Discover Reliable
發現信賴
CTCI Successfully Constructs Taiwan’s First-Ever Coal-Fired Ultra-Supercritical Power Plant: Taipower Lin Kou Power Plant Renewal EPC Project
— K. S. Chen, Project Engineer, Power & Energy Dept. II, CTCI Corp., Group Engineering Business
- Market:Power
- Owner:Taiwan Power Company (Taipower)
- Technology authorized by:Mitsubishi Corporation (MC)/Mitsubishi Hitachi Power Systems (MHPS)
- Commercial Operation Date:
Unit-1: October 2016, Unit-2: March 2017, Unit-3: October 2019 - Location:Lin Kou, New Taipei City
- Scope of Work:EPC work for main generating equipment
- Capacity:2,400MW
After forty years of service, Lin Kou Power Plant, a power station located in northern Taiwan and owned by Taiwan’s Taipower Company, gradually saw declining generating efficiency. Coupled with rising power demand across the nation and an aim to reduce carbon emission, the owner decided to renew the plant by building coal-fired Ultra-Supercritical (USC) Power Generating Units. In this massive-scale and important national project undertaken by the Consortium of CTCI Corporation (CTCI) and Mitsubishi Corporation (MC), Japan, three 800MW-coal-fired USC power generating units (totaling 2,400MW) were constructed in several phases, with existing power plants remaining in operation all the while and only to be demolished after full completion of the project. Each new unit comprises cutting-edge coal-fired USC boiler, steam turbine generator, air quality control system (AQCS), as well as primary and supporting systems, such as condenser, flue gas desulfurization system, dust collection equipment, electrical system, and instrument and control system. Other common facilities, such as demineralized water treatment system, piping system, compressed air system, crane, monorail hoist, and civil work for foundations and buildings, are also involved. Work began with all efforts as soon as CTCI was awarded the contract in August 2011, undergoing intense design, procurement, construction, and commissioning phases. Thanks to the efforts put in by project team members, difficulties and challenges have been overcome, resulting in the successful commercial operation of Unit-1 and Unit-2 on schedule in October 2016 and March 2017, respectively. The plant became the most crucial source of power supply in northern Taiwan. Unit-3—the only Taipower’s new unit put into power generation operation in 2019—was completed and synchronized in February 2019, with commercial operation achieved in October later that year. The completion of this project stands as a testimony to the fact that Taiwan’s power generation industry technology and its construction techniques have been on par with top global players. This is indeed epoch-making.
Why CTCI?
EPC Experience and Capability in Power Plants of Taiwan
CTCI has been engaged in and has successfully completed several power plant projects in Taiwan, including Taipower’s Dah Tarn Combined Cycle Power Plant, Hsin Ta Combined Cycle Power Plant, Nan Pu Power Plant, and some other power plants operated by independent power producers (IPP), such as Ever Power, Kuo Kuang, and Chia Hui. CTCI has professional expertise, project management ability, and a reliable supply chain. In particular, the completion of Dah Tarn Combined Cycle Power Plant proves that CTCI is skilled in execution of power plant EPC projects, winning Taipower’s utmost trust with excellent quality of service during plant constructions.
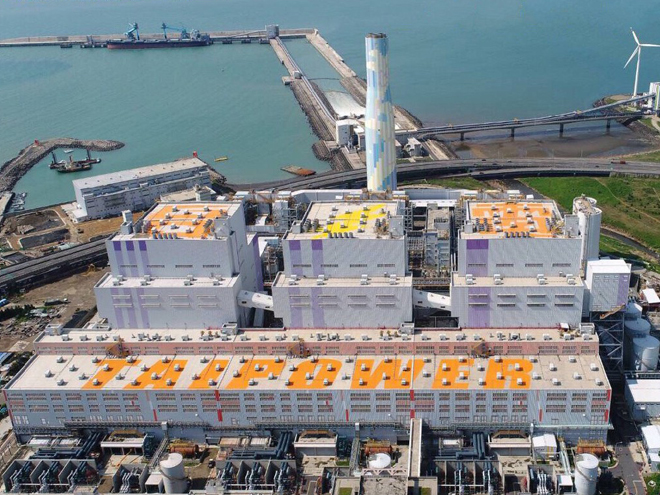
An aerial view of Lin Kou Power Plant.
