Discover Reliable
發現信賴
CTCI Successfully Expanded into the Middle East's Non-Ferrous Metal Industry: Saudi Arabia Titanium Sponge Plant Project
— Yu-Ming Chen, Project Manager, General Industry Dept., CTCI Corp., Group Engineering Business
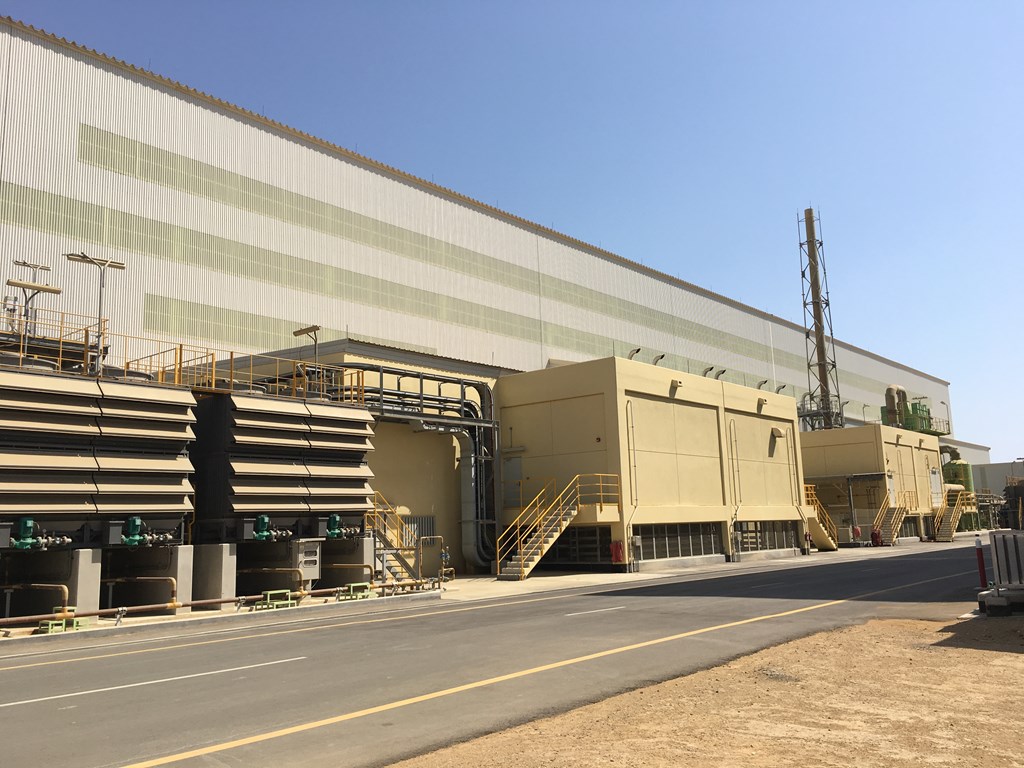
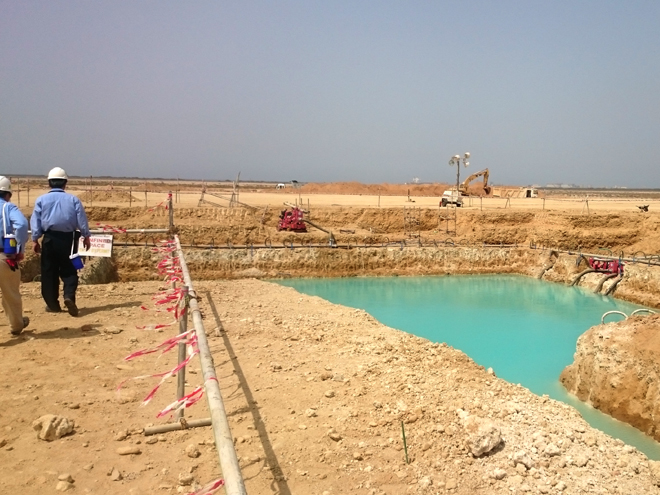
- Market: General industry
- Owner: TOHO / AMIC (Toho Titanium Co., Ltd. / Advanced Metal Industries Cluster Company Limited)
- Completion date: 31 May 2017
- Location: Saudi Arabia, Yanbu Industrial City
- Project scope:EPC turnkey project
The owner is a company co-invested by TOHO of Japan and AMIC of Saudi Arabia. In 2014, CTCI and Chiyoda of Japan jointly undertook the Saudi Arabia YNP Ti-Sponge plant construction project. The titanium sponge manufactured by one of the owners, TOHO of Japan, is well-regarded in the industry for its high quality. Their unique process technology continues to put them in the leading position in the titanium manufacturing industry. Based on customer materials or product application, the titanium sponges that are produced are melted under a vacuum into titanium ingot, or else rolled into sheets. A majority of the product is supplied to the aviation industry as material, and it is also widely used in automobiles, ship structure, power plants, construction, medical equipment, etc. The project accumulated 7 million safe man-hours without any disabling injuries, and it attained mechanical completion ahead of schedule on 28 May 2017. In August this year (2018), the titanium sponge was successfully manufactured, and 15,600 tonnes of Ti-Sponge will be produced annually for Saudi Arabia. The success of the project has established CTCI's reputation and foundation for entering the Middle East's non-ferrous metal industry.
Why CTCI?
Solid Track Record and Reliable Intellectual Property Protection
