Center for Research on Earthquake Engineering were used for the entire building, providing high-efficiency support of the beams in case of buckling, allowing them to display a good level of resilience and dissipate energy when an earthquake occurs. For the underground foundation, wall-type foundation piles were set underground with an average depth of 60m. They were used in order to overcome the uplift damage from the weak clay layer and transmit the weight of the upper building to the solid load-bearing foundation layer. This was paired with the pile bottom grouting method and verification using test piles proved that it was effective.
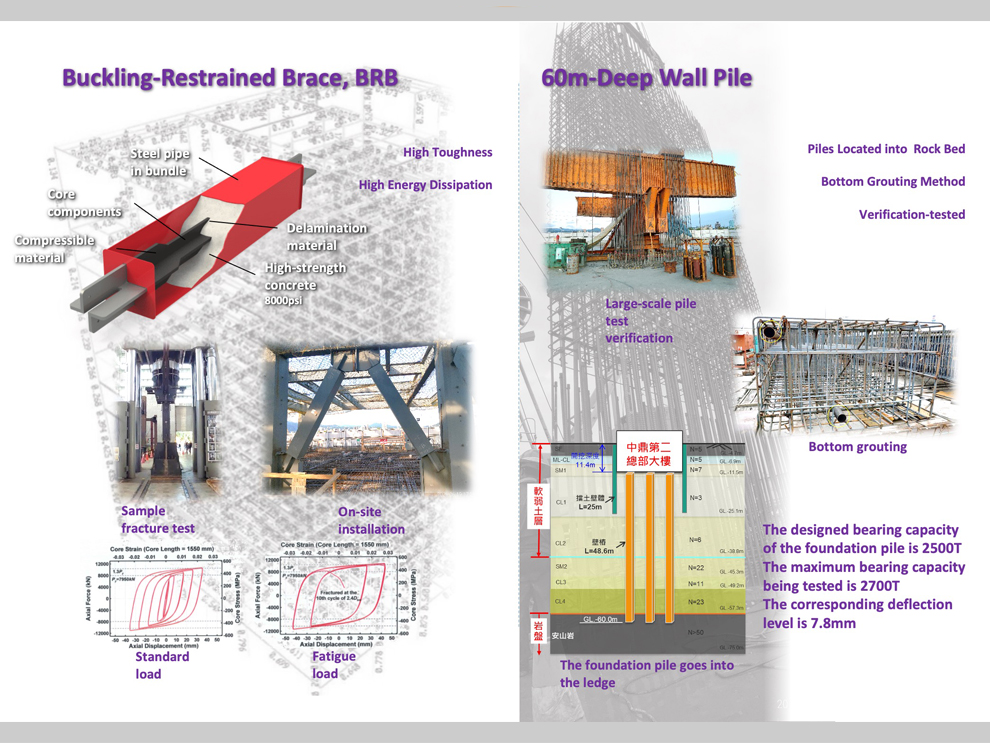
CTCI's second headquarters has a high-efficiency, state-certified seismic system.
Generally, when it comes to smart buildings, the more points of control a building's central monitoring system has, the greater the degree of intelligence. For this project, the number of central monitoring system control points was 17,525, which is equivalent to a 50-story smart building. These points include air-conditioning, lighting, monitoring, water supply, shutters, meeting rooms, parking management systems, among others, which are integrated into the central monitoring system and perform various smart applications. In addition, the CTCI team is committed to sustainability, which is the core of the engineering industry. The total recycling rate of construction waste generated during the project's construction was 79.1%. In terms of industrial safety, it accumulated more than 600,000 safe working hours and successfully achieved the highest possible standard of having a "zero incident rate in the workplace".
Smarter Engineering
Maximizing Management Synergy through the Introduction of Smart Solutions
In order to build a smart building that communicates with people, the environment and facilities, the project started off by focusing on the infrastructure, which involved setting up various environmental detection sensors, collecting data through the central monitoring system, and using the smart platform server for the application of intelligent solutions. An example of smart solutions: Mr. Energy, the smart air conditioner and intelligent energy management system developed by CTCI ASI, is able to collect information on the flow of people and air conditioner usage in the office, and work with the temperature and humidity sensor of the micro-weather station on the roof to perform big data calculations and import that data for machine learning. By adjusting the amount of wind, temperature, and ventilation, it not just provides a comfortable working environment, but also helps save energy on air-conditioning. The BIM 7D maintenance management system developed by CTCI SEC uses visualization, uses 3D and complete information from MEP to integrate functions such as early warnings, maintenance, repair into a single platform that provides quick and easy operation. In order to allow for smart building maintenance and operation management, the CTCI team further customized the smart building maintenance and operation facility management system and integrated the group’s internal assets, performance, organization, maintenance, and long-term management information into it. This was combined with the central monitoring, smart energy management, and smart maintenance systems to establish a management platform on the network, which resulted in maximum management efficiency.
