Technology
技術分享
ECOVE, Company of CTCI, Utilizes Self-developed Energy-from-Waste Plant O&M Technology, Winning Recognition for Improving Gangshan Energy-from-Waste Plant Performance
— Chieh-Ming Yang, Engineer, Technology Development Department, ECOVE ESC, Group Resource Cycling Business — Jackson Jih, Senior General Manager, Technology Development Department, ECOVE ESC, Group Resource Cycling Business
ECOVE, a CTCI company, has been engaged in Energy-from-Waste plant O&M service for more than two decades. With rich experiences, ECOVE introduces the latest Energy-from-Waste process/technology to optimize performance operation of Energy-from-Waste plants, successfully completing the first Energy-from-Waste plant life extension project in Taiwan. ECOVE not only won the owner’s affirmation, but has established a milestone for Energy-from-Waste plant revamping in Taiwan.
Solving the Low Operation Performance Problem of Old Energy-from-Waste Plant by Virtue of Self-developed Technology
More than 20 Energy-from-Waste plants in Taiwan have been operating for nearly 20 years and are entering the peak period of revamping. After decades of operation, the performance of plants has significantly declined. Take Gangshan Energy-from-Waste plant for example, started operation from 2001, it faces the issue of aging with all kinds of equipment and systems . Non-planned shutdown often has occurred in recent years, resulting in low operation runtimes and impacting on waste management of the whole city. So the Owner Taiwan Sugar Company has been working hard to seek solutions to improve the performance of the Gangshan Energy-from-Waste plant. ECOVE Environment Services Corp. (hereinafter referred to as ECOVE ESC)., a subsidiary of ECOVE Environment Corporation, belongs to the Group Resource Cycling Business of CTCI. ECOVE ESC is one of the best Energy-from-Waste plant O&M professional managers in Taiwan. Of the total 24 Energy-from-Waste plants in Taiwan, ECOVE ESC operates seven of them, accounting for 26.4% of the designed capacity of the 24 plants combined in 2018, while the actual waste treated were 29.8% and power generated was 32.5%. In daily operations, colleagues continue to work by the principle of optimizing "Resource Cycling Efficiency™" in terms of plants maintenance, technology and equipment upgrade. ECOVE ESC won the Gangshan Energy-from-Waste plant performance improvement contract in May 2017 for having plenty of experiences in Energy-from-Waste plant operation and maintenance. After the project team entered the plant, it worked towards two major directions “Revamping” and “O&M” simultaneously. It collected cross-plant resource, knowledge, and experience to provide strong backing for project implementation.
Rapid Mobilization, Multi-pronged Approach for Capability Enhancement
In terms of revamping work, the ECOVE ESC project team, consisted of experienced professionals in different backgrounds, has s investigated all the process systems and analyzed operation data, proposing a plan in four directions: Waste treatment capacity improvement, Energy-from-waste efficiency improvement, pollutant discharge reduction, and operation safety and stability improvement.
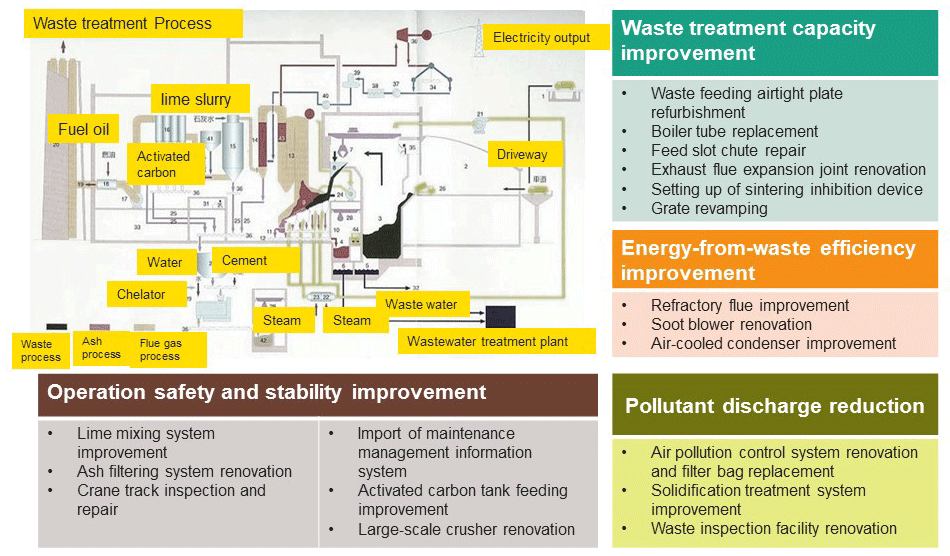
Revamping plan (excerpted version).
