Technology
技術分享
A New Generation of Intelligent Control Systems
— Yi-Shen Lien, Engineer at the Instrumentation & Control System Engineering Department, CTCI Corporation, Group Engineering Business
With a strong foothold in the field of automated control, CTCI Group provides customers around the world with stable and reliable system integration services while accumulating a wealth of performances in various industries, including oil refineries, petrochemical plants, and natural gas. This article will introduce the development of intelligent control systems and analyze the benefits of intelligent control systems when applied to each stage of EPCKM projects (including engineering, procurement, construction, commissioning, operation and maintenance) by drawing on CTCI’s experience in executing EPC turnkey projects around the world. The aim is to continuously propel the intelligentization of project execution, thereby opening a new chapter for the evolution of control systems and providing clients all over the world with better intelligent services.
Introduction to Control Systems
Distributed control system (DCS) is a key platform for automatic production processes. Back in the 1980s, when computer technology was growing by leaps and bounds, DCS grew into a leading product equipped with automated precision control, acute processing speeds, and a stable system architecture through its technological capabilities, and was widely adopted in various industries, including oil refining, petrochemical, electric power, and energy, thereby leading industrial control into a new era at one go. Over the past 30 years, new technologies such as “the internet” and “digital technology” continue to drive the growth of industrial control technology and transform traditional control systems in the 1980s into foundation fieldbus systems, thus ushering in an era in which traditional control systems are compatible with foundation fieldbus systems. In recent years, control systems not only possess the stability of traditional control systems and the digital characteristics of fieldbus control systems, but are also equipped with features such as “universalization” and “standardization,” thereby making control systems even smarter. A new generation of control systems built upon new technologies, including Universal Input/Output (UI/O) module, Smart Marshalling Cabinet (SMC), and Smart Junction Box (SJB), further enable control systems to take on more complex tasks through intelligent operations, including new functions such as automatic instrument configuring and launch, and automatic loop testing. At the same time, these control systems make things simple through the standardization of a variety of complex signal modules into universal ones, thereby achieving various goals, including an effective cost-reduction of total plant construction cost, shortening construction time, universalizing hardware, and standardizing spare parts.
Evolution of Intelligent Control Systems
Before the introduction of intelligent control systems, the most troublesome and impressive characteristic of control systems is its specificity of input/output (I/O) signals and complex wiring due to signal grouping. Similar to synapses in human neurons, wiring contacts transmit field instrument signals to the controller, with zero tolerance of even the slightest error in the paths. In order to ensure that the correct signals are transmitted, engineers have to make lots of effort in wiring design and carrying out wiring with respect to the connection paths. As shown in Figure 1, when planning instrument signals in traditional way, the signals are first grouped into specific signal types, such as analog signal, discrete signal, and resistance temperature detector (RTD) signal, and are sent to the corresponding junction box (JB) that is connected to the control room by multi-cables. At this moment, the signals have to be further grouped according to the I/O card. After cross wiring in the marshalling cabinet, the I/O card is connected to the designated contact before it can be used correctly by the controller. In order to implement the field instrument-connected control system architecture above, it requires considerable time and labor costs in construction, repair, and maintenance, in addition to engineering.
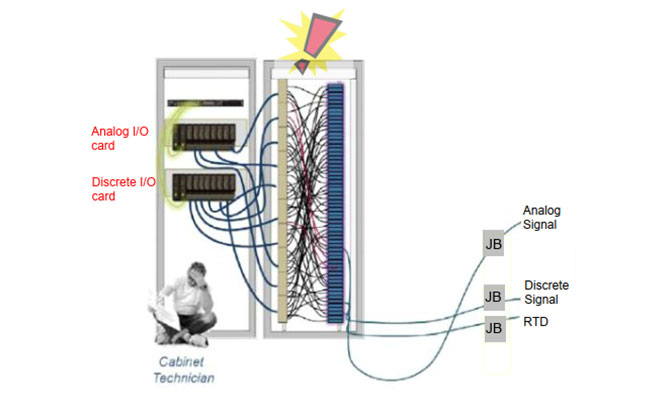
Figure 1 Traditional field instrument signal grouping.
