Discover Reliable
發現信賴
CTCI Helps Oman Qaboos Achieve High-Value Production Target in LPIC EPC 1, the 870 KTA Steam Cracker Project
— Project Engineer Jun Quan (Ben) Yao & Shao Yu (Eric) Chen | Hydrocarbon Business Operations, CTCI Corporation
- Market:Hydrocarbon
- Owner:Oman Qaboos (OQ)
- Execution:CCJV (CB&I – CTCI B.V.)
- Completion Date:Q4 of 2020
- Location:Sohar Port, Oman
- Project Scope:Engineering, procurement, construction, and commissioning
- Productivity:870 kilo tons per annum (KTA) of ethylene
The client of this project, Oman Oil Refineries and Petroleum Industries Company (ORPIC)— renamed as Oman Qaboos (OQ) in 2019— is a national petroleum company of the Sultanate of Oman in charge of the development and production of oil and gas resources of its country. Located at Sohar Industrial Port, 230 km north of the capital of Oman--Muscat, this contract is not only the largest in terms of value, but is also one of the most important part of Omani economic developing plan, namely Liwa Plastics Integrated Complex (LPIC) development project. The LPIC EPC 1-870 KTA Steam Cracker Project was secured by a joint venture established by CTCI Corporation and McDermott, called CCJV, in 2015. The project scope included steam cracking units (SCU) for the main process, Pygas unit, MTBE unit, API tank, sphere tank, bullet tank, desalination, waste water treatment, spent caustic treatment, and incinerator. The project is challenging because there are 4 EPC projects being executed simultaneously at LPIC project site, with complex interfaces between EPC 1 (contracted by CCJV) and other projects, and that the products produced by each plant are related to both upstream and downstream sectors. Despite the challenges and the impact of the COVID-19 pandemic, CTCI Corporation has held the spirit of “reliable engineering services provider,” managing to push the project forward steadily through horizontal and vertical communications. The project is expected to complete commissioning phase in Q4 2020. Once this project is completed, products and side products from OQ’s existing plants, including Sohar refinery and aromatic plant, will become feedstock for LPIC, helping to optimize product efficiency, extend petroleum production further downstream, achieve high-value production targets, and thus assist the client to ensure high profitability from Omani oil and gas resources. This project will not only help OQ become one of the companies with the most comprehensive product lines in the global hydrocarbon market, but will also set an important milestone for CTCI Corporation’s successful entry to the Omani market.
Why CTCI?
Extensive and Proven International Track Records and a Highly Competitive Team
Lummus-licensed processing selectively hydrogenation design was selected for the ethylene cracking process in the LPIC project. In fact, back in 2013, CTCI Corporation had previous experience in using Lummus-licensed processing technology to carry out engineering, procurement, construction, and commissioning (EPCC) work for a 720 KTA naphtha cracking plant in Kaohsiung, owned by CPC Corporation, Taiwan's state-owned oil company. Thanks to CTCI Corporation’s international track records and its experience in adopting Lummus-licensed processing technology, CTCI Corporation was able to form a successful strategic alliance with McDermott (formerly CB&I, which later merged with Mcdermott in 2018), the Lummus-license holder. This allowed the joint venture CCJV to eventually stand out from the intense competition.