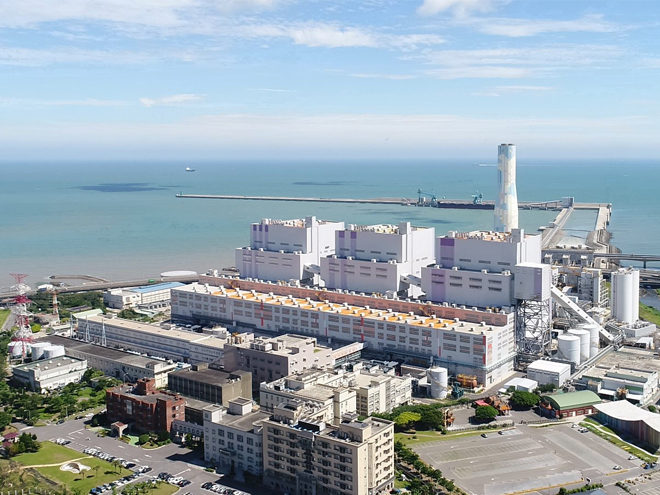
An overall view of Lin Kou Power Plant.
Reliable Realized
Integration of Design Interfaces and Control of Procurement Schedule
Currently, coal-fired power generation remains a major source in Taiwan’s energy structure. Given Taiwan’s highly developed economy, maintaining stable power supply has become the nation’s most important infrastructure priority. However, controversy remains with respect to coal-fired power plants’ contribution to environmental pollution and global warming due to massive amount of carbon dioxide emissions. In face with such a crucial task to strike a balance between coal-fired power generation and environmental protection, the solution that the power industry proposes and is committed to is to boost the generation unit’s operation efficiency, reduce energy loss, and raise environmental standards. This is why the coal-fired USC power generating unit, with its enhanced capacity and power efficiency, is now not only the most advanced power technology, but is also the mainstream in thermal power plants. To ensure that the whole design can be considered and examined in the most thorough manner during the engineering stage, a task force was formed, where CTCI works with Mitsubishi Corporation (MC) and Mitsubishi Hitachi Power Systems (MHPS) to integrate design interfaces by feeding equipment, piping, steel structure, electrical, instrument and control data into the system with 3D model. This integration enhances constructability and reduces disruptions to site installations. In addition, such data can be transferred to the site for construction uses. In all, around 384 vendors responsible for major material and equipment and nearly 400 subcontractors responsible for construction and installation were involved in this project. To lower the risk of price escalation, the orders of critical equipment or packages of Unit-1, 2 and 3 were placed concurrently in the early stage of this project. To keep track of the progress of the requisitions and orders on material, equipment, and construction, a procurement schedule control log was set up according to the construction plan as well as equipment manufacturing and delivery schedule. This ensures timely control on the vendors’ manufacturing status to meet the demand of construction progress.
Technical Matters
Boosting Welding Techniques and Quality
Depending on the main steam pressure and temperature inside a boiler, which are measured against “the critical point of water” at 22.115Mpa and 374.15°C, respectively, coal-fired power generating units can be classified into various types. A typical “subcritical” power generating unit—that is, with main steam pressure and temperature lower than the “critical point of water”—stands at around 16Mpa and 538°C, whereas a “supercritical” unit stands at above 22.115Mpa and 374.15°C. An “Ultra-Supercritical” unit, on the other hand, sees main steam pressure higher than 27 Mpa and temperature higher than 580°C. In the case of Lin Kou Power Plant, the state-of-the-art and highly efficient coal-fired USC power generating units are operating at 25.35 Mpa and 604°C. The higher the boiler pressure and temperature, the higher the power efficiency, which also means lower coal consumption and pollutant emissions. Compared to old units, USC units can save up to 50 tons of coal consumption and 108 tons of carbon emissions per year. In addition, the advanced air quality control system (AQCS) in place helps reduce SOx level to 5-10ppm (EPA standard: 60ppm), NOx level to 16-23ppm (EPA standard: 70ppm), and particulate matter to 2-10 mg/Nm³ (EPA standard: 20 mg/Nm³), which are all far better than the EPA standards (see table below for details).
