Technology
技術分享
Resource Regeneration for Infinite Energy
Advancing, Integrating and Utilizing Energy from Waste Plant Technology
Group Resource Cycling Business (GRCB), a member of CTCI Group, has more than 20 years of accumulated experience in operation and maintenance (O&M) of EfW plants and waste management. Apart from aggressively converting waste into sustainable energy and resources, GRCB also constantly improves the specialized O&M technologies of EfW plants, serving as a role model for the nation in waste reduction, energy recovery and environmental impact minimization.
The equipment & system of facilities in domestic EfW plants are mostly manufactured in Europe, USA, and Japan. Spare parts and technical support are provided by overseas suppliers, so when system abnormalities or malfunctions happen or when spare parts are phased out by their manufacturers, immediate support is normally not available. As a leading provider of waste management and O&M services to EfW plants, GRCB has developed, improved and integrated technologies and offers the end results as services to EfW plants, enabling them to break away from their dependence on overseas suppliers. Our achievements include high-alloy boiler tube cladding, stoker-side clinker inhibitor, sodium bicarbonate (SBC) acidic gas control, lime and semi-dry and dry co-operation acidic gas control system. These combine with intelligent solutions to form an integrated platform that enhances the efficiency of key systems and overall operation of EfW plants. Furthermore, GRCB has extended its business into other fields, including mass rapid transit, airports and hospital.
Convert heat into electricity
Achieve highest utilization of energy and resources in EfW plants
The incineration process in an EfW plant completely burns out the combustibles. A steam boiler recovers combustion heat to generate live steam, which is then converted into electricity by a steam turbine generator, thus maximizing both waste reduction and energy and resource utilization. By continually improving such technical practices and resources, GRCB has developed its localized technical service capability for upgrading various equipment and systems.
1. Technology localization – steam turbine generator system
The steam turbine generator is the core equipment in a plant for converting heat into electricity; its loading control should react to grid power demand and quality instantly and simultaneously. In early 2007, due to a control system malfunction in one of GRCB’s plants, we were faced with the risk of an original spare part from overseas being phased out, so we commenced our own repair and upgrade plan. Back then, the source code for the control program was not available and the control logic diagram came from the original supplier. GRCB adopted countermeasures by summarizing the trip and protection list, start up and stop operation standard operation procedures, and related information to produce control logic. It then coded the control program accordingly and, step by step, simulated each individual function offline. After that, it conducted online tests to translate the black box, completed the system upgrade, and built a localized independent capability for troubleshooting, repair and system upgrade (see Figure 1).
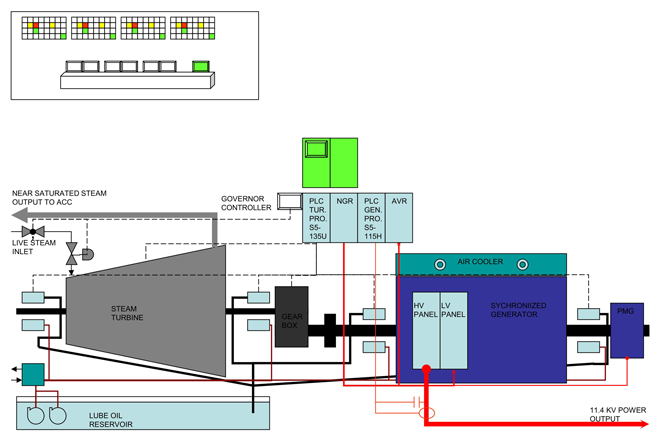
Figure 1. Upgraded steam turbine generator control system.