Reliable Realized
Effective Communication and Sound Management
The LPIC EPC 1 project is a testament to the “most reliable engineering services” quality CTCI team brings from the start to the commissioning stage. Being CTCI’s first successful entry to the Omani market, it also breaks CTCI Corporation’s contract record overseas, securing US$2.8 billion for lump sum turnkey projects. The following are the key elements for the project’s success: 1.Procurement: Considering that the client sources its finances from several countries (Korea, Italy, Germany, the UK, and the Netherlands), CCJV managed to place equipment orders at these five countries based on competitive prices and qualities to meet the client’s requirement of 41% guarantee from export credit agencies. 2.Project management: As mentioned earlier, this project was carried out with three other LPIC EPC projects simultaneously on site, whose products are interrelated for upstream or downstream purposes. For instance, ethylene that comes from EPC 1, which is contracted by CCJV, serves as raw material for making polyethylene and polypropylene at EPC 2. On the other hand, natural gas liquids (NGL) produced at EPC 3 serves as upstream material for EPC1. To manage project interfaces effectively, CTCI team arranged weekly meetings to discuss engineering design, procurement, and construction issues with the client, while project director, the leader of the project, would also discuss important issues face-to-face with the client every month. Through horizontal and vertical communication and coordination with the client on every important topic and reaching a consensus on all levels, the team successfully dealt with the problems and carried out the project steadily. 3.Work safety: As of July 2020, the project exceeded 76 million man-hours without lost-time injury, an all-time high record for CTCI Corporation. All important milestones of this project from construction to commissioning phases, including flare light up, boiler light up, and ethylene imports were reached under the guidance of CTCI Corporation with strict adherence to HSE standards, thus achieving superb safety man-hour record.
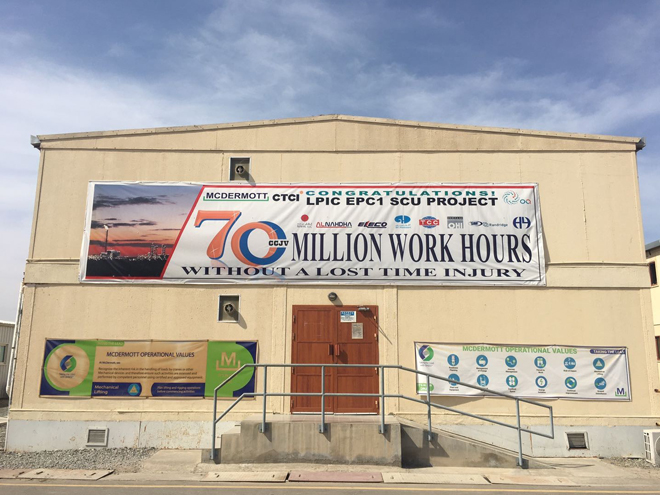
70 million man-hours without a lost time injury were achieved in the LPIC EPC 1 project.
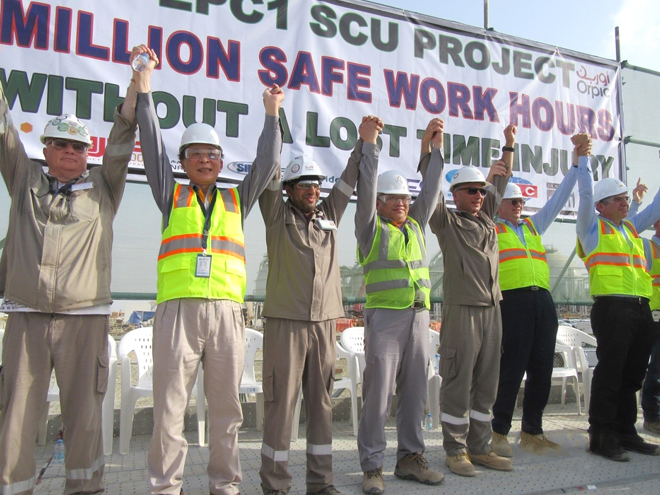
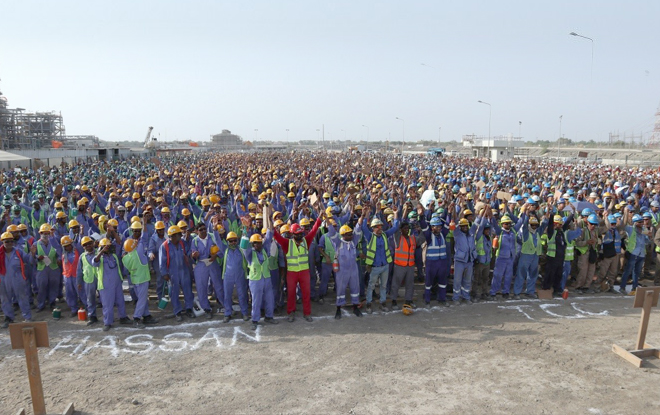
Project Highlight
Highly Efficient Construction and Convenient Maintenance