Take "Waste treatment capacity improvement," as an example. The project team cladded high corrosion-resistant alloy “INCONEL” on the tube surface in corrosion prone areas. This tube anti-corrosion process has been verified since 2004, and has effectively reduced the tube breakage caused by corrosion, and the risk of shutdown. In addition, the project team applied two new self-developed patented clinker breaker system (patent number M424465, M563523). So far, there has been no shutdown caused by clogging of the clinker. In comparison with the pervious situation where the average shutdown frequency was once every two weeks, the improvement is remarkable. For the O&M service, the project team organizes an expert team whose members are from other Energy-from-Waste plants operated by ECOVE ESC. The team refined the management and technology of the operation and maintenance of the Ganshan plant, and conducted education and training to ensure stable and safe operation.
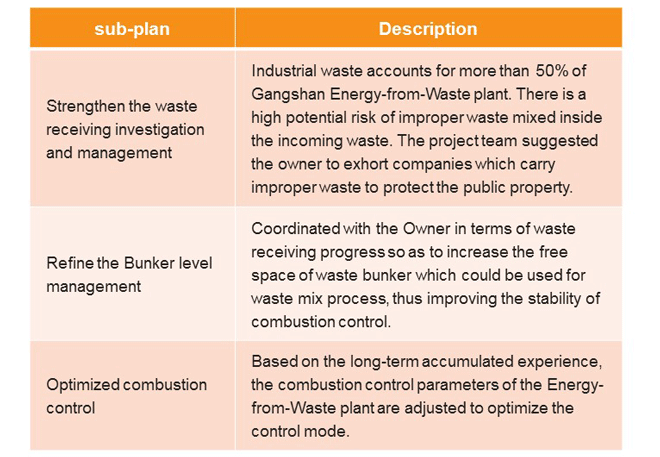
Operation items of the O&M plan (excerpted version)
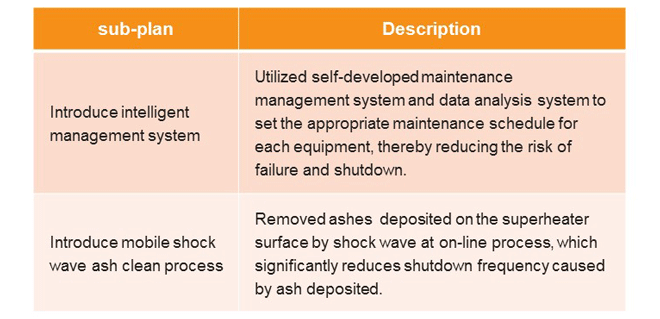
Maintenance items of the O&M plan (excerpted version)
Completed Gangshan Energy-from-Waste Plant Performance Improvement, Receiving Recognition from the Owner
The Gangshan Energy-from-Waste Plant Revamping Project contracted by ECOVE ESC has achieved numerous effects as below for Gangshan Energy-from-Waste Plant Revamping Project contracted by utilizing multiple technologies. ● Boiler average steam production rate increased by 26% (compared to 2017). ● The number of shutdowns caused by tube breaking decreased by 73%, which only occurred once in the first half of 2019. ● Increased operating run time by 18% (compared to 2017). ● In 2019, the treated waste quantity increased by about 7% (compared to 2018), over 38% higher than the average waste treated of the past five years (2014-2018). ● In May 2019, it set a new monthly record of incineration quantity of past five years, and was praised by the owner.
