Discover Reliable
發現信賴
CTCI Assisted CPC to Increase Production Capacity -- Talin Refinery #3 RDS (Residue Desulfurizer) Unit Revamping Work
— Wei-Hsiang Hung, Project Engineer at CTCI Corporation, Group Engineering Business
- Market:Refining and Petrochemical
- Owner:Construction Office, CPC Corporation, Taiwan
- Executive team:CTCI Corporation
- Completion time:2017
- Project location:Siaogang District, Kaohsiung City
- Project Scope:EPC turnkey project (production capacity enhancement / debottlenecking project)
- Production capacity:Refinery capacity for heavy oil from 30,000 barrels per day (BPD) to 40,000 BPD; production capacity for sulfur from 200 metric tons per day (MTPD) to 250 MTPD
To meet with increasing refinery capacities for crude oil from improved refinery process and demand to supply domestic gasoline and diesel/propylene, the project owner, CPC Corporation, invested in the revamping of #3 Residue Desulfurizer (RDS) Unit to augment the production of low sulfur fuel oil for the supply of residue fluidized catalytic cracking (RFCC) unit. Also, coincided with the closure of CPC’s Kaohsiung refinery and hence the fact that the overall refining capacity of residue oil cracking unit was insufficient, CPC also aims to increase capacity of #8 Sulfur Recovery Unit (SRU) to deal with the newly produced polluted acid gas due to increased production of low sulfur fuel oil. Specifically, production capacity of #3 RDS Unit has been increased from 30,000 barrels per day (BPD) (199 m3/hr) to 40,000 BPD (265 m3/hr), a 133% growth in refinery capacity. Moreover, #8 SRU has expanded its original production capacity from 200 metric tons per day (MTPD) to 250 MTPD, signifying an 125% increase in acid gas processing capacity. In this revamping project, CTCI is responsible for the EPC of the major unit. As a debottlenecking project, CTCI team had to cope with limitations at the operating site for making production capacity enhancement plan and construction schedule alignment; at the construction stage they also needed to overcome the various interfaces of pre-existing buildings, equipment, pipelines, and ensure the safety of other adjacent units in operation. Other challenges faced CTCI team include having to comply with CPC’s annual overhaul and the limits of construction schedule within the period of debottlenecking. Furthermore, interface problems and emergencies at site also demanded to be eliminated and handled promptly to complete the project on schedule and with quality. In the end, under the excellent project management of CTCI team, the project successfully reached the target of mechanical completion two days ahead of the date specified in the contract.
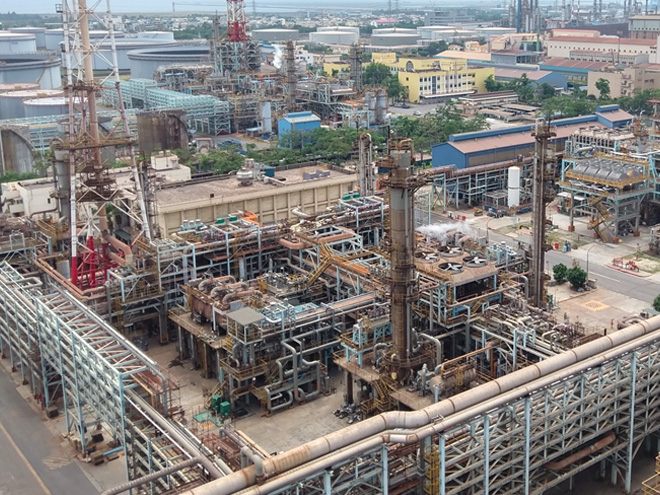
Why CTCI?
Rich Performance and Expertise in Refining and Petrochemical Engineering
CTCI wins this contract as the most advantageous bidder for having plentiful experience and track records in the global oil refining and petrochemical field. Apart from having engaged in several major domestic turnkey refineries projects of CPC, including Talin RFCC Project, Talin Alkylation Project, Talin #10 SRU Project, and No.6 Naphtha Cracker Project. CTCI also has accumulated experience for executing related large-scale refining and petrochemical projects overseas. With technological expertise, excellent project management capabilities, and fully-integrated supply chain, CTCI has won CPC’s trust to commission this project.