Given the giant scope of this project, traditional Construction Work Package (CWP) model is not detailed enough for construction area break down. Instead, CTCI Corporation used Installation Work Package (IWP) model to further break down Work Breakdown Structure (WBS) in the plot plan in terms of structures, pipe racks, main equipment, and package equipment. It is then able to track and monitor the latest status of piping fabrication according to the forecast schedule of piping installation in each IWP, arrange ISO drawing issuance sequence accordingly, and set up pipe spool delivery schedules with fabrication shops to meet construction requirements to avoid further delay or back charges from subcontractors by preparing sufficient work front. Besides, the application of IWP can help fabrication shops better arrange fabrication schedules and quantities, allowing subcontractors to come up with more accurate mobilization plans. During constructions, CTCI Corporation kept improving construction efficiency by paying close attention to details and planning well in advance. Take bullet tank railway as an example, in the past sand beds were prepared manually to meet 1:200 slope for bullet tank installations because there were not so many bullet tanks. In this project, however, there were four bullet tanks to be installed, so CTCI Corporation improved installation efficiency by designing railways and related devices to prepare sand beds in a fast and precise manner. Another example is the fiber cables in the E/I Interface system. To meet the IEC 61850 standard set by International Electrotechnical Association, which seeks to reduce hard-wired cable usage in Supervisory Control and Data Acquisition (SCADA), fiber cables and Power Management System (PMS) is used for cable quantity reduction and noise reduction, while allowing easier management, control, and modification in the future. In addition, CTCI Corporation took into consideration the need for maintenance in the future, and made designs that can help the client save future man hours, manpower, and costs. For instance, an increased pavement strength by design can reduce the size of damage caused by heavy lifting cranes during future equipment maintenance, so that only the pavement structure right beneath the crane needs to be fixed. Another example is the secondary cooling water main pipeline, which was originally designed as a 120” huge underground pipe during Front-End Engineering Design (FEED) phase. Considering that not only the installation of underground pipe would require large excavation, but also does during future maintenance, which is both time-consuming and expensive, CTCI Corporation changed the pipe design to above the ground after careful analysis. This saves money and time for our client in the future.
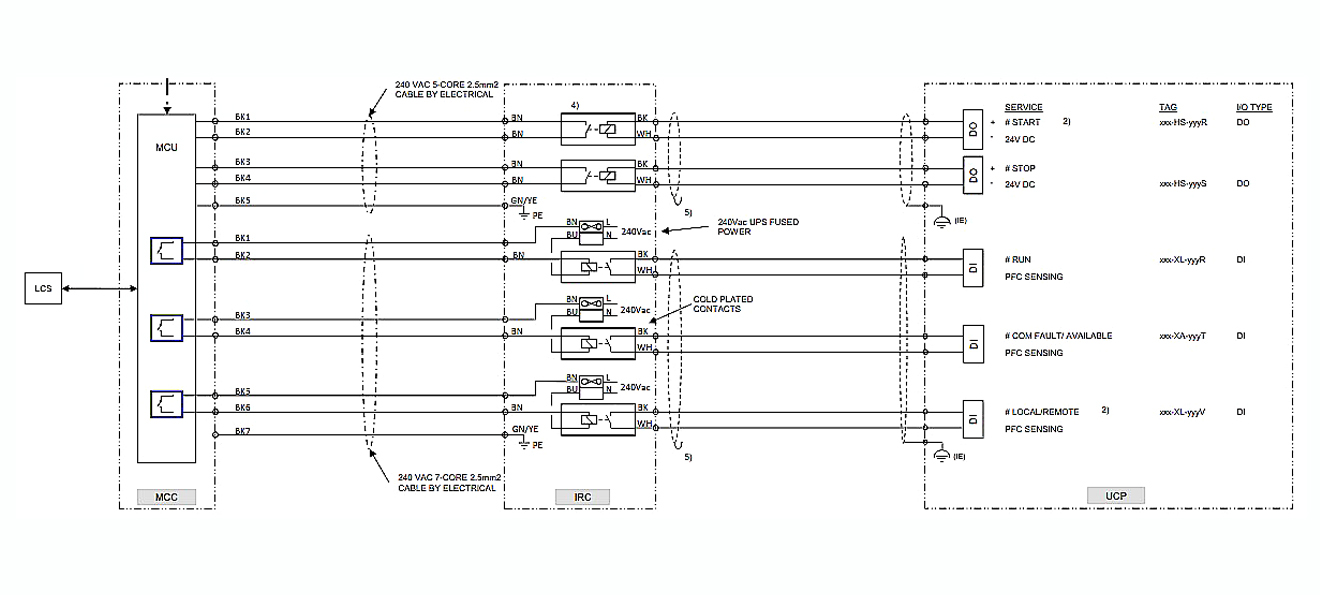
Using hard-wired cables to transfer motor signals through IRC.