After the 311 earthquake, Japan's nuclear power plants limited their operations, resulting in a sharp increase in electricity price. It was a blow to titanium production due to its high power consumption, with the price of electricity being its main production cost. Hence, the owner, Toho Titanium Co., Ltd. actively began looking for an overseas production base with a low electricity price. However, as the process is a government-controlled process technology, special considerations have to be paid to its confidentiality and to the national interest. As CTIC has accumulated solid track record and safety performance in the Middle East, and with its stringent control on intellectual property protection, the owner is totally confident to let CTIC be part of the team.
Reliable Realized
Effective management and full communication
The project's executive team is comprised of members from Japan, Taiwan, China, India, Pakistan, Bengal, Nepal, Jordan, etc. During the course of the project, with the different cultures being exchanged, the culture shock and culture fusing, the executive team nevertheless delivered on schedule and was in control of the construction progress. They have fully obtained the trust of the owner. The construction met the quality expectations and was completed within the schedule. Also, the project accumulated 7 million safe man-hours without any disabling injuries from 15 November 2014 to 31 May 2017. This was commended by the owner. The project manager of AMIC praised CTCI for their performance in the project: CTCI Taiwan employees were "Good"! "Good" symbolizes the recognition that the owner in Saudi Arabia gave to CTCI's "Most Reliable" engineering quality.
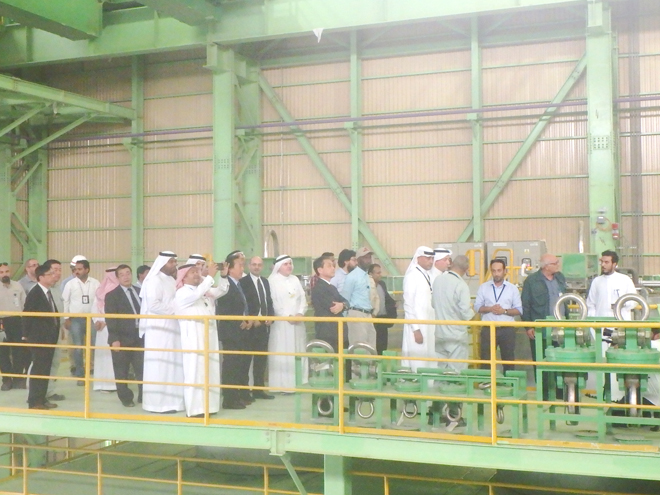
The owner in Saudi Arabia visited the titanium sponge plant
Technical Matters
Application equipment and process characteristics overcome plant limitations
The project's work scope included advanced processing equipment for titanium manufacturing, especially the new, environmentally friendly, steep angle conveyor with wave edges for titanium sponge transportation, which has successfully overcome the narrow plant limitation. This equipment is a new trend in the modern conveyor process. Its principle and control pattern is quite important for the execution and promotion of raw material transportation, high-value metal, and the related metal process.
