Technology
技術分享
CTCI Intelligent Solutions
Digital Transformation and Intelligent Services under Industry 4.0
Since the Industrial Revolution in the 18th century, industrialization has evolved from merely replicating labor processes to that of human intelligence in the era of Industry 4.0. In response to the current surge in industrial transformation, Group Intelligent Solutions Business from CTCI looks at factory and corporate operational performance from digital traces (i.e., data) produced by customers, factories, and companies with the aim of finding a new business model and enhancing operational performance for customers worldwide.
In 2014, a petrochemical underground pipeline gas explosion occurred in Kaohsiung City, Taiwan. In the wake of the accident, the Kaohsiung City Government led various industries to jointly construct a pipeline transmission monitoring system. The development and design of the monitoring system was contracted to ASI from Group Intelligent Solutions Business. The main function of this system was to disclose the transmission data. ASI's role in the Taiwan underground long-distance pipeline monitoring project was to provide platform services to match with downstream petrochemical businesses. While this type of platform as a service (PaaS) was a rare commercial model in the past, it enabled us to provide real-time optimized solutions and services.
CTCI Cyber Integration Platform: A Tool for Dynamic Factory Operations
The German government coined the term “Industry 4.0.” The objective was to re-shape industrial norms through advanced technologies, and thereby adapt to complex market demands, reduce wasted time and costs, and improve corporate competence. When looking at the history of CTCI’s intelligent manufacturing services, ASI is noted for being an expert in instrument and control systems integration, helping owners rationalize, standardize, and automate systems integration. In recent years, ASI entered the intelligent manufacturing business with the aim of helping owners automate factory data to a state of intelligent automation, thereby completing a factory’s digital transformation. Data is the key to driving digital transformation. Enabling the owner to access a data stream is crucial. By means of a proprietary manufacturing intelligent virtual integration platform, called the Cyber Integration Platform (CIP), ASI centralizes the management of digital traces left behind by the equipment and helps owners analyze and interpret the data via algorithms or external software. An optimal dynamic model can then be placed back into the overall equipment circuit to provide functions identical to that of the human brain, thereby providing equipment and production lines with the ability to respond to various situations. ASI collects a downstream petrochemical plant’s transmissions data on the intelligent data management platform and conducts a preliminary arrangement before uploading the data to the Chunghwa Telecom cloud platform. Users can use their personal accounts and log in to the cloud platform via the Internet to view the transmission status.
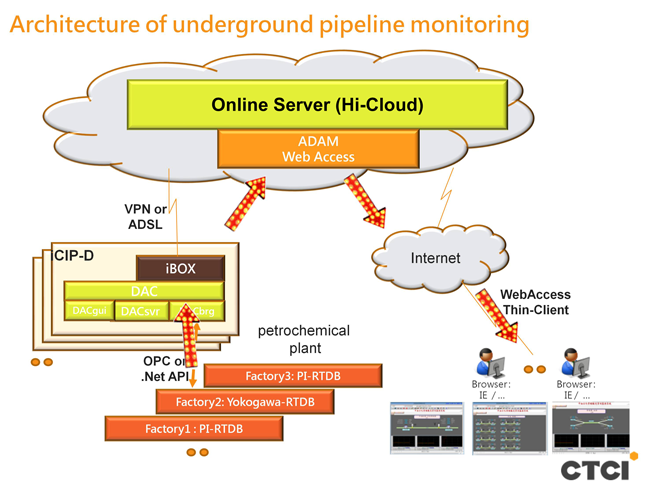
Figure 1. Underground long-distance pipeline monitoring system architecture
CTCI GPS-Compressor System Assists with Decision Making in Factories
From an industrial perspective, if the utilization behaviors of assets (e.g., production equipment) could be digitized, we will be able to create more valuable applications. For instance, in the past, we determined product quality mainly through sample inspection, which was time-consuming and incapable of identifying every faulty product. Now, the quality of each product can be indirectly obtained through analyzing the production machines’ operating data. This defines the data-based intelligent application — i.e., virtual measurement technology — and serves as an application of data technology in factories. Typically, equipment operating conditions are periodically checked by professional inspectors, and are thus often delayed and prone to human error. Therefore, the application of data technology in intelligent factories includes judging the health and life of machinery and equipment.
