Sustainable Future
永續未來
Optimized Application of Virtual Plant in Chemical Process
— Jung-Chieh Chiu, Engineer, Factory Optimization Department, CTCI Advanced Systems Inc., GISB
With its commitment to global sustainability, core expertise that responds to UN's 17 Sustainable Development Goals (SDGs), and through total participation in CSR excellence practices, CTCI plans to enlarge its influence in global sustainability through engineering expertise. CTCI Advanced Systems Inc. has been committed to the development of smart technology and green technologies, and encouraged industrial upgradation. It has invested in the development of process simulation technology and applications for over 30 years using simulation technology to solve various problems of customers in chemical process. With improved performance in cutting-edge process simulation tools, more features and greater integration make process research and analysis easier. Using AspenTech® process simulation software, it builds a complete virtual plant and extends it to dynamic simulation. It hopes to build a complete Cyber-Physical System through Virtual Plant, and assist customers in industrial upgradation and intelligent transformation to achieve the highest production, improve plant management, reduce sewage and energy waste economically, and develop high-efficiency plant based on the four goals of industry: innovation and infrastructure, sustainable cities, responsible consumption and production, and climate action that echoes SDGs.
Important Part of the Industry 4.0
Cyber-Physical System (CPS) is the key technology in Industry 4.0. In the virtual plant, the process, related equipment and facilities can be established as a virtual model of the factory. In addition to virtual and physical interface, virtual plants are an important part of technology development in the factory. However, it is not a new concept. Aspen Technology, Inc. (AspenTech®) has been developing and integrating process simulation-related software for over 30 years. Flow-field analysis software, such as Autodesk CFD and COMSOL can simulate the flow of fluids in a device; Intergraph SmartPlant® 3D builds real-world 3D models into the computer. It can create a virtual plant in the virtual end, but we can classify it into the following three virtual plants as per need: process flow, process equipment and visual model. The virtual plant of the process flow is suitable for process analysis in chemical and petrochemical industry owing to its accuracy and reliability in calculation.
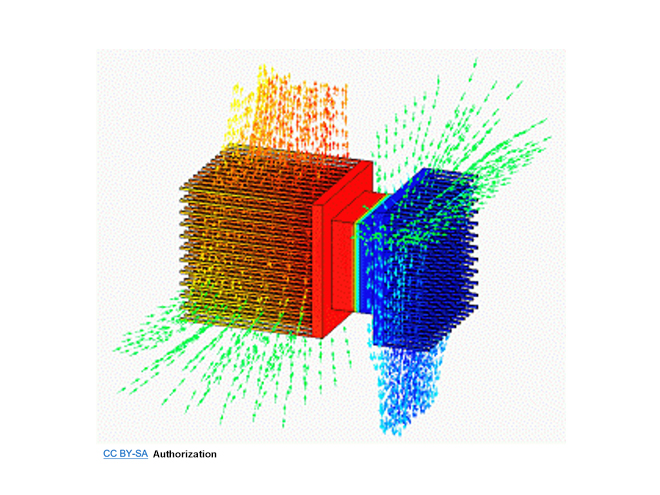
Graphical flow-field analysis in a Virtual Plant.