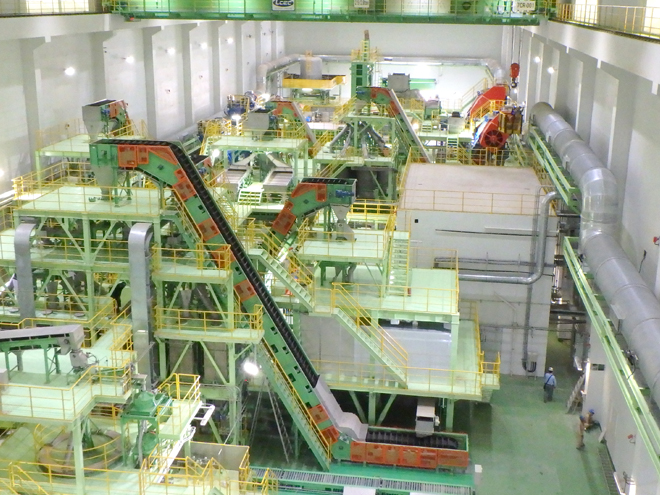
A steep angle conveyor can effectively reduce space and is a new trend in the modern conveying process.
Titanium sponges are a high value-added metal industry. Unlike a normal metal process that includes melting, crushing, screening, and remelting to remove impurities, high-value metal requires melting under a vacuum and then uses electrolysis or reduction to remove other impurities to obtain high-value metals. The project process includes methods such as electrolysis, reduction, a vacuum, crushing, screening, etc. It makes use of chlorine and titanium oxide in titanium ore to form titanium tetrachloride, goes through the electrolysis of magnesium oxide, and uses a vacuum distillation method to remove the magnesium and magnesium oxide generated from titanium sponges, and then they are made into porous and high-quality titanium sponges through a reduction reaction. The CTCI project team has had to overcome difficulties with the processing technologies, and the product was successfully manufactured in August of this year. TiO₂+2Cl₂+C→TiCl₄+CO₂ TiCl₄+2Mg→Ti+2MgCl₂
Smarter Engineering
Meeting client's requirements on schedule with cloud-based integration
The project is concurrently executed in Japan Chiyoda's Yokohama office, Taipei CTCT Headquarters, and Saudi Arabia's Yanbu site. To overcome the site's bandwidth limitation, it uses Aconex's integrated cloud system for all images, files, exchanges, and drawings to effectively control the documents. Besides reducing the owner's time in reviewing the drawings, it concurrently provides relevant information of the site's actual construction, thereby effectively increasing the entire project's EPC execution efficiency. For its typical-sectional crushing plant and warehouse, the project uses PEB (pre-engineered building). This reduces a significant amount of steel work, and with PEB's advantages such as its lightweight, easy, and quick assembly, it effectively reduces installation time and reduces workspace. The project team also coordinated with the owner in installing the overhead crane in advance for construction and installation work, and concurrently pre-assembled the ground machine and electric equipment. Besides expanding the work area by splitting, large area scaffolding that complied with safety standards was set up by the overhead crane to facilitate the installation of large-area anti-static top plates by moving to and fro, effectively reducing installation time and increasing construction safety.
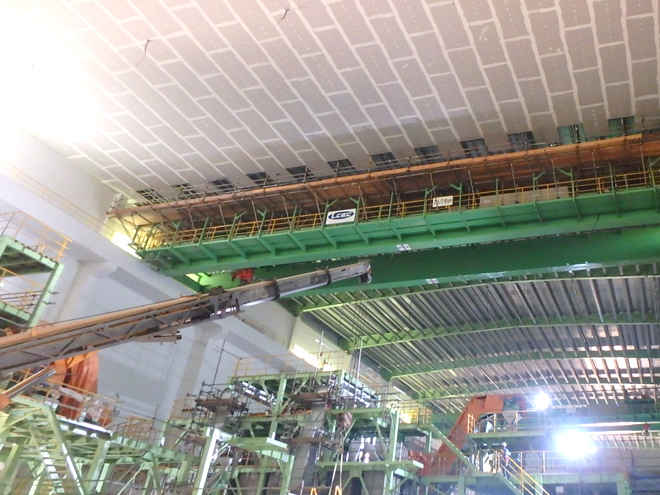
Installing large area anti-static top plates by moving the overhead crane to and fro.