1. Universalization - Universal I/O Module
Universal I/O (UI/O) module is the pioneer of intelligent control systems, which is developed for the purpose of incorporating universalization into I/O modules and effectively applying intelligent instrument functions with the DICED approach, which was proposed by ExxonMobil in the Control Engineering journal in 2014. The acronym DICED, which stands for detect, interrogate, configure, enable, and document, means that intelligent instrument can be automatically identified and linked by the control system after it is connected to the UI/O module, and instrument configuring may be completed to further activate instrument control functions and intelligent options (e.g., unit conversion for process data and instrument self-diagnosis and analysis), as well as generate accurate system configuring documents. Figure 2 shows the “universalization” feature of U/O module. The module allows different types of signals to be digitized, then connected to random contacts. Connecting the contacts to each controller via the control-layer network and using them across controllers can not only improve the effectiveness of field instrument configuring, but can also greatly reduce communication load between controllers, thereby enhancing communication speed in the control-layer network.
2. Standardization - Smart Marshalling Cabinet
Due to the “universalization” feature, cabinets equipped with UI/O modules have now been developed as “standardized” products. As Figure 3 demonstrates, traditional I/O module cabinets need to conform to controller assignment and be customized with I/O module assignment. Now with the introduction of UI/O modules, we no longer require customized design, assembly, and manufacturing, thanks to the universalization feature of UI/O module. The cabinet now comes in a standardized format, thereby greatly reducing the time taken to build module cabinets and the manpower required for assembling module cabinets. Intelligent control systems with both “universalization” and “standardization” features, coupled with DICED approach, can not only facilitate intelligent identification and automatic configuring tasks, but also can also benefit EPC project execution. More related details will be introduced in the latter part of this article.
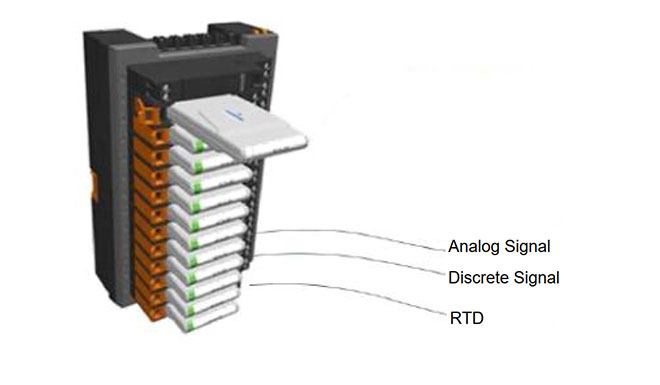
Figure 2 UI/O and the universalization feature.
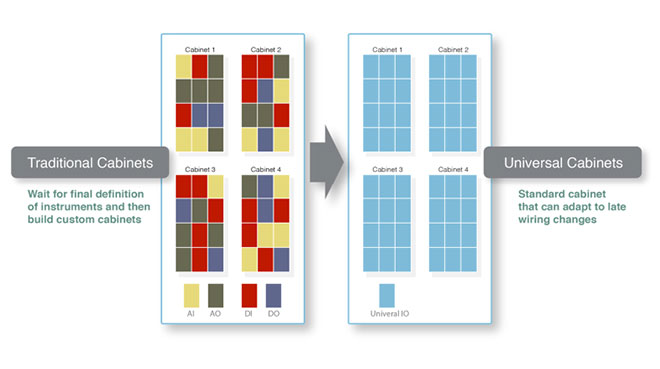
Figure 3 Standard I/O cabinets following the application of UI/O.
3. Extension of Digital Intelligence - Smart Junction Box
With an increase of user demand, digital intelligence modules are further expanded from the central control room to all corners of the field. When UI/O modules and communication modules are further integrated into a traditional field junction box (JB), it becomes a smart junction box (SJB), which is similar to the field JB shown in Figure 4. As you may find in Figure 4, various types of signal in the field are collected by SJB and converted into digital signals, then connected to the control system via Ethernet communication cables. This intelligent application, which is more flexible and standardized, converts analog signals in the instrument into digital signals in advance, streamlining not only the complicated and tedious engineering of cross wiring to be carried out by engineers (represented by the light-colored items in Figure 4), but also complicated wiring-related works, subsequent maintenance, and repair requirements at the site due to the simplification of large numbers of signal cables of traditional control systems into fiber-optic cables.
