Discover Reliable
發現信賴
CTCI Helps Stabilize Electricity Supply in Taiwan Taichung LNG Terminal Phase II Project - Gasification Facility and Pipeline EPC Turnkey Project
— Ken Chang, Senior Engineer, LNG Project Division of Hydrocarbon Business Operations, CTCI Corp.
- Market: Hydrocarbon
- Owner: CPC Corporation
- Completion date: August 2018
- Location: Wuqi District, Taichung City
- Project scope:Gasification Facility Expansion and Integration Phase II Project
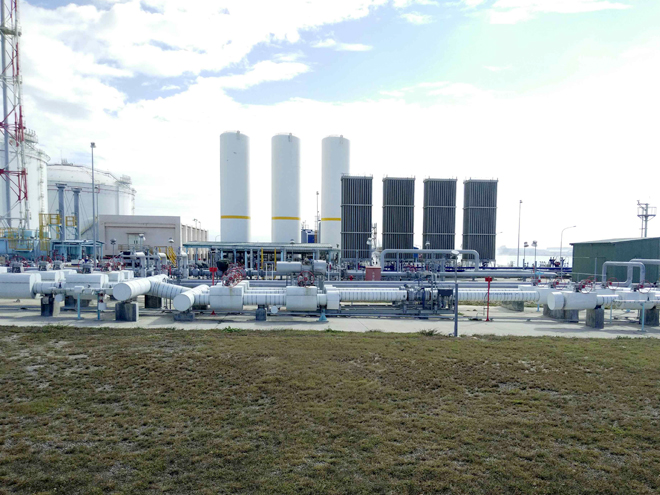
Gasification Facilities at Taichung LNG Terminal.
The Taichung Liquefied Natural Gas (LNG) Terminal was originally used to supply fuel resources required by electricity generator sets at Taipower's Datan Power Plant. As electricity generation capacity at Datan Power Plant plays a decisive role in Taiwan's energy distribution, the stability of natural gas supply at this natural gas plant is considerably vital. In line with the government's sustainable energy development policy in recent years, CPC Corporation has implemented the Phase II investment construction project at this LNG terminal in cooperation with the Tunghsiao Power Plant Upgrading and Expansion Project, and has additionally done so to increase gas supply needs for industrial and domestic users in central and northern Taiwan. This project not only includes the addition of gasification facilities and power systems, but also involves the construction of three LNG storage tanks and core process control systems (DCS, SIS, FGS, and SCADA), and long-distance natural gas pipelines, involving complex construction interfaces. This project commenced in October 2014, and was completed 46 months later in August 2018. The scope of this project included the addition of open rack vaporizers, secondary high-pressure pumps, boil off gas (BOG) compressors and 3,000 kW emergency electricity generator sets and power systems to be combined with LNG storage tanks, as well as pipelines, system control and electricity for core power control systems and long-distance gas pipelines, while cooperating with integrated testing and assisting in commissioning. Upon completion of this project, the gas supply capacity of this natural gas plant can be increased from 3 million tons per year to 5 million tons per year, while peak gas consumption turnover can be extended from 7.5 days at present to 10.4 days, thus effectively increasing gas supply reliability and reserves. Due to the large number of interface contractors in this expansion project, numerous interface integration issues, including design, construction, testing, and commissioning, arose between the existing system and other contractors in this project. At the same time, the agreement signed with the company contracted by the owner to carry out the construction of main substations was terminated, nearly causing the incompletion of Phase II power systems for which CTCI was responsible. Upholding our brand spirit of being "the most reliable," CTCI quickly developed an alternative solution by changing the source of electricity supply, thereby overcoming all difficulties in the process. CTCI promptly assisted the owner in relieving pressure on the natural gas supply schedule, and successfully completed work within the contractual deadline. CTCI’s professional technologies and high degree of cooperation were highly praised by the owner.
Why CTCI?
Extensive International Experience and High-Quality Performance in Engineering Services
CTCI has established deep roots in Taiwan's LNG sector for more than 30 years. Since 1983, CTCI has participated in the planning, design, commissioning and supervision of the first Yongan Liquefied Natural Gas Plant, while undertaking Yongan Phase II to III expansion projects and the Taichung LNG Terminal Phase I EPC Turnkey Project thereafter. CTCI also expanded its business overseas as it undertook the Shanghai and Hainan LNG terminal projects, as well as the Kochi, Dahej and Adani LNG terminal projects in India. Under a complex situation where conditions for expansion of existing facilities under the Phase II project were restricted and four separate engineering interfaces had to be coordinated simultaneously, CTCI's performance and interface integration experience in the LNG sector at home and abroad have allowed the Company to stand out among the most economically advantageous tenders, thus making it the best option to undertake this project.