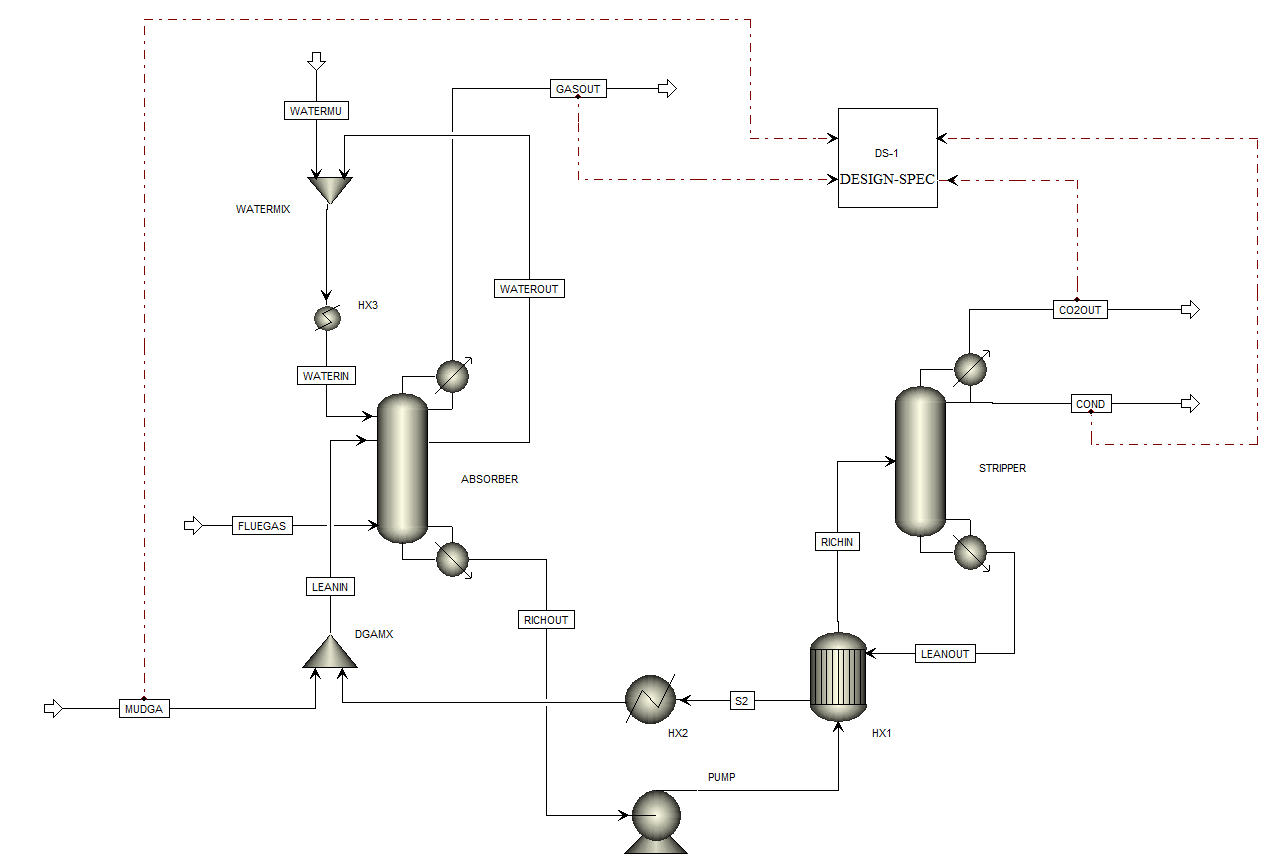
Process flow diagram of the Virtual Plant.
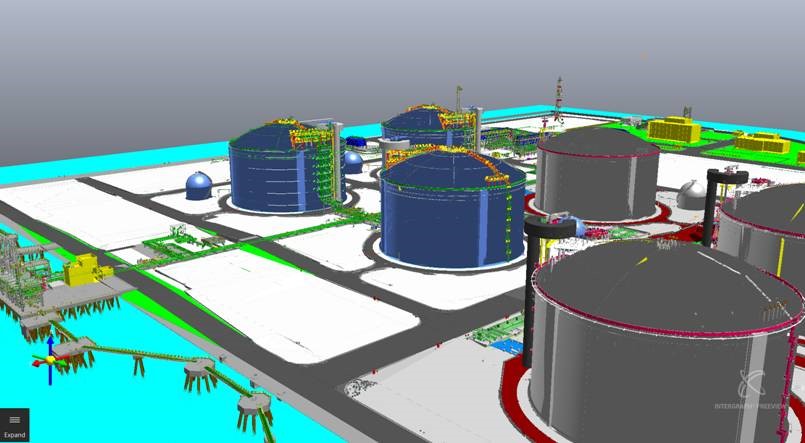
The Visual 3D model built by the software.