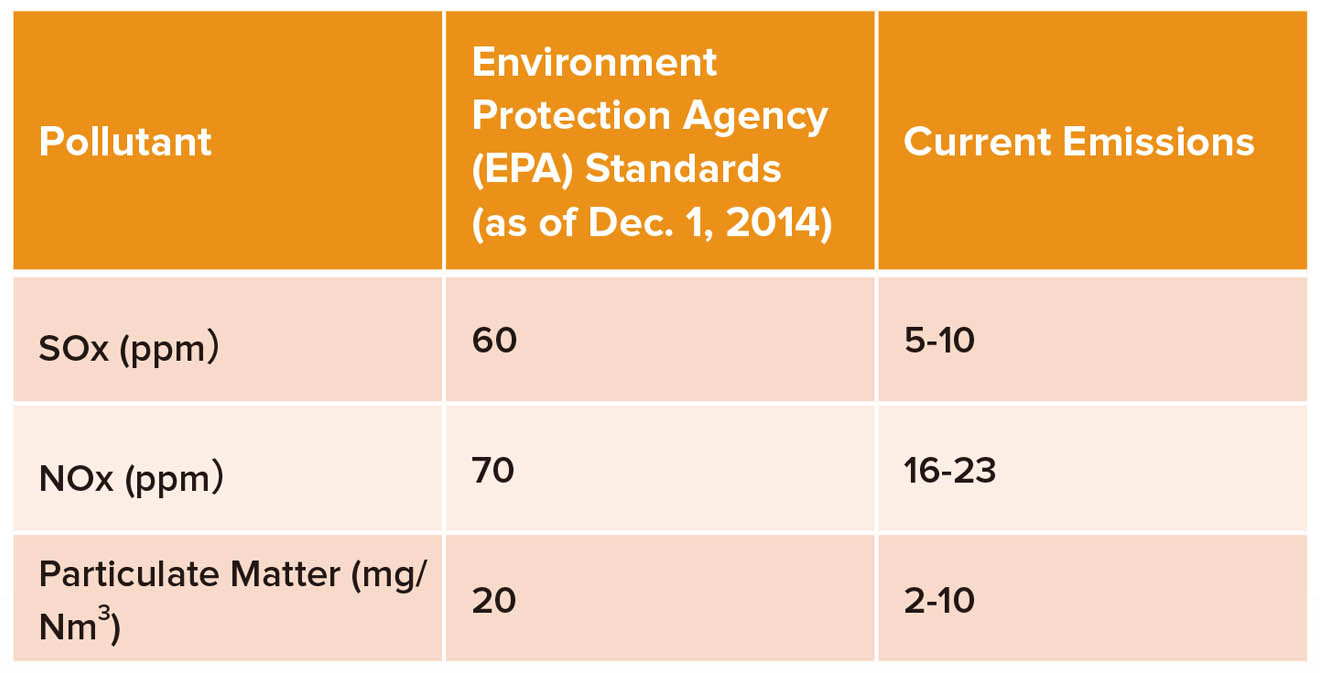
Comparing Lin Kou Power Plant’s air pollutant emissions against legal standards
Compared to subcritical generating unit, USC unit’s extreme main steam pressure at 25.35 Mpa and high temperature at 604°C means that the boiler requires a large amount of cutting-edge alloy steel materials (such as P91/P92) that are stronger and can withstand extreme heat. Welding quality is another direct factor on the unit’s stability and power efficiency, requiring high-quality welding techniques with respect to various high grade materials. CTCI took advantage of this construction project to train a large number of certified technicians, something that in turn robustly boosts Taiwan’s overall power construction project skills.
Smarter Engineering
New Installation Method for Heavy Equipment Lifting
Soaring more than 80 meters, the boiler at Lin Kou Power Plant is Taiwan’s first-ever mega equipment installation, an extreme challenge in terms of installation techniques. Therefore, the lifting plan and installation method of such heavy equipment have been thoroughly discussed and arranged in details during the early stage of engineering. For example, the boiler top girders were installed using bar jack lifting system, while the generators and IP/HP turbines were secured on-base using heavy equipment lifting method by combining gantry, bar jack and turn table. These two methods effectively shorten the installation schedule of lifting work, boost installation efficiency, and enhance work safety. For this reason, CTCI has earned recognition and praise from the owner, Taipower.