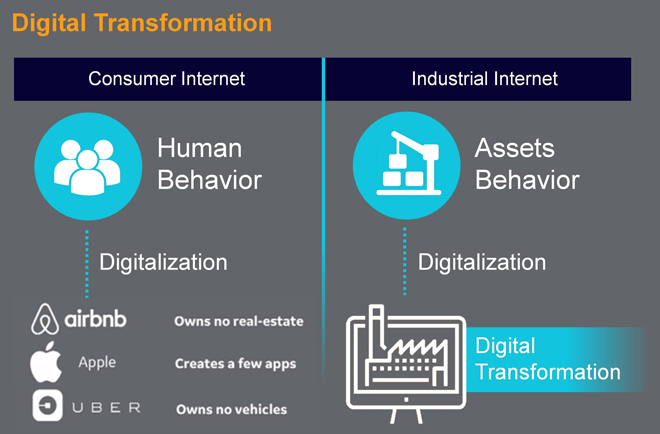
Figure 2. Digital transformation (please refer to the GE M+M 2016 conference)
ASI is extensively experienced in the chemical engineering industry. We developed the Guiding Process Simulator (GPS) Compressor System to collect various data and construct virtual models through a professional consulting team. At the end of it, the operating status is displayed through a human machine interface (HMI) that provides instructions and helps on-site operators to make decisions. Additionally, in determining the health and life of the machinery and equipment, ASI uses a prognosis monitoring system (PMS) which is developed by ITRT Mechanical and System Research Laboratories to collect data such as vibration, sound, voltage, current, and temperature through sensors on the rotating parts of the equipment. As such, it provides total control of the health and life span of the equipment. The data can then be analyzed by field experts or with the use of algorithms to determine potential equipment downtime ahead of time. By way of example, consider the compressor, which is a crucial piece of equipment in a petrochemical plant. A surge in the compressor can lead to tripping, with severe consequences for the production schedule. In the past, operators increased the opening of by-pass valve or recyle valve to prevent a surge in the compressor. However, this increased wastage, deviated from the optimal operating range, or destabilized the steam valve. With the use of the CTCI GPS-Compressor System and the PMS, it is possible to provide field operators with the correct advice to maintain operations at the most efficient point in time and to understand the equipment usage.
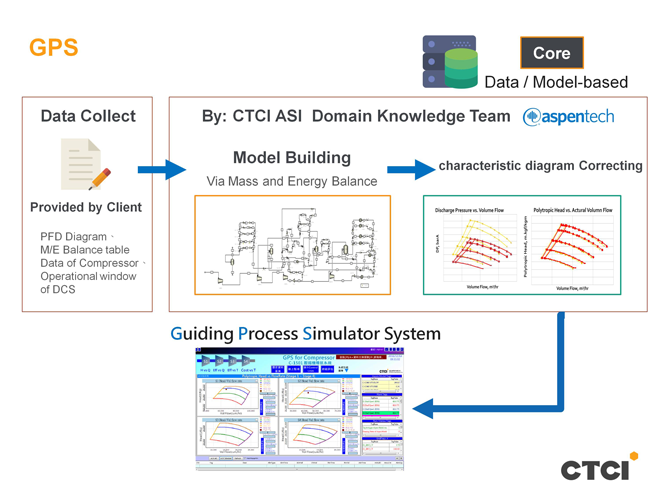
Figure 3. CTCI GPS-Compressor method
Comprehensive Intelligent Services & Applications: Win-Win Solutions for CTCI’s Global Customers
Based on the history of industrial development, the transformation from replicating labor to that of human intelligence is inevitable. Since the 18th century, when James Watt improved the efficiency of the steam engine and commercialized it, the general perception toward products and services has changed. This pushed the demand for mass production and prompted the need for replication, as factories began to produce various consumer goods. During that period, industrial technologies replicated manpower while humans used their machine inventions to replicate mass labor, freeing up tremendous amounts of time for other work. By the 21st century, problems such as an aging population, declining birth rates, and labor shortages began to surface. Humans then began to contemplate machines as capable of rational reasoning (intelligence) and handling a variety of tasks; this would allow humans to focus on making more important decisions on their priorities list. CTCI has a strong foothold amidst the current surge of industrial transformation. The elements of our corporate culture, which consists of professionalism, integrity, teamwork, and innovation — provides owners not only with advanced services for iEPC turnkey projects and intelligent manufacturing, but also comprehensive innovative technologies, such as BIM Life Time Service and digital integration platforms, which assist customers with global transformation and lay the foundation for future development of smart shopping centers and intelligent technology parks. Digital transformation is not a one-directional process, but provides benefits through mutual leverage, creating a win-win solution for businesses, vendors, consumers, and the environment.