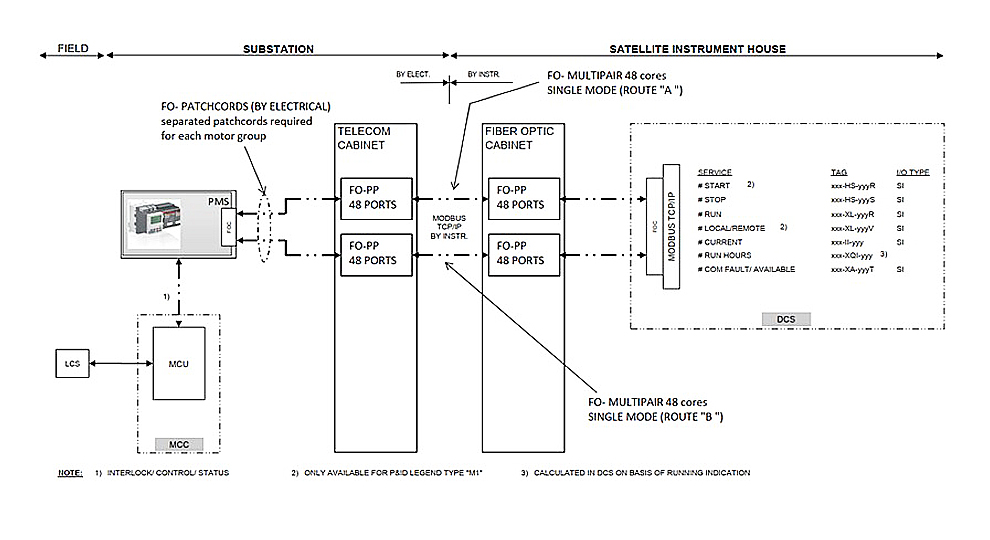
Using fiber cables to transfer motor signals through PMS.