Focus on Process for Best Solution
Process simulation software uses lumped models to simulate the operational state of the process. The lumped model does not consider the influence of spatial gradients in the equipment, which improves calculation speed and versatility. The model adds the correction parameters depending upon deviation from the real situation, and the reliable material thermodynamic model is used to improve the reliability of the model calculation. CTCI Advanced Systems Inc. uses AspenTech® process simulation software (includes Aspen Plus and Aspen HYSYS) to create virtual plants with plant data (design data and process historical data) provided by the customer. The virtual plant can be a single device or a complete process, and uses a built-in virtual plant combined with process knowledge to analyze possible bottlenecks in the process and explore options for their elimination and suggest optimal solutions. In general, if the customer provides more complete plant data, the model reliability will be greater, as also its completeness of analysis. CTCI Advanced Systems Inc. provides a variety of services in virtual plant: process evaluation, safety analysis, pipe network analysis, operator training system, process control strategy analysis, etc. Before building a process virtual plant, the team must have a deep understanding of process-related knowledge, and when the virtual plant is put in place, it can identify potential problems and provide advice. Once the virtual plant model is in place, it is possible to use the known data to estimate the data that is difficult to measure in the plant, as well as generate safety analysis and pipe network analysis for the plant, etc. To create a dynamic model of the process, it can analyze the dynamic behavior of the process, such as the process control strategy, or apply this virtual plant to the operator training system. Various applications described enable the process plant to be analyzed by virtual plant from design to operation and maintenance to maintain the plant in the optimal state of operation.
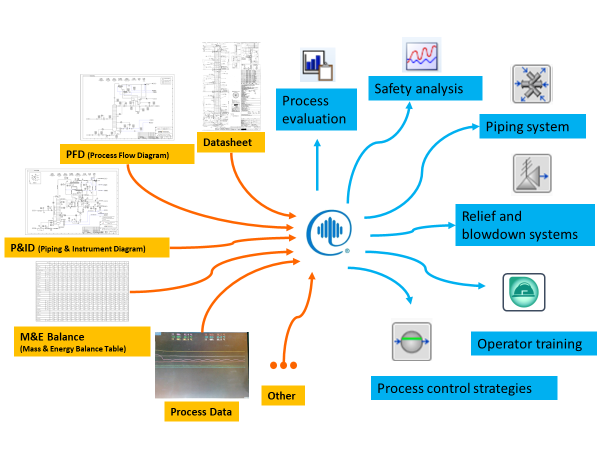
Required information and computable analysis for Process Virtual Plant.
Create the Best Benefits for Our Customers
Every part of the plant is indispensable. A well-known pigments and specialty chemicals company of Taiwan uses large amounts of organic solvents in the process of color material production. It employs CTCI Advanced Systems Inc. virtual plants. Owing to economic and environmental factors, most of the solvent produced will be recycled to avoid solvent accumulation and waste. The solvent-handling unit of the plant is therefore an important operating unit. In the customer's product process, the process has been upgraded, and the solvent replaced. However, the solvent treatment unit has not been updated simultaneously and problems like capacity and solvent loss have gradually emerged over years of operation. To solve these problems, the process needs a complete evaluation. CTCI Advanced Systems Inc. first made a preliminary assessment of the on-site process, then helped the customer install the instrumentation equipment the unit was lacking, and then used the collected data to make up for the lack of design data, and finally developed a process virtual plant. While creating it, the process data must be compared with the virtual plant's calculations to ensure consistency with on-site measurements. Then the virtual plant is used to re-evaluate the process to understand the responses of actual process under different conditions, and tests are conducted and data analyzed to find the optimal operation mode to suggest an improvement plan. After improvement, the customer's solvent treatment unit not only reduced the solvent loss by more than 2% and 70% of the solvent gas lost from the top of the distillation column but also improved the purity and quality of the recovered solvent and doubled the capacity of solvent treatment. These improvements have improved the efficiency of the original solvent-handling unit, reduced the load on the waste processing unit, generated millions of savings per year, and created a model of automation and virtual plant application for the customer. It even became a demonstration model among various plants within the company.