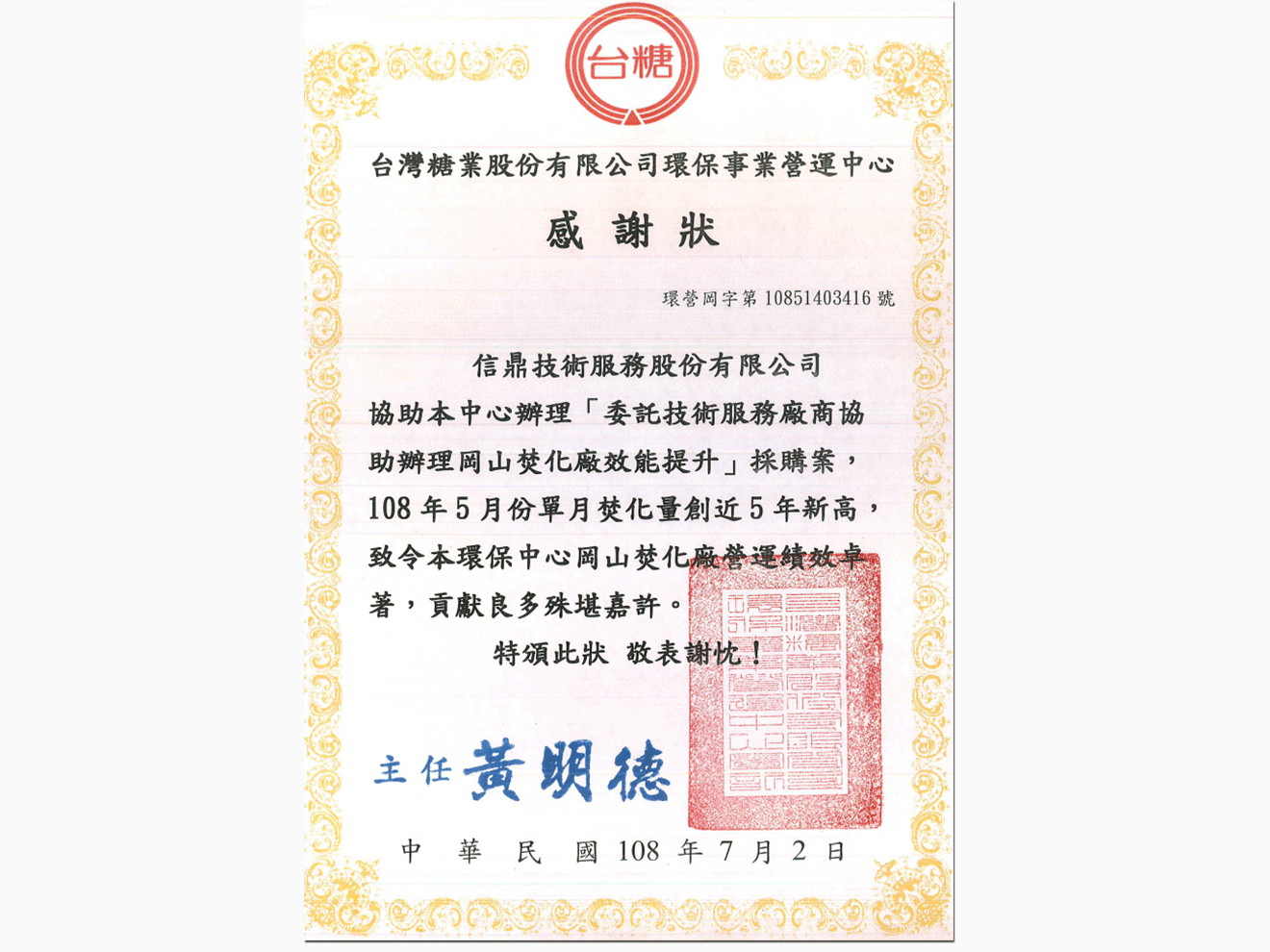
The Owner Taiwan Sugar Company gives a letter of appreciation to ECOVE ESC.
The success of the Gangshan Energy-from-Waste plant performance improvement project showcases the expertise of CTCI Group Resource Cycling Business for capability enhancement of Energy-from-Waste plants. In the future, CTCI will continue to utilize experience and developing technology in this field, relying on intelligent operation, maintenance management system, and equipment upgrading knowledge in Energy-from-Waste plants to resolve the aging bottleneck encountered by Taiwan's Energy-from-Waste plants and increase the resource cycling efficiency.