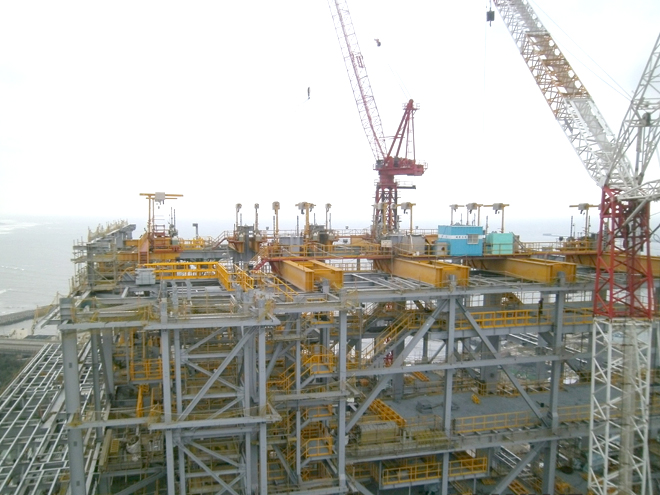
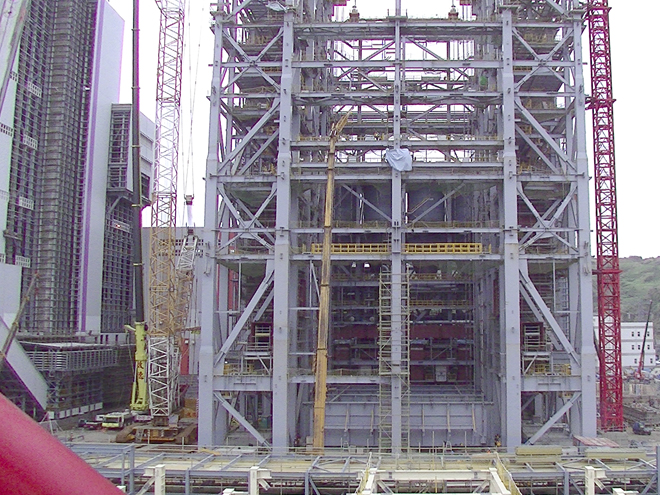
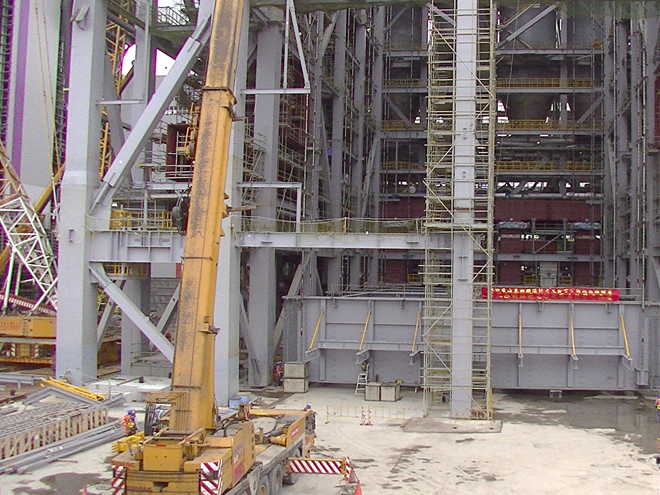
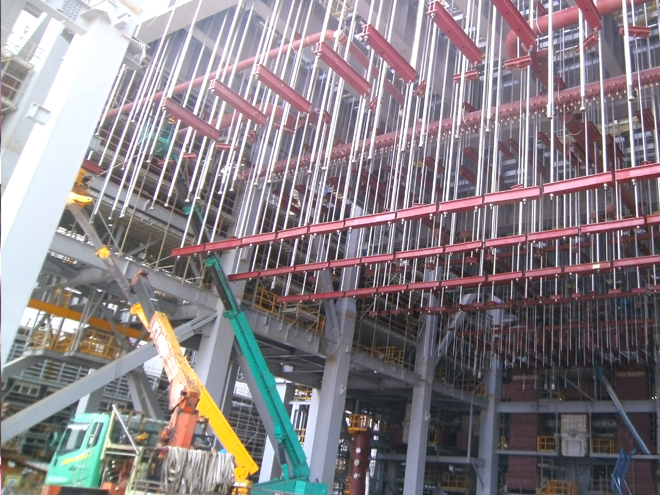
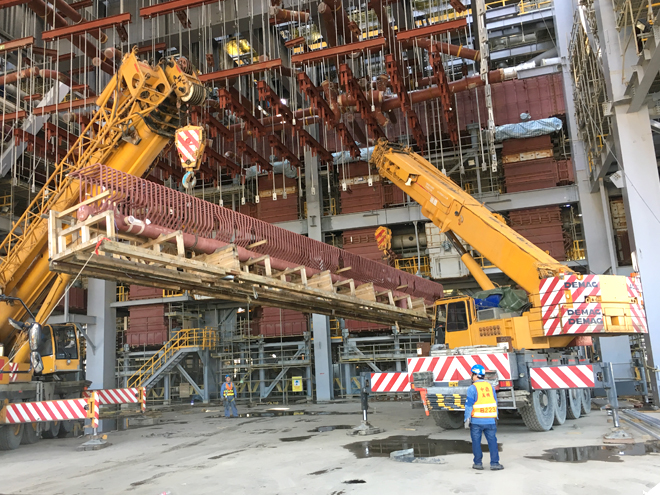

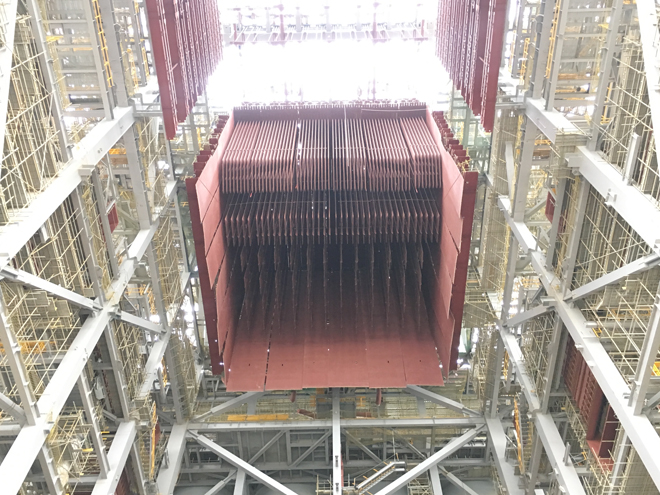
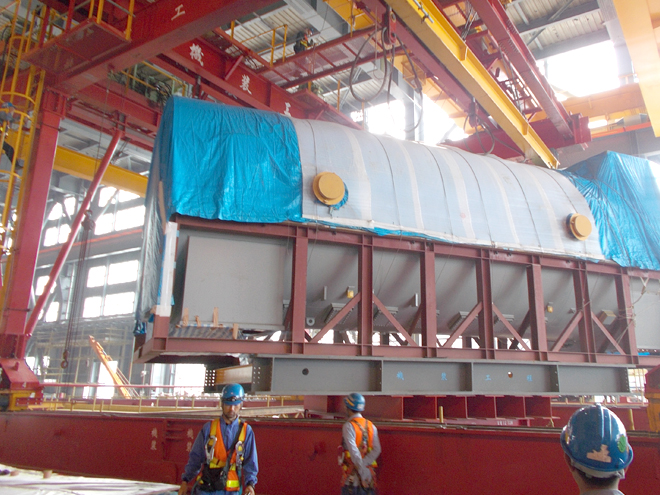

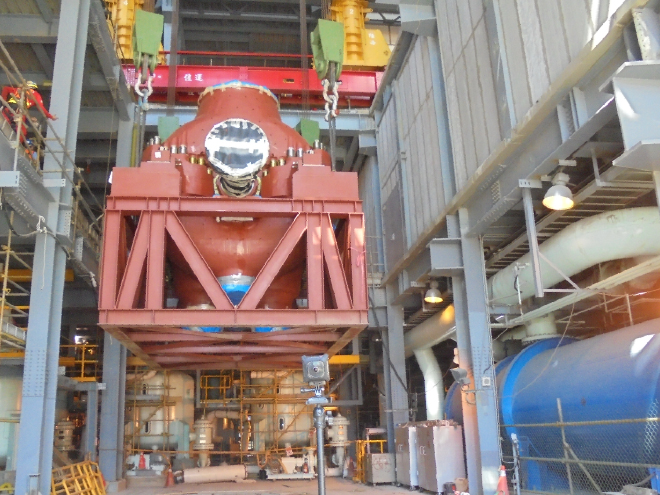
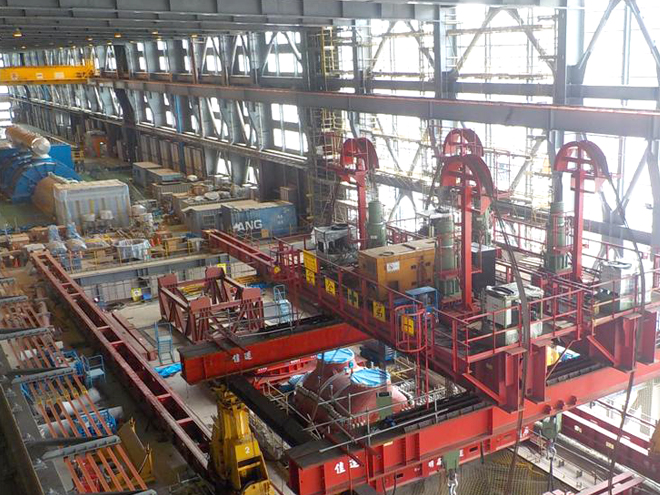
During the execution of Lin Kou Project, CTCI project team coordinated very well