2. System stabilization – Incinerator auto combustion control system
Boiler steam production stabilization is the core of boiler loading control; it achieves target value by combustion control. Refuse combustion is influenced by various parameters, including refuse heating value, excess air ratio, combustion temperature, and steam flow and variations. These parameters are variable (see Figure 2) and the accuracy of control and adjustments rely on the operator’s experience. Leveraging its years of O&M experience in domestic and overseas EfW plants, GRCB has developed an advanced auto combustion control (ACC) system. The system applies fuzzy control and the characteristics of refuse in Taiwan to classify key parameters and refine control outputs, induce and compile statistics, and analyze manual control patterns into rules to standardize and program operations that minimize manual operation mistakes. Rigorously tested on site over long periods of time, the ACC has a reliability of over 95%, far above that of designs from original suppliers. This helps plant owners reduce pollutant emission while increasing combustion stability and system performance (see Figure 3 and Figure 4).
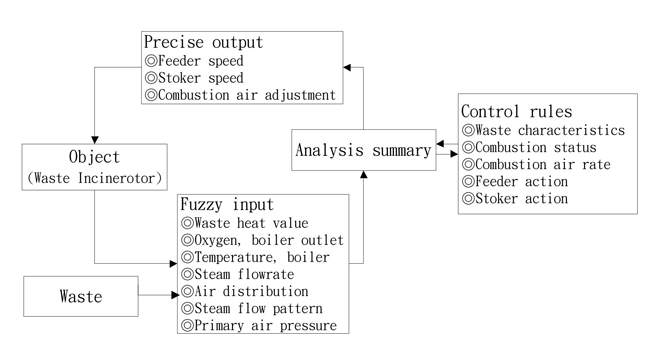
Figure 2. Auto combustion control system logical diagram.
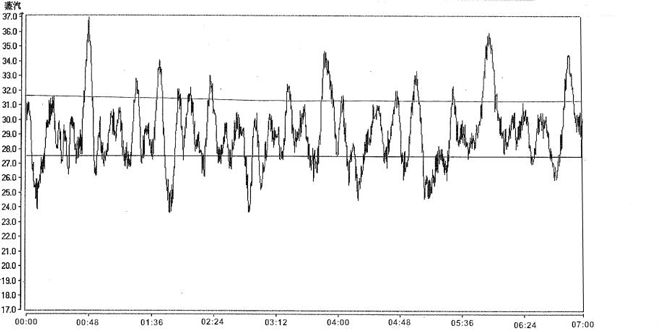
Figure 3. Original ACC system combustion condition trend.
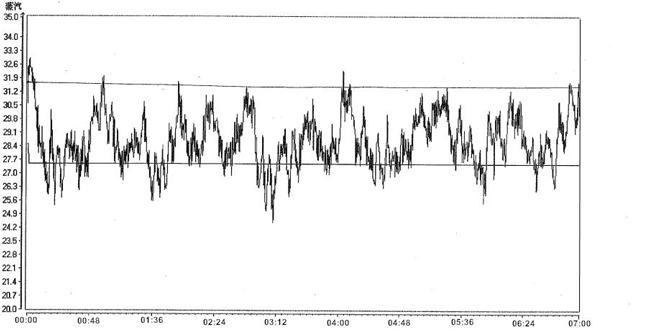
Figure 4. GRCB ACC system combustion condition trend.
3. Technology upgrade – refuse crane system
The refuse crane is the core unit to implement refuse reception and homogenization and ensure stable combustion. GRCB utilizes electromechanical integration technology and practical experience to upgrade the refuse crane system in many plants. Such upgrades not only ease worries about spare parts obsolescence, but also reduce spare parts costs. Our technology and expertise also simplify adjustment and calibration procedures, increase operation efficiency, and eliminate errors. They also turn the typical refuse crane structure from an enclosed blind one into an open one, creating diversity of repair and maintenance such that the stability of the plant is in complete control, thus increasing plant availability and performance while keeping a lid on costs. (For typical refuse crane control system upgrade conditions, please see Figure 5 – 7.)