Reliable Realized
Thorough Planning and Highest Safety Standards for Zero Accident
In the planning and design stage of the project, CTCI team conducted extensively surveys for the existing sites and construction feasibility studies. Besides checking whether the entire space and the operation and maintenance configuration would interfere with each other, CTCI specifically expanded the inspection scope to confirm whether the addition and modification work of the debottlenecking project is compatible with pre-existing facilities and whether the traffic flow is smooth. For this project, four phases (25%, 50%, 75%, 95%) 3D model review and three phases (30%, 60%, 90%) design check were specially arranged to ensure the smooth bridging of new facilities and existing processes. CTCI is committed to providing the most reliable quality of engineering service. Besides ensuring high-quality preliminary planning and design for the smooth execution of subsequent construction, "safety first" is also our top priority during the project execution stage. For this project, we successfully reached the highest safety standard of "zero lost-time injuries" during the whole project implementation, ensuring the safety and health of all colleagues and business partners. For this very reason, CTCI was awarded the Certificate of Excellence in Industrial Safety by CPC, after the completion of the project.
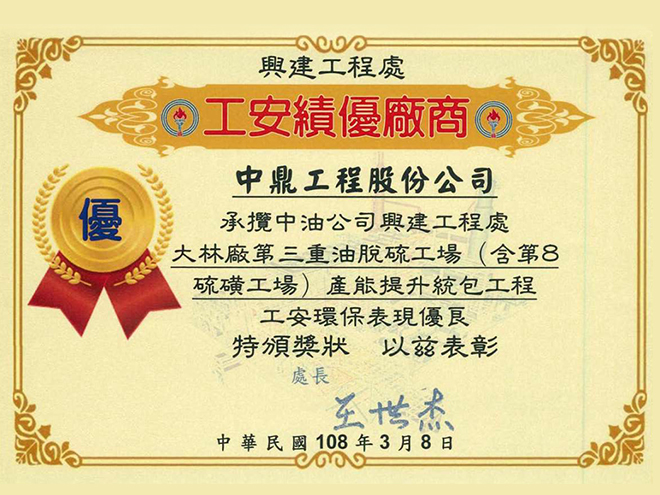
CTCI was awarded the Certificate of Excellence in Industrial Safety by owner, CPC, after completion of the project.
Project Highlight
Application of 3D Scanner to Reduce Interference and Shorten Construction Schedule
The pre-existing plant for the project has been in operation for 24 years. In the absence of a 3D Model in the first place, CTCI team used 3D scanner to record pre-existing pipelines and equipment, and then transferred the scanned data into a new 3D Model. The successful application of this technology greatly reduces the clashes of pipelines on-site under construction, and shortened subsequent modification time. The excellent implementation results have also been highly recognized by CPC.
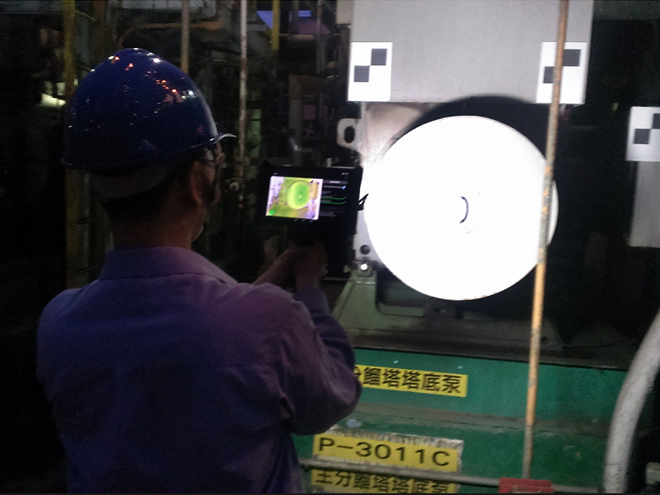
3D scanner is used for scanning pre-existing pipelines and equipment.
Smarter Engineering
4D Simulation for Transportation of Main Equipment (Reactor)
The largest heavy equipment in this unit is “Up Flow Reactor,” a patented process equipment from Chevron Lummus Global (CLG), which utilizes ASME Code Section VIII Division 2 as design basis. Up Flow Reactor is an essential equipment for the RDS unit in this project which uses catalysis reaction and hydrogen to reduce metal impurities from the feed oil. Weighing 1,034 tons, and with a diameter of 5.8 meters and a length of 31.3 meters, the heavy equipment needs to be transported by a heavy duty low-platform truck (self-propelled pallet truck) after being transported by sea freight (barge) from Port of Kobe, Japan to CPC’s Pier 105, Talin Refinery Plant. In order to ensure the smooth transportation and hoisting operations, CTCI conducted a feasibility study for construction (Constructability) with the installation personnel in the design stage, and carried out on-site hoisting operation calculations using 4D simulation technology. Finally, this heavy equipment was seamlessly integrated with on-site construction interface upon arrival.