Process diagram of a special chemical plant.
Virtual Plant Re-evolution--Dynamic Simulation and Analysis
Steady-state process simulation establishes a virtual plant that simulates the state of a continuous process plant during steady operation. Dynamic simulation takes into account changes in plant operations over time, and the model is more complex and closer to the state of plant operation. Dynamic virtual plants need more information, and whether the data is complete or not is often the key to the reliability of the model. In the AspenTech® process simulation software, dynamic models need to be generated from a steady-state model. In other words, we must first establish a steady-state virtual plant, coupled with equipment-time-related parameters and controllers, and then "convert" it into a dynamic virtual plant.
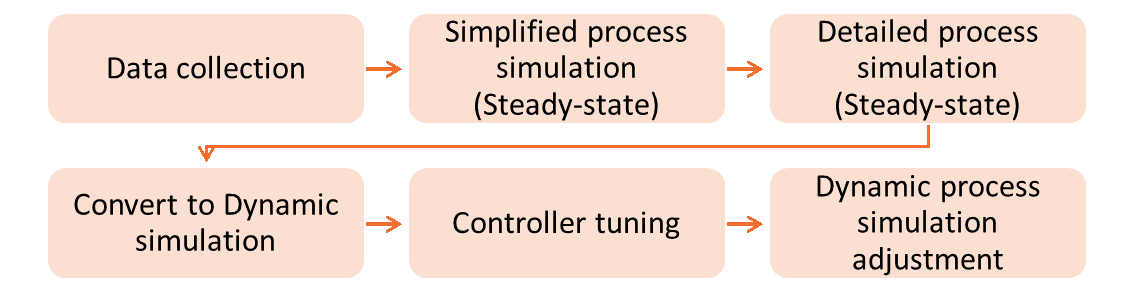
Flowchart for building a dynamic Virtual Plant.
After converting to a dynamic model, the subsequent steps are the same as of a plant operation preparation. These preparations take a lot of time, even taking time several times of the original steady-state model. The plant needs to do controller tuning, and the dynamic virtual plant is still inevitable. The plant must ensure the device