Reliable Realized
Reliable Realized Integrate work interfaces, formulate plans to connect new and old systems, and maintain the normal operation of the existing system
This project mainly revolves around the expansion of gasification facilities, which serve as the core system for outputting LNG after turning into a gaseous state through heat exchange. Due to the importance of natural gas transportation to this plant, some of the existing process equipment would not be operational when connecting the existing system to the new system. In the event that no standby equipment was available in this project but natural gas still had to be transported in full quantity, connection works must be 100 percent safe. Hot tapping was even carried out on some system pipelines through hot line operation. As natural gas must be continuously delivered by the existing system without any interruption, CTCI connected both new and old pipelines and conducted system integration, thereby successfully adding new gasification facilities to production operations in a smooth manner. Starting from the design stage in this project, CTCI actively communicated with CPC Corporation and other interface contractors, and regularly convened meetings to clarify the design and work interfaces. Furthermore, CTCI formulated an interface connection plan based on its professional and extensive experience in LNG projects, while simulating pipeline integration using 3D SmartPlant Review drawings to ensure zero errors during the execution of connection works. Due to overlapping work with other manufacturers during the project period, coordination meetings and work safety meetings were held every day to confirm the daily work content and sequence with other interface manufacturers. After on-site connection works were completed, trial runs and test plans were developed, while trial runs and functional tests were jointly conducted with storage tank manufacturers and process control system manufacturers for other interfaces. The excellent engineering quality and outstanding performance of 721,000 safe man-hours without any disability and injury record in this project also earned high recognition as the project won the Public Construction Quality Award given by the Ministry of Economic Affairs.
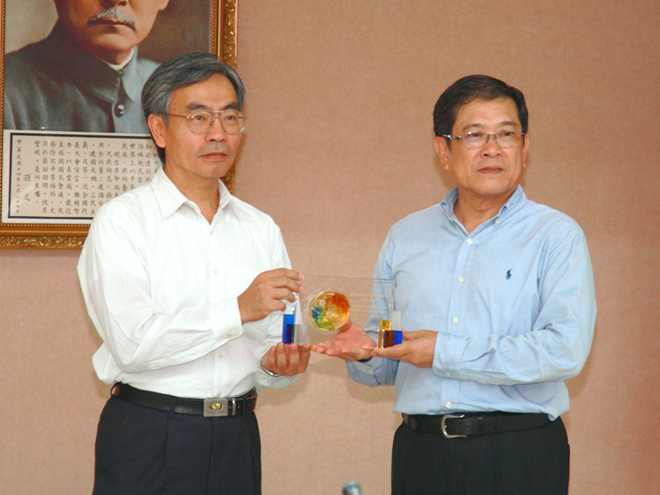
Ho I-Kang (left), Senior General Manager at CTCI, received the Public Construction Quality Award on behalf of the company from Vice Minister of Economic Affairs Yang Wei-Fuu.
Technical Matters
Improve heat transfer efficiency using special material for open rack vaporizer
An open rack vaporizer (ORV) is a type of LNG gasification equipment that contains ultra-low temperature LNG on the inside, and seawater at normal temperatures on the outside. During the operation of an ORV, the fin tubes have to withstand a temperature difference of approximately 180°C (-162°C to room temperature), and must meet a design pressure of 144 kg/cm²G (an operating pressure of 78 kg/cm²G). Hence, a special aluminum alloy material has been selected for ORV fin tubes to increase resistance to seawater corrosion, low temperatures and high pressure, as well as facilitating heat transfer efficiency. A special design was adopted to increase heat transfer efficiency, while the volume of the equipment was reduced, thus improving land utilization by 16%. In addition, the amount of materials (e.g., concrete) used in buildings was also reduced, thereby lowering carbon emissions by approximately 11 tons.
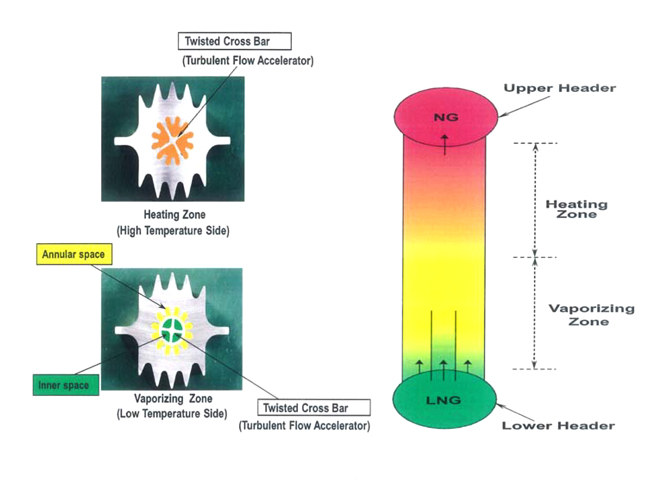
(The special star fin design applied to the fin tubes of an ORV, along with the inner spiral guide tube design, increase residence time and heat transfer area, thereby improving heat exchange efficiency.)