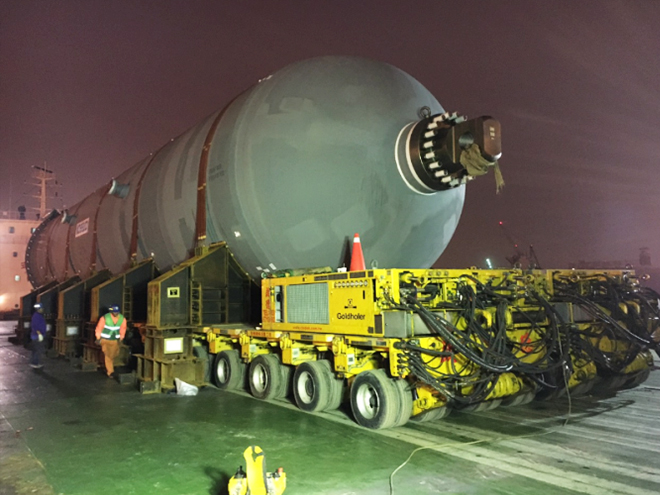
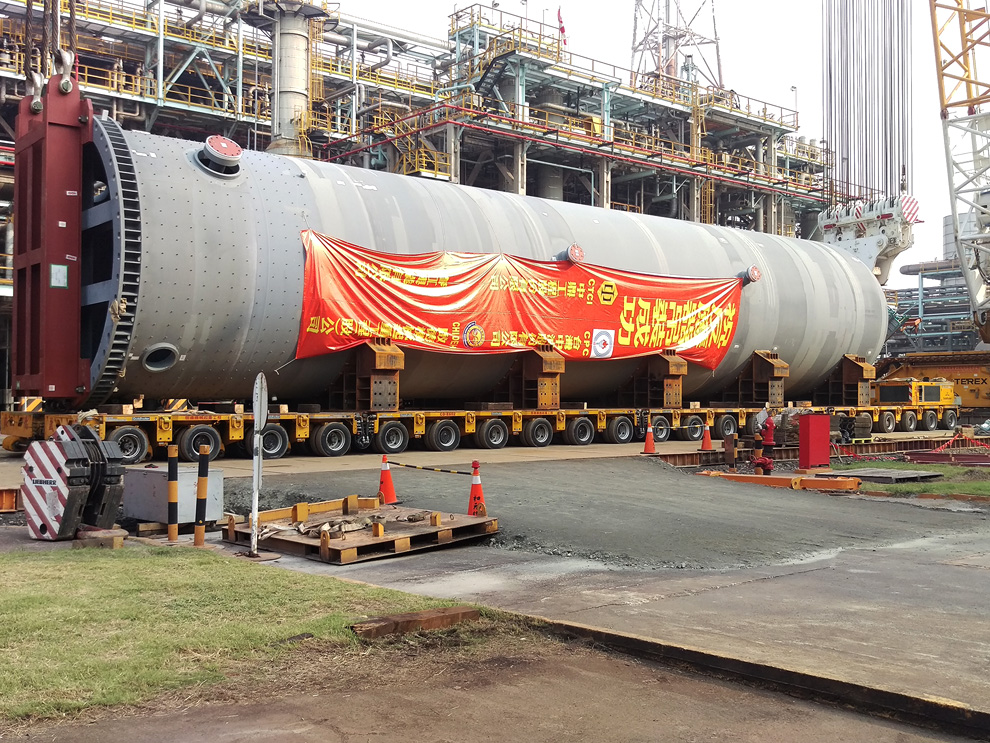
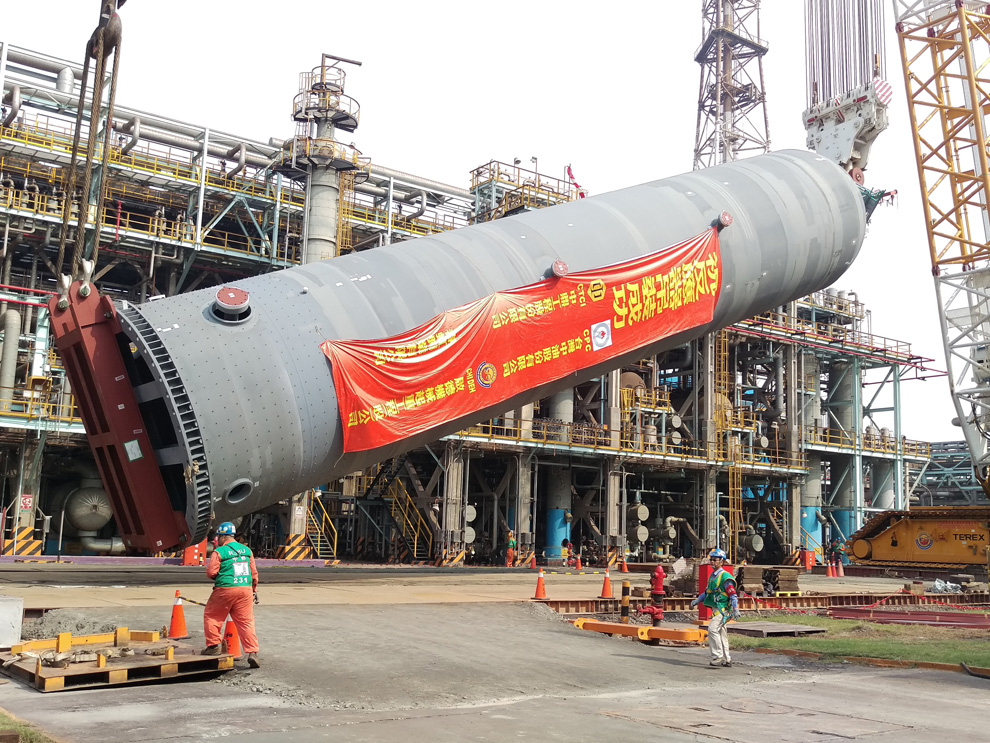
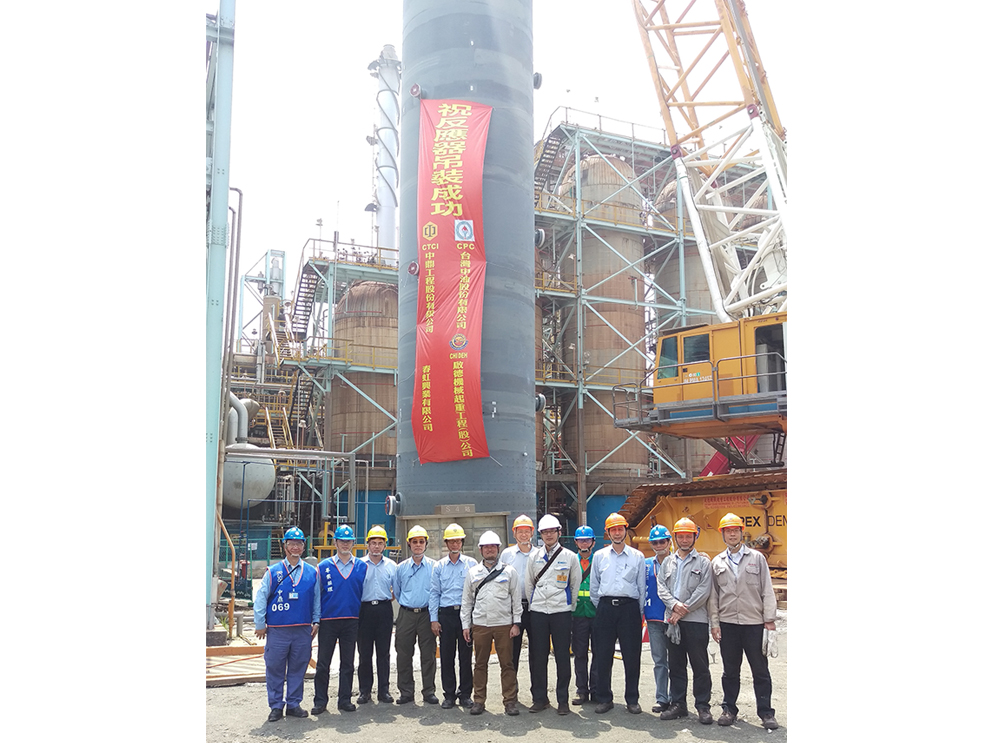
Talin Refinery #3 RDS unit revamping work is a debottlenecking project; unlike general constructions, CTCI not only needs to consider the pre-existing plant configuration in the design stage, but it also has to align with the construction schedule and traffic flow during annual overhaul of the plant. Last but not least, it has to overcome space conflict issues of pre-existing buildings, equipment, pipelines, etc. at site when construction is underway while maintaining the safety of adjacent areas. Hence, it is more complex and more dangerous than other construction projects. CTCI project team demonstrates superior teamwork and work ethic during the whole project. The team fully communicated and discussed with us regarding project details since the design stage and when encountering issues in the construction stage, it always propose an ideal improvement plan immediately so that they can achieve the completion target on schedule and with quality. I would like to thank all CTCI partners for their dedication. In conclusion, it is great to have CTCI! --Chih-Chiang Ke, Project Manager, Construction Engineering Division, CPC Corporation, Taiwan