function, and the virtual plant must also confirm that each unit of the model works as usual and provides correct and reliable information. Experience shows that when a team tries to copy a plant in operation it often takes more time to control and adjust to the baseline case in the virtual plant if the plant is not easily controlled.
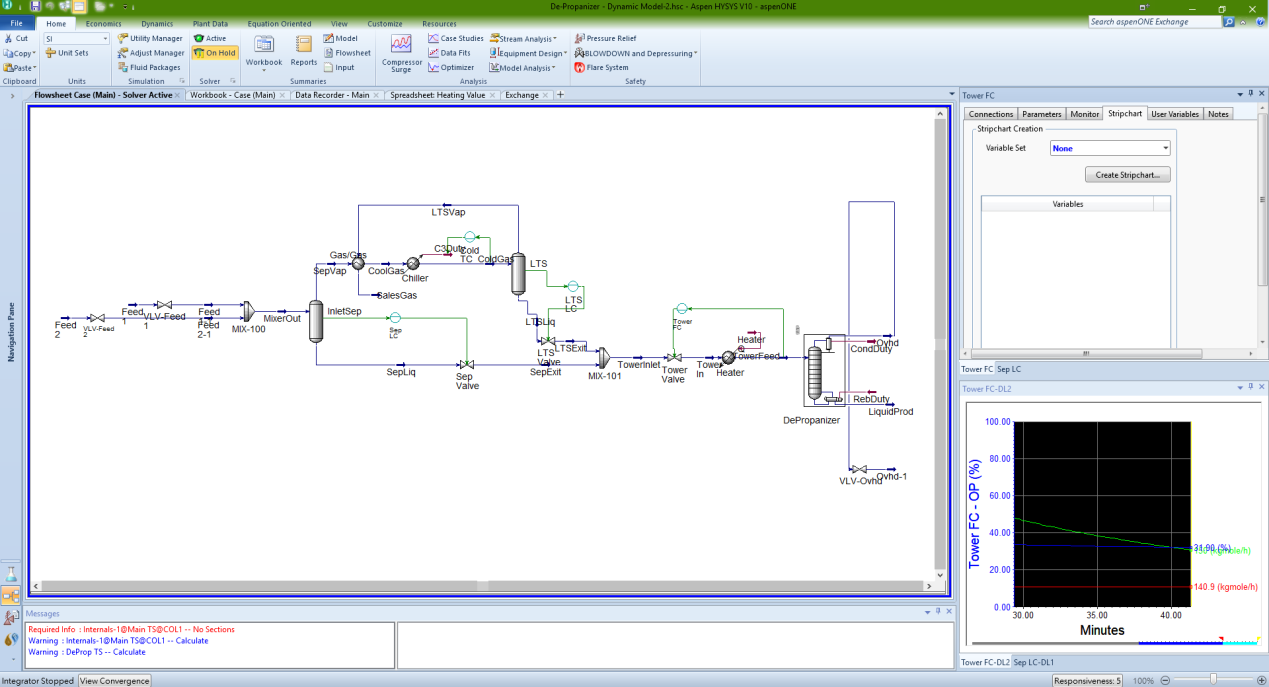
Dynamic simulation software interface.
After the completion of the dynamic virtual plant, more practical problems can be analyzed. At the design stage, dynamic control can be used to understand the control effect of the current control strategy, and the entire plant process can be analyzed for startup-and-shutdown operation to understand the operating behavior of the plant in these states. For instance, process compressors are important and are expensive equipment in the plant. After inputting the parameters of the compressor into the dynamic virtual plant, one can do Surge Analysis of the compressor to understand the behavior of the compressor under abnormal conditions, and then propose action during design or actual operation to avoid safety issues and loss.
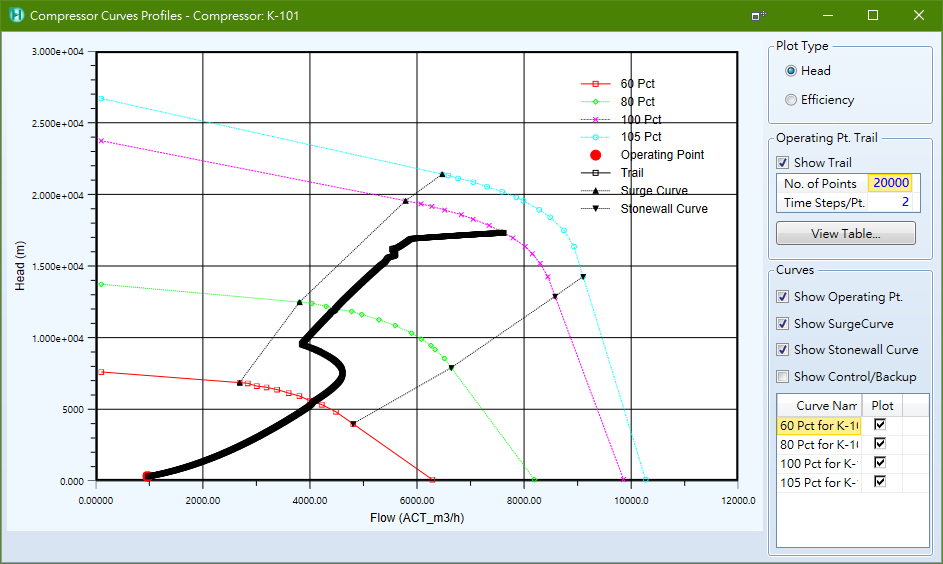
Dynamic simulation analysis example: Normal stop of the compressor.