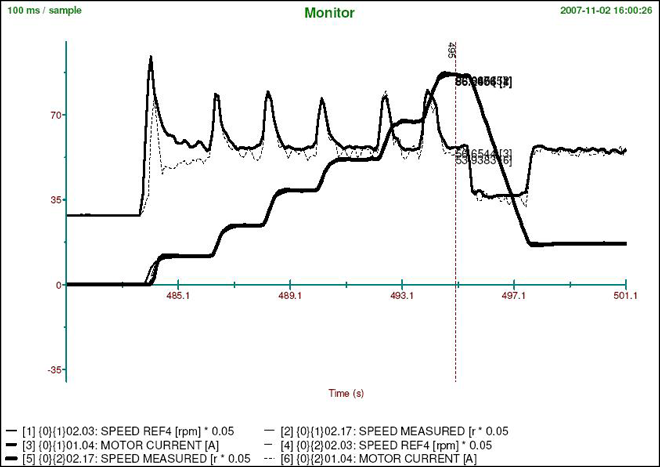
Figure 5. Refuse crane lifting synchronize acceleration loading curve.
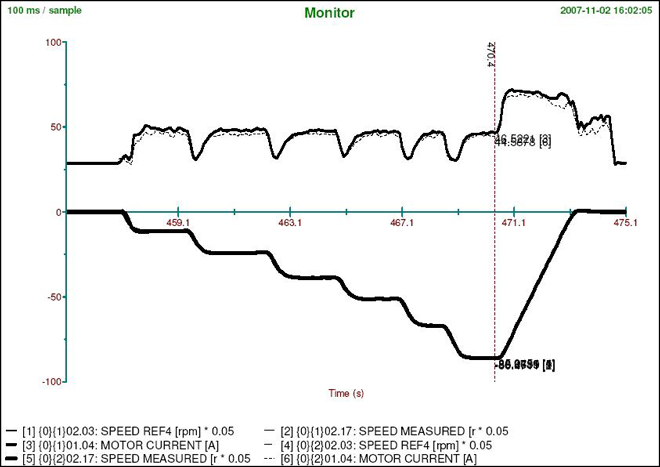
Figure 6. Refuse crane lowering synchronize acceleration loading curve.
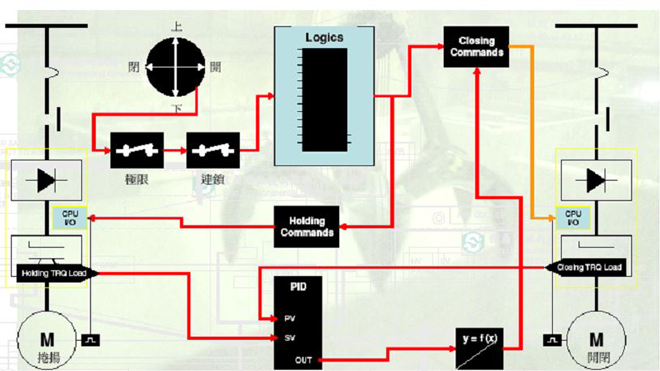
Figure 7. Crane grab rope control system diagram.
Technology for better pollution prevention control
Create safety and best performance of EfW plant
Refuse is inherently unstable and inhomogeneous, and its combustion generates huge amounts of ash and flue gas. This results in accumulation, erosion, failure and clogging at various stages of the boiler process, which stresses the stoker, boiler tube, refractory, and flue gas treatment system. Scheduled cleaning and repairs are required, otherwise the acidic and highly corrosive gases that are produced cause process equipment & system to corrode. For example, chlorine (Cl) content forms hydrochloric acid (HCl) and sulphur (S) content forms SOx during the combustion process. GRCB has developed high-alloy cladding boiler tube, stoker-side clinker inhibitor, sodium bicarbonate (SBC) injection, lime semi-dry and dry acidic gas control technologies that effectively reduce the impact to equipment and the ambient environment caused by the combustion flue stream.
