Sustainable Future
永續未來
Intelligent Applications of Digital Plants
─Vincent Chang, Intelligent Service Department Manager, CTCI Advanced Systems Inc.
CTCI Advanced Systems Inc. (CTCI ASI), a subsidiary of CTCI, is committed to the development and introduction of intelligent technology and plant assets solutions. By using data technology, we assist plants reduce energy consumption and optimize their productions. We are dedicated to align our business to the United Nations Sustainable Development Goals (SDGs), including "industry, innovation and infrastructure," "sustainable cities and communities," "responsible consumption and production," and "climate action" to promote global sustainability through our engineering expertise. Over the past decade, CTCI ASI has been actively developing process simulation technology and intelligent digital plant implementation services to solve problems customers face during the process of chemical engineering. As information and data application and visualization have become the foundation of plant transformation, the case for developing digital plants is stronger than ever. By applying Intergraph Corporation (Intergraph®)'s SmartPlant® Enterprise for Owner Operators (SPO) to management of design-to-operate phases, CTCI ASI can effectively and systematically build up and apply plant data for visualization of all equipment, instruments, design data and plant reality. Thanks to digital plant, we can assist our customers to manage their plants safely and with high quality. We can also ensure that construction is carried out according to design, reduce the cost of human resources and other costs, and help customers connect to intelligent applications. This article will discuss the issues and systems related to digital plant.
The Need for Digital Plants
A digital plant can effectively help owners solve the cost and aging employee issues associated with physical operating assets and data-based virtual assets. Issues include:
1.Heavy consumption of human resources
In an operating plant, it often takes a lot of time and manpower to look for and compare engineering information because such information is scattered in different storage locations. Therefore, manpower and time reduction become prevalent issues.
2.Diagrams and documents do not match current reality
The documents that contractors hand over to the owners at the time of plant completion may possibly become out-of-date right away because from the owner’s perspective, process optimization and P&ID (Pipeline and Instrumentation Diagram) modification are constantly being carried out since the day of completion and when the plant starts operating. In particular, the technical documents of older factories may have been lost long ago. Another problem is that the paper-based P&IDs or AutoCAD drawings in the past are not in a structured management format, which cannot be used to express the internal data and attributes. It is also impossible to ensure that the P&IDs are fully compatible with the site conditions or whether the detailed parameters correspond to other departments. This discrepancy between diagrams/documents and reality is one of the biggest problems for the owner.
3.Reducing project timelines
Owners always want to complete plant maintenance as quickly as possible to reduce production loss. Therefore, maintenance staff are often given a limited amount of time to do repairs, and even need to do repairs for only part of the plant when the rest of the production line keeps running. It is therefore very important whether or not the owner can provide accurate documents for plant maintenance on time to reduce industrial safety risks and shorten the modification time.
4.Complying with government regulations
On January 1, 2020, the Ministry of Labor rolled out a set of implementation rules on periodic process safety assessment based on U.S.’s PSM, which requires plant owners to conduct process safety assessment every five years. The assessment scope includes safety information and process hazard control measures. Reducing work safety risks requires solid employee trainings. However, there are certain areas within a plant that, when in operation, do not allow staff access. So it is not easy to carry out such trainings. Another issue is the systematic preservation of the documents and assessment results related to process safety assessments, which must also be taken into account.
5.Aging employees and loss of talents
Preserving the operating know-hows of a plant becomes an issue when senior and experienced employees gradually retire and talent gap emerges. How can a plant help new employees get the most of the operating know-hows as quickly as possible? The need for knowledge transfer between various generations of employees remains a challenge to plant owners.
An Optimal Digital Plant Focused on Management
Before a plant can be handed over for production and operation, it needs to go through an engineering process that includes conceptual design, detailed design, and mechanical setup. 10% of the plant project cost is spent on creating engineering asset information. This is the point where CTCI ASI can help owners set up digital plants to allow them review and control more efficiently all engineering assets handed over by the plant contractor. This ensures the quality of information delivered. Once a plant finishes construction, there are various extended applications that can be done on SPO platform through panoramic pictures taken with laser scanning technologies. Below are some application examples of digital plant solutions:
1.Visualized searches
SPO is a visualized system platform that offers a different way of searching for instrumentation and equipment documents. It allows users to intuitively click on the instrumentation and equipment symbols on the diagram while reading P&IDs, and the system will show the attributes and archive files associated with the instrumentation and equipment. Moreover, if there are 3D models or laser scan files in the archive, the system can directly point out the position of the instrumentation or equipment.