Dynamic Simulation & Virtual Reality Integration of the Future
Simulation technology continues to advance with developments in computer technology. The process simulation software we are using now still uses the equation of chemical engineering principle. Without development of mathematical algorithms, continuous research on chemical engineering principles, and breakthroughs in computer computing technology, process simulation cannot be a practical tool. After continuous development, each individual process simulation was continuously expanded and combined to form a virtual plant. However, the virtual plant of the process flow is not perfect. When difficult to accurately represent a system that is not ideal in the real world, its reliability will be greatly reduced. At present, it takes a lot of time and computing resources to rebuild the entire plant in the simulation software for a large-scale chemical process. However, virtual plant can provide valuable and detailed information and trends to make management decisions, which is the value that virtual plant can bring. In the past, process simulation was focused on steady-state processes and has been applied in all phases of design, operation, and maintenance. Dynamic virtual plants are still an emerging architecture with potential so far and are closer to the actual plant and more suitable for virtual part in the Cyber-Physical System. To complete the Cyber-Physical System, several aspects need to be considered and worked out, but under the development of the dynamic virtual plant, the complete virtual and real integration system is closer at hand. We hope to build a complete Cyber-Physical System with the current information and computer technology to maximize the benefits of the virtual plants.
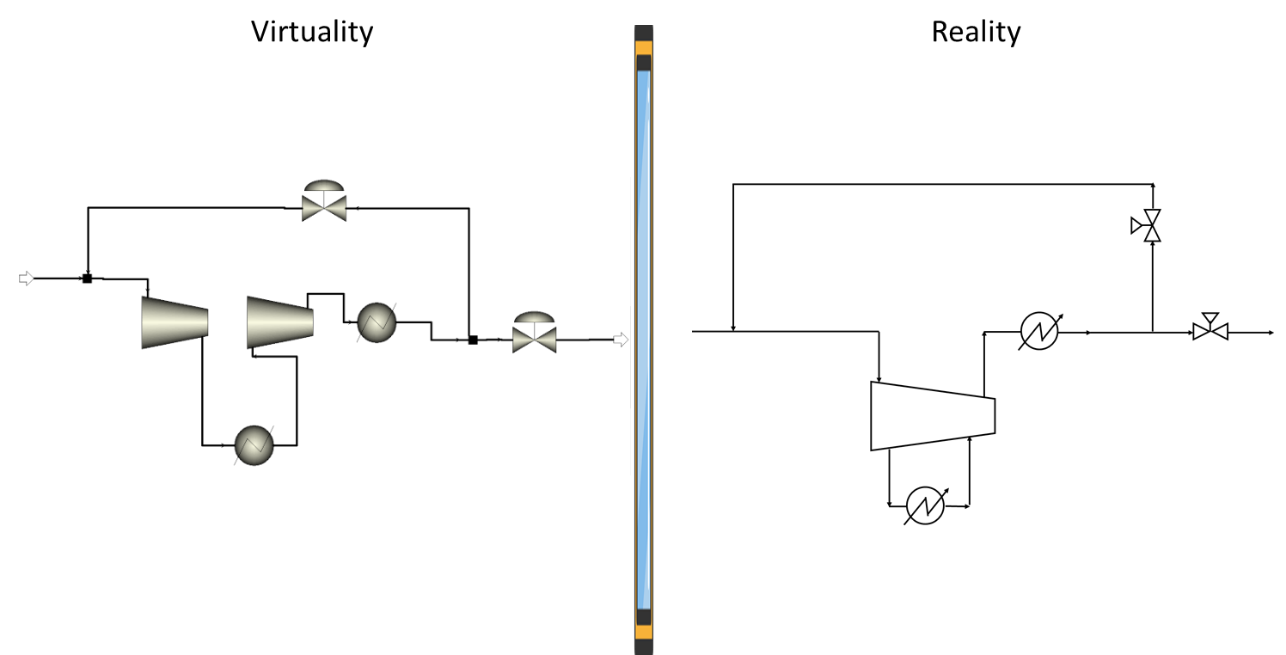
The concept of Cyber-Physical System: Establish digital twins for the factory and exchange information with each other.