with Taipower, and had always been willing to communicate with related parties who have different opinions. Hence, there were no significant disputes. --Mr. H. P. Tseng, Project Manager, Department of Nuclear and Fossil Power Project, Taiwan Power Company
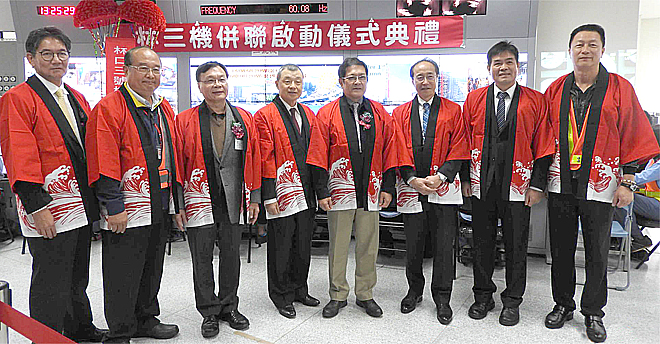
Lin Kou Power Plant Unit-3 Synchronization Ceremony (from left to right): MC President Go Ishikawa, Taipower Vice President W. T. Chen, Taipower Director C. B. Li, CTCI Group Chairman John T. Yu, Taipower Chairman W. F. Yang, MHPS Executive Vice President Yoshiyuki Wakabayashi, Taipower Director M. T. Chiang, and Taipower Plant General Manager Y. C. Chu.
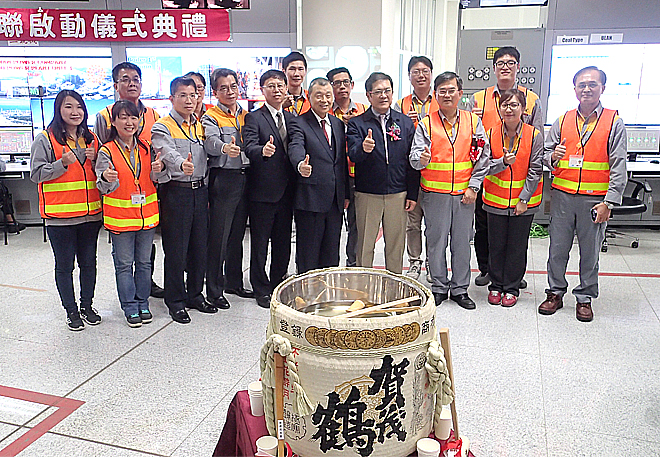
CTCI Group Chairman John T. Yu (fifth from right) poses for a group photo with Taipower Chairman W. F. Yang (fourth from right) and CTCI project team at Lin Kou Power Plant Unit-3 Synchronization Ceremony.