1. High-alloy cladding boiler tube
In addition to periodic annual outage for overhaul, occasional unscheduled shutdowns due to boiler tube leaks happen due to the highly erosive and corrosive characteristics of combustion flue in EfW plants. After exploring advanced technologies in developed countries in Europe and the USA, GRCB conducted field tests with various technologies and concluded that a new method called “high-alloy cladding boiler tube method” is highly feasible. This method significantly extends the service life of boiler tube and increases the availability and reliability of the plant (see Figure 8).
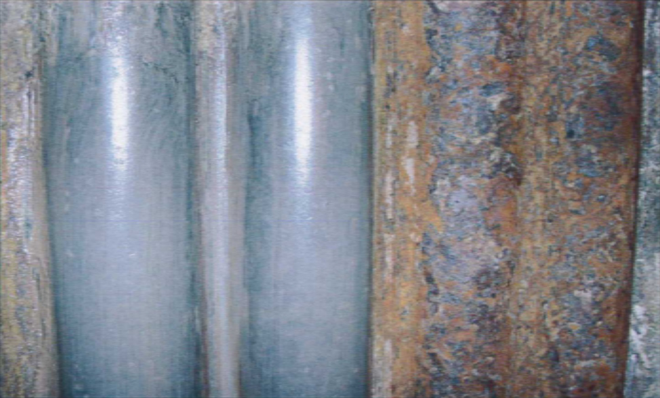
Figure 8. Comparison of boiler tubes with (left) and without (right) high-alloy cladding.
2. Stoker-side clinker inhibitor
For specific types of stoker, clinker forms on the stoker side and obstructs waste feed. When this happens, shutdowns are needed for cleanouts, constraining EfW plant operation over the years (see Figure 9). Using theoretical analysis and methodology verification, GRCB has developed clinker inhibiting technology that improves treatment capacity and electricity output performance (see Figure 10).
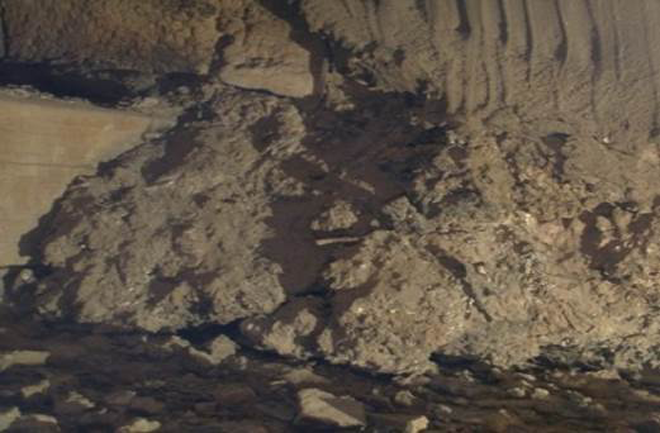
Figure 9. Stoker-side clinker build-up before inhibition. measures.
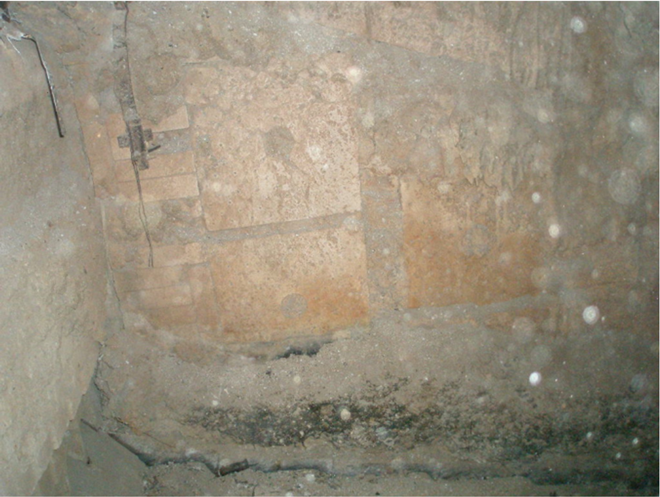
Figure 10. Stoker side after inhibition measures.