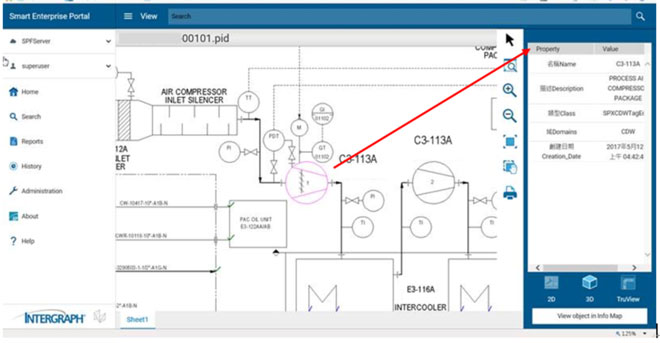
Visualized data searches for P&IDs
Users can use the 2D and 3D interactive search modes on the same screen to browse information such as equipment attributes, technical documents, and plant panorama. Since panoramic pictures support point cloud technology feature, users can directly measure instrumentation and equipment without needing to be physically present on field sites. This reduces potential safety hazards when staff carry out such operations on-site.。

2D and 3D interactive browsing
2.Extended applications of real plant models
Not only can laser-scanned panoramic pictures be used for intuitive data searching, they can also become training, repair, and maintenance materials for owners. Training records can even be integrated with a learning system as one of the implementation materials of PSM training. With digital plant solutions, CTCI ASI not only brings field environment into the office, but also realizes a training mode that integrates the virtual and the real. Intergraph® 3D pact allows full simulation of various training scenarios, under which owners may carry out operation and work safety trainings in a real plant model environment.

Screenshot of 3D virtual reality training
Under training mode, the system will give test takers hints on current scenario and required operations before evaluating the accuracy of the test taker's operations. Finally, the system will calculate and provide total score of the test taker so that the management team can evaluate training effectiveness.
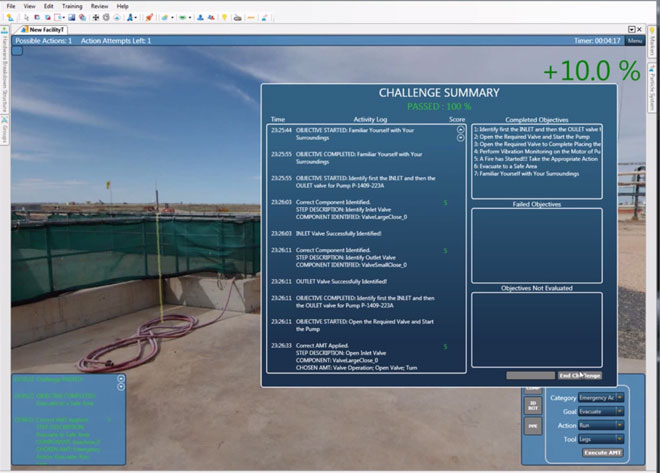
Screenshot of 3D virtual reality training score
As soon as training scripts for each plant are defined, simply drag and click to define characters, actions and environment scenarios. This is the excellent part about the system: it can be used in the most simple and intuitive way, without any need to write underlying codes, greatly reducing usage difficulty.
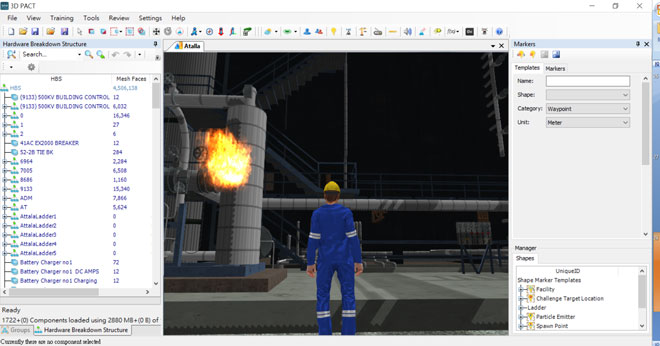
Equipment ignition scenario setting
3.Mobile solutions
In the past, whenever on-site operators or maintenance staff need to refer to the equipment and instrumentation documents, they needed to bring paper copies to sites. This is not very mobile and efficient. Input errors would also happen when transcribing data into the system. SPO's mobile solution provides a more convenient option for owners to access information and documents offline by simply using the office computer system, selecting the information and documents for reference, and then downloading them from the system to the app on the tablet, which can be used as an offline briefcase to browse 3D scans, diagrams and information on site. To record information, users can input it directly into the app or attach multimedia data such as photos or audio recordings, and then upload the recorded data to SPO after returning to the office, greatly enhancing efficiency.