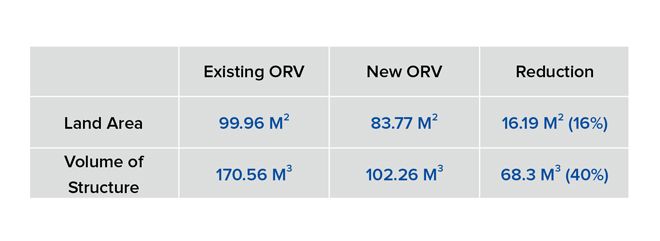
Smarter Engineering
Modular installation of equipment reduces installation duration from 2 weeks to 1 day
Natural gas metering station facilities included ultrasonic flow meters, control valves, noise reduction pressure-reducing valves and flow computers. Since these facilities provided the basis of pricing natural gas supplied by the owner to downstream users, the measurement accuracy and repeatability of these facilities were subject to extremely strict specifications. With the adoption of modular technology in this project, modular assembly of all equipment was first carried out together with elements such as supporting steel structures, pipelines and meters before they were delivered to the site. Next, calibration and testing of measurements were conducted using natural gas. After the process was witnessed on site by a third-party notary organization, the entire module package was delivered to the site for installation, thereby reducing the installation duration from 2 weeks to 1 day. Upon on-site positioning and installation, it was only necessary to connect the pipe connection between the upstream and downstream systems to the instrument, electrical and communication systems. Commissioning could be prepared once integration testing and sealing of pipelines using dry nitrogen were completed. To ensure that modular installation could be carried out smoothly, CTCI clearly divided and verified the division of labor and interface conditions for the equipment during the design stage of the metering station in this project. Conditions such as pipeline specifications, instrument control and communication specifications, power systems and wiring methods were confirmed with manufacturers during the technical clarification stage. Furthermore, since the metering station facilities had already been tested and verified at the time of shipment, no modification of metering detection values was allowed after on-site installation. Therefore, only detailed and repeated confirmation with manufacturers during the design stage could ensure that modular equipment had no errors nor experienced any modification after on-site installation. Compared to traditional on-site assembly and construction, modular installation of metering stations can effectively shorten on-site installation duration. Furthermore, the accuracy of measurement values can be ensured since the entire module of metering station facilities undergoes testing and calibration in the plant. In addition, this installation method can eliminate several problems, including one in which traditional on-site installation is easily affected by the cleanliness of pipelines in both upstream and downstream systems, as well as contamination or even damage of metering station facilities during pigging due to foreign matter, as such issues raise the risk of on-site construction time and cost increases.
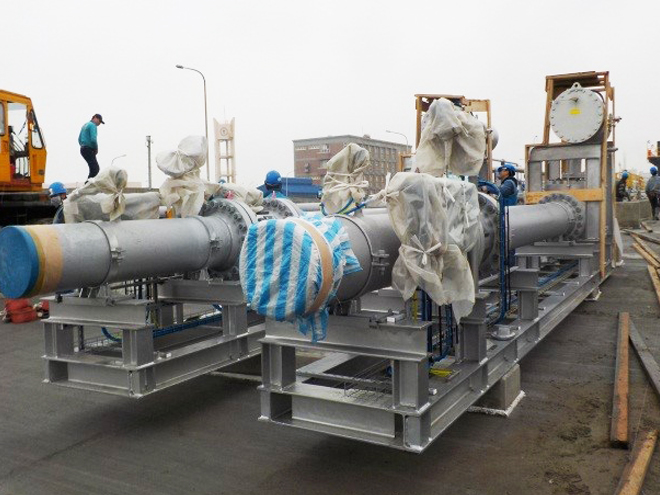
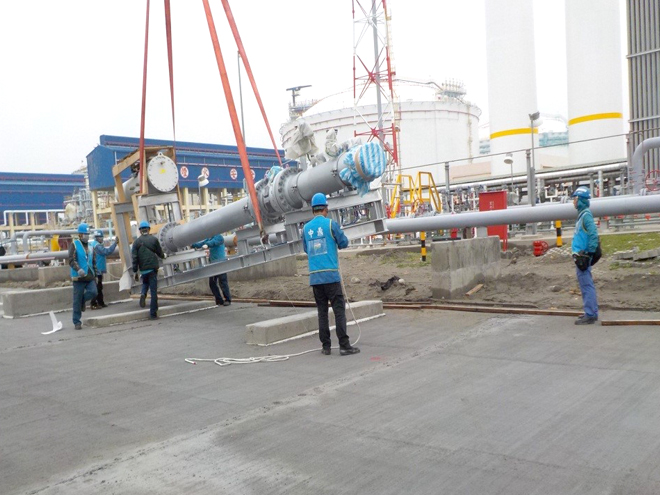
With rich technological expertise and experience, combined with an attitude to accommodate every need and contractual requirement of CPC, CTCI is able to deliver the project with success. --Zhang Yi-Cheng, Director Engineer of Construction Department, LNG Project & Construction Division, CPC Corporation