The first batch of titanium sponge had been successfully produced this August (2018). As part of the team, we are very honored as well as proud of the CTCI "Most Reliable" brand spirit during the project execution. We hope that all the CTCI staff will continue to fulfill customer requirements with the "Most Reliable" engineering quality, and practice "We’re CTCI. We’re Reliable." -- CTCI project manager, Chen Yu-Ming
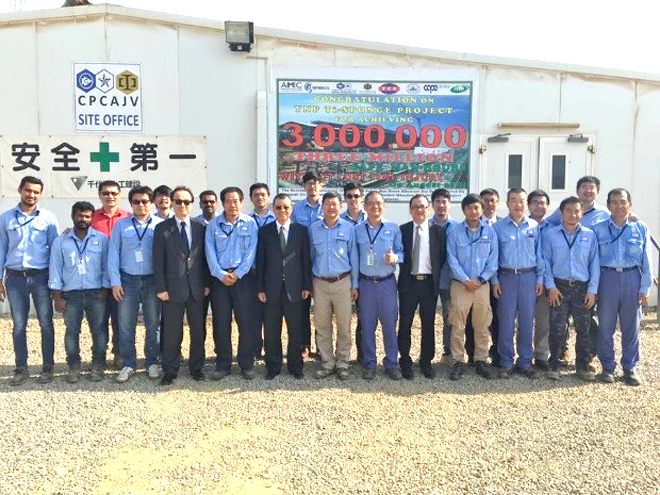
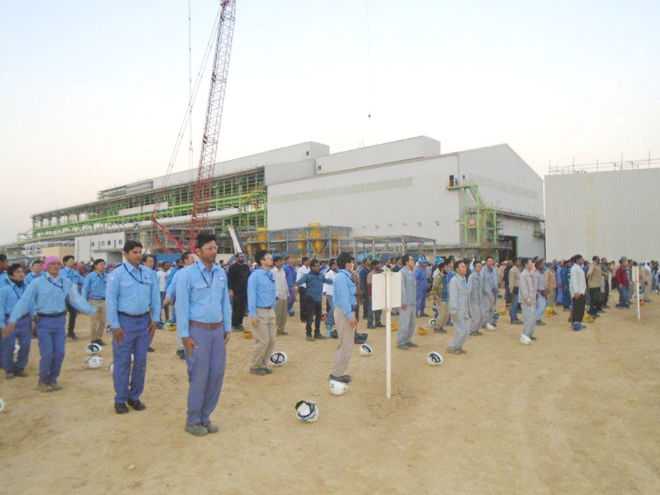
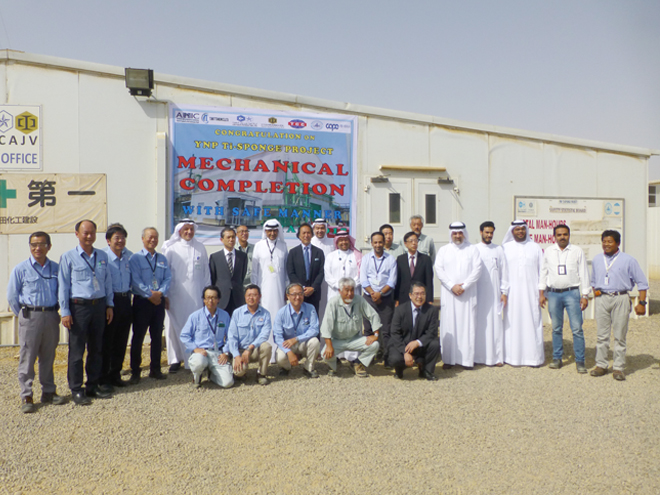