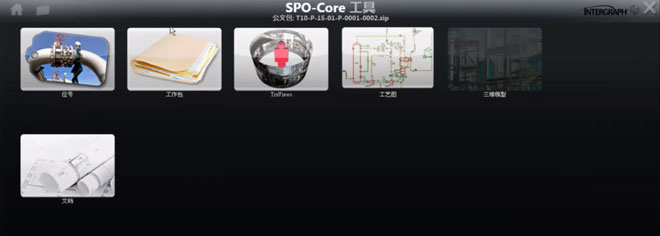
SPO tablet app

Intelligent inquiry on tablet
4.Systematic tracking of change management
With SPO's built-in workflow, CTCI ASI provides value-added management services to owners by mapping the steps associated with a production plant’s management of change (MOC) to the system and establishes a system sign-off process for the approval of diagrams and documents. The MOC system can record the items affected by the change, the department that carried out reviews, approvals, rejections, changes, and diagram updates by using simple electronic forms and rigorous workflow. Approvals are then conducted for each duty section. Ultimately, this forms a traceable and integrated change management for processes.
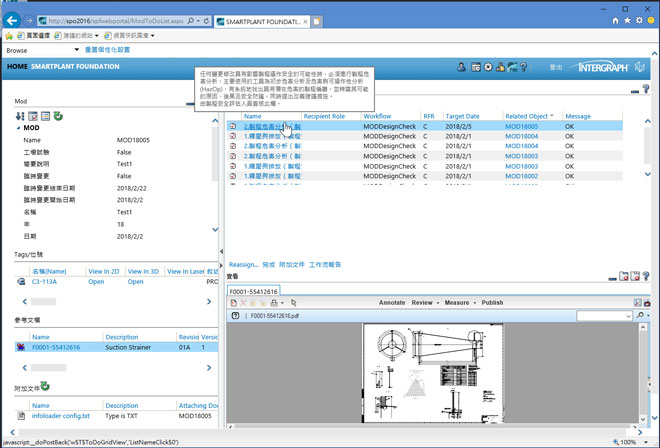
MOC approval list
In addition, thanks to SPO's powerful correlation function, users only need to select the change code they want to view, and the system will bring out the Tags and files affected by the change. Re-clicking each Tag and file will bring out relevant Tags and files, even relevant changes so that users can fully evaluate the possible direct and indirect impact from such change.
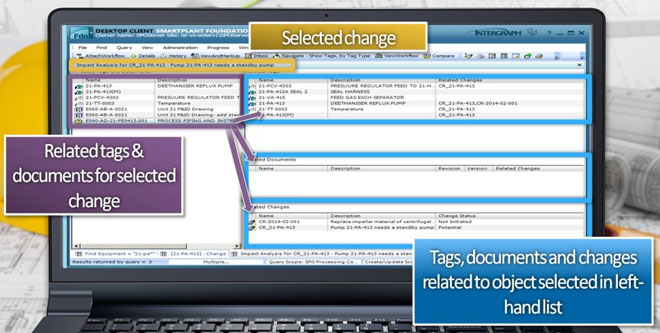
SPO change evaluation
5.System integration
In order to meet the operational and industrial safety requirements, plant owners have invested in many systems and accumulated a large amount of relevant data; however, the biggest problem among these systems is that each system operates independently and cannot connect with each other. Through its open and flexible interface, SPO can connect these systems and achieve data usage synergy. As shown in the picture below, SPO can synchronize with SAP in both directions in real time. When a Tag is added, modified, or deleted in SPO, it will immediately notify SAP's Functional Location to carry out corresponding addition, modification, or deletion.
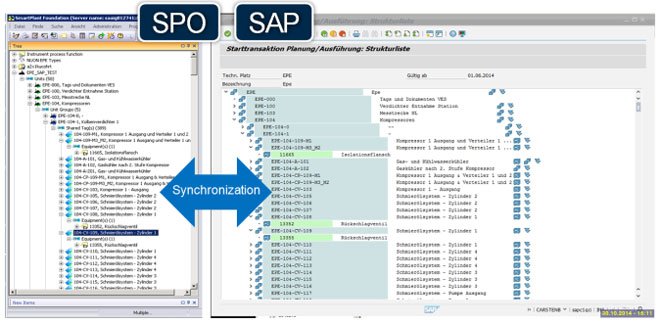
Two-way synchronization between SPO and SAP
Visual Data Integration Helps Realize Intelligent Concept
Engineering information is the basis for plant construction, equipment construction and installation. Operation information is the basis for commissioning, start-up, maintenance and normal operation after plant construction. Maintenance information is the basis for commissioning and maintenance of new equipment. Vendor information is the important basis for equipment and spare parts purchase and renewal. These information are indispensable for constructing plants and ensuring normal production. It is a big challenge to maintain such large amount of data, keep them in a safe place, and update the status of changes so that they are consistent with the current (as-built) plant status. Digital plant provides a solution built upon structured data system and visualized point cloud technology, which facilitates problem discussion, enhances data searching efficiency, and ensuring file consistency. Through built-in version control and MOC, it also ensures that documents and data are up-to-date and accurate. This not only allows digital plant to become more complete, but also allows historical data to serve its maximum value in the future.