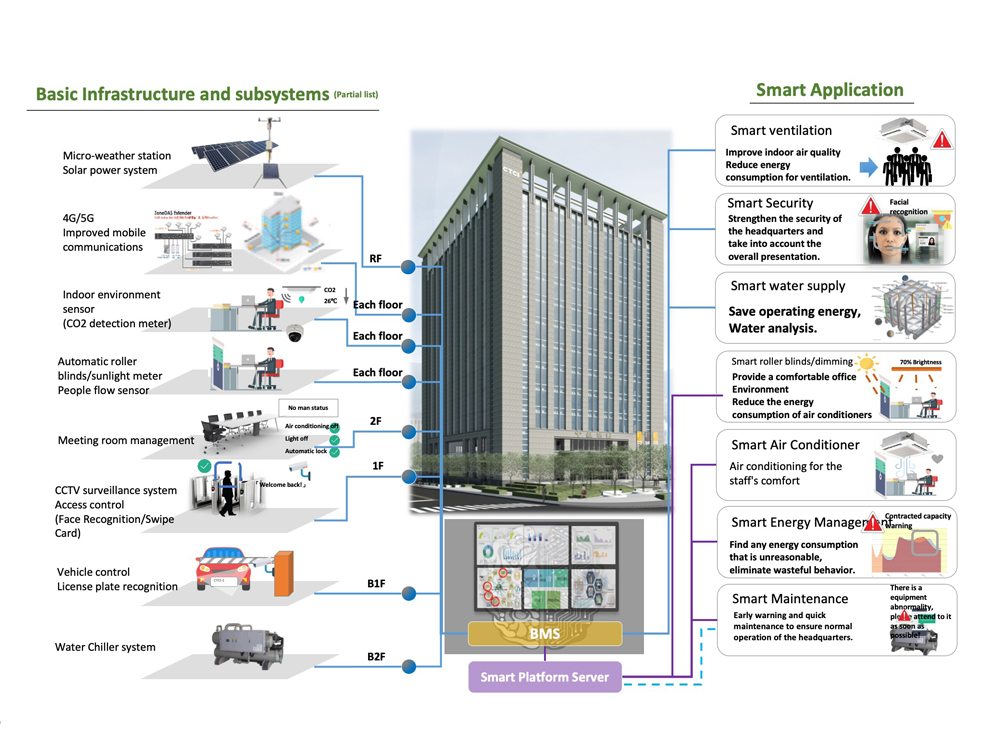
In terms of construction methods, the project adopted a number of innovative construction methods to solve the challenges of having a tight construction schedule and a small worksite. For the electromechanics portion of the project, a pipeline first and modular construction approach was adopted. When large pipelines such as the main pipe of the air-conditioning cooling unit were assembled within the steel structure, it was first bound and hoisted together with the steel components to avoid traditional pipeline installation, which would affect the engineering progress of the main structure and interior decoration. The modular construction method involved first modularizing the pipelines and then testing them on site. After test verification was completed, the subsequent pipelines would be worked on in accordance with the modularization and would be brought into the site. This was to reduce using cutting tools to perform on-site work, which would unnecessarily take up work space. As for the main project, the eastern part of the project site is close to land occupied for other use, and as such, vehicles that were needed to construct the curtain wall would not have enough space to hoist it. The project instead utilized circular rail cranes to hoist it from the assembly area with an aerial relay method.