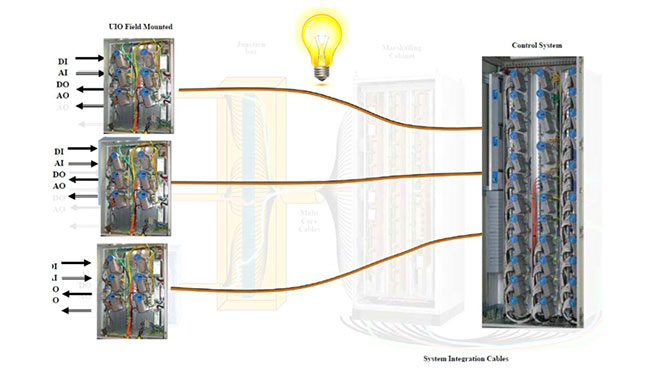
Figure 4 Architecture of SJB applied in an intelligent system.
4. Future Development
Apart from the advantages above, intelligent control systems have other development potentials, leading to an even wider application of digital intelligence. For instance, UI/O modules can support more interfaces (e.g., surge protection device), while SJB can be deployed in extreme environments (e.g., hazardous areas classified Zone 1 and above or chemically corrosive environments). Meanwhile, a single UI/O channel can drive instrument with high power consumption (e.g., gas detectors or high-power solenoid valves). Possibly, within less than 30 years, we will have a more “comprehensive” control system with wider range of applications.
Advantages and Flexibility of Intelligent Control Systems in EPCKM Projects
With a wealth of experience in undertaking all kinds of projects at home and abroad, CTCI has, in fact, gone through the evolution of control systems from those with traditional configurations to intelligent ones today, and applied intelligent control systems and products in the execution of projects all over the world. For instance, CTCI has applied intelligent products, including SMC and SJB, in recent Carbon Black Project owned by Continental Carbon Eco Technology Private Limited (CCET) and the Saudi Basic Industries Corporation’s (SABIC) ULTEM™ Plant Expansion Project, showcasing CTCI’s cutting-edge engineering capabilities. The following table is a compilation of the benefits of intelligent control systems for the execution during each stage of EPCKM projects, based on our previous experience.
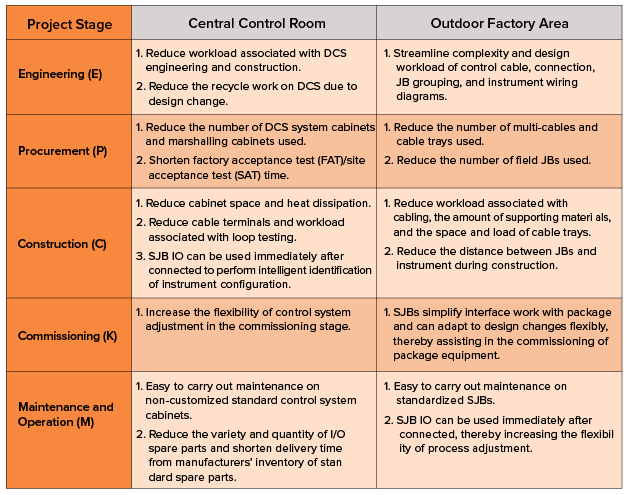
Table 1 Benefits of intelligent control systems for each stage of EPCKM projects
In addition to the projects above, CTCI has also applied SJB to modularization during the construction process in the ExxonMobil’s GCGV Mono-Ethylene Glycol Turnkey Project, which fully realizes the advantages of SJB. Loop testing is completed after SJBs are directly installed in the modular shop, which maximizes work completed in the modular shop and minimizes work on site, thereby shortening on-site construction time and reducing construction costs.
Conclusion and Outlook
With the universalization and standardization of new-generation intelligent control systems and the extension of these applications to outdoor factory areas, ever more outdoor factory areas will be adaptable to digital intelligence modules, while intelligent instrument and intelligent control systems will become more integrated. Following these development trends, intelligent control systems and related technologies may become the mainstream of manufacturing applications. Making best use of state-of-the-art technologies and constantly innovating EPC project executions is the key for CTCI to staying ahead of the competition. The development of intelligent control systems is the deciding factor for success in dynamic competition for engineering firms. Only by learning about new technologies and introducing new work methods in a timely manner can CTCI predict market trends and maintain its leading position in the industry during this rapidly changing era of technological development. Reference 1.Universal Process IO, Honeywell, 2012. 2.Electronic Marshalling Overview, Emerson, 2013. 3.Innovation of automatic control technology, Honeywell, 2020.