Smarter Engineering
Optimized Spent Caustic Treatment System and Dismantlable Flare
Once the ethylene cracking plant of this project begins operations, it will produce considerable amount of spent caustic, which is hazardous to the environment. Proper treatment of spent caustic is therefore very important. Traditionally, spent caustic are treated with wet air oxidation (WAO), which is to thermally oxidize organic pollutants in a high temperature and high pressure environment. Despite WAO is a mature and widely adopted technique for treating high concentration of polluted wastewater, its effectiveness is conditioned upon treating the wastewater with high temperatures and high pressures, otherwise the result will be less than optimal. Since it is costly to own such equipment and operate under high temperatures and pressures, it is not economical to use WAO for stand-alone spent caustic treatment without an ideal environmental condition. To resolve this issue, CTCI Corporation came up with another optimized spent caustic treatment system by combining WAO with Fenton technology. Fenton is a chemical oxidation process, where H2O2 is used as oxidant and Fe2+ as catalyst. This method is advantageous in that it enjoys flexibility and low-cost. In the end, CTCI Corporation successfully used this novel way to treat spent caustic thoroughly. Not only will this help the client to reduce cost on spent caustic treatment, but will also help protect the environment. Another innovation in this project is the dismantlable flare. Standing at 175 meters, the flare of this project is the highest in CTCI’s project history. To build such a long flare, CTCI Corporation broke down the whole flare piping into 7 sections, which were fabricated separately in a fabrication shop, then assembled on site. On average, each section only required two to three days for assembly, which substantially saves man-hours and manpower. Furthermore, there is an additional advantage using the dismantlable flare. Traditional flares occupy a large area of land and need to be kept a considerable distance (usually in different areas) from each other because the flares are not tall enough to ensure safety when flammable and toxic organic waste gas are burnt inside the flares. The tall and dismantlable flare used in this project, on the other hand, can reduce safety radius required at ground level, and can even allow a second flare to be placed in the same area. Thanks to such design, maintenance work no longer needs to be performed at the top of the flare. Instead, one only needs to hoist the top section of the flare to the ground level for maintenance. When the maintenance work of one flare is ongoing, the rest of the flares can keep working, ensuring normal operations of the whole plant.
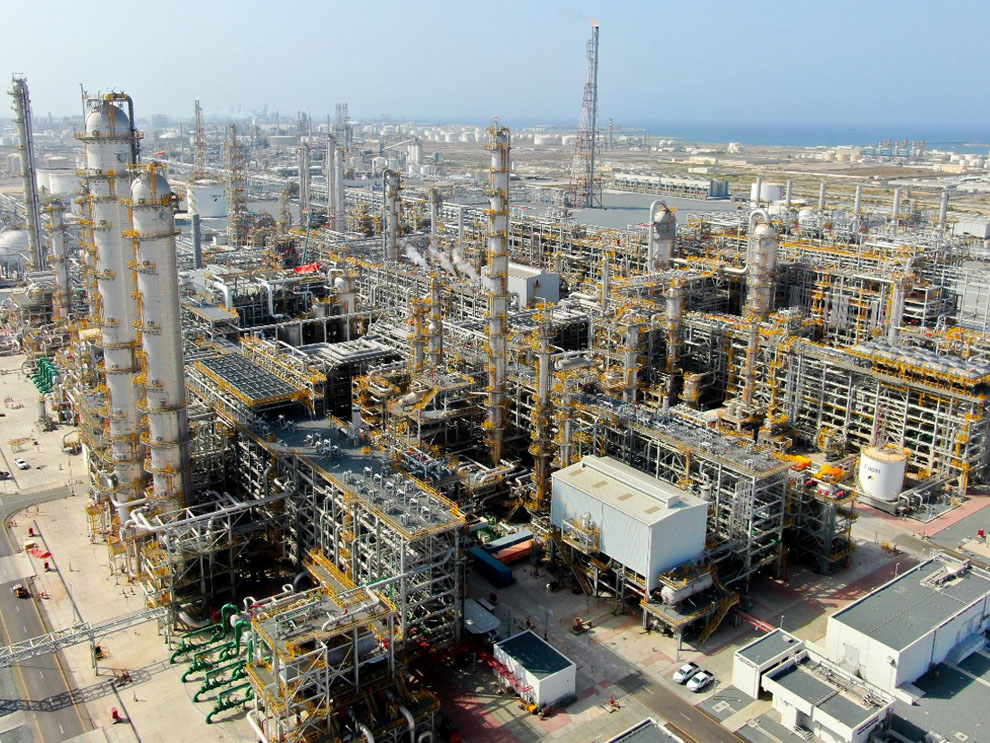
An aerial view of the completed plant.
The Key to complete this critical project lies in the perseverance of its team members. Through determination and perseverance, we can accomplish great things. As the famous saying goes,” Where there is a Will, there is a Way” --Oman Qaboos, the owner