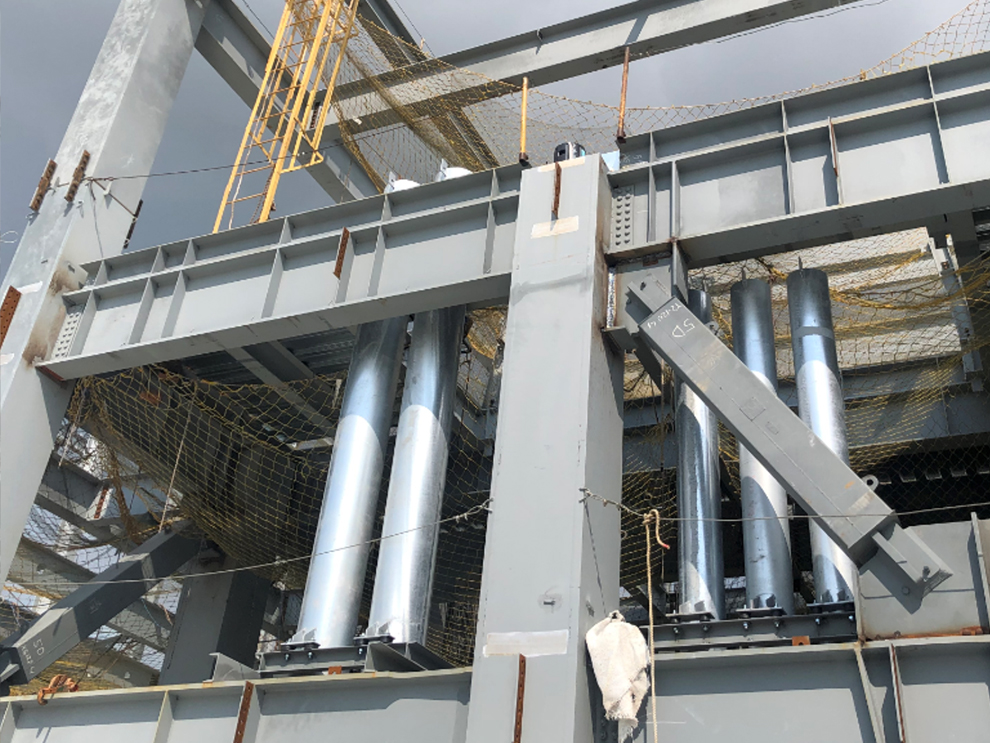
During the project, an innovative construction method was used to install both the large pipelines and the main structure, solving the issue of the tight construction schedule.
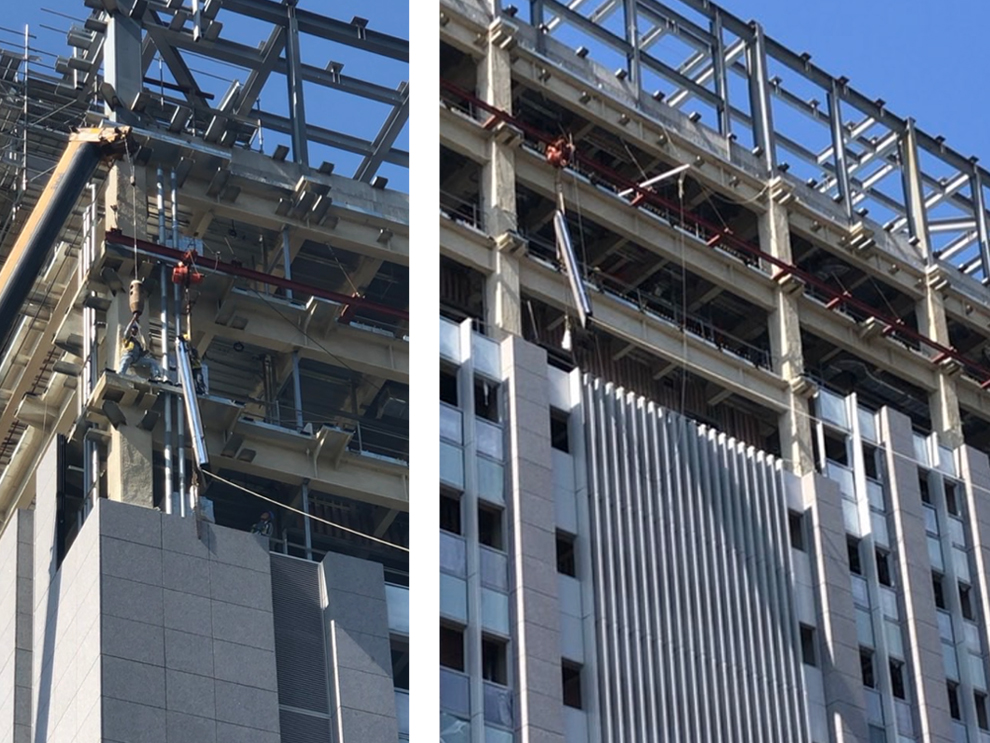
During the project, a circular rail crane was used to carry out aerial relay to overcome the challenge of the small site area.
On the 40th anniversary of CTCI's establishment, we set out to build our second group headquarters, which was completed and launched in 2021. The building, which was built by CTCI's professional team, cost TWD3.85 billion. Such building with green energy and smart applications will greatly improve the group's image and brand. I hope that the high-quality and comfortable office environment will lead the colleagues to become more united, thereby increasing their sense of shared identity, and their motivation to create new achievements. --John T. Yu, CTCI Group Chairman