3. SBC dry injection acidic gas control
The injection of Sodium Bi-Carbonate (SBC) powder to a flue gas treatment system removes acidic gas with a high degree of efficiency. However, the SBC needs to be of very high particle quality, the grade of reagent required costs twice that of industrial-grade reagent, and reagent-grade SBC presents hygroscopic and caking effect during storage, which causes the dosing system to clog and increases the dosing rate to 20% to 30%, increasing the cost of dosing 1.4 ~ 1.6 times. GRCB has developed and verified online SBC particle size control technology which was practically applied in overseas special waste treatment plants at the end of 2011. We are now able to use low-cost industrial-grade SBC to create the fresh reagent-grade SBC dosing effect, enabling us to prepare for the increasingly stringent emission standards and establish the basic ability for the group to expand the use of flue gas treatment technology with higher removal efficiency.
4. Lime semi-dry and dry co-operation acidic gas control
GRCB has developed lime semi-dry and dry co-operation acidic gas control technology which ensures that the HCl and SOx emission values comply with the relevant regulations during the period when the atomizer systems of the semi-dry reactor are regularly maintained, chemical dosing interrupted and the acidic gas concentration increases rapidly. In addition, GRCB also applied lime online separation purification technology to improve the application of low-quality lime such that it provides the performance of high-quality lime.
Intelligent Management Integration
Extend applied technology from EfW plants
For more than 20 years, GRCB has undertaken O&M tasks in EfW plants designed and constructed by different professional manufacturers. These tasks include the establishment of various operations, maintenance, management of standardized systems and procedures, integration of plant operation and management, factory patrol, maintenance dispatch, regular maintenance, warehousing and material management, and procurement management. We have also combined operations, maintenance, and operations management into an integrated operation information platform (IOI, see Figure 11). This smart platform includes a maintenance management information system (MMIS) and an operational performance index report system (ORS). Equipment monitoring data, on-site job feedback and the operational performance database are collated, analyzed and presented as Big Data using an online expert diagnosis system. This way, data is presented via a single smart platform.
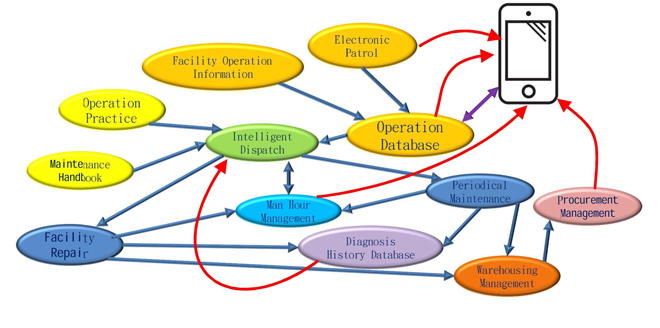
Figure 11. Integrated operation information platform diagram.
GRCB strives to improve and enhance the operation technologies of EfW plants by combining EfW plant O&M, intelligent data management, successfully upgrading important equipment, and accessing technical patents. In particular, the successful upgrades we have performed have enabled GRCB to establish its core mechanical and electrical capabilities. Not only have we actually applied these in operational plants to resolve the current bottlenecks of EfW plants in Taiwan, but we also have optimized the efficiency of resource recycling and extended this success to other industries for related applications, e.g., Kaohsiung MRT station equipment operation and maintenance, power system maintenance and track system testing and commissioning services in 2017. Lately, we also gradually extended these technologies to Taipei MRT, Taoyuan MRT, airports, hospitals and other fields in different industries. In the future, GRCB will focus on further enhancing resource recycling efficiency, intelligent data application, and participation in national community environmental issues and community care co-operation efforts. We look forward to trends and developments in the market, promoting Taiwan’s successful EfW plant operation technology and experience abroad, and becoming "the most reliable provider of industry-leading ‘resource cycling’ services" that marries the protection of Earth's resources with business growth for the